Automotive Structural Adhesives Application
Automotive Structural Adhesives Application
Structural adhesive application has been growing in automotive body-in-white (BIW) applications because of ongoing requirements for vehicle weight reduction, increased safety, and increased reliability. High-strength adhesives, combined with mechanical joining methods, can increase automotive structures' rigidity, strength, and fatigue life. Along with more robust, stable structures, other benefits can also be obtained, such as decreased noise and vibration levels.
Precise application of adhesives is key to realizing the benefits they offer. Accurately placed adhesive beads provide optimal bonding at suitable locations. With modern application equipment, manufacturers can achieve this needed accuracy, improving efficiency and decreasing required maintenance on equipment.
Accuracy of Bead
To achieve optimum strength, adhesive beads must be applied at just the right size and location. Insufficient width can result in inadequate strength, while excessive widths can result in material squeeze-out, affecting downstream applications. Similarly, inconsistent beads can hinder proper bonding and result in various performance problems. Well-placed beads have uniform widths and are precisely located, as shown in Figure 1.
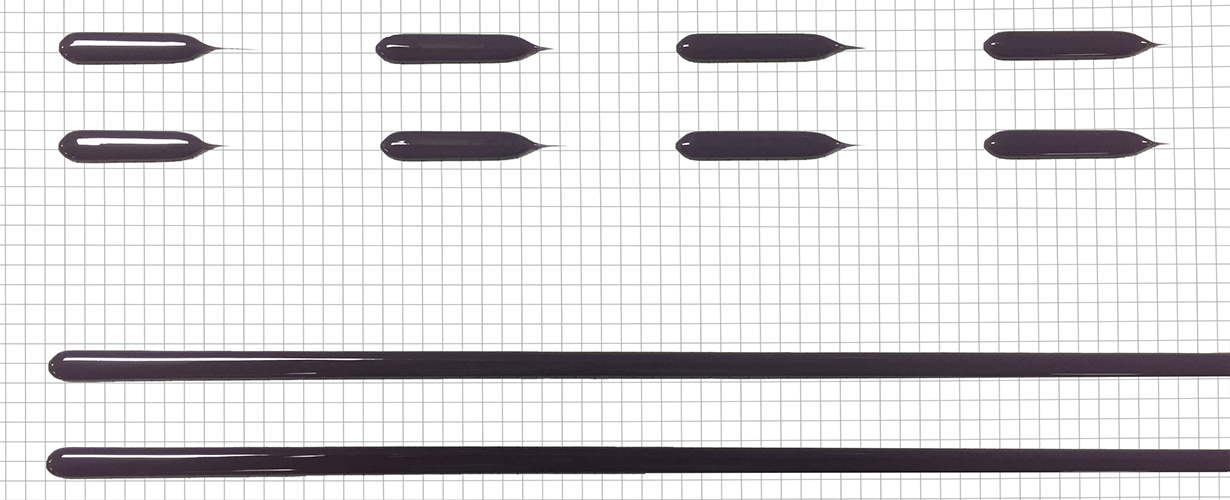
Figure 1.
Because structural adhesives often work in conjunction with other mechanical fastening methods, accurate bead placement is critical to providing a bonded system. For example, precisely placed adhesive beads can be stitched around spot welds to form a hybrid joint that saves adhesive material and cost.
With optimally applied adhesives, the concept of “lightweighting” is more feasible, meaning manufacturers can produce vehicles that use less steel, weigh less, and achieve better fuel efficiency and handling. Vehicle lightweighting strategies also enable the joining of dissimilar materials, such as ultra-high-strength steel, aluminum, and composites. These materials cannot be joined using traditional mechanical techniques, further increasing the value of structural adhesives.
Improved Quality and Precision Without a Metering Device
With traditional adhesive application equipment, a pump typically feeds a shot meter, which controls adhesive placement. These devices can be quite accurate under controlled conditions but are expensive and difficult to maintain when implemented in the plant, where requirements can vary widely.
Modern systems such as the Graco E-Flo iQ eliminate the need for a metering device such as a shot meter. An electric, servo-driven pump is controlled by a system of sensors and controls to dispense material precisely. With the iQ signifying “intelligent flow,” the E-Flo iQ system provides a simple, reliable, tank-to-tip installation, as shown in Figure 2.
Figure 2.
Improved Integration
The E-Flo iQ system can be easily integrated with a robot and programmable logic controller (PLC) controls to improve the overall performance of the manufacturing cell. Performance feedback communicates actionable information, reducing scrap and rework while drastically reducing the maintenance cost of the system.
Reduced Maintenance
The metering device is often the most expensive component in a dispensing system. It is also often the most expensive component to maintain. Because the E-Flo iQ meters material right from the container, maintenance labor is drastically reduced. With a tandem system, the E-Flo iQ can be supported without stopping production.
Summary
Shot meters can provide accurate adhesive placement in a controlled environment; however, due to their complexity, these devices have a high installed cost, rarely deliver sustained in-plant performance, and are expensive to maintain.
For robotic dispensing applications in automotive BIW, the Graco E-Flo iQ sealant and adhesive dispensing system delivers sustained in-plant performance, lowers maintenance costs, and drastically reduces system complexity. This advanced system accurately dispenses material without the need for an additional metering device. Tests have proven that the E-Flo iQ system provides sustainable performance, increases overall equipment effectiveness, and reduces the total life cost of body shop dispensing applications.
Contact an Expert
Related Articles
Anti Flutter Application for Body Shop Closures
Designed to protect the exterior of vehicles and reduce noise during operation, anti-flutter applications are an important step in the automotive assembly process.
Comparing 1k Metering & Dispensing Systems
Shot size and flow rate, material properties, and manufacturing style are important when evaluating the correct metering system for single component sealants or adhesives.
Silicone Sealant for Form-in-Place Gasketing (FIPG)
Engineers and scientists from Graco and Dow Inc. work together to help automaker effectively dispense silicone sealant. Software upgrade improves E-Flo iQ accuracy and consistency with all high yield stress sealants.