Knit Line Techniques
Dispense Techniques for Cure-in-Place and Form-in-Place Gasketing
In cure-in-place (CIPG) and form-in-place (FIPG) gasketing applications, the gasket creates a seal used to protect critical components from air, dust, and moisture intrusion, prevent leaking and dampen vibration. Achieving a good knit line can help to eliminate voids and ensure bead fusion to deliver a reliable seal.
Knit Line Dispense Techniques
Determining the appropriate knit line dispensing technique is an important consideration in dispense system programming and setup. Several knit line techniques include the overlap, parallel pass, butt joint, and sloping overlap.
Overlap

Sloping Overlap

Parallel Pass

Butt Joint

Automation Techniques
Programming of the robotic dispensing system can also play a critical role in achieving bead path application requirements. Depending on part complexity and axis, adjustments to the automation motion can help optimize the dispensing process. Several automation motion techniques include the rake motion, traditional motion, reverse rake, and reverse rake and brake motion.
Traditional Motion
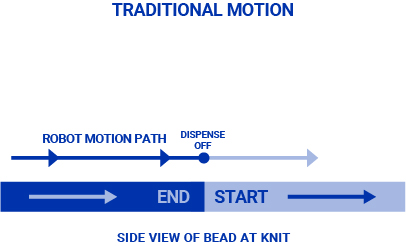
Rake Motion
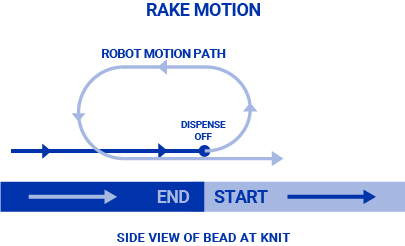
Reverse Rake Motion
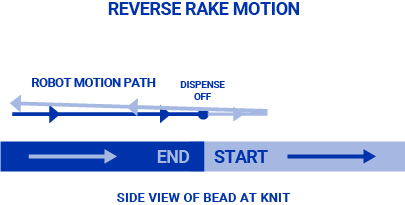
Reverse Rake and Break Motion
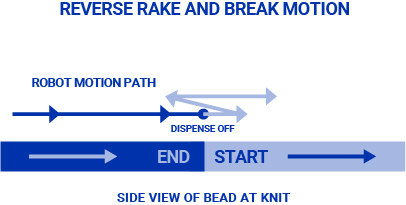
Summary
In CIPG and FIPG, knit line dispense techniques and automation motion techniques play a critical role in proper bead dispense and achieving the desired knit line. In addition, here are some other important considerations:
- Rheological properties of the material
- Material viscosity
- Temperature
- Bead profile and functionality
- Dispense valve sealing technology
- Dispense parameters
- Equipment fixturing
- Substrate design and complexity
Contact an Expert
Related Articles
Silicone Sealant for Form-in-Place Gasketing (FIPG)
Engineers and scientists from Graco and Dow Inc. work together to help automaker effectively dispense silicone sealant. Software upgrade improves E-Flo iQ accuracy and consistency with all high yield stress sealants.
Comparing 2k Meter Mix Dispense Systems
Chart compares advanced two-component meter mix dispense (MMD) systems, including PR-X, PD44, PR70, EFR, and HFR.
Extreme Material Abrasiveness? Problem Solved with Elite
Some thermal interface materials (TIMs) are so abrasive, it’s like pumping diamond dust or liquid sandpaper. Explore why and how we developed Elite™, the longest-lasting pump construction for abrasive material dispense.