Hem Flange Bond in Automotive Closure Assemblies
Hem Flange Bonding
Hem flange bonding is an application method where adhesive bonds inner and outer panel edges in automotive closure assemblies such as metal hoods, doors, trunks, or tailgates. This automotive panel bond of two thinner panels offers considerable weight savings over a single, thick panel. The precision of automotive hemming is essential to improve crash safety, prevent corrosion, and perfect appearance.
The Automotive Hemming Process
The flanging process happens in the body shop manufacturing process before painting. It begins by securely positioning the inner and outer sheet metal panels. The hemming adhesive is then dispensed on the outer panel, typically in a bead or swirl application, and bent or folded over the inner panel. The adhesive is pressed to spread and fill but not squeeze out of the bond line (between the panels), forming the hem flange bond. This process allows for more noise-resistant, vibration-resistant, impact-resistant car closures.
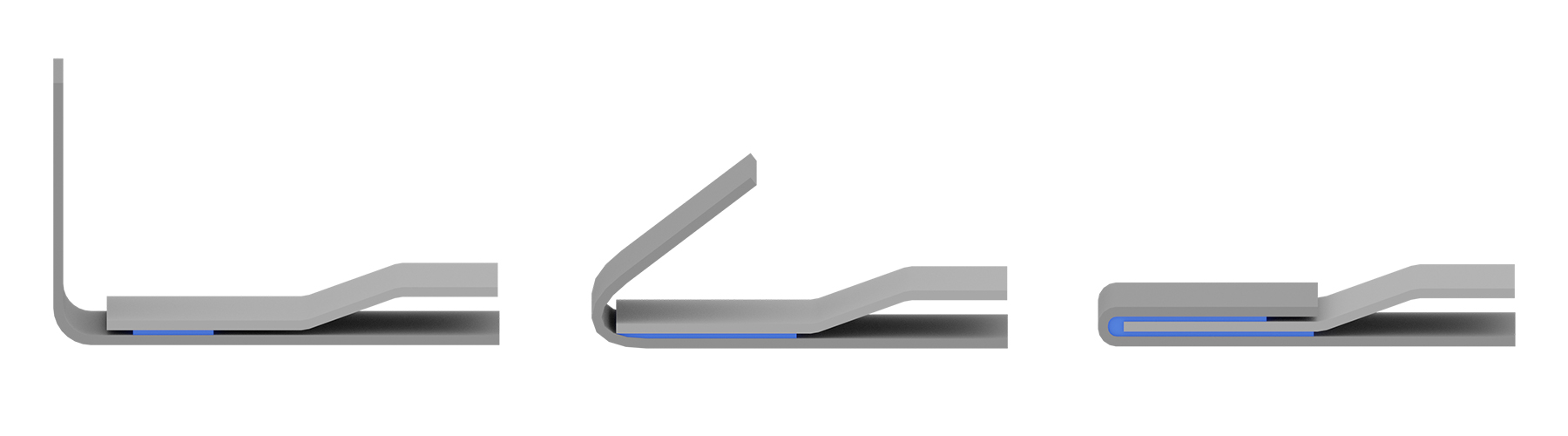
Panel Adhesive Dispensing
The most critical factor of hem flange bonding is precisely filling the hem between the two panels. An epoxy adhesive, often filled with glass beads, is the specific hemming glue used to create a consistent thickness between the panels to adhere and seal the two sheet metal panels properly. There are two optimal application methods of epoxy adhesives in hem flange bonding: a traditional bead application and a swirl application. Accurate bead size and dispense need to be carefully controlled to secure the bond while maximizing adhesive usage.
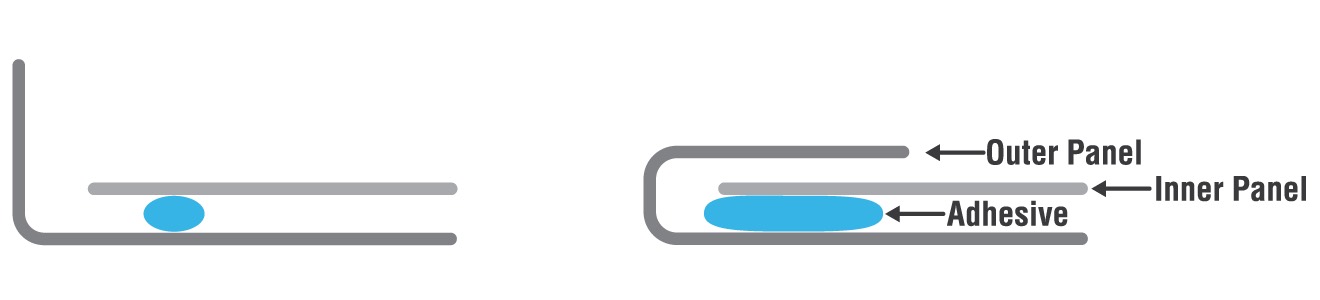
Challenges of Automotive Hemming
Hem flange bonding can be considered a challenging application in automotive construction. If the sheet metal hem is insufficiently filled or adhesive is not precisely distributed on the inside, the stability of the bond can be compromised. Additionally, if excess hem glue squeezes out, the equipment would be contaminated, causing cleanliness and maintenance issues within the manufacturing plant. It is imperative to have a flexible application solution to execute automotive panel bonding effectively.
Summary
Proper material dispensing and distribution will determine the quality and structural stability of the car body. Graco offers several solutions to perform high-quality sheet metal hemming. Our one component metering systems provide greater control when applying a uniform bead or swirl pattern. We can precisely dispense to your desired bead pattern, width, and thickness to meet your application needs while minimizing downtime and ultimately reducing the costly rework of parts and maintenance. See our configured one component metering system solutions below:
Contact an Expert
Related Articles
Why Electric Motors Improve Quality and Precision of Dispense for 1k Metering
Electric motors have the capability to drive the pump lower more intelligently and therefore dispense an accurate bead without the need for an intermediate metering device.
Lightweighting in Manufacturing Processes
Lightweighting is a modernized, cost-effective manufacturing concept that is proving superior to old methods. Find out about additional benefits and how lightweighting can bring auto manufacturing to the next level.
Four Reasons Why Electric Motors Are the Greener Solution
Industrial manufacturing companies are moving from air to electric to reduce their costs and environmental footprint.