New technologies cut costs
Inefficient processes drive costs
Transportation accounts for about one-fifth of global CO2 emissions. In 2020, the industry was the single largest contributor of greenhouse gases of any sector in the US with a whopping 30% share of emissions.
With that baseline in mind, consider this: Integration of electric technology into vehicles can reduce vehicular carbon emissions by as much as 80%. And in pumping-intensive industrial settings, where pumping systems account for over 50% of electricity consumption, the value of more efficient solutions quickly becomes apparent – both in terms of savings and reduction of energy use.
The point is that yesterday’s technology isn’t built to help manufacturers capitalize on the opportunities of tomorrow, either in terms of their sustainability goals or economic motivators. Think about the fact that pumping systems, which are only one essential part of manufacturing operations, could be driving almost half of manufacturers’ energy costs while preventing them from reaching their sustainability goals.
In a world where renewable energy is projected to be the US’s fastest growing source of energy, today’s electric technologies – like QUANTM pumps – prime manufacturers for a more sustainable future.
How Electric Pump Technology Saves Money and Boosts Sustainability
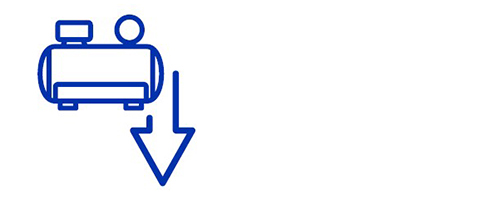
Eliminate compressed air
As mentioned before, the cost and noise level of using compressed air to power pumps really adds up – especially at scale and in pressure-intensive applications. Using a pump technology that does not rely on compressed air delivers significant noise reduction, improving worker health and safety. But it also delivers a considerably lower cost of operation.
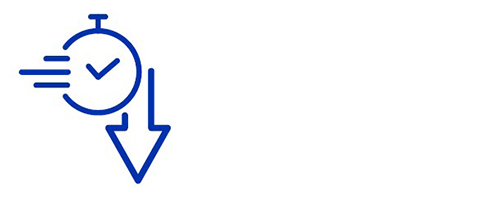
Quick plug-and-play installation
Downtime on your production line creates supply chain disruptions and cost overruns that put you at a serious disadvantage in an increasingly global marketplace. With plug-and-play integration into existing pump lines, electric pump technology allows you to immediately improve the metrics that matter – cost, productivity, agility and responsiveness.
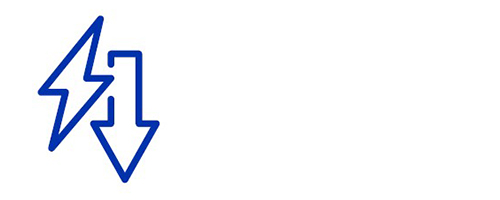
Decrease energy use
Facility managers and procurement specialists know that purchase price is only a small part of the overall cost of owning a pump, and that most of the cost of ownership comes from the energy it consumes and maintenance required over its lifetime. When you invest in technology that reduces those, including electric pumps, you’re kick-starting savings instantly with the initial investment.

Simplify maintenance processes
Since 2021, manufacturers have been facing alarming labor shortages. The last thing they need now is equipment that takes a long time to install and requires new specialized training to operate and maintain before they start seeing the benefits. QUANTM is easy to maintain, so your team can spend more time adding value to your manufacturing processes and less time just keeping things running.
Replacing Pneumatic Pumps with Electric
Because they’re so central to your manufacturing operations, pump systems are some of the lowest-hanging fruit for improving sustainability and efficiency in your factory. While replacing AODD pumps with QUANTM sounds like a big investment, it’s actually a fairly light lift in terms of equipment cost and the steps required to make them part of your manufacturing operations. But if you’ve ever replaced a traditional incandescent lightbulb with a long-lasting LED bulb, you’re already familiar with the concept.
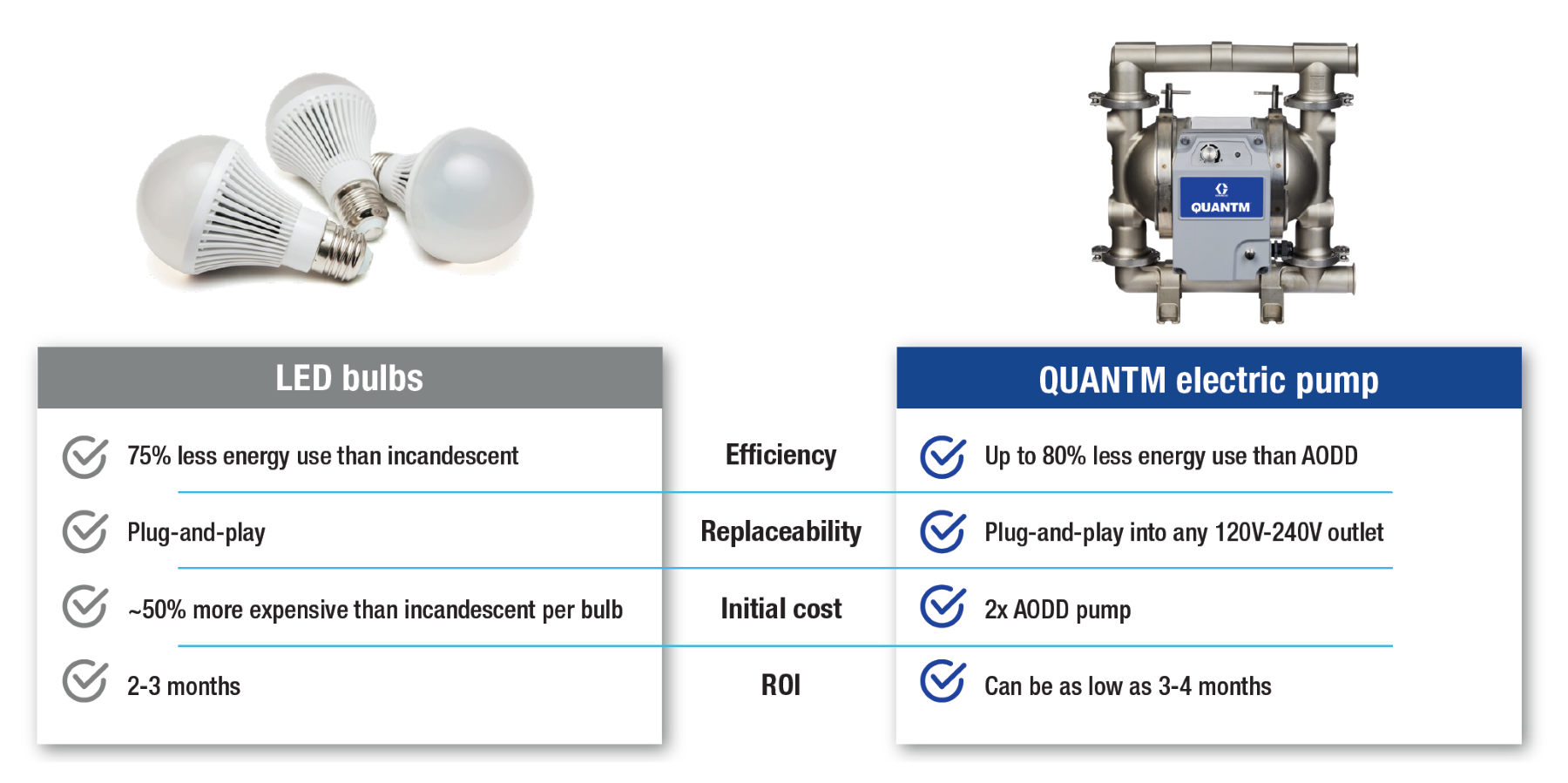
With investment costs that are comparable to AODD, efficiency that starts paying off immediately, and minimal retrofitting, QUANTM technology is ideal for any manufacturer interested in reducing energy use, saving money and satisfying key stakeholders. Graco’s QUANTM pump is perfectly suited to bring any facility’s pumping system into a sustainable future.
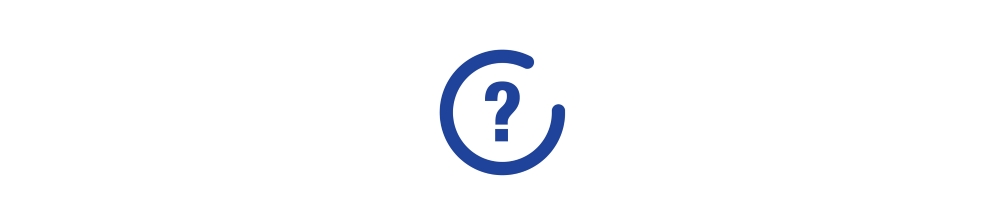
Just getting started with sustainability?
QUANTM pumps are a great starting point for sustainability – more efficient, more affordable and feature a quicker ROI than ever before.
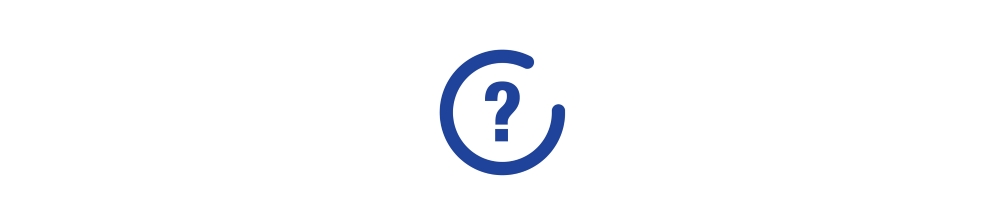
Already following a plan?
Electric technology is a great accelerator toward sustainability goals, helping you meet investor expectations and hit regulatory benchmarks faster while driving significant energy savings.
Cost-Cutting Wins for Energy Savings
Government-sponsored funding and rebate programs alone are enough of a financial driver to begin exploring electrification in manufacturing operations. But even if those funds aren’t available, the ability for new devices to reduce energy consumption is compelling from a financial perspective.
Win #1
Determine how much compressed air is costing you.
Compressed air and the electricity to produce it eat up more of your budget than you might think. In fact, it’s estimated that 30% to 50% of compressed air is wasted — that’s before considering other inefficiencies in the process. For perspective, it takes about 7 horsepower of electric power to operate a 1 HP compressed air motor (a high ratio that gets even higher when the pressure is higher than the typical 90 psi).
Win #2
Talk to your energy provider.
Your energy bill is a great indicator of how much you’re spending month to month, but a conversation with your energy provider can reveal a lot more than recurring costs. Dig into your energy use over time; cross-reference energy use with the age
of your equipment to see how much more it’s costing as it ages; compare your annual energy use to your region and industry standards. Understanding how much energy you’re using today is the first step to finding out how much you can reduce it in the future.
Win #3
Find out what incentives you qualify for.
In the US, many states offer incentive programs to offset the cost of integrating sustainability initiatives into manufacturing facilities and processes, either in the form of rebates, tax credits, or direct incentives. A 2022 PwC study of the EU Green Deal showed that a majority of environmentally focused improvements to manufacturing equipment and technology in the EU have been made using ‘preferential financing’ like incentives (40%), grants (31%) and tax credits (26%).
These motivators are often tailored to specific issues and goals, like a rebate for investments into recycling technology or emissions-reducing equipment, and they’re not always dependent on an established or wide-ranging commitment to sustainability initiatives. Take stock of your processes, equipment, goals and other factors to make your facility as eligible as possible.
How Graco can help you build a cost-saving strategy
Graco is currently working with manufacturers across multiple industries to drive measurable and sustainable energy savings in their operations. The recent development of our electric-operated double diaphragm (EODD) pump allows us to bring cost-saving ideas to manufacturers of all sizes. We’ve collected data from plants around the world that shows air-operated double diaphragm (AODD) pumps drove the large — if not the largest — consumption of electricity in a manufacturing operation.
Graco sustainability and electrification experts can help you calculate current energy costs and potential energy savings if you transition old AODD pumps to modern electric alternatives. We also can help you explore incentive programs offered by utilities, power aggregators and government organizations that help pay for — or entirely cover — the deployment of sustainable new pump technology.
Request more info
Related Articles
Sustainable paths to profitability
Energy savings and sustainability are becoming profit drivers for companies around the world. Graco can help you build a cost-saving strategy and explore incentive programs to improve efficiency of processing technologies.
Electric pumps lead the way to energy efficiency and sustainability goals
Electric pumps lead the way to energy efficiency and sustainability goals
How Does a Diaphragm Pump Work?
Understand the working principle of a diaphragm pump, the different types of diaphragm pumps, and the common uses and applications.