Glue Pump Features for Efficient Corrugated Cardboard Manufacturing
The role of starch glue pumps in corrugated cardboard manufacturing
Without glue, the corrugated cardboard industry would grind to a halt. Pumps are needed to transfer the glue throughout the production process.
Starch Glue Transfer
Pumps are a necessity in the carboard manufacturing process as they transfer the glue to the single facer and the glue machine.
The glue itself is prepared in the glue kitchen where it is collected in the buffer tank. From there, a pump is needed to move the glue from the main storage bucket into separate storage buckets beside the single or double facer glue pans.
The glue roll picks up the glue and transfers it to the medium tips, while the metering roll keeps constant glue thickness on the roll in order to deposit a constant volume of glue on each tip.
Starch Glue Circulation
To prevent the glue from settling in the glue pans, it’s constantly circulated to and from the buffer tank. Here, another pump is needed to transfer the glue from the glue pans back into the buffer tank.
Any remaining glue flows into a tray under the machine. A third pump is installed here to move this remaining glue in the tray to a storage bucket. From there it can be recycled and reused.
After shutdown, all glue in the corrugated line unit is pumped into the main storage tank for use the next working day.
Conclusion: For every corrugated cardboard manufacturing machine in operation, at least three pumps are required.
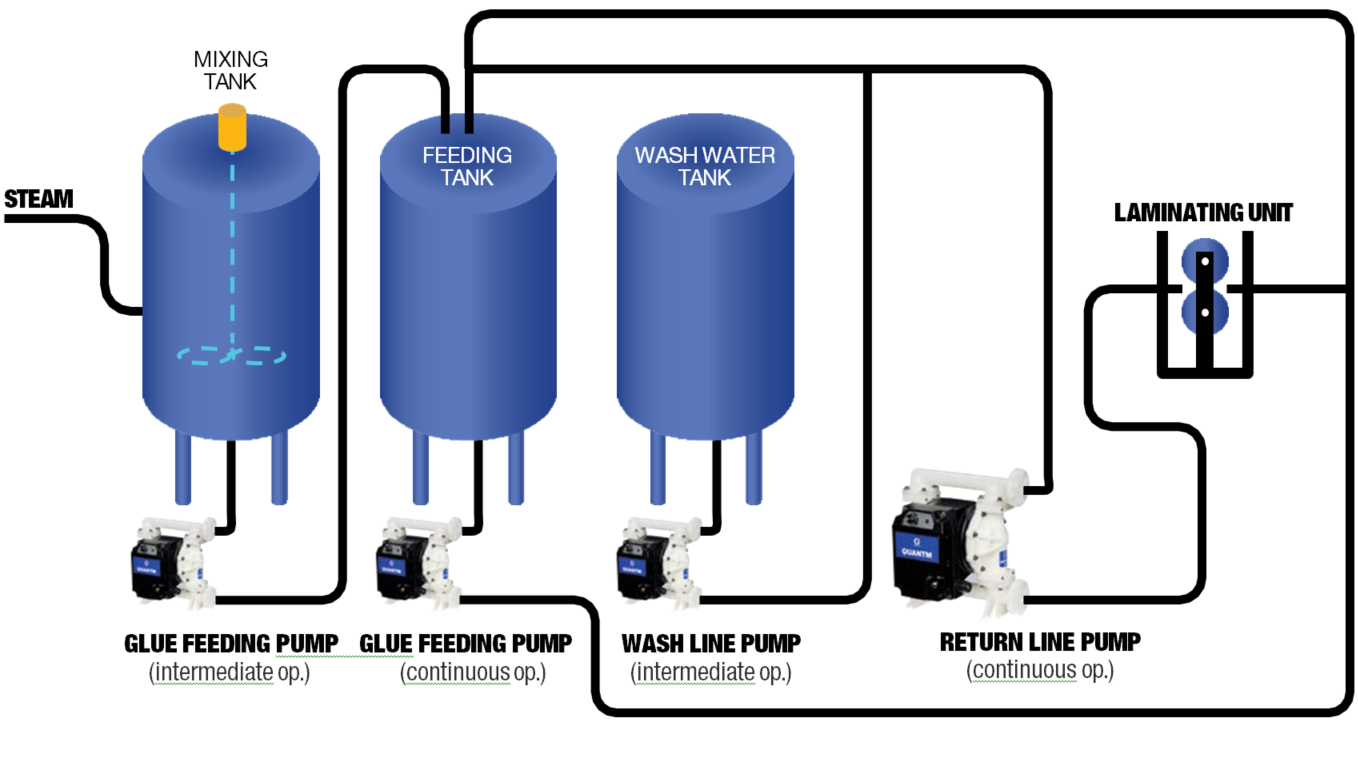
Common problems with starch glue pumps and how to fix them
Problem | Solution | |
The higher the viscosity, the more difficult it becomes to prime the pump. | One solution is to apply light heat to the product. This lowers the viscosity of the glue, facilitating priming and pumping. | |
Any glue left in the pump will stick to the interior or solidify and cause a blockage. | Removing this set glue is difficult and time-consuming and could damage the pump components. It is therefore essential to keep the flow of adhesive through the glue pump or clear it out between processes to prevent issues | |
Glue polymerizes upon contact with air. | When this hardened glue circulates in the line, it can block the line or the pump, which can cause the line to rupture. A QUANTM pump can stall against pressure without additional accessories being necessary to prevent damage to the line or pump. Other electric pump technologies need additional costly accessories to prevent this from happening, such as pressure sensors, a controller, or extra equipment to create a bypass. |
Features to look for in a starch glue pump for the corrugated cardboard industry
Starch glue isn't the easiest material to pump. However, you can pump it efficiently as long as you understand some basic properties of glue.
- Abrasiveness: Some glue contains ingredients with small particles. These particles wear against the pump's internal components causing failure.
- Corrosiveness: A chemical reaction can occur between certain glues and the pump's materials of construction and cause corrosion inside the pump.
- Shear Sensitivity: Many glues are shear-sensitive. Meaning, the product may be adversely changed while being pumped due to the shearing nature of the pump's operation. This can affect the performance of the glue.
- Viscosity: Viscosity is a major factor in choosing the right pump for a glue application. Glues can have a wide range of viscosities. Highly viscous liquids affect pump performance and output.
- Temperature: Some pumping technologies can heat up glue during operation; electric-operated double-diaphragm pumps do not have this effect. In general, glue temperature should not exceed 110°F otherwise the glue could turn into a gel.
- Flow: Minimum and maximum flow rates must be understood in order to efficiently manage glue transfer and application.
A revolutionary new solution for starch glue transfer and circulation
The QUANTM Revolution: Gluing just got smarter
QUANTM electric double diaphragm pumps offer a good solution for glue transfer. This new solution is specifically designed to handle even the most demanding glues with ease.
Here's how QUANTM sets itself apart:
- Shear sensitive: Unlike other pumps than can damage delicate glue molecules, QUANTM's gentle pumping action ensures the glue's properties remain intact, guaranteeing optimal performance.
- Viscosity? No problem: From thin to thick, QUANTM pumps can handle a wide range of viscosities effortlessly. They even adapt to changing viscosities, maintaining consistent flow regardless of back pressure.
- Cool under pressure: Unlike pumps that heat up the glue, QUANTM pumps integrate temperature sensors into the pump's electronic controls, helping to prevent the glue from turning into gel.
- Stalls for safety: Worried about clogged lines or closed valves? QUANTM pumps can stall under pressurem preventing pump damage and minimizing downtime.
- Built to last: Say goodbye to expensive wear parts and leaks! With no mechanical seals, QUANTM pumps require less maintenance and have fewer breakdowns, even with abrasive glues.
- Energy savings: Go green and save green! The energy-efficient operation reduces energy consumption by up to 80% compared to pneumatic alternatives.
- Quiet operation: By eliminating compressed air from the pumping process, QUANTM pumps deliver significant noise reduction, improving worker health and safety.
- Precise control: The integrated electric controls allow users to adjust speed at the pump using the one-touch dial control. Alternatively, users have the option to connect to the I/O port to enable remote operation and monitoring.
- Rock-solid reliability: Count on QUANTM pumps for 24/7 operation. Its robust construction handles even the most challenging glues with ease.
Quantm ROI Calculator
Interested in going electric?
Calculate how much you could save by converting your facility to Graco electric double-diaphragm pumps.
Related Articles
Choosing the Right Glue Pumps for Corrugated Cardboard Manufacturing
Double-diaphragm pumps are the preferred pumps to use as glue pumps since they are ideal for pumping high-viscosity fluids and can be adapted to the required abrasion resistance and soda concentration.
Why choose an electric-driven double-diaphragm glue pump for corrugated cardboard manufacturing?
An electric-operated double diaphragm pump definitely has clear advantages over its air-operated equivalent. Let’s have a closer look.
How Does a Diaphragm Pump Work?
Understand the working principle of a diaphragm pump, the different types of diaphragm pumps, and the common uses and applications.