Silicone Sealant for Form-in-Place Gasketing (FIPG)
Engineers and scientists from Graco and Dow Inc. work together to help automaker effectively dispense DOWSIL™ 7091 Adhesive Sealant. Software upgrade improves E-Flo iQ accuracy and consistency with all high yield stress sealants.
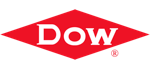
DOWSIL™ 7091 Adhesive Sealant
DOWSIL™ 7091 Adhesive Sealant is for applications that demand a strong but flexible bond, such as glass to metal or glass to plastic. Its durability and longevity has made it an industry standard for electronics applications. Automakers use the alkoxy-cure silicone sealant for form-in-place gasketing (FIPG).
Like many other highly filled elastomer sealants and adhesives, DOWSIL™ 7091 Adhesive Sealant has a high yield stress. Unless the initial yield stress effect is dealt with, the sealant’s flow rate can be difficult to control, making accurate dispense a challenge.
- For complete material profile data, visit dow.com.
Factors Affect FIPG Flow Rates
A global automaker was using Graco E-Flo iQ systems to meter and dispense DOWSIL™ 7091 Adhesive Sealant on its assembly line. During form-in-place gasketing (FIPG) applications, some E-Flo iQ systems were dispensing inconsistent beads of the silicone sealant
These factors were making material flow rates difficult to control, affecting product quality and production costs:
- The high pressure needed to overcome yield stress compressed the silicone sealant.
- Sudden pressurization at the pump outlet increased shear on the material. Pressure in the 2-ball pump increased and then quickly decreased, affecting pump changeover.
While the sealant exhibited yield at the start of dispense, once flowing through the system, the flow rate was higher than anticipated.
Troubleshooting Together
To solve control issues and perfect dispensing, Graco and Dow Inc. took these steps:
- Conducted extensive testing in both companies’ labs.
- Developed a corrective action plan.
Graco Tests Address FIPG Bead Control
At the Graco Customer & Innovation Center in North Canton, OH, application lab engineers set up a test that mirrored the automaker’s form-in-place gasketing (FIPG) application.
Pump Changeover Adjustments
Since initial field observation showed that pump changeovers might be causing inconsistent bead dispense, they worked with programmers to modify the pump changeover algorithm in the E-Flo iQ software.
- Before the software modifications, pressure spiked at the pump during a top changeover. The pressure changes caused the dispensed beads to be much wider than standard.
- After the software modifications, the pressure spikes decreased, yielding smoother and more standardized bead segments.
Pressure Trends Compared
Original Software
Pressure readings recorded at the pump with the original software show broad and unpredictable pressure ranges, with some pump pressures exceeding 200 bar.
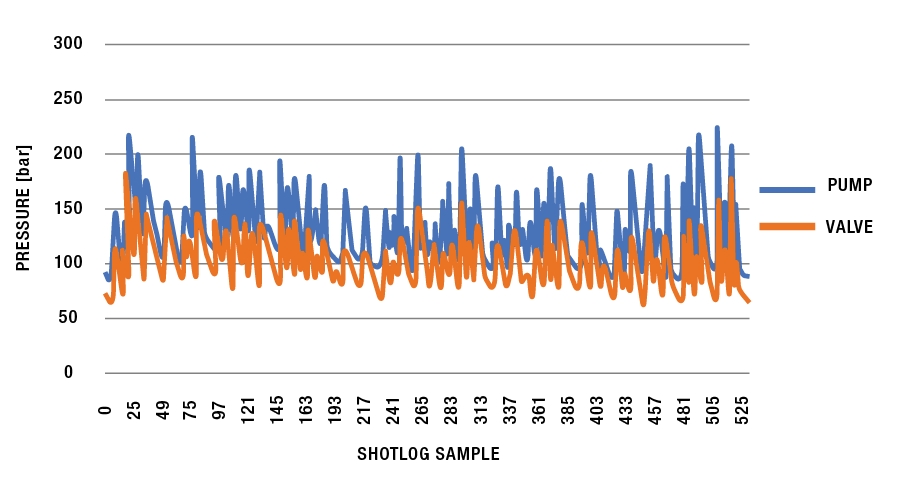
Updated Software
Pressure readings recorded at the pump after the software update show tighter pressure ranges, with no spikes and no pressures over 160 bar.
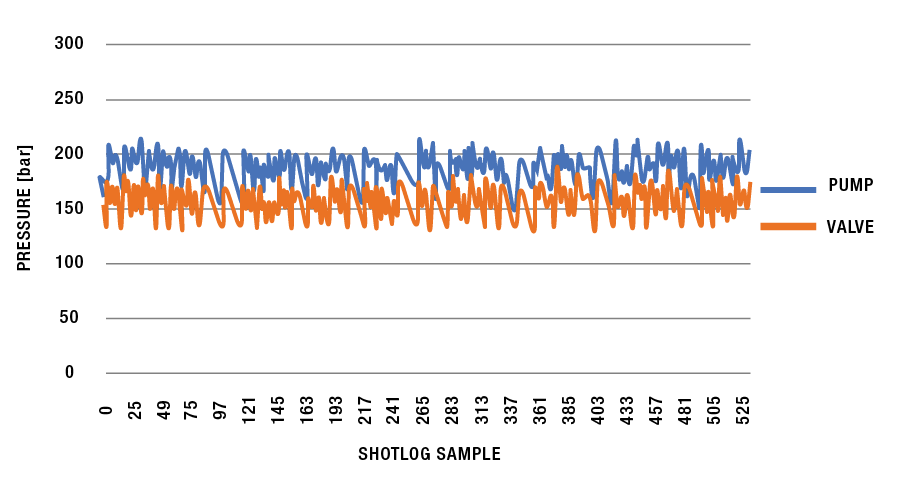
The updated software had a reduced pressure target calculation after each pump changeover. The new pressure target resulted in more controlled and tighter pressure trends. This yielded smoother, more standardized dispenses.
Dow Inc. Completes Root Cause Analysis
To better understand the material properties contributing to the dispensing issues, Dow Inc. scientists and chemical engineers evaluated two different hypotheses as to the potential root cause of the dispensing challenges:
- Fluid compressibility was causing contraction and expansion of the sealant throughout the dispense equipment and following dispensing of a bead, resulting in poor dispense controllability.
- Yield stress effects of the sealant caused inconsistent flow at a given pressure, resulting in poor dispense controllability.
Pressure volume temperature (PVT) testing revealed that compression of the material upon startup was not the main cause of the inconsistent bead dispense.
Computational fluid dynamics (CFD) modeling concluded that yield stress effects primarily caused the dispensing challenges – and that the Graco E-Flo iQ software upgrade effectively addressed those issues.
What are Yield Stress Effects?
“Yield stress effects” describes the minimum force or stress needed to make material start flowing or change shape. Think of it like squeezing a tube of toothpaste: until you apply enough pressure, nothing comes out.
As such, the initial dispense pressure needed to overcome the yield stress is often higher than the pressure needed to maintain flow. If an industrial metering and dispensing system’s software is not accounting for this type of effect, the sealant or adhesive will not come out at the right rate and in the correct amount to form the best shape or bead on a part or product.
Advances in Dispense Technology for High Yield Stress Sealant
Initial findings by Dow Inc. and Graco showed that changes to the E-Flo iQ software significantly improved the metering and dispense system’s ability to accurately and consistently handle DOWSIL™ 7091 Adhesive Sealant. To verify this, several customers also tested the software in their factories.
When the automaker installed the software upgrade, they conducted trials and saw positive results.
- In the original software, the range of pressures was very wide and pressure spikes were obvious.
- With the updated software, the pressure spikes were gone. Pressure stabilized in a tight range, with none seen over 160 bar. Due to pump changeover improvements, shot repeatability increased.
“This is an example of some great collaboration that’s helping any manufacturer who handles high yield stress sealants,” said Andy Kenney from Dow Silicones Corporation.
“I couldn't agree more,” added Grant Nelson from Graco’s Industrial Division. “It was great to collaborate and learn more on both sides. I hope we can do more of this as well.”
All trademarks and registered trademarks are the property of their respective owners.