Reduce Energy Consumption by 36 percent
Testing proves that dispensing low application temperature (LAT) hot melt adhesive with the InvisiPac HM10 means more efficient cardboard packaging.
Precisely, how much energy can be saved when dispensing a high performance low application temperature (LAT) hot melt adhesive with the InvisiPac® HM10 melt-on-demand system?
An adhesives solutions company asked the packaging experts at Graco's Customer and Innovation Center in Maasmechelen, Belgium, to find out.
Their comparison of lower and standard temperature applications showed a 36 percent savings on energy costs. Let’s have a closer look at the lab test setup, process, and results.
Equipment and Application Setup
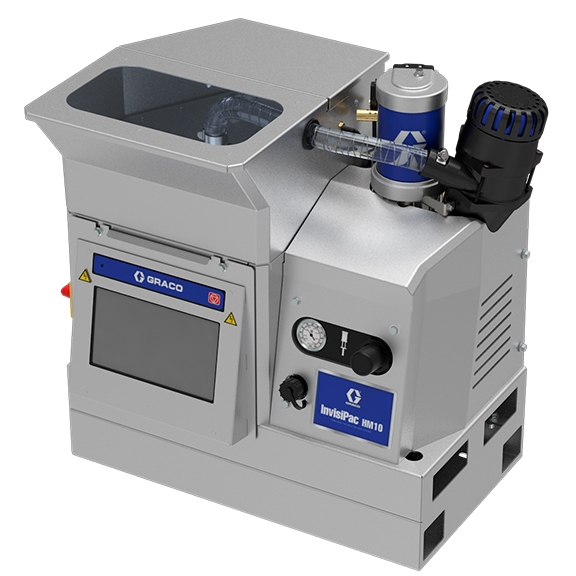
The tests used the InvisiPac HM10 Tank-Free™ melter with on-board hopper to compare low and standard temperature hot melt adhesives.
- For the low temperature adhesive, temperature settings for the melter, hose, and gun were 110° Celsius (230° Fahrenheit).
- The tests for the standard temperature adhesive application were carried out at 160° C (320° F).
The hot melt adhesive consumption was ~ 1,7kg/h.
Startup and Production Testing
Application lab engineers monitored how much energy it took to heat up the hot melt adhesive to the right temperature and keep it at the right temperature throughout production.
Heating Up Hot Melt Adhesive
How much energy was consumed to get the adhesive ready to be dispensed? And how much time did it take?
This comparison shows you can save up to 39 percent on your energy bill during the start-up phase. On top of that, your system can start operating 5 minutes faster.
Standard temperature adhesive | Low application temperature (LAT) adhesive | |
Energy consumption | 440 Wh | 270 Wh |
Start-up time | 13 minutes | 8 minutes |
Maintaining the Perfect Temperature
The production phase focused on how much energy it took to maintain the adhesive at the perfect operating temperature.
In the energy consumption graph below, the vertical axis shows watt-hour (Wh), the number of energy units used in an hour. The horizontal axis shows the number of minutes needed to keep the adhesive at the right temperature.
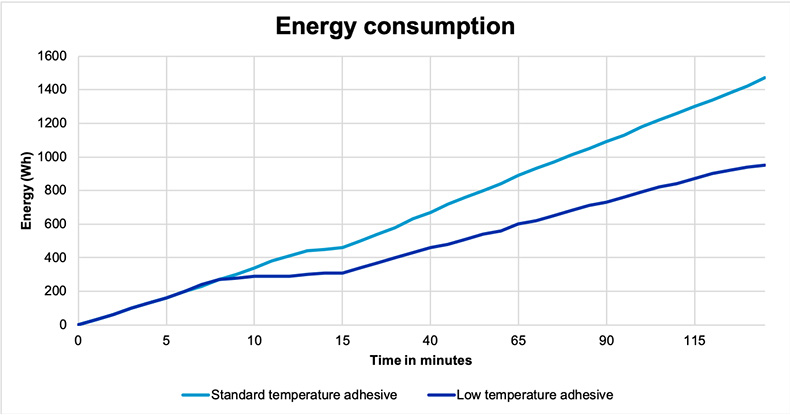
The production testing results in the graph above, show a 36 percent total energy savings.
- The dark blue line shows that the low application temperature (LAT) hot melt adhesive clearly outperforms standard temperature adhesive. Where the light blue line keeps climbing at the same pace, the dark line rises less rapidly.
- At around the hour mark, it takes up to 800 Wh to maintain the standard temperature adhesive at the right temperature. In contrast, the LAT adhesive remains below the 600 Wh mark.
What Does This Mean for Your Cardboard Packaging?
In short, if you are still dispensing a non-LAT-adhesive or using a tank-based hot melt system, you are losing time and money.
By switching to InvisiPac Tank-Free™ hot melt delivery, you can save up to more than one-third on energy, lowering energy bills and reducing your packaging line's carbon footprint.
For a more detailed look into the hot melt adhesive testing setup or results, fill out the form below.
All trademarks and registered trademarks are the property of their respective owners.
Related Articles
The Cost of Hot Melt System Cleaning & Maintenance
Maintenance costs can quickly add up. Avoid unplanned downtime and replacement parts costs.
Fruit Packager Seals Cardboard Boxes with 64% Less Glue
The hot melt delivery system for a large fruit packaging house was causing major problems. The packaging manager explains how InvisiPac reduced costs and liability issues.
Refresco Achieves 45% Hot Melt Adhesive Savings
An operations manager and engineering manager for the world's largest independent bottler of beverages share how they reduced hot melt adhesive use by 45%. Since their factory yearly packages 1 million liters of soft drinks and juices, that is a lot of money.