Do you have an icing problem?
How to tell if you have an air motor icing problem and what you need to do to fix it
Air Motor Icing
Why Is It Happening And How Do I Fix It?
No Air Consumption Means No Icing. Icing is a problem inherent to all air motors. Since electric motors do not use compressed air, they do not ice.
There are several other factors that influence icing which include:
- Compressed air temperature
- Compressed air dew point
- Compressed air pressure
- Compressed air volume flow rate
- Air quality due to contaminants
- Ambient air temperature
- Ambient air dew point
- Ambient air flow
- Motor air valve material
- Motor air valve geometry
- Cycle rate of motor
- Exhaust port restrictions such as a muffler
These factors can interact in unpredictable ways and can be temporary, which is especially true with seasonal fluctuations in relative humidity.
How do you know if you have an icing problem?
Before you try to fix an icing problem, you should be reasonably sure that icing is the problem. You likely have an icing problem if the following conditions exist:
- The pump has erratic pressure fluctuations
- The air motor stops but will restart after the ice melts
- This may take an extended period of time
- The motor or muffler is heavily frosted
- The compressed air you are using is moisture laden because little or no drying equipment is installed
- You need to do air supply or fluid control adjustments to maintain a constant cycle rate (This problem may be temporary if it is a seasonal fluctuation in humidity)
How do you fix air motor icing?
There are several possible solutions to motor icing. We recommend trying the less expensive options first.
- Change the operating parameters.
- Decrease pump air supply pressure. This will change the output rate of the fluid. Lower pump line restrictions.
- Change the exhaust configuration. Put a muffler on the air motor to restrict the exhaust. However, this will lower the performance of the pump.
- Attach a tube to the air exhaust port. Exhaust the air to a remote location.
- Install an air line heater. You may want to install an air supply heater if none of the above solutions work satisfactorily or the problem is not temporary or seasonal. The heater should heat the air supplied to the pump to 130°F, raising the exhaust air temperature to above 32°F to eliminate the icing.
- Warning: Only install these heaters in areas not prone to explosions or use an approved explosion-proof heater. The drawback to this solution is the ongoing energy cost for the electricity.
- Install an air drying system. If none of the previous changes solve the problem or are feasible, you may have to lower the pressure dew point temperature with an air compressor dryer.
There are three levels of solution for improving air quality:
- After cooler
- Refrigeration system air dryer
- Desiccant air dryer
This list is in order of expense and effectiveness. The after cooler may be enough for intermittent use, while a pump running continuously may require a desiccant air dryer.
How can I prevent air motor icing?
Obviously it is best to prevent a problem before it occurs. Motor icing is very likely in any installation where the following occur:
- High pressure demand
- Long duty cycle, especially if running continuously
- High cycle rate
- High dew point most of the year
If any of the above are true, you may want to install a larger sized pump.
Obviously, if you think you have an air motor icing problem and are seeking the best solution for your specific application, contact your local Graco Distributor. They will be able to assess the problem and provide you with the most cost efficient, practical solution.

ELECTRIC MOTORS
Icing never occurs on electric pumps like the E-Flo DCi. This means that paint mix room operators and maintenance staff do not need to worry about contamination or safety issues caused by air motor icing.
ICED MOTORS
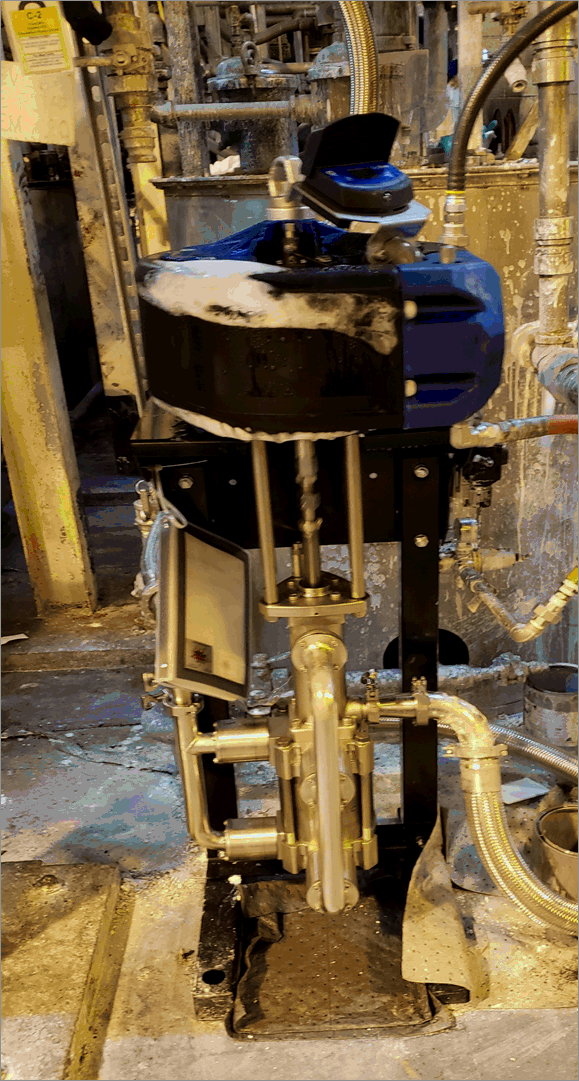
Icing occurs when moisture in the air supply lines condense and freeze on the pneumatic air controls. If the accumulated ice melts into material containers, it can cause contamination issues. If the melting ice drips on the factory floor, it becomes a safety hazard.
Learn More
Related Articles
5 Ways to Reduce Unplanned Downtime
Looking for ways to stop unplanned downtime? Follow our simple tips, and downtime should not be a problem.
Automaker improves productivity by solving air motor icing and leaky lower
Air motor icing and leaky lowers in the paint kitchen were cutting productivity at a large automotive plant – until they tried a new pump package.
Selecting the Optimal Motor for Paint Circulation Pumps
Paint shop pumps with pneumatic motors have been mainstays in many plants. However, electric pumps perform four to seven times more efficiently. What’s the best motor for your paint shop? Use this guide to weigh the pros and cons.