White Paper: Elite Construction Testing
Extreme Material Abrasiveness? Problem Solved with Elite™
Some thermal interface materials (TIMs) are so abrasive, it’s like pumping diamond dust or liquid sandpaper. Explore why and how we developed Elite™, the longest-lasting pump construction for abrasive material dispense.
Dispense Pump Construction Holds Up Against the Most Abrasive Materials
Ever had factory equipment that doesn’t hold up? It not only slows down production, it diverts time and money that would be better spent on improving business.
When extreme material abrasiveness decimated traditional dispense pumps and valves, Graco’s research and development team solved the problem with Elite™ construction. Here’s why and how they did it.
Highly abrasive materials challenge traditional dispense pump construction for electric vehicle battery, electronics and general industrial manufacturing. And the most notorious equipment-shredding culprit is thermal interface material (TIM).
What is Thermal Interface Material, and Why is TIM So Abrasive?
Thermal interface material (TIM) dissipates heat away from components, thus improving their speed, longevity, and manufacturability. Batteries and electronics especially need heat dissipation so that they perform as consumers expect.
Thermal interface materials (TIMs) contain high-thermal-conductivity particles suspended in a viscous carrier fluid. The nature of these particles is extremely hard. The higher their concentration in the fluid, the more abrasive the material becomes.
More and more manufacturers are using advanced TIMs that are so abrasive, it’s like pumping diamond dust or liquid sandpaper. Such material abrasiveness etches away metals and seals as it moves through factory dispense pumps and valves.
Testing and Re-Testing Long-Lasting Construction
To make sure Graco dispense pumps and valves withstand extremely abrasive materials, our research and development team took a new look at their seals and surfaces.
Elite™ construction came out of iteration after iteration of design and testing. The tests involved typical thermal interface materials (TIMs), and proprietary fluids with extremely abrasive qualities. Supply pumps, metering systems, and valves were cycled on and off for months at a time, with regular observation and inspection to document and strengthen any weak points.
The following test results demonstrate how Elite™ construction outperforms standard dispense pump and valve construction. Manufacturers can expect…
- to dispense at least 50,000 gallons (200,000 liters) before noticing any wear on pump pistons and cylinders
- to get at least 10 times more life out of products with Elite™ construction, compared to standard supply and dispense systems*
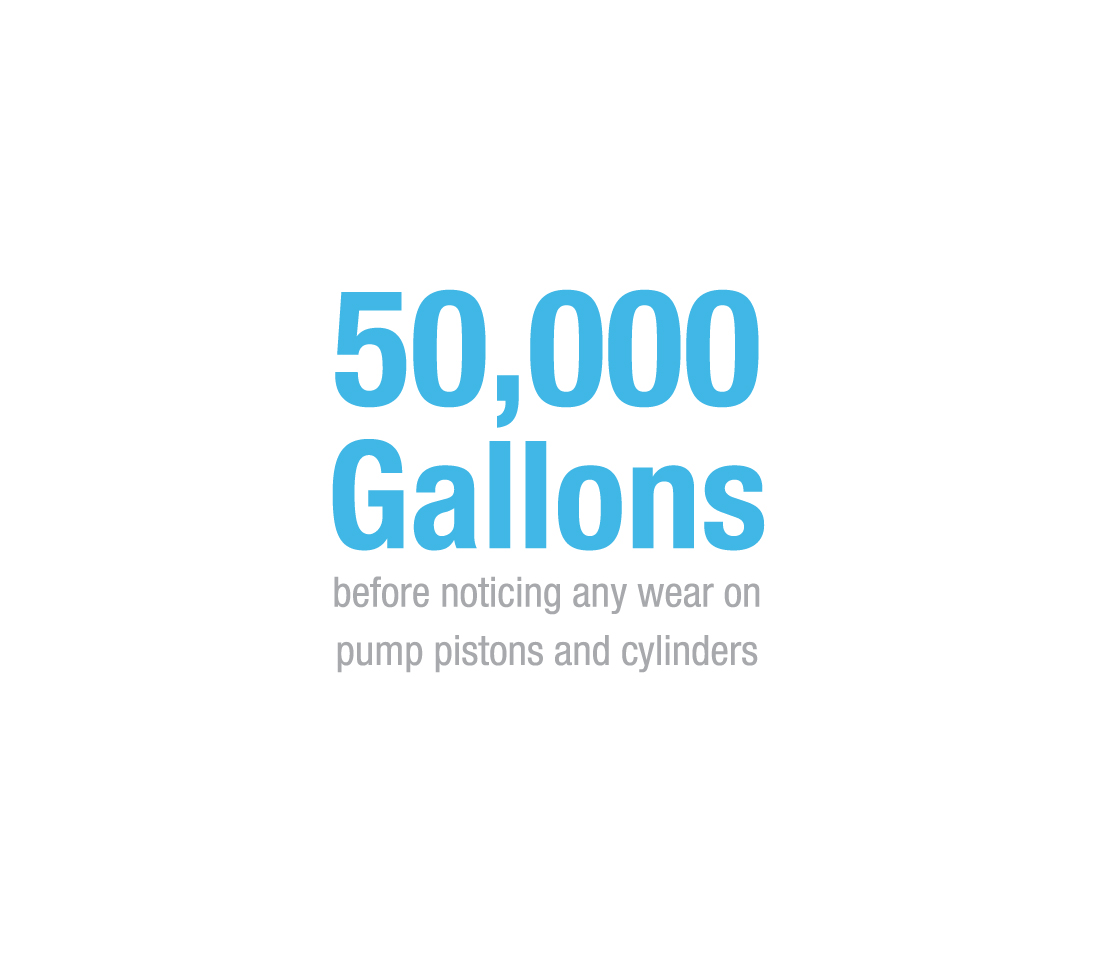
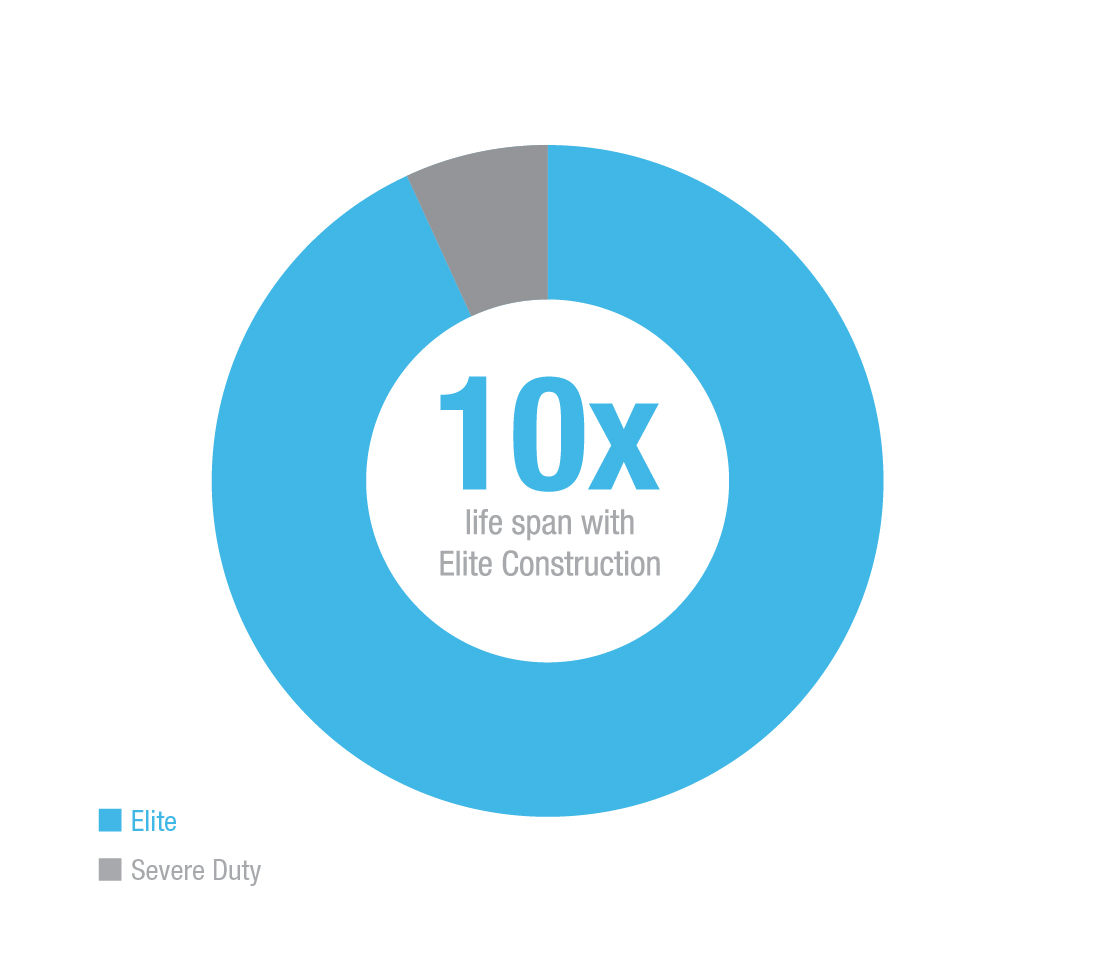
* Results may vary. Variables affecting component life include, but are not limited to, material chemistry/fillers, flow rate, cycle rate, maintenance diligence, and system pressure.
Dispensing Bondway 2K Adhesive
Bondway two-component (2K) thermally conductive polyurethane adhesive is used in the bonding, fixing, and heat dissipation of heat generating electronic components.
A typical setup for this material includes supply pumps that feed a meter, mix and dispense system. For this test, the Graco team equipped it with Elite™ construction.
The Bondway 2K material was supplied in two 5-gallon pails, with the B-side containing the most abrasive properties.
- Two 100 cc Check-Mate supply pumps with Elite™ construction evacuated material from the 5-gallon pails.
- The supply pumps moved the material through hoses to a Hydraulic Fixed Ratio (HFR) meter, mix and dispense system outfitted with two 100 cc Z-Pumps with Elite™ construction.
- The Z-Pumps metered the material back to the pails, so it could be reused for the next cycle.
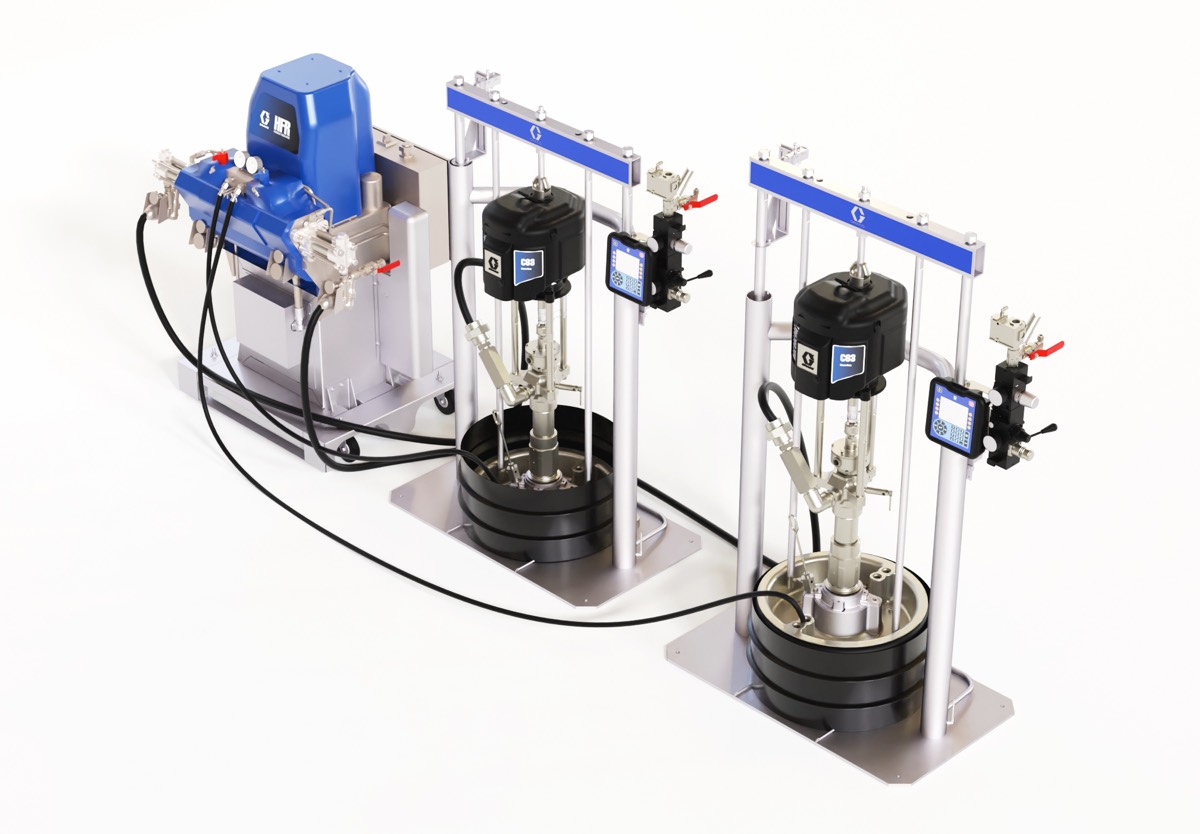
Check-Mate Supply Pumps with Elite™ Construction
- No leakage detected
- Over 190,000 liters of material dispensed
- Grease applied to the throat retainer every 1,900 liters
- No dimensional change or scratching/scoring observed on the pump piston or cylinder
Z-Pumps with Elite™ Construction
- No external leakage observed
- Over 200,000 liters of material dispensed (100,000 on A-side, 100,000 on B-side)
- Grease was applied to the throat retainer cartridge grease cup every 1,900 liters
- Internal piston seals should be replaced at 280,000 cycles
- No dimensional change or scratching/scoring observed on the pump piston or cylinder
- No seal wear detected
- No seat wear detected
Metering CoolTherm SC-1200 2K Gap Filler
LORD CoolTherm® SC-1200 is a two-component (2K) silicone gap filler that provides thermal conductivity for electronic and battery applications.
A typical setup for this material includes supply pumps, a metering system, and a mixing and dispense valve. For this test, the Graco team equipped all components with Elite™ construction.
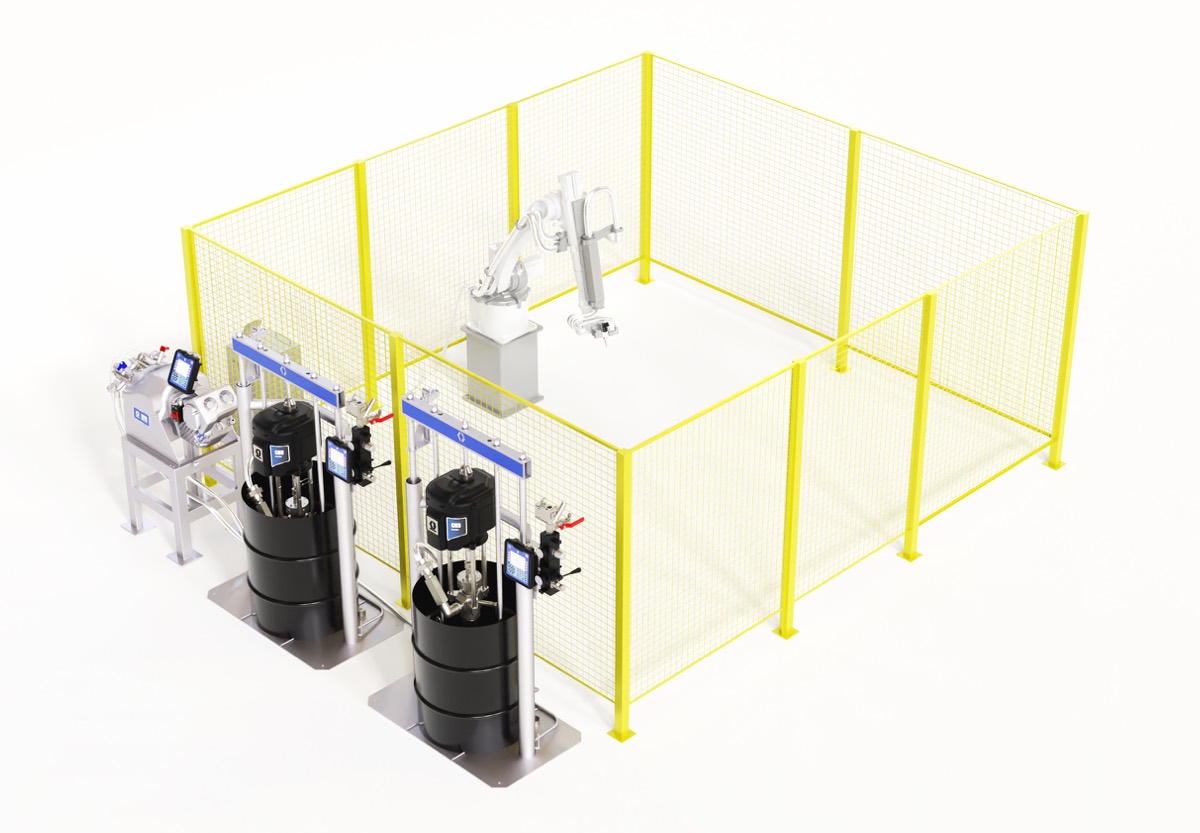
Both the A-side and B-side contained highly abrasive properties, and were supplied in 55-gallon drums.
- Each drum was evacuated by a 200 cc Check-Mate supply pump with Elite™ construction.
- The outlets of the supply pumps were plumbed to the inlet of an Electric Fixed Ratio (EFR) metering system outfitted with 100 cc pumps with Elite™ construction.
- The Z-Pumps directed the fluid back into the supply containers through a forward-acting MD2 valve with Elite construction, so that it could be reused for the next cycle.
- The EFR controlled a 15 cc/sec flow rate at 1740 psi (120 bar).
After nearly five months of running constantly, the test ended. No leakage was detected in any system components with Elite™ construction.
- The MD2 Elite™valves dispensed 10,019.6 gallons (37,924.3 liters).
- Each 200 cc Check-Mate Elite™ pump moved 10,877.1 gallons (41,170 liters).
- The EFR system with two 100 cc Z-Pumps Elite™ dispensed 24,256.4 gallons (91,810.3 liters).
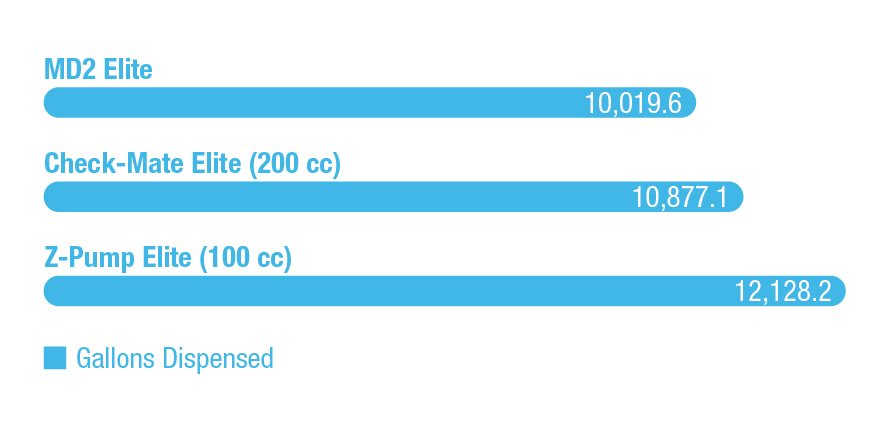
Comparing TIM Blend Compatibility
To compare MD2 Valve models and cycle performance, a representative thermal interface material (TIM) blend** was used to simulate abrasive material blends often used in electric vehicle (EV) battery manufacturing.
The one-component (1K) fluid was made in a 5-gallon pail. A 200 cc Check-Mate supply pump with Elite™ construction moved the fluid out of the pail and into a manifold block. The manifold split the fluid stream into three outputs, each directed to one of these valve models:
- MD2 hard seat with standard construction
- MD2 snuff back with Elite™ construction
- MD2 forward acting with Elite™ construction
Test results showed a clear difference in cycle performance between standard and Elite valve construction.
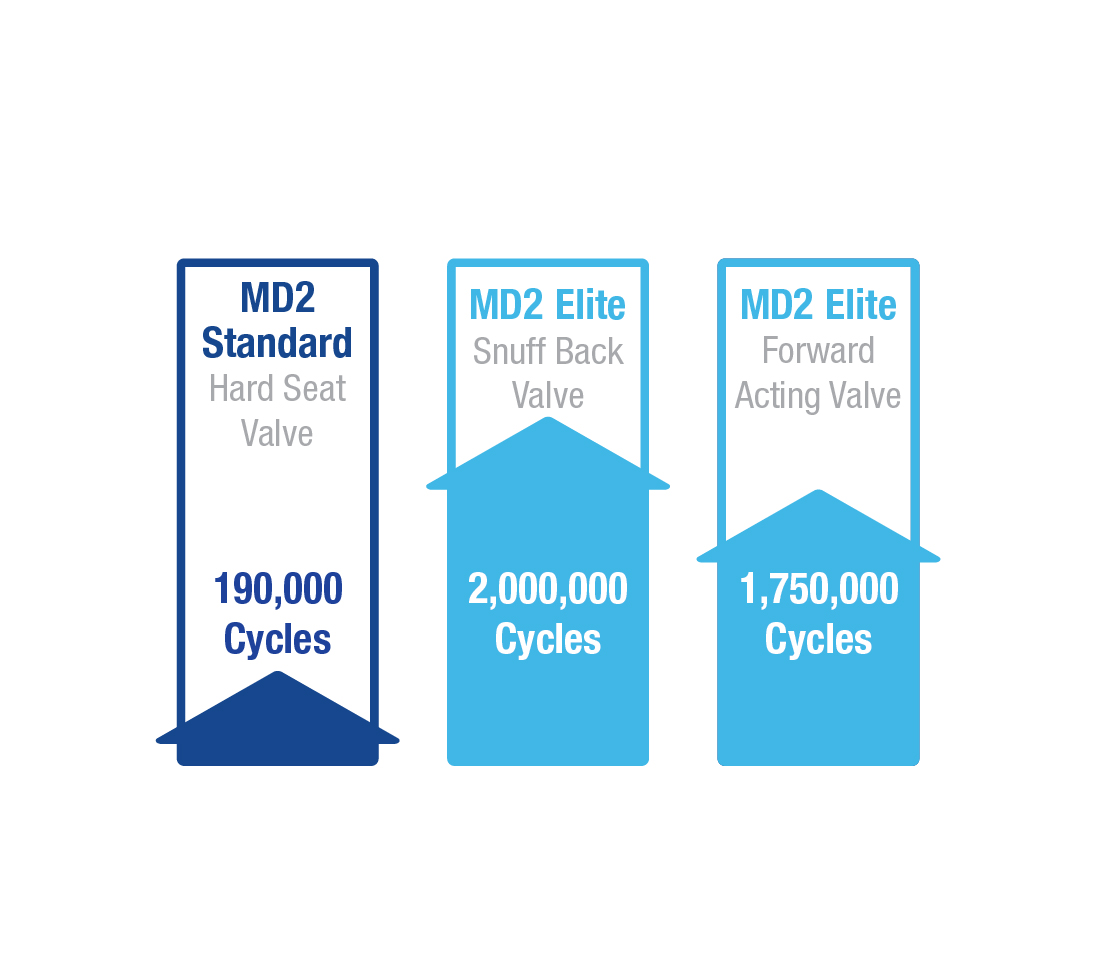
MD2 Standard Valve - Hard Seat
- Used to establish a reference baseline for the test
- Leakage detected after only 190,000 cycles (about 250 liters)
MD2 Elite™ Valve - Snuff Back
- Valve tested to over 2 million cycles (about 2,750 Liters)
- No failures detected
MD2 Elite™ Valve - Forward Acting
- Tested to over 1.75 million cycles (about 2,400 Liters)
- No failures detected
** Blend included 80 percent aluminum oxide AI2O3 and 20 percent silicone oil carrier fluid.
Contact Us
Graco Elite™ is a clear choice when you need dispensing equipment that holds up to the most abrasive materials. Contact us to solve your challenging dispense applications.
Related Materials
Bondway 8868
Bondway 8868 is a two-component thermal interface material (TIM) used for high bonding strength, and good thermal conductivity.
LORD CoolTherm SC-1200
Since CoolTherm® SC 1200 thermally conductive silicone gap filler is highly abrasive, Parker LORD® asked Graco to find out how to dispense one million shots of the two component material without equipment failure.
Related Resources
Comparing 2k Meter Mix Dispense Systems
Chart compares advanced two-component meter mix dispense (MMD) systems, including PR-X, PD44, PR70, EFR, and HFR.
Battery Pack Seal - EV Battery
A quality seal is critical for the performance and longevity of EV batteries and for protecting integral components from water intrusion and other harsh environmental conditions.
Controlling Excess Heat
Proper heat dissipation keeps electronic components running optimally.