What to Consider When Selecting a Hot Melt System
5 Questions to Ask When Buying Equipment
One of the biggest weaknesses in many traditional hot melt adhesive systems is the melting process, where tanks heat the adhesive. These tank-based systems take a lot of time to heat the material and generate adhesive char, leading to plugged hot melt nozzles and equipment failure.
Some new hot melt systems utilize specially-designed heating chambers with a significantly improved surface to adhesive ratio for fast, efficient melting. Buyers must educate themselves to ask tough questions and ensure they are getting reliable, efficient equipment that will drive profitability over the long term.
Before making a hot melt equipment purchase, be sure to ask these questions:
1. Are you able to track system performance?
2. How safe is the system for packaging equipment operators?
3. Is the hot melt system able to provide you operational savings?
4. Can you depend on the hot melt system for consistent quality?
5. How much maintenance is required?
1. Are you able to track system performance?
If you don’t know how much adhesive you are using, you will never know how much you are wasting. The ability to monitor all critical performance metrics such as temperature, production levels, and adhesive usage allows you to optimize overall equipment efficiency further. Remote monitoring of system performance is an additional element of a complete packaging solution to get real-time line updates 24/7.
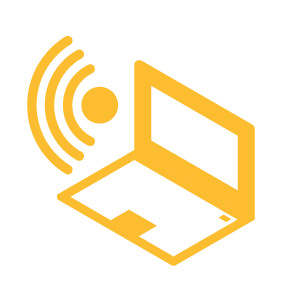
2. How safe is the system for packaging equipment operators?
Working with hot melt systems can be dangerous. Operators are at risk of burns when in close proximity to the heated system components along with the melted adhesive while working with tank-based and tankless systems. Inhaling toxic fumes from melted adhesive is also a common risk when operating hot melt equipment. The development of automatic feeding for transferring adhesive now allows operators to avoid direct contact with hot melt material and eliminate these hazards. We recommend checking to see if switching to an automated feed system is an operation for your manufacturing process.
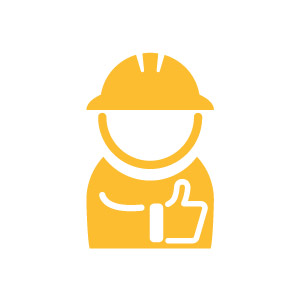
3. Is the hot melt system able to provide you operational savings?
The selection of the right hot melt system can not only offer you high-quality results but can also contribute to savings in the following ways:
Adhesive savings: When comparing hot melt systems doing the same application, the amount of adhesive each system uses is different. This all depends on the way the system is handling/maintaining/treating adhesive quality throughout the operating process. If the selected hot melt system keeps the adhesive viscosity constant throughout the line, the system will dispense a consistent bead of adhesive on every box. If not, the amount of adhesive dispensed will fluctuate, resulting in big differences in the adhesive used.
Maintenance savings: Every hot melt system requires preventive maintenance. However, most of the maintenance performed on a hot melt system is unplanned and caused by adhesives charred inside the tank, hose, or applicator/nozzle. Selecting a hot melt system that minimizes charring will provide important savings in maintenance.
Time savings: Adhesives need to be heated before dispense. The time needed to get the system up and running depends on the size of the reservoir and its melting surface. Hot melt systems with the highest melting surface ratio (melting surface vs. adhesive volume) will start up much faster and increase your production time.
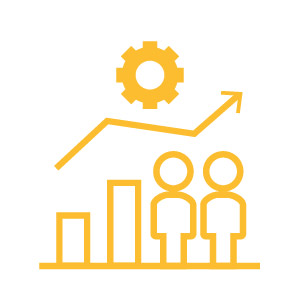
4. Can you depend on the hot melt system for consistent quality?
Having a reliable seal on every box is crucial. Inconsistency in dispense can not only result in the quality of the seal but also bring costly re-work. It is important to understand how the hot melt system is handling the adhesive quality from the melter to the applicator to ensure high-quality results. If a system is more likely to create char or cause thermal shock, it is more likely to see quality fluctuate when dispensing adhesive. When char forms, it will start creating blockages in the melter, hose, or nozzle, resulting in inconsistent beads. On the other hand, thermal shocks change the viscosity of the adhesive, which could lead to differences in dispensed adhesive per box. To guarantee high-quality results throughout, your hot melt system needs to avoid charring and keep adhesive temperature as constant as possible from melter to applicator.
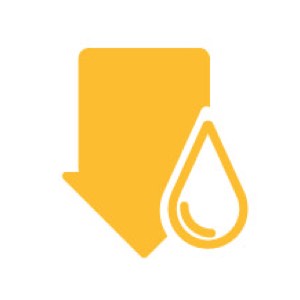
5. How much maintenance is required?
The amount of maintenance a hot melt system requires is directly linked to the way a system handles the adhesive. If a system is keeping hot melt adhesive heated for long periods of time, the material will start to burn and char. This char will stick to the sides of the system, hoses, applicators, and nozzles and will eventually cause blockages that need to be cleaned. Systems that use melt-on-demand technology do not suffer from these issues as only the required amount of adhesive is heated and dispensed, eliminating any risk of charring.

Related Articles
What Causes Hot Melt Adhesive Char
Overheating, contamination and oxidation. Learn about the three causes of adhesive char and how to avoid them.
The Venturi Effect and InvisiPac
Video explains how a simple concept from a dude with a fancy name makes an incredible piece of packaging equipment, called the InvisiPac® Tank-Free™ Hot Melt System, work.
The Cost of Hot Melt System Cleaning & Maintenance
Maintenance costs can quickly add up. Avoid unplanned downtime and replacement parts costs.