Automotive OEM Sustainably Powers Up
Electric pumps with intelligence make paint mix room upgrade cost effective and sustainable.
Background: Paint Line Automation and Waterborne Electrostatics
To keep up with production demands and to meet sustainability goals, the paint process engineer of an established automotive original equipment manufacturer (OEM) needed to upgrade the paint mix room of a major assembly plant.
For years, alternating current (AC) electric pumps had been powering an automated finishing line that uses electrostatics to spray waterborne coatings. Water-based paint lessens the factory’s carbon footprint because it does not contain volatile organic compounds (VOCs) that release toxic fumes into the air. To safely apply the environmentally friendly coating with electrostatics, the manufacturer isolates the charged paint in 24 canisters. When the canisters are emptied, as many as 24 must be reloaded within seconds.
Challenge: High Pressure Paint Circulation
Paint circulation system demands often challenged the old equipment. With regular circulation pressures above 200 psi, and intermittent flow rate peaks, the legacy pumps could fill a maximum of 11 canisters before faltering. Low pressure faults would halt production until pump cycle rates were corrected.
The paint process engineer had experience using pumps from Graco and Binks at other factories. Since the Binks equipment tended to have high maintenance costs, he asked Complete Automation, a leading industrial integrator known for turnkey paint circulation system installation, about Graco solutions.
Challenge: Save Energy in a Small Footprint
The automotive factory’s new paint circulation pumps not only needed to work well under high pressure, they also had to save energy within a small footprint. Floor space for each pump needed to stay within 17 by 20 inches.
Complete Automation recommended trying to Graco’s newest electric paint circulation technology: E-Flo® DCi™ 4-Ball Pumps with DCi Link™.
Why E-Flo DCi and DCi Link?
Compared to other electric paint circulation pumps, the E-Flo DCi dual control (DC) pump with intelligence (i) offers:
- more power and efficiency in a small footprint that takes up less space
- more reliability and ease of use with less parts to maintain
- more intelligence with less hardware to communicate important data
Dual control (DC) allows operation in flow mode for constant circulation, or pressure mode for dynamic speed adjustments. Such flexibility could help paint mix room operators keep the pressure rates needed to fill all 24 canisters in seconds.
The DCi Link control module could connect via ethernet to the plant’s programmable logic controller (PLC). Ethernet access to web-based setup and programming would provide real-time access to the data needed to identify issues, such as under/over pressure or flow events, before they affect production.
Approach: Turnkey Installation and Integration
Before bringing E-Flo DCi technology to the automotive assembly plant, Complete Automation set up each unit in its shop. Although technicians liked how easy it was to assemble each pump, they especially valued the ease of integration.
“The pump part was easy,” said Aaron Elliott, Graco field sales specialist. “The thing that impressed them at the very beginning was getting into the web interface for the DCi Link and being able to establish the registers needed to communicate with the factory PLC.”
Web-based setup and assembly done in advance, Complete Automation installed 15 E-Flo DCi pumps in the factory. As the integrators finetuned the automated setup, paint mix room operators easily jumped in.
“Having the pumps run in local mode was a great feature,” said the paint process engineer. “It allowed the operators to run the pumps to flush the system before they were fully integrated into the PLC controls.”
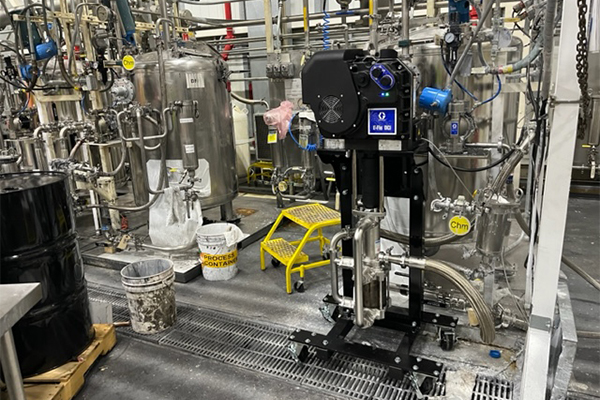
Additionally, E-Flo DCi pumps operate without a VFD (variable frequency drive), further simplifying installation.
Using DCI Link to connect the E-Flo DCi pumps to the factory PLC allowed real-time access to pump data.
Outcome: Energy Efficiency and Real-time Data
Since upgrading to E-Flo DCi and DCi Link, the automotive OEM paint mix room can maintain the required paint circulation system pressure and flow, doubling concurrent canister full capacity.
For ongoing paint circulation efficiency, paint mix room operators set each E-Flo DCi pump to pressure mode. This allows the pumps to:
- run steadily during circulation
- adapt immediately to higher flow conditions when all of the canisters need to be filled at once
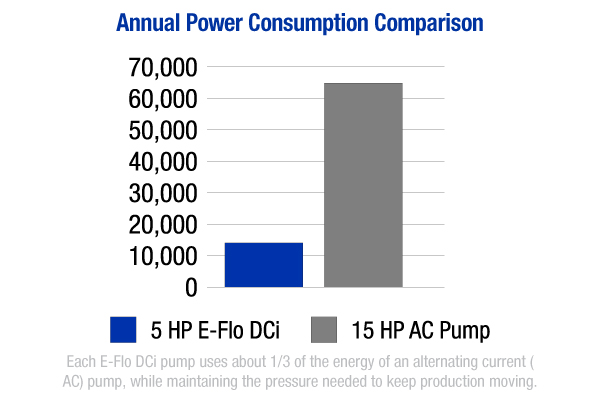
They quickly adjust to pressure mode when it’s time to replenish waterborne paint. All 24 canisters refill in seconds - without pressure drops and shutdowns due to low pressure faults.
The ability to access real-time data via DCi Link has proven essential to making sure all 15 E-Flo DCi pumps run efficiently at high cycle rates that keep up with production demands.
All trademarks and registered trademarks are the property of their respective owners.
Collaborate with Us
Innovation truly comes through collaboration with Graco expertise and customer partnerships. We strive to deliver custom solutions backed by our global support network.
Contact our team for help with your application.
Related Resources
Electrifying Your Industrial Process and Grow Your Bottom Line
Electrification of industrial processes is not only good for the environment, it makes good business sense. Explore how sustainable manufacturing leads to cost savings and competitive advantages.
3 Steps to Reduce VOCs in Paint Lines
To minimize VOCs, manufacturing companies are looking for ways to reduce paint and solvent waste with more efficient equipment and automated processes.