Industrial Networking 101: A High Level Overview
How does equipment in a factory spray line, dispense line, or other assembly line know what to do and when? This video gives a birds-eye view of how industrial networking and automation works.
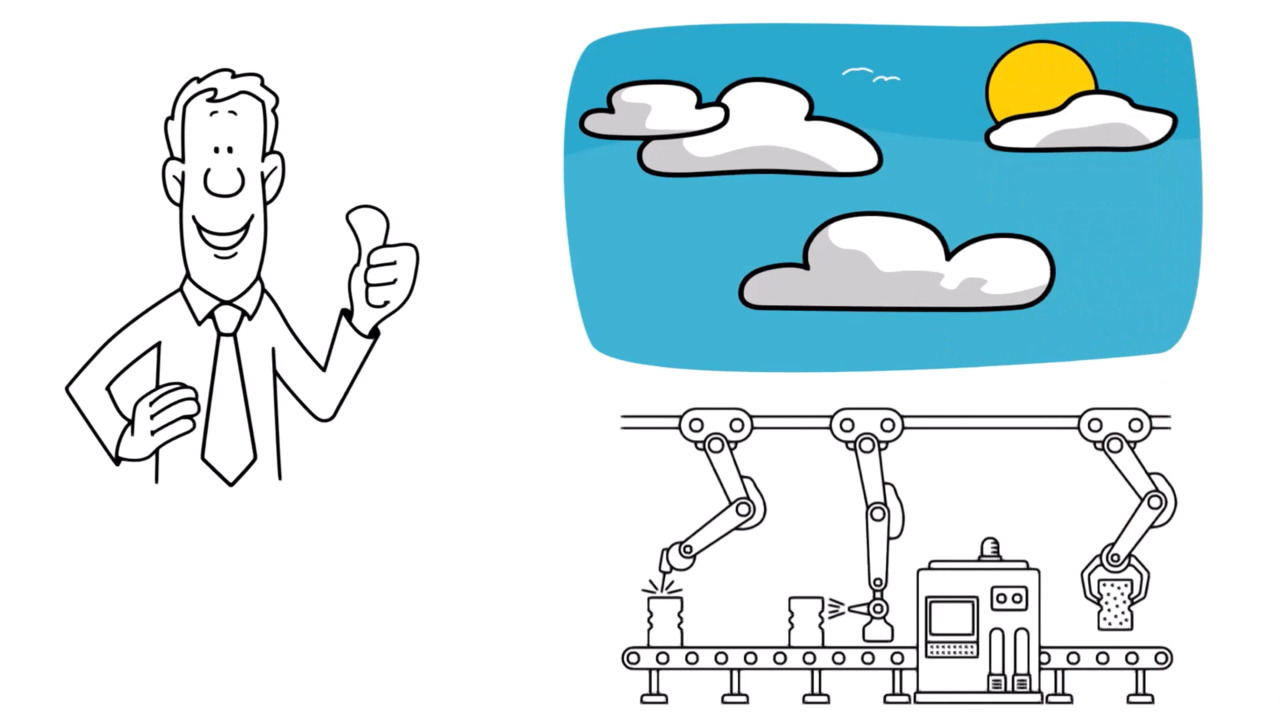
Ever wonder how equipment in a spray line, dispense line, or other assembly line just know what to do and when? The process is known as industrial networking and automation.
These answers to basic questions about how industrial networking and automation works should help you gain a birds-eye view.
What is Industrial Networking and Automation?
Industrial networking and automation refer to the systems and processes that enable various pieces of industrial equipment to communicate with each other and with human operators. This helps streamline manufacturing processes, improve efficiencies, and reduce human error.
What is a PLC?
Industrial networking starts with the central brain or hub of the system: the PLC, or programmable logic controller.
A PLC is a small computer running a program that integrates and controls all external components of an industrial system, such as an assembly line. The program tells each component what to do, when to do it, and what data to provide back.
How Does a PLC Control an Industrial System?
The programmable logic controller (PLC) runs a program that integrates and controls external components of an industrial system, such as an assembly line. The program instructs each component when and how to perform tasks, as well as what data to provide.
- PLCs contain digital and analog inputs and outputs that connect to sensors in the system, such as a proximity switch or a level sensor on a tank of material.
- The PLC collects data from these sensors and communicates it out to the rest of the system by using a typical Ethernet-based network port connected to a network switch.
What is a Network Switch?
A network switch serves as a shared network port that connects all equipment within the industrial system. For instance, sensors, motors, robots, and other devices can communicate with the network switch to coordinate their actions.
A network switch is essentially like the router in your home connected to your computer, printer, smart TV, phone, and tablet.
How Do a Network Switch and PLC Control an Assembly Line?
To answer that question, let’s take a closer look at how a network switch and programmable logic controller (PLC) communicate with the components of a basic industrial assembly line.
A typical assembly line has a conveyer belt with position sensors that communicate with the network switch.
It also has a motor controlling the position of the conveyer belt that’s attached to a variable frequency drive (VFD) that also communicates with the network switch.
It probably also has a robot placing parts. That robot also communicates with the same network switch.
When we add Graco equipment to the assembly line, it also communicates with the same network switch.
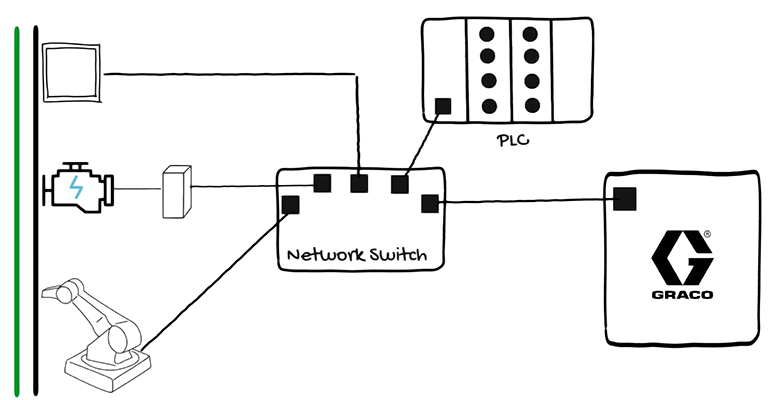
Like many other pieces of Graco equipment, the InvisiPac HM10 hot melt adhesive dispense system contains a communication gateway module (CGM) with an Ethernet port connected to the network switch.
It also contains a control board and an advanced display module (ADM), Graco’s version of a human-machine interface (HMI). All of those components communicate with one another over a CAN bus cable.
What is a Communication Gateway Module?
The communication gateway module (CGM) is the main communication device. It communicates with the control board, runs equipment software, and communicates with the advanced display module (ADM).
An essential component of industrial networking, the CGM enables seamless communication between different systems and protocols. It consolidates data, streamlining the flow of information and minimizing complexity.
The CGM provides a means for exchanging data with external interfaces, enabling remote monitoring and control.
Why use PLCs for Industrial Networking?
Using programmable logic controllers (PLCs) to set up industrial networking allows for centralized control and integration of different parts of an industrial system.
With PLCs, you can automate processes, enhance efficiency, gather data from sensors, and ensure seamless communication between devices. This can lead to improved productivity, reduced downtime, and easier maintenance of the overall industrial system.
What Does a PLC Programmer Do?
A programmable logic controller (PLC) programmer uses a computer that either communicates through the same network switch or is connected directly to the PLC, and PLC software (typically provided by the PLC manufacturer) to write a program that runs on the PLC.
As many PLC programmers would most likely tell you, programming a PLC is extremely time consuming.
To save programmers precious development time, Graco has developed software development kits (SDKs).
Customers and integrators who utilize SDKs save a significant amount of development time - in some cases up to four weeks.
What is an SDK and How Does It Work?
A software development kits (SDK) a collection of files containing code tailored for a specific PLC software environment.
This code provides building blocks in the correct format that provide built-in logic. For example, it can show how to trigger an action, such as change spray recipes, or collect data from external devices.
SDK files are available on help.graco.com as downloadable zip files.
After a PLC programmer downloads and unzips a specific SDK file, they simply import the files into their software environment and make adjustments to the code as needed for their specific application. This can save them weeks of development time.
Contact Us
Connect with someone who can help you determine your industrial networking needs.
Related Articles
Intelligent Control Improves Productivity for Tier 1 Supplier
Paint technicians are happier with more productive activities than manually monitoring an otherwise automated system.
Pneumatic Pump Control and Hybrid Mode Resolve Shift Change Problems
Intelligent Paint Kitchen advances automation and quality for agricultural equipment manufacturer.
How to Make Your Factory Paint Mix Room Industry 4.0 Ready
Advanced control and interconnectivity are key components to making factory paint mixing rooms Industry 4.0 ready.