How to Lower Compressed Air Costs in Your Factory’s Paint Mix Room
More efficient agitator motors and pumps can cut energy bills – and improve the environment.
Top 2 Ways to Cut Costs Involve Agitators and Pumps
Every factory is different. But most have this in common: the need to save energy costs. It not only supports good profits, it’s also good for the environment.
For established manufacturing plants, cutting energy bills means taking a hard look at their compressed air system. Where can you use less air? The answer often points to the paint mix room.
The top two ways to lower compressed air use – and energy costs – in your industrial paint kitchen involve agitators and pumps.
1. Agitate material more efficiently
Out of any paint mix room equipment, agitator motors usually use the most air. This makes efficient industrial agitators an important part of your paint circulation system.
Graco equipment uses three types of agitator motors. Each has its pros and cons when it comes to compressed air use and cost.
Rotary vane air motors
Many factories with compressed air or pneumatic systems use rotary vane air motors.
Pros:
Used for decades in finishing industry, their initial cost is the lowest of the agitator motor types. Rotary vane motors run the most efficiently at medium to high speeds (typically above 1,000 rpm). Speed can be regulated manually or with a pneumatic speed controller. When paired with a high ratio gear reducer (which slows down speed and increases torque at the agitator blade), rotary vane air motors are ideal for mixing high viscosity material.
Cons:
Rotary vane motors run less efficiently and use more compressed air at speeds ideal for many industrial paint materials (typically <500 rpm). Daily lubrication to the motor is often required. They’re also known for being loud.
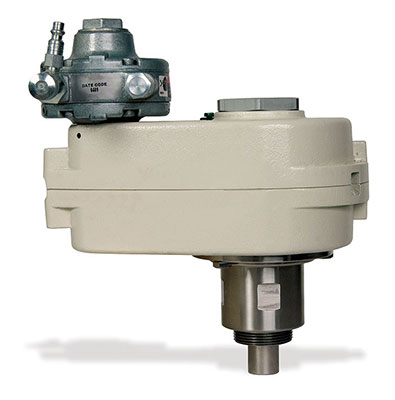
Radial piston air motors
Finishing operations with moderate budgets can easily upgrade to radial piston air motors.
Pros:
Compared to rotary vane motors, radial piston air motors often consume one-third or less air. They also run much more quietly.
Radial piston air motors run the most efficiently at low to medium speeds (<500 rpm). This makes them ideal for agitating most industrial coatings (up to 1,000 cp) in direct drive mode. When paired with a low ratio gear reducer (which slows down speed and increases torque at the agitator blade), they're ideal for mixing high viscosity material.
Radial piston agitator motors do not require air lubrication, supporting clean industrial paint kitchen operation.
Cons:
Efficiency decreases at speeds higher than 500 rpm.
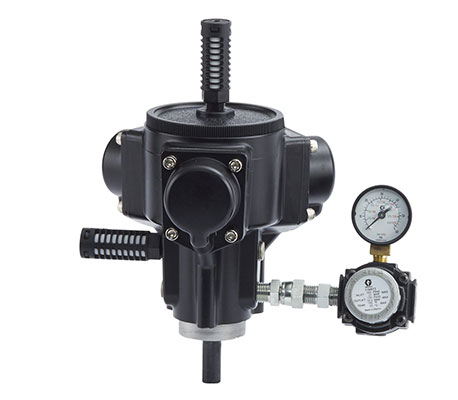
Electric agitator motors
Electric agitator motors are most commonly used in industrial paint kitchens that are in the process or have already moved from pneumatic to electric control.
Pros:
Switching from a pneumatic to electric paint circulation makes compressed air available to other parts of the factory. Electric agitators are up to five times more efficient than pneumatic agitators and have the quietest motors.
Cons:
Since electric agitator motors have the highest initial cost, it may take longer to gain a return on investment (ROI) than the other options. To meet safety requirements, electric motors must connect to explosion-proof conduit and wiring.
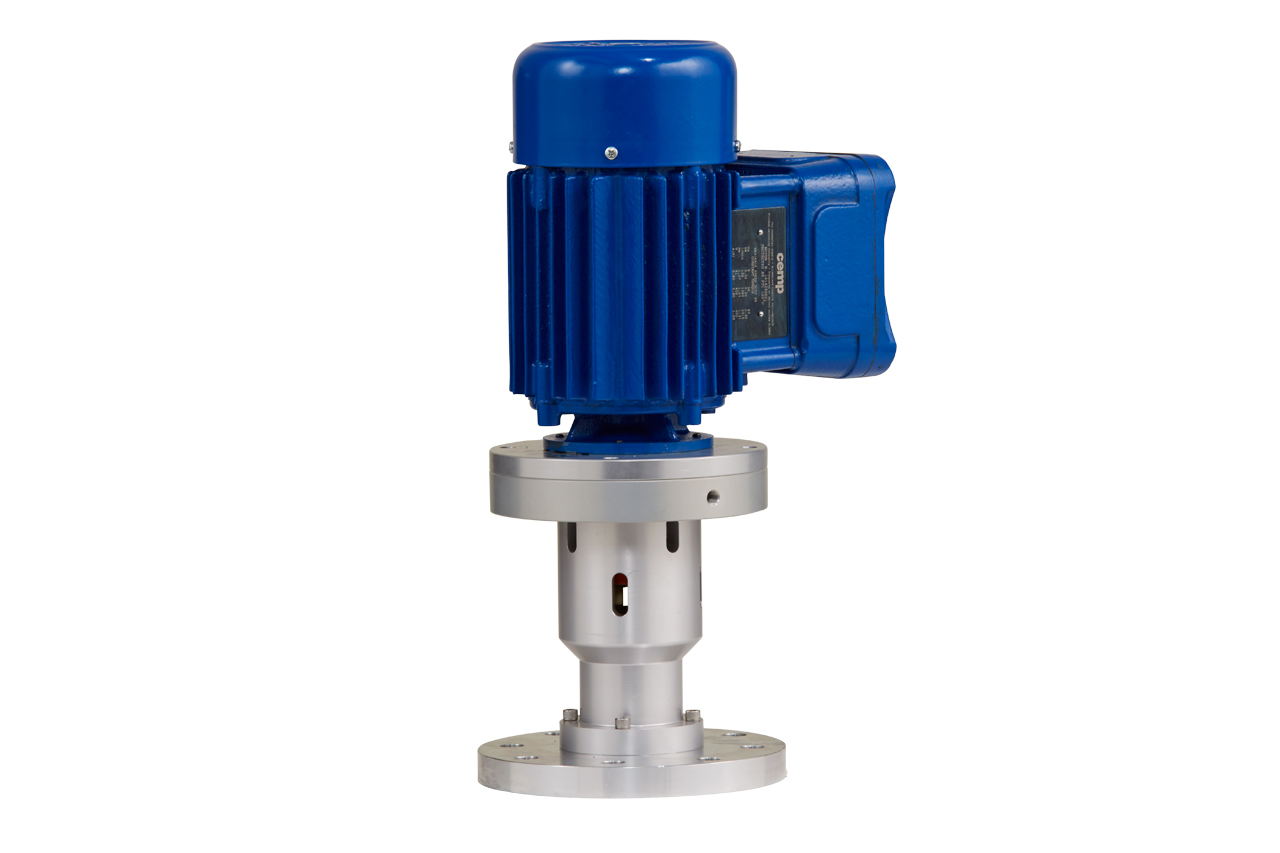
2. Pump material more efficiently
Pumps are the heart of any industrial paint kitchen. Paint circulation system design usually relies on compressed air or electric power.
Pneumatic pumps
Pneumatic pumps use compressed air.
Pros:
They are safe for mixing solvent-based paints or solvent components that cause fumes or VOCs (volatile organic compounds).
Cons:
The cost of running pneumatic pumps goes up with the number or size of air compressors needed. Using compressed air to run paint circulation pumps 24 hours day consequently worsens energy expenses.
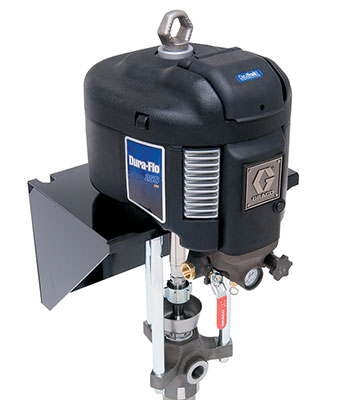
Electric pumps
Electric pumps can run up to five times more efficiently than pneumatic pumps.
Pros:
Since they’re powered by electricity, they make air compressors obsolete. This significantly cuts energy costs.
Factories that have switched from pneumatic to electric paint circulation systems consistently report major savings.
Cons:
Not every plant has the budget to switch to electric.
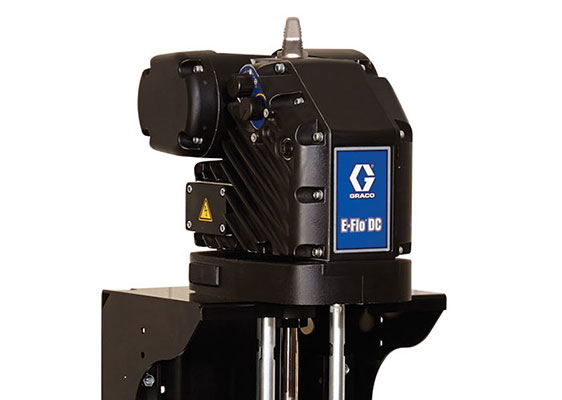
Formerly only available for electric paint mix room equipment, Graco's Intelligent Paint Kitchen technology now applies to pneumatic systems. The ability to remotely monitor and control pump pressure improves efficiency. More efficient pump operation decreases compressed air use – and energy expenses.
Related Articles
Cabinetmaker Decreases Compressed Air Use and Cuts Costs
Radial piston agitator motor uses less air, makes less noise and requires no maintenance.
How to Make Your Factory Paint Mix Room Industry 4.0 Ready
Advanced control and interconnectivity are key components to making factory paint mixing rooms Industry 4.0 ready.
Agitator Motor Supported Locally – Without Hidden Costs
Graco radial piston agitators backed by quality guarantee and A+ Service.
Free On-Demand Webinar
Circulation 101
Choosing the right pump for your application can help reduce downtime, increase production and avoid waste.
This 50-minute webinar covers:
- Tools you can use to verify the right pump and setup for your needs
- Options for traditional pneumatic and electric pump management