Automated mining mill lubrication helps Slovenská banská save 1.095 maintenance hours a year. And 40% on lubricants.
Graco lubrication solutions help mining company work faster and safer
Two mining mills requiring three hours of manual lubrication. Every single day of the week. Mining company Slovenská banská was looking for a more efficient and safer way to lubricate both ball mils. Our distributor DIAGO introduced them to the concept of automatic lubrication. “They were sceptical at first”, says Martin Šimončič from DIAGO. “But a test set-up convinced them of the benefits.”
Slovenská banská is a mining company in Hodruša-Hámre, Slovakia. They operate in the Rozália mine, located in the depths of the Tanád and Paradajz peaks, where they mine and process polymetallic ores.
For the processing, they rely on four mining mills, of which one functions as a backup. The three mills work 24/7 for a period of three weeks straight. Each ball mill has an output of 10.000 kilograms per day.
It was for two of these three mills that their Head of maintenance was looking for a better way to take care of the lubrication. For a solution, he turned to our distributor DIAGO, a leading supplier of goods, services, and manufacturing of components to industrial companies.
Before: time-consuming and unsafe
Martin Šimončič, vibration analyst and technical support at Diago: “Like most mining companies and cement plants here in Slovakia, Slovenská banská was still lubricating their mills manually.” And just like those companies, they were facing two typical problems:
- It’s time-consuming. In this particular case, it took their technician one hour and a half each day to lubricate just one mill.
- It’s quite an unsafe task to carry out. Or as Martin puts it: “The technician had to lubricate the open gears with a brush, while all the gears were in motion. He had to be very careful as there is no protection.”
Test set-up in the Rozália mine
“We explained to the Head of maintenance how an automatic lubrication system could counter these pain points. Their team was sceptical about our solution at first. I totally understand that as it’s a different way of working. So we did a test set-up in the Rozália mine. It ran for two months. And they liked it.”
After the test, DIAGO got the go-to design, a solution for the two ball mills. The main components of that solution are:
- A Fireball pump
- Air-Assisted PerformAA Spray Guns
- And a GLCX Controller
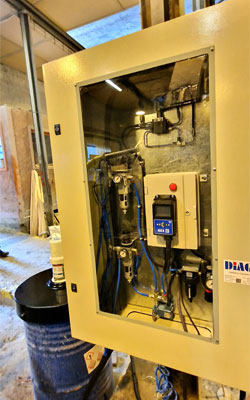
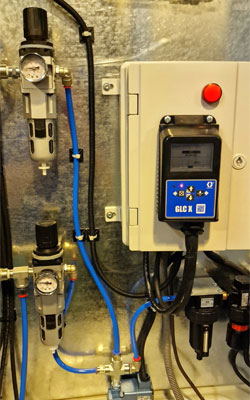
“The Fireball is ideal for tough environments like the mining industry. Slovenská banská wanted to dispense the lubricant from 200-liter barrels – this pump is perfect for that.”
“Our technicians set up the automatic lubrication system in our own workshop first. That way we could test everything out and make sure the installation would run smoothly. On site, it took us just four hours per mill to integrate this new system.
“The pinions now last longer. Before, they used to wear out very quickly”
Martin Šimončič, vibration analyst and technical support at DIAGO
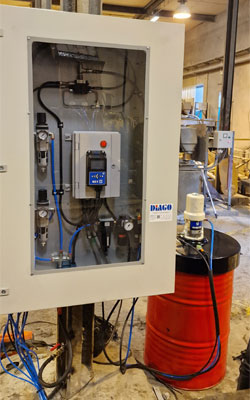
“The system has been operational for a few months now. And the results are great. They especially notice that the pinions last longer”, says Martin. One of the advantages of an automatic lubrication system is consistency. Once you have determined the ideal spray pattern and frequency, you are sure the gears are constantly being lubricated correctly: the right amount of lubrication, in the right place at just the right time. “This also means a big savings in lubricants. Slovenská banská now saves up to 40% compared to manual lubrication.”
Often overlooked
The savings in lubrication is often overlooked when calculating the ROI of switching to an automatic lubrication system. Companies are primarily looking to cut back on maintenance hours and improve worker safety. But the big savings in lubricants also have to be taken into account.
“The system has been up and running for a few months now”, concludes Martin. “Slovenská banská is satisfied. And for me, this proves that other mining companies and cement plants could greatly benefit from an automated lubrication system.”
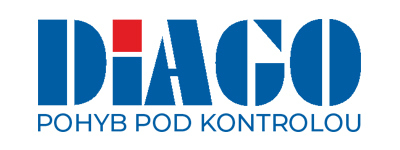
Contact us for more info
Related Articles
1956 Fire-Ball Pump Unearthed
In 1955, Graco introduced its first Fire-Ball Air-Powered Oil and Grease Pump. Since then, the Graco Fire-Ball pump has built a strong name for itself as the most reliable oil and grease pump in the industry.
How to choose the right Off-Road Auto Lube System
Each type of heavy equipment has different component specifications that are required to make up an auto lube system that will properly supply the correct amounts of lubricant to each lube point at the correct time intervals. Learn about these specifications and components...
Keeping Komatsu dump trucks up and running
The Graco Mining Kit was installed on 14 Komatsu dump trucks to provide efficient automatic lubrication in tough conditions.