Tier 1 Supplier accomplishes more with less equipment
ProMix PD enables a paint line to do the work of eight robots with only four.
CUSTOMER: Tier 1 Automotive supplier
GRACO EQUIPMENT: ProMix positive displacement (PD) proportioning system
CHALLENGE: A Tier 1 automotive supplier needed an automated paint system that could do the work of eight robots with only four. They were about to get an influx of business from another plant. That plant used eight robots to coat jeep hard tops with high viscosity material at high flow rates along their paint line. The Tier 1 Supplier needed to do the same, but only had space for four robots.
For more than 10 years, four robots and four 2K flow-metering units had been running low viscosity, two-component primer for lower volume items. The old equipment needed to be replaced within the same footprint. They could not add more robots without completely changing the paint line, which was not an option.
The paint line manager originally looked at a positive displacement, two-component system to run low viscosity primer at low flow rates. But after testing a couple of systems, it was found that neither could handle high viscosity material at high flow rates. With only four robots, flow rates needed to be upwards of 800 cc / minute. This put pressures above 200 psi, causing pressure faults.
They needed a system that could run low viscosity primer at low flow rates to meet current production needs; and handle high viscosity spatter material at high flow rates to cover new, incoming demands.
SOLUTION: The paint line manager went to Graco’s application lab in Minneapolis to see how the ProMix Positive Displacement (PD) Proportioner Platform handled the new spatter material. The ProMix PD2K pump managed flow rates all the way up to 930 cc / minute without faulting. Finish quality also met specifications without fault.
The PD2K allowed spatter and primer materials to have their own pump sets. This made for fast color changes.
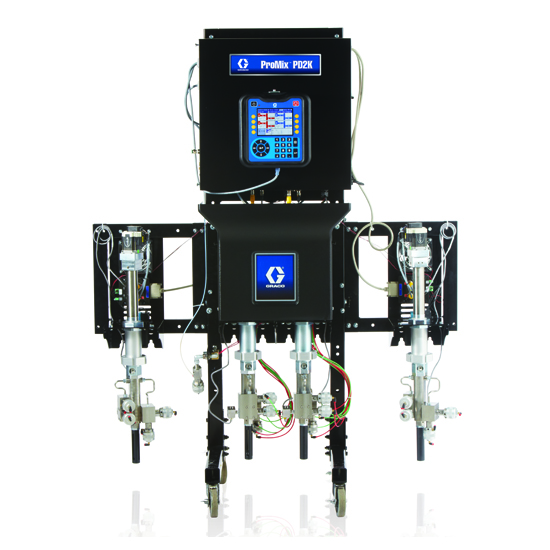
RESULT: Since the ProMix PD can manage high viscosity and low viscosity materials at full flow rate range, the paint line manager found they could accomplish more with less equipment.
The Tier 1 automotive supplier upgraded its automated paint system with four ProMix PD2K pumps and four FANUC P-250 painting robots.
To help paint line operators successfully manage and maintain the new system, their Graco representative and distributor gave several on-site training and follow-up sessions. Such support helped them troubleshoot and improve the automated paint line.
After more than two years, the equipment continues to run low viscosity primer and high viscosity spatter material, meeting production demands.
All trademarks and registered trademarks are the property of their respective owners.
Tier 1 Automotive Supplier
OEMs (original equipment manufacturers) demand components that look good and work well under harsh conditions. Tier 1 suppliers throughout the automotive industry achieve durable coatings and precise fluid dispense with Graco solutions.
Related articles
Graco’s IPK Easily Beats the Competition
Every 7 to 10 years, manufacturers replace their paint kitchen equipment due to normal wear and tear.
Transfer efficiency increases 30 percent with a ProBell atomiser
The paint line improves aluminium extrusion finishing, sending a lot less back to a touch-up booth.
Manufacturer Saves £365,000 with Rotary Bell Atomisers
Replacing Nordson RA20 with ProBell increases paint line speed and decreases solvent use. Bell applicator technology pays for itself within a year.