How to reduce the maintenance costs of your packaging line
DISCOVER THE BENEFITS OF SWITCHING FROM A TANK-BASED SYSTEM TO A TANK-FREE SYSTEM
Line stops on a packaging line are a nightmare. By changing your traditional tank-based system to a tank-free hot melt system, you can eliminate the risk of costly line stops and have more production uptime.
Having to stop production and clean or replace broken or clogged parts leads to significant downtimes. Productivity drops and maintenance costs rise. There are four main reasons why parts need cleaning or replacing:
- Char or burned adhesive
- Manual changes to pressure settings on your hot melt system
- The service life and type of your applicators
- Too many reactive maintenance stops
Tank-free systems handle these problems far better than tank-based systems, minimising downtime a
Reduction of char or burned adhesive
When you are working with tank-based systems, you often see char on the sides of the tank or clumps of adhesive floating in the tank, which increases your risk of costly line stops. This occurs because large amounts of adhesive (at least four litres) are kept at a high temperature for a long time. The main reason for this is the long heat-up time of the machine (+/- 40 minutes). This is needed partly because of the very low melting surface but mainly because of the lack of an automatic refill.
By choosing a tank-free system like the Graco InvisiPac, you can eliminate all these risks from your production. InvisiPac has no tank and works on a melt-on-demand principle. In other words, it heats only the amount of hot melt adhesive material that is necessary. By doing this, you can be sure that the first material that comes in is also the first material dispensed. With this “first in, first out” approach, charring and nozzle blocking are eliminated, thus eradicating any risk of line stops and significantly reducing your maintenance and adhesive costs.
Avoid viscosity changes
Tank-based systems keep adhesive at high temperatures for prolonged periods. When the tank level is getting low, operators refill the tank to the maximum level with cold adhesive, cooling down the remaining molten adhesive and thus raising the viscosity of the material.
With a higher viscosity, the output of material is lower than usual. To compensate for this low throughput, most operators will increase the pressure on the system. However, operators will often forget to lower the pressure again when the viscosity drops. This increases material consumption and adds stress to all components, reducing the lifetime of these components.
The InvisiPac tank-free system works on the “first in, first out” principle. Because there is no tank, the adhesive you melt has the same viscosity every single time. So, there is no need to adjust the settings of your system and no need to worry that the pressure is set too high.
Use applicators without dead zones
Nozzle plugging is a very costly problem. Unfortunately, it happens way too often on a production line. It is often considered a normal issue for hot melt applications, but what if we told you it could be resolved?
In the InvisiPac applicators, the manifolds are designed so that they eliminate any dead zones. This means that there is nowhere for char to build up, eliminating the possibility of nozzle plugging. In other words, simply by changing your traditional tank-based system to a tank-free hot melt glue carton sealing machine, you can eliminate the risk of costly line stops and have more production uptime.
Changing from reactive to proactive maintenance
Finally, it makes sense to consider moving from reactive maintenance to developing a proactive maintenance process for hot melt equipment. It is certainly the best approach for facilitating maximum uptime.
InvisiPac has a built-in material tracker that indicates how much adhesive you are consuming. This helps you to easily schedule maintenance stops based on the amount of adhesive that has gone through the system. You can also enter reminders into the system that will alert you to perform preventive maintenance when the system has gone through a certain number of cycles.
If you want advice on the optimal equipment set-up to eliminate all these risks in your packaging line, feel free to contact Graco’s experts. We would be delighted to help.
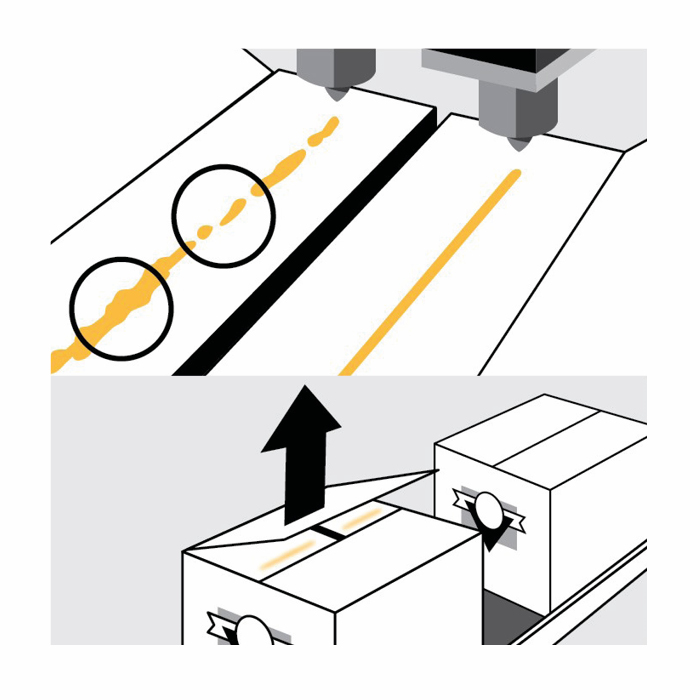
Related articles
Why InvisiPac is the reliable option for your packaging line?
An InvisiPac tank-free hot melt glue system with melt-on-demand process avoids charring and nozzle blocking.
How to reduce cleaning of your hot melt system
A tank-free system like InvisiPac reduces the cleaning time and expense of your hot melt system.
Summit Brewing: Packaging line success story
New packaging technology helps Summit Brewing improve their production efficiency.