Automatic lubrication enables efficient and safe greasing
Automatic lubrication is the only option for safe and efficient greasing of heavy equipment.
Many fleets require their machines to be lubricated once per shift, which can take up to an hour for the operator to complete. In most cases, manual lubrication means shutting down the machine and thus losing productivity. On top of that, manual lubrication increases operator fatigue, which is a critical safety issue in high-risk environments.
The downside of battery-powered grease guns
Because of the fatigue caused by manual greasing, many operators choose to use a battery-powered grease gun to make their job easier. Battery-powered grease guns are slightly heavier than their manual counterparts, but a simple trigger pull can deliver grease at pressures of up to 10,000 psi. It is a powerful tool to remove any blockages in the linkage. Combine that portable power with the decreased risk of fatigue and it is easy to see why operators choose battery-powered units.
Although battery-powered grease guns can solve operator fatigue, they also have a downside. With the power and ease of use, operators lose the feedback that lets them ‘feel’ if a grease point is blocked or if the linkage is appropriately greased. Some fleets don’t provide their operators with battery-operated grease guns because they waste too much grease. Some grease fittings may also be very difficult to reach with a manual grease gun and cannot be visually checked for cleanliness. This means that installations cannot be properly lubricated, compromising operator safety and system performance.
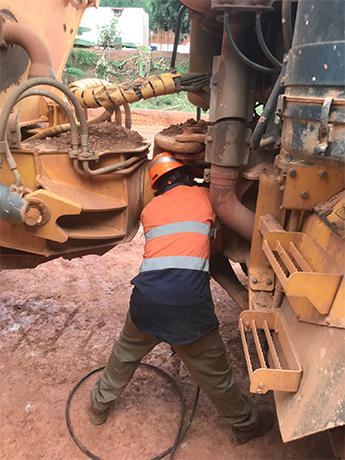
Some grease fittings can’t be visually checked for cleanliness.
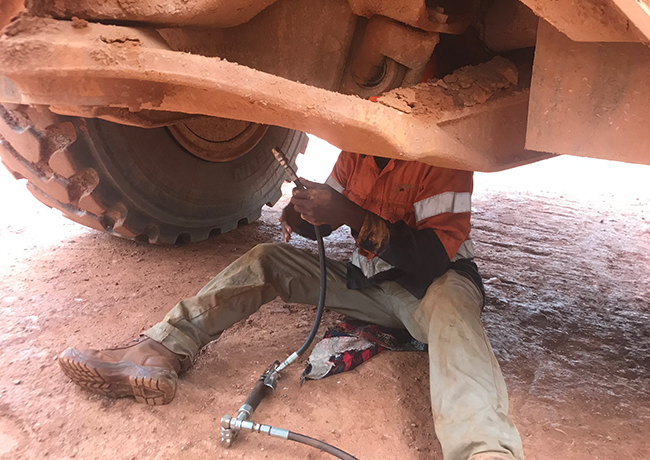
Difficult-to-reach lubrication points lead to unsafe working conditions.
Lubrication should not be a purging operation
Many lubrication technicians treat greasing and lubricating as a purging operation: fresh grease goes into the grease fitting until ‘clean’ grease flows out elsewhere. By doing this, the contaminants are presumed to be flushed out of the system. Given the choice between leaving abrasive and corrosive materials inside the linkage, or wasting grease with a purge operation, most will choose to waste grease, as it is considered the lesser of two evils. After all, it is just ‘a little bit’ of extra grease, right?
However, this method doesn’t waste ‘a little bit’ of grease; it wastes a lot of grease. And the waste increases if the operator is distracted or inattentive during the greasing operation. Using too much grease is not only a waste of material, it also risks violating environmental and safety laws.
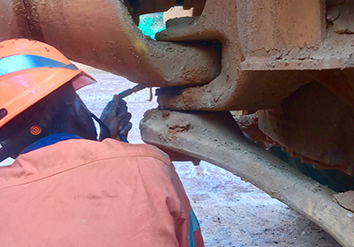
Using too much grease is a waste of material and risks violating environmental and safety laws.
Modern lubricants call for modern lubrication methods
Modern lubricants are specifically engineered in laboratories to provide exceptional linkage protection and high machine performance in some of the worst operating conditions. While the jump in lubricant technology is great for fleet uptime and utilization metrics, it also means old lubrication practices are no longer relevant. Technological innovation provides fleets and operators with more options to optimally lubricate their fleet and increase uptime. Beyond manual, air-powered, or battery-powered grease guns, fleets can choose automatic lubrication systems that lubricate while the machine is in operation, reducing if not eliminating operator fatigue and downtime.
AUTOMATIC LUBRICATION ELIMINATES DOWNTIME
Automatic lubrication is a reliable method to increase your utilization and performance metrics. Automatic lubrication systems deliver a consistent and reliable lubricant supply, continuously keeping machine linkages freshly lubricated, but not over-lubricated. The persistent supply of grease keeps dirt out of the linkage, eliminating the need to purge. Furthermore, the machine doesn’t have to come out of service to be lubricated – further enhancing utilization. Many cases in the field have proven that you can lower annual lubricant usage by 50% or more when switching from manual to automatic lubrication.
Refilling automatic lubrication systems is not without challenges
Just like any machine, automatic lubrication systems require periodic attention, from refilling to ensuring the system is operating as expected. Most automatic lubrication reservoirs are mounted high on mobile, off-road equipment to keep them out of harm’s way. This means most refill technicians have to climb to get access to the reservoir for preventive maintenance.
On very large machines, it is quite common for a refiller to climb a ladder or stairs with a fill hose to connect to the reservoir. Carrying a hose automatically takes away one hand that should be used to safely maintain three-point contact in moving to the reservoir. With reservoirs mounted at great height, it can be difficult to tell when the reservoir is full. There are various solutions to this issue:
- Clear reservoirs within line of sight
Some automatic lubrication systems use clear reservoirs within line of sight of the ground-level fill port. That makes it easy for the refill operator to see when to stop the refill operation in order to avoid spilling or overfilling the reservoir.
- Overfill hoses
In cases with steel reservoirs, some systems use an overfill hose to allow the excess grease to flow out of the reservoir and (hopefully) into a bucket to alert the refiller that the reservoir is full.
- Automatic fill shut-off
These systems automatically stop the flow of grease when the reservoir is full. The operator does not need to see the grease level and no overfill hoses are required. These systems reduce the risk of pressurizing the grease reservoir or wasting grease.
Graco enables refills at ground level with automatic fill shut-off
To make refilling safer, Graco offers automatic lubrication systems with automatic fill shut-off and ground-level refilling options for both electric and hydraulic Dyna-Star and G3 pump auto lube systems. Graco’s solutions work mechanically, meaning one person can safely refill the reservoir at ground level, without the machine being electrically powered.
FIND YOUR PERFECT GRACO AUTOMATIC LUBRICATION SYSTEM
Graco manufactures automatic lubrication systems specifically designed for yellow iron construction and mining equipment. Use our Yellow Iron Kit Selector to find out which automatic lubrication system is the perfect match for your installation.
5 Reasons Why You Need Automatic Lubrication
Protect your equipment and your employees by utilizing automatic lubrication to grease critical lube points.
Related Articles
The pitfalls of manual lubrication
Manual lubrication poses important disadvantages in terms of costs, safety and productivity.
Graco’s leading automatic lubrication solutions: a brief overview
Graco provides a wide portfolio of complete automatic lubrication solutions for any application.
What’s the return on investment (ROI) of an automatic lubrication system?
An automatic lubrication system provides many benefits, but how do you calculate its ROI?