Choosing a hot melt nozzle
The choice of hot melt nozzle impacts the performance of your end-of-line packaging operations.
Selecting the right nozzles for your end-of-line packaging operations is important. With the appropriate hot melt nozzle, you can maximise the performance and efficiency of your hot melt adhesive system. Correct nozzle selection impacts material management, operating expense, and operator safety.
In order to select the right hot melt nozzles that will have the greatest impact on improving performance and production efficiency, you must take into account the following:
- the differences between various hot melt adhesive materials
- the unique demands of the application
- the maintenance requirements
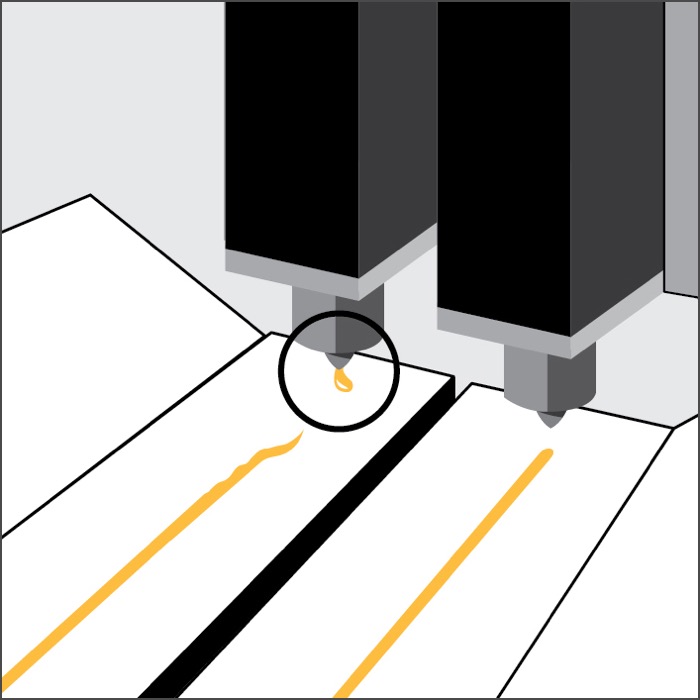
What are hot melt nozzles?
Once hot melt adhesive has passed through the heating process, the molten adhesive is transferred to the applicator or “gun” for dispensing. Located at the very end of the gun, hot melt nozzles ultimately control the volume, velocity, and direction of the dispensed adhesive. As part of a hot melt adhesive system, hot melt nozzles play a significant role in helping avoid waste and improve efficiency.
Nozzles are interchangeable and are manufactured in multiple sizes and designs for a variety of dispensing applications. Most nozzles fit into the following categories:
- Bead nozzles: provide a single continuous bead or patterns
- Spray nozzles: dispense in patterns with various widths and diameters
- Multi-line nozzles: deliver multiple beads and patterns from a single nozzle
How to determine the nozzle diameter?
When determining the effective hot melt nozzle diameter, a common misunderstanding is that bigger is better to avoid downtime from nozzle plugs and keep the production line moving. While this approach may provide a short-term gain, it is important to understand that the size of the nozzle does not directly correlate to the amount of glue dispensed.
The limitations of the hot melt equipment should never dictate hot melt nozzle specification but, unfortunately, it does. It is common for manufacturers and maintenance managers to view hot melt nozzles as a consumable. However, the nozzles directly affect the performance and pump life of some hot melt systems.
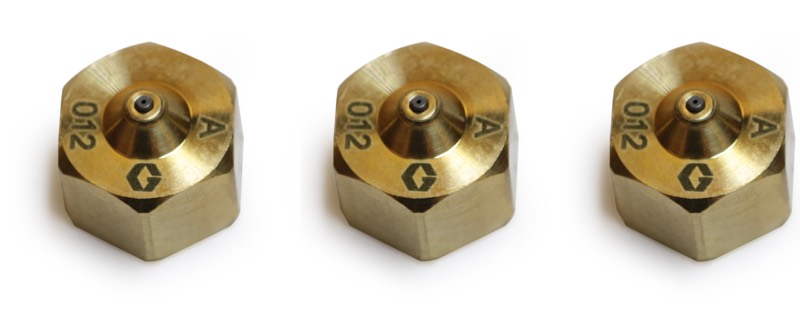
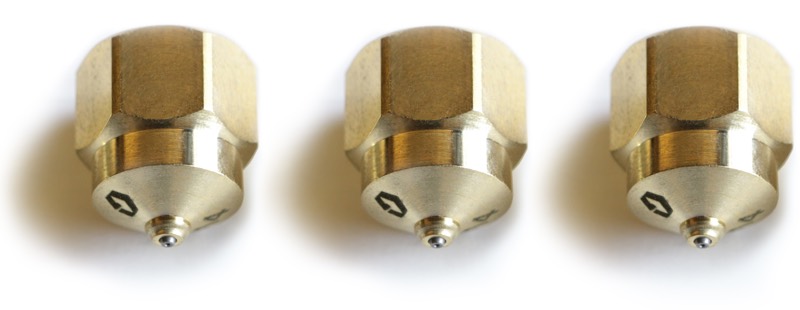
Understanding the properties of hot melt adhesive material
With hundreds of hot melt adhesives available, the first step in selecting the right hot melt nozzle for optimum performance is to understand the characteristics of the hot melt adhesive material itself. Even within the same manufacturer product line, hot melt adhesive properties vary. For example, the viscosity of an EVA hot melt adhesive may be 1100 centipoise @ 350 degrees where a metallocene hot melt may have a thinner 700-900 centipoise at the same temperature.
The performance of the hot melt adhesive will have an impact on the performance of the hot melt adhesive system. This will be most noticeable at the point of dispense – the hot melt nozzles. Best practice would be to involve your material supplier when optimising hot melt equipment and specifying nozzles.
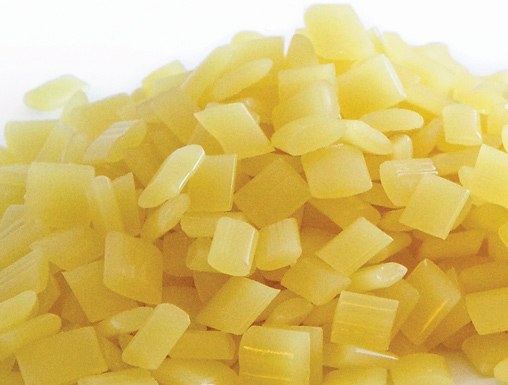
Hot melt adhesive pellets
Understanding the demands and possibilities of your application
While there are common themes to most end-of-line packaging and case and carton sealing applications, every application is unique. When specifying hot melt nozzles for your application, you must take into account a multitude of elements: the finished goods inside, the carton stock, marketing display elements, line speed, and glue throughput.
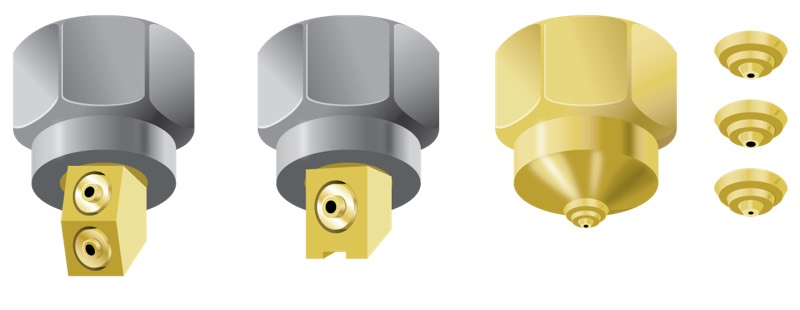
Some application elements that effect nozzle selection include:
- nozzle engagement: the length of the nozzle hole
As engagement increases, the flow of adhesive decreases. - Dispense pattern requirements
The nozzle orientation determines the possible dispense patterns. Using a nozzle with a single orifice enables straight and 90° angle dispense patterns. When using nozzles with multiple orifices, you can choose the setup to create specific dispense patterns with a wide variation in angles. - Cutoff requirements
A clean cutoff of the adhesive flow is important to avoid stringing or the formation of “angel hair” and to eliminate scrap. - Velocity
Smaller nozzles enable a higher back pressure and provide a more powerful stream of adhesive that carries further. - Pump pressure capabilities and fluctuations
Air-powered piston pumps allow a high, consistent pressure and support a variety of nozzle orientations. An electric-powered gear pump provides a continous flow with low pressure and requires larger nozzles. The nozzle orientation options are limited.
Single- and multiple-orifice considerations
It is common to see an application where multi-orifice nozzles have been avoided because of low performance, carton pop-opens after packages leave the manufacturing facility, and concerns over potential downtime issues.
Another common mistake is when multi-orifice and single-orifice nozzles have been unnecessarily oversized to avoid nozzle plugs, rather than because either is the right nozzle for the application. Regardless of when this occurs (when setting up the line or implemented over time), it is always best to specify nozzles for the application rather than allow the limitations of the hot melt system and equipment to dictate nozzle selection.
Maintenance requirements to extend nozzle life
Regardless of the nozzle selection, one constant to maintain throughput and uptime is the need to clean and maintain the nozzle. Adhesive char is a common problem for end-of-line packaging systems and is the biggest issue in hot melt nozzle performance.
It is not uncommon for maintenance to extend the nozzle life or to reuse nozzles by using hole pricks or small drill bits to keep hot melt nozzles open. While it may be a short-term solution to keep adhesive flowing, this approach will often increase the nozzle orifice size and lead to higher adhesive costs. Identifying and confirming maintenance parameters with equipment suppliers will help maintain optimum performance without increasing material or spare parts costs.
Avoiding plugs in nozzles
Unwanted downtime and the issues that come with it can be avoided. In manufacturing environments with poor air quality, there is an increased risk of contaminants entering the hot melt adhesive. By selecting hot melt equipment and nozzles that provide the highest amount of filtration, you can prevent contaminants from clogging nozzles, thereby reducing downtime incidents. Some systems and nozzles are engineered to provide “zero plugs.”
Where possible, ask equipment manufacturers for proof of these claims and see if a demo program is available. The ability to see the equipment performing in the actual environment will help validate how their technology can improve issues with unplanned downtime related to maintenance issues.
Ultimately, correct nozzle selection has a direct influence on material management, operating expenses, and operator safety. Make sure you have a detailed understanding of hot melt adhesive materials, the unique demands of the application, and the maintenance requirements, so that you can specify the right hot melt nozzles that will have the greatest impact on improving performance and production efficiency.
Related articles
Improve hot melt system performance
Improve the overall profitability of your packaging line by understanding the high price of outdated processes.
How to reduce the maintenance costs of your packaging line
Discover the benefits of switching from a tank-based system to a tank-free system
How to reduce cleaning of your hot melt system
A tank-free system like InvisiPac reduces the cleaning time and expense of your hot melt system.