Why InvisiPac is the reliable option for your packaging line?
An InvisiPac tank-free hot melt glue system with melt-on-demand process avoids charring and nozzle blocking
Based on their long experience in fluid handling equipment in multiple industries, Graco looked into why problems were occurring with hot melt glue systems. Unexpected equipment problems can cause system downtime, hindering productivity and increasing costs. To maximize uptime, it is vital to choose the right hot melt system.
You want your packaging line to run smoothly, efficiently, and continuously in order to maintain productivity and profitability.
Choosing the right hot melt system
If your line is not running optimally, your costs will go up and your production will drop. To prevent this from happening, it is vital to choose the right hot melt system. In other words, for your line to run smoothly, efficiently, and continuously, you need a hot melt system that also runs smoothly, efficiently, and continuously. As none of these three words normally describes most conventional hot melt adhesive systems, Graco decided to take action. Our goal was to find a solution to ensure risk-free production.
InvisiPac with a melt-on-demand process
The main reason we identified is that most hot melt systems process adhesive with a heated tank. This process creates temperature fluctuations and inconsistency with the adhesive, leading to line stops and unnecessary downtime.
To eliminate these risks, Graco developed the InvisiPac tank-free hot melt glue system. Its key innovation is that it utilises a melt-on-demand process. In other words, it heats only the amount of hot melt adhesive material that is necessary. With this “first in, first out” approach, all charring and nozzle blocking is eliminated. Adhesive and maintenance costs are significantly reduced, while reliability and productivity are improved.
The InvisiPac tank/tank-less system vs. tank-free melter
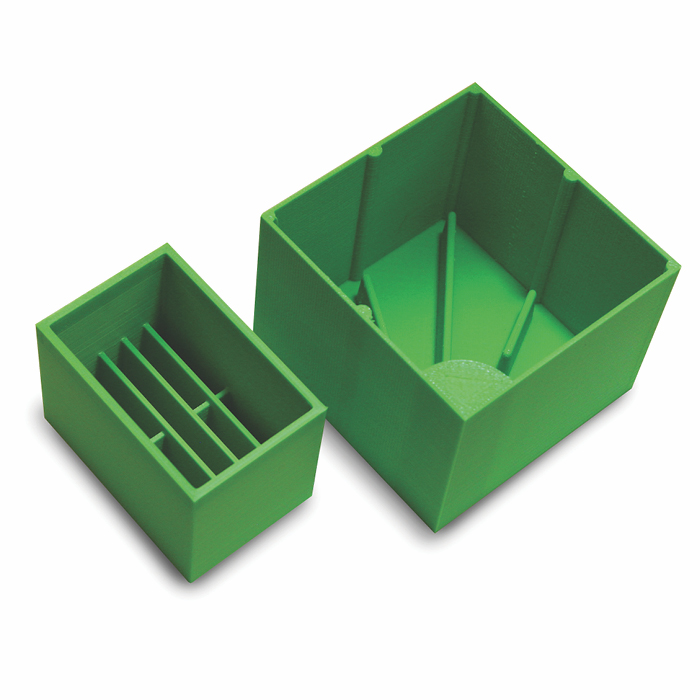
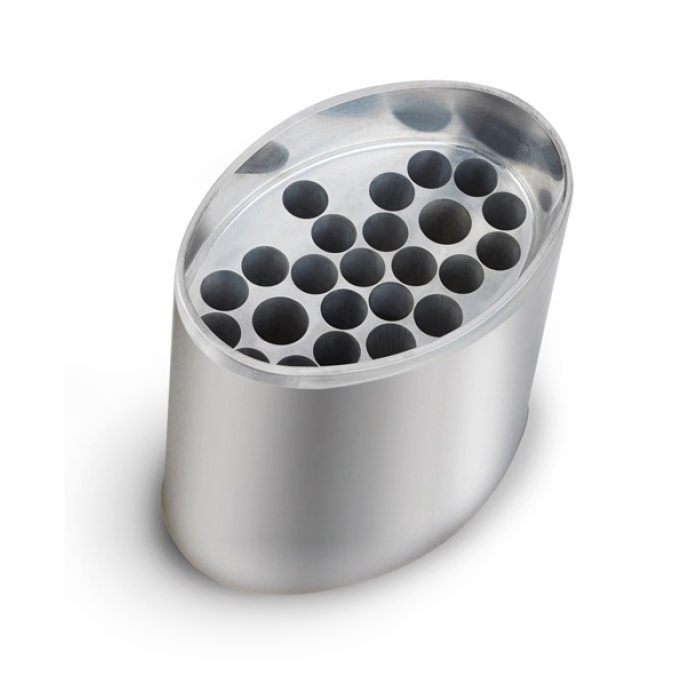
Tank/tank-less system | InvisiPac tank-free melter |
Slowly heats up to its operating temperature (up to 45 minutes)
|
Reaches its operating temperature in less than 10 minutes
|
Large quantities of adhesive kept at high temperatures for a long time
|
“First in, first out” melting provides continuous flow of adhesive
|
Degrades adhesive integrity
|
The melt-on-demand process maintains adhesive integrity
|
Creates adhesive char which causes plugged nozzles
|
Eliminates plugged nozzles and adhesive char
|
Causes thermal shock (temperature fluctuations) when refilling adhesive
|
Removes operator exposure to burn hazards
|
Exposes operators to burn hazards
|
Built-in adhesive tracking technology
|
Realise the benefits of tank-free
With InvisiPac, you will experience far less downtime and produce more with a better seal. You will use significantly less adhesive and be able to drastically reduce your spare parts inventory. All of these benefits produce greater profits. InvisiPac also creates a safer working environment, especially for operators. Moreover, its compact size easily integrates into your existing packaging lines.
In short, InvisiPac redefines the reliability of hot melt systems, improving your productivity and helping you realize maximum profitability. Convinced? Contact our hot melt experts for more information in the form below . They would be happy to explain more about how the reliability of InvisiPac helps your packaging line run smoothly, efficiently, and continuously.
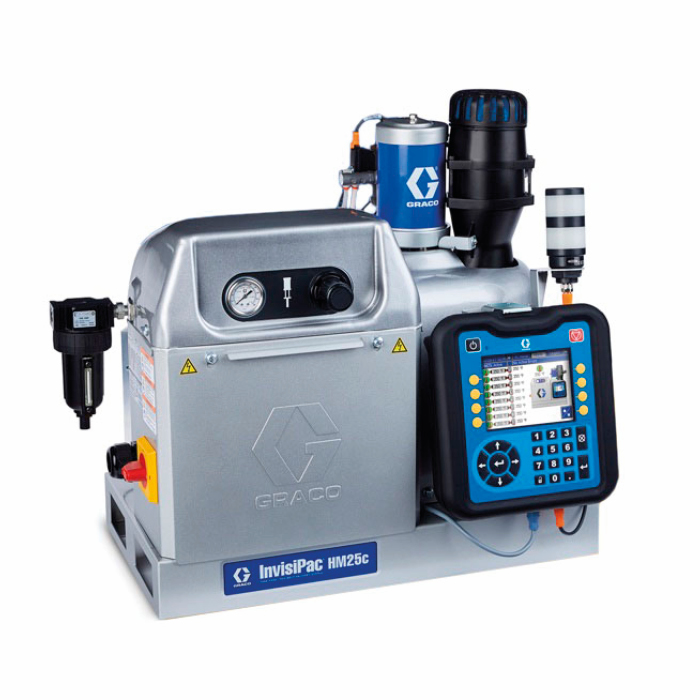
Related Articles
How to reduce the maintenance costs of your packaging line
Discover the benefits of switching from a tank-based system to a tank-free system
Precisely monitor your hot melt adhesive dispense
With Graco’s Adhesive Tracking Technology you can easily monitor your hot melt adhesive consumption.
Summit Brewing: Packaging line success story
New packaging technology helps Summit Brewing improve their production efficiency.