Improve hot melt system performance
The high cost of old technology
The hot melt system, while only one part of the complete end-of-line packaging process, can have a large impact on your overall production efficiency, manufacturing costs, and operator safety. When comparing traditional tank-based systems designed like a “crockpot” with the newer technology of tank-free systems, you will notice a drastic difference in the potential of the greater profitability and reliability possible with non-tank-based hot melt systems.
Knowing the right questions to ask before selecting your hot melt system can help you find the best solution to complete for your end-of-line packaging process.
Five questions to ask when buying equipment
1. Can one depend on the hot melt system for consistent quality?
2. How much maintenance is required?
3. Is the hot melt system able to provide you with operational savings?
4. Are you able to track system performance?
5. How safe is the system for packaging equipment operators?
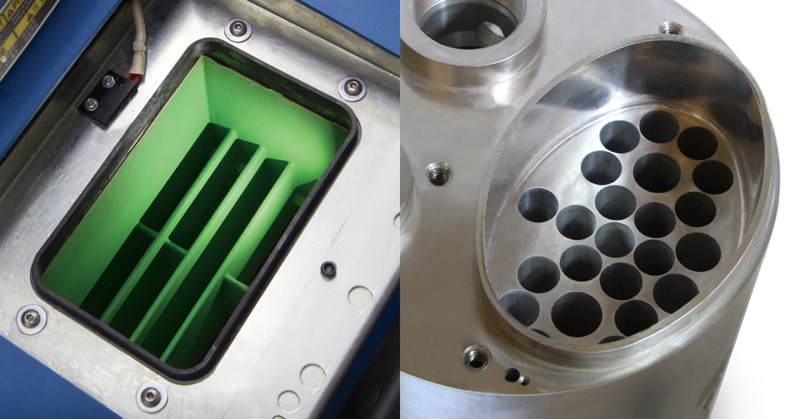
Figure 1 - The melter on the left is called “tankless”, but it is not. The right image shows a truly tank-free melter.
Viscosity variations and wasted hot melt adhesive
Viscosity changes can result in poor adhesive performance and fluctuations in the amount of adhesive dispensed. If too much glue is dispensed, material is wasted and money is left on the table. If too little is dispensed, there will be pop opens which could lead to scrap or returned product.
Some newer hot melt technologies available today use an integrated vacuum system to feed hot melt adhesive to the melter. With this approach, an ultrasonic sensor constantly monitors the adhesive in the chamber. Additional adhesive is automatically added as needed, depending on the application's demands. Material is added at a rate of only about one-quarter of a cup at a time, eliminating thermal shock to the molten glue that could directly result in problematic viscosity changes.
These integrated vacuum feed systems also save on labour costs, since they do not' depend on anyone to keep an eye on adhesive. The system automatically keeps adhesive at optimum levels while keeping the heat in, and dust and debris out. It also promotes consistent bead weights by eliminating thermal shock.
The surface area to adhesive volume ratio
The high surface area to volume ratio found in tank-free hot melt adhesive systems is responsible for the decreased charring and minimal start-up times. By eliminating heated tanks and increasing the melting surface, hot melt equipment performance improves dramatically. The higher this ratio is, the lower the likelihood of charring and shorter the start-up time will be.
When systems are not dependent on a tank, adhesive pellets can be melted on demand and then dispensed quickly, which greatly reduces the char and material degredation caused by prolonged exposure to heat.
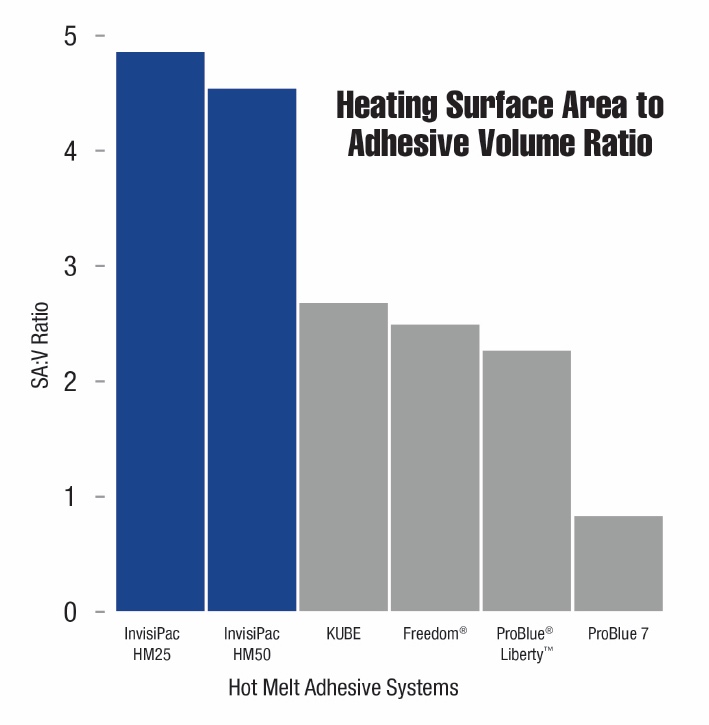
Figure 2 - The heating surface area to adhesive volume ratio chart
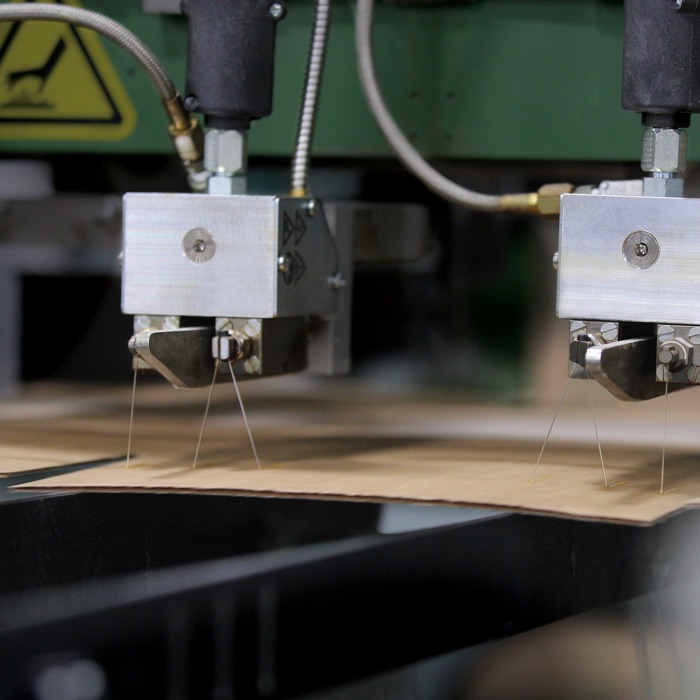
Adhesive char and hot melt nozzle plugs
While traditional heated tanks store anywhere from 4-50 litres of adhesive material, tank-free designs heat less than two litres of adhesive at a time, which means the adhesive is brought to temperature more quickly - under 10 minutes in most cases. This decreased start-up time makes a great difference in uptime and yield over the course of a hot melt system’s lifetime, and therefore translates directly into greater profitability.
The shortened exposure of the hot melt adhesive to heat in vacuum-based tank-free systems also reduces the amount of char formation within the system. With a minimal melted volume, hot adhesive spends less time at a high temperature and is quickly replenished with a fresh supply. Reducing char also reduces material waste and nozzle plugs leading to less overall system maintenance and less production line downtime.
Related articles
Success story: Refressco saves 45% on hot melt adhesive
How bottler Refresco saves 45% on hot melt adhesive in their end-of-line packaging.
InvisiPac optimises QED Environmental System’s packaging process
Learn how QED worked with a packaging consultant to identify areas of improvement and optimise their packaging process.
Tank vs. tankless
Find out what differentiates a system with a tank vs. one that is tank-free.