Large EV Manufacturer Increases Flexibility in Production Process with Customized System
Customized system adds flexibility to electric vehicle (EV) battery production process.
Background
A large electric vehicle manufacturer needed a more versatile battery encapsulation system. They wanted to change their process to use variable ratio meter-mix dispense equipment.
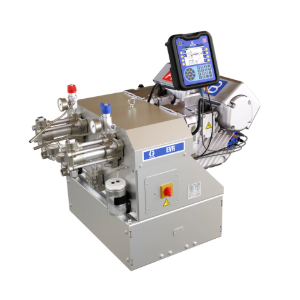
The Challenge
The manufacturer asked for our help designing the system that they needed, and they were on a very tight timetable. The development process was demanding, because there was a lack of clarity about some of the components they needed until late in the schedule. In fact, some of the key elements were designed after development began.
Our Approach
The Graco engineering team partnered with our customer to create a system that met their needs. We proposed an EVR (Electric Variable Ratio) system that allows mixing, metering, and dispensing a variety of two-component materials with the same equipment. The result was a customized system that gives our customer’s production process more flexibility, and shipped ahead of schedule.
EVR (Electric Variable Ratio) System
- 480 volt 3-phase power supply
- Graco G3 Electric Grease Pump to Auto Grease Z-Pumps
- Heated Hoses with Integrated Heat Controller
- Mass Flowmeters for ratio monitoring
- Automatic Inlet Ball Valves for Material Inlets from customer bulk supply
- Recirculation for B Side Material
- Entire System Controlled By One ADM
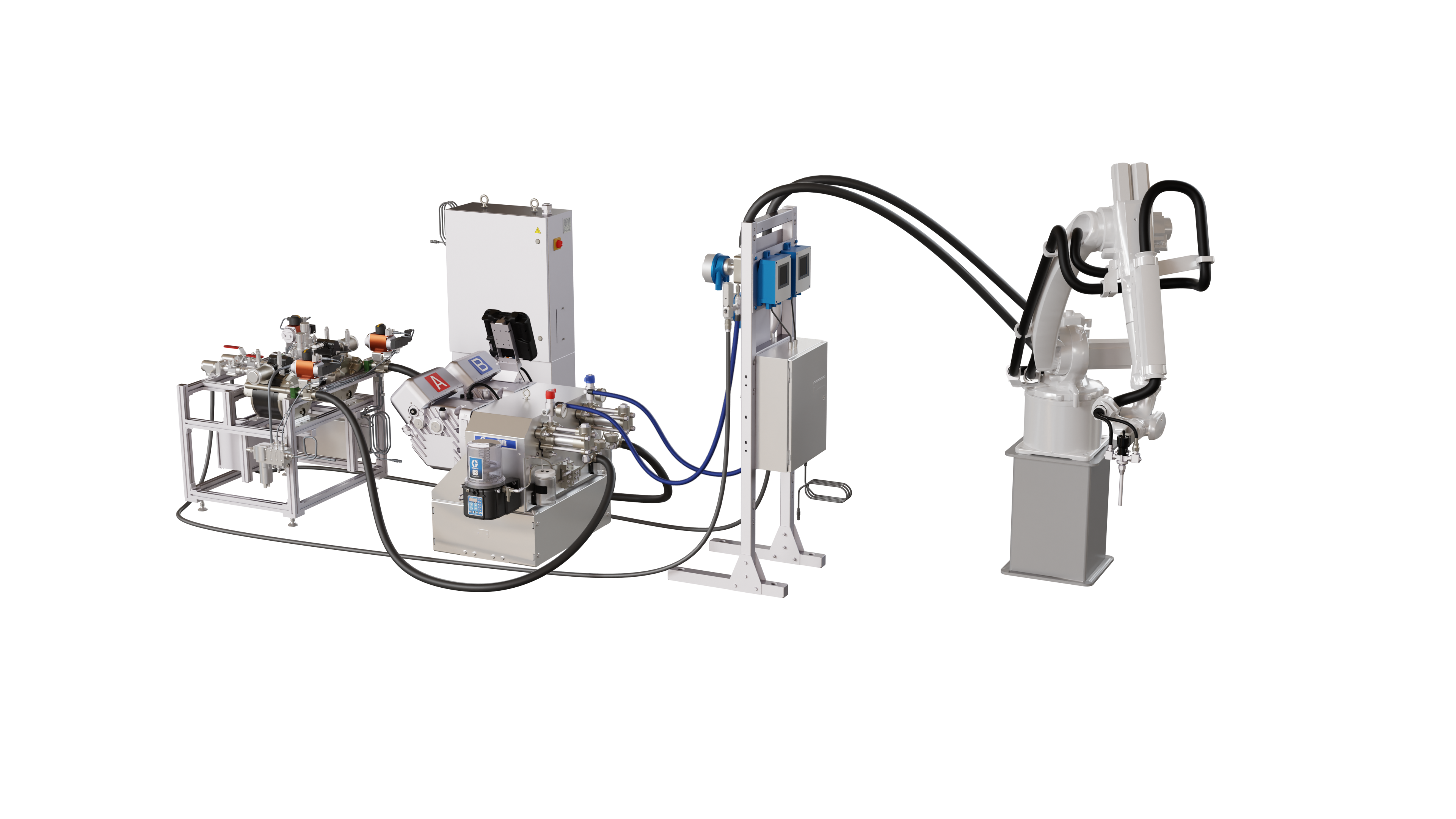
Custom-engineered major components to create a specialized solution:
- Inlet assembly – automated ball valves for A side, B side, and recirculation
- Coriolis mass flowmeters for ratio monitoring
- Heat control box
- 480-volt EVR with automated Z-pump greasing
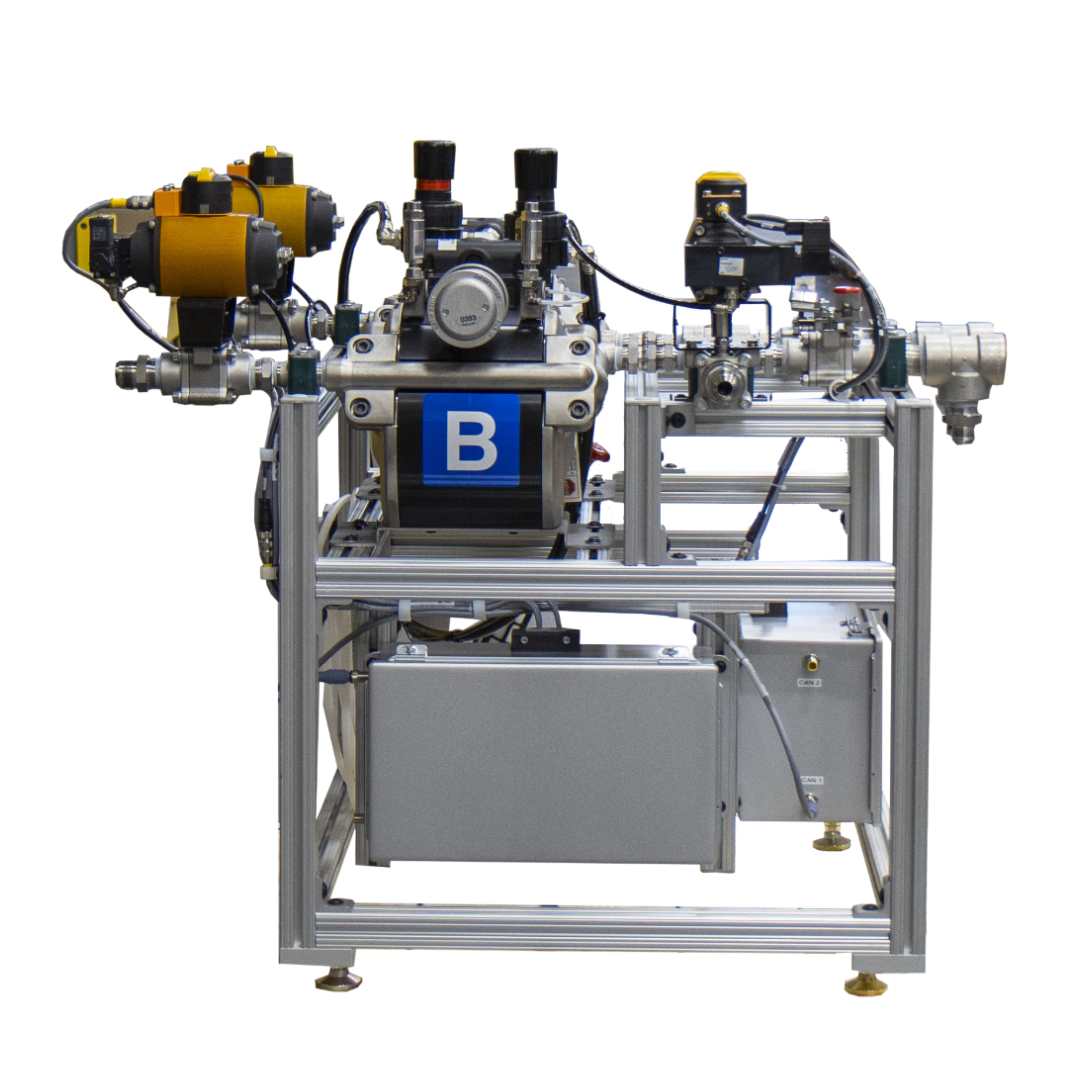
Inlet Assembly
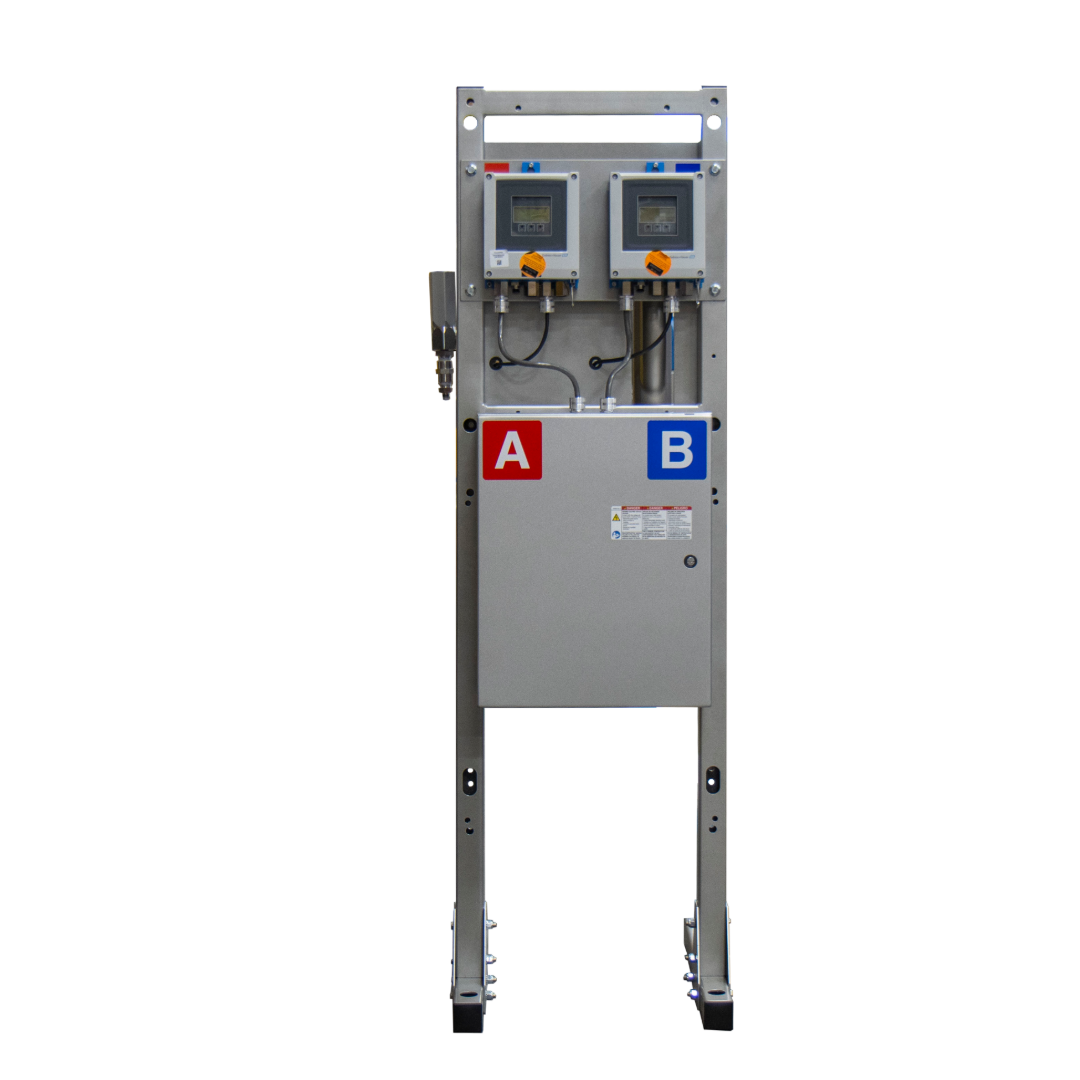
Flowmeters
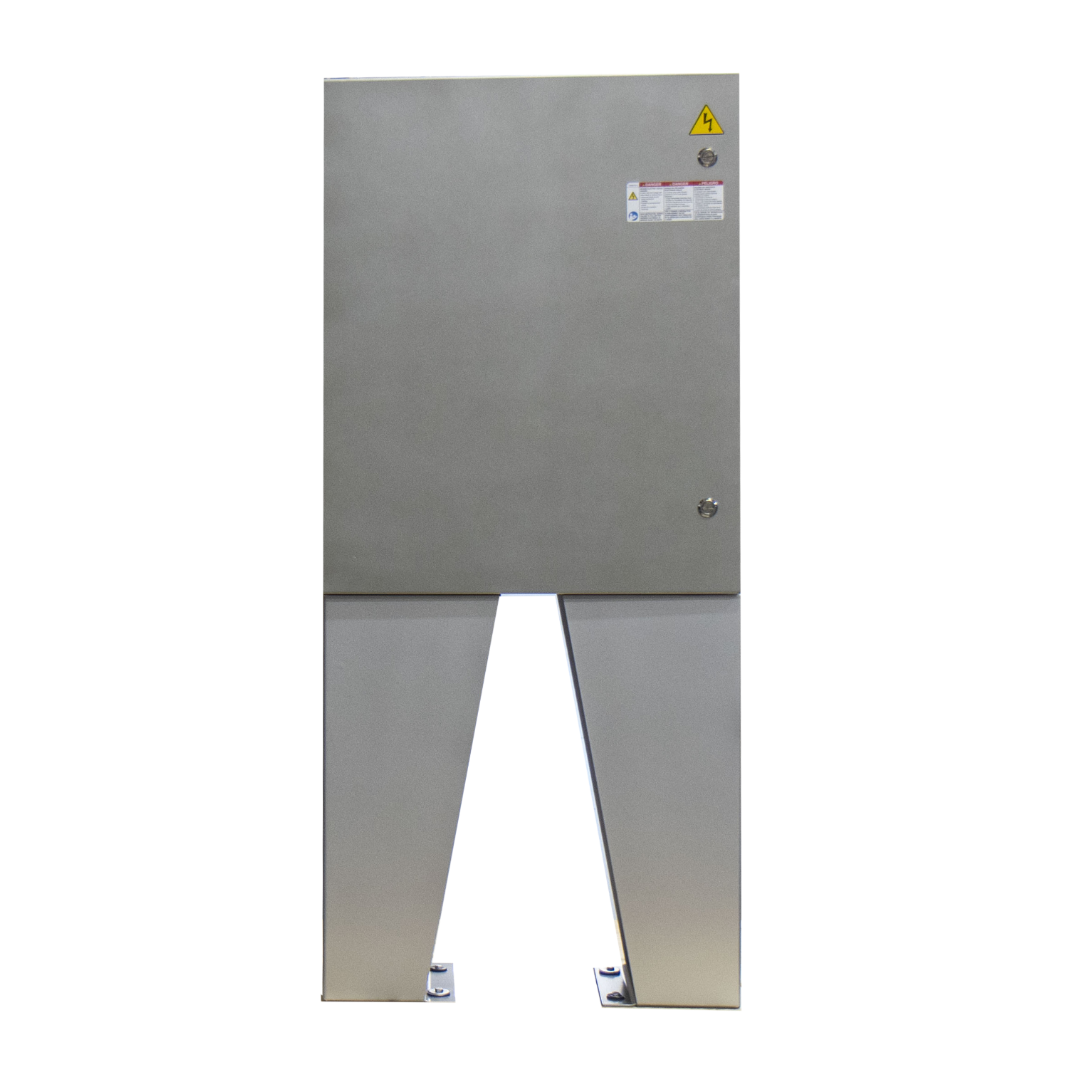
Heat Control Box
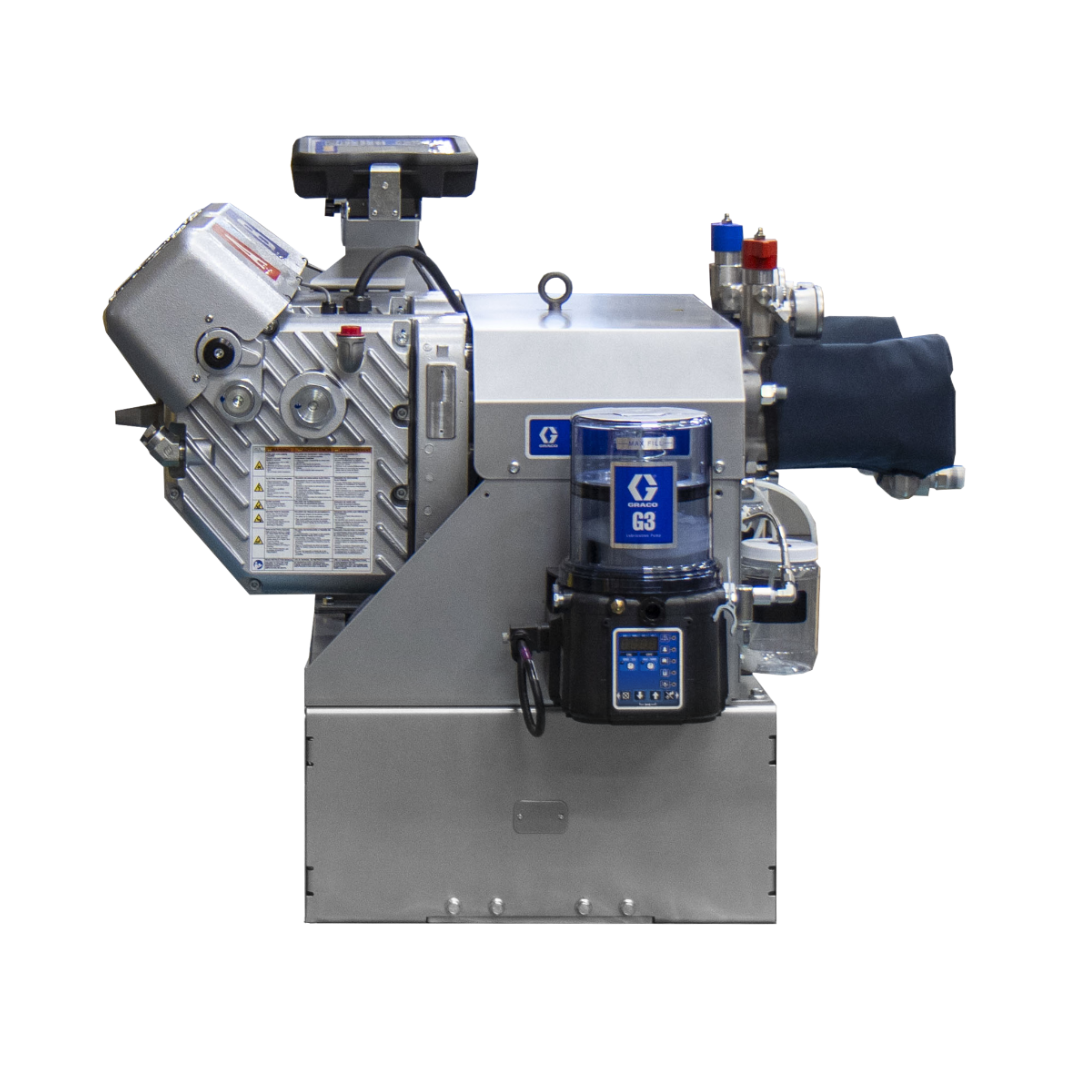
EVR
Outcome
Our manufacturing client needed many specialized components, on a very tight timetable. Working together, we created an integrated system that solved our customer’s issues and shipped the first unit in only 18 weeks.
CONTACT EV BATTERY EXPERTS
We understand the complexity of electric vehicle (EV) battery designs, and how material application affects their manufacturability and ability to mitigate thermal runaway events. We look forward to collaborating with you.
"This customer asked for a lot of specialized components, delivered quickly, and our engineering team really stepped up and created a solution. Even though design and build for some components happened after we took the order, we shipped the first unit only 18 weeks later."
-Mike Bozzelli
Related Articles
Extreme Material Abrasiveness? Problem Solved with Elite
Some thermal interface materials (TIMs) are so abrasive, it’s like pumping diamond dust or liquid sandpaper. Explore why and how we developed Elite™, the longest-lasting pump construction for abrasive material dispense.
Foam Encapsulation of Cylindrical Cells
Careful attention to thermal management and foam encapsulation are important to manufacturing high-performance battery modules that remain safe in any circumstance.
Manufacturer Optimizes EV Battery Foam Encapsulation Process
An EV battery manufacturer had to determine the best foam encapsulation process for a new cell module design. Quick collaboration with Graco put it into production by a critical deadline.