Energy From Waste (EFW) facility switches to automatic lubrication system: “Manual lubrication was too error prone”
Graco’s solution reduces stress, maintenance time and grease bill for Lakeside EfW
“This automatic lubrication solution has completely removed any chance of human error. Every lubrication point on our moving grate system and ash conveyor is getting the right amount of grease at the right time.” Mechanical engineer Darren Jones and mechanical technician Alex Fox take you behind the scenes at Lakeside EfW in Colnbrook, United Kingdom, to give you a closer look at the Graco pumps, controllers and injectors that make this possible.
Waste comes in, electricity goes out.
Lakeside EfW generates electricity from burning residual waste, using steam to power a turbine. The incinerator obviously plays a crucial role in this process. It is in this part of the plant two of our distributors integrated two automatic lubrication systems: one for the moving grate system, and one for the ash conveyor.
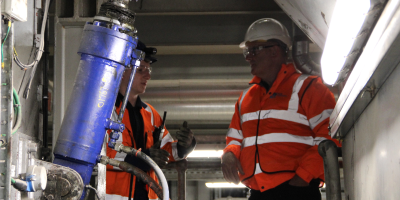
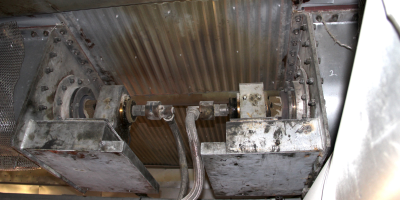
Two different locations, yet both were facing the same problem: the quality of lubrication was too dependent on the technicians.
Darren Jones: “We were carrying out the lubrication tasks manually. But this proved to be too error prone for different reasons. This plant runs 24/7, so we have different shifts of technicians carrying out these tasks. And not everyone has the same level of expertise.”
Alex Fox: “There are also some difficult to reach places. Making it hard to lubricate these parts correctly or even visually check if everything is in order. With over 90 different points to maintain, this led to parts being under- or over-greased. The bearings degraded faster, and there was grease on the floor, causing slip hazards. Plus, we were wasting lubricant.”
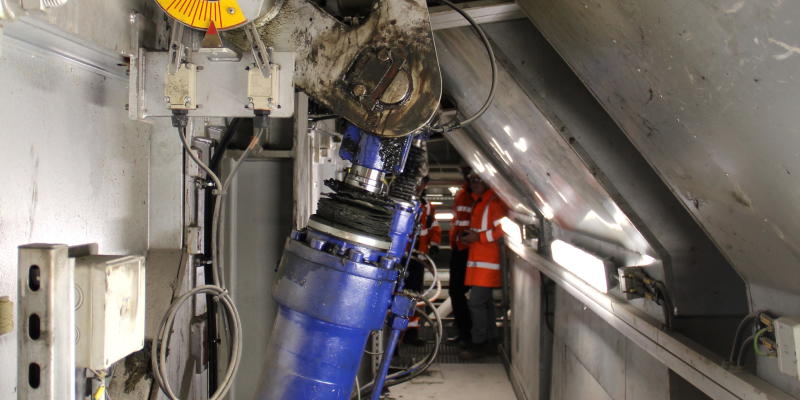
Alex Fox: “There is still old grease coming out and dripping on the floor, so it’s still a bit messy. But before, the over-greasing would create an absolute mess, which then would attract dust and dirt.”
It was clear manual lubrication was not working for Lakeside EfW. So the team started looking for an automatic lubrication system that could guarantee a consistent quality, and would not make the quality of maintenance dependent on the technicians.
Darren contacted our distributor TCE Transmission, who engineered the solution. The installation was done by Lubezone. The distributors got the support of two Graco product specialists.
Now let us have a look at the set-up. First for the moving grate system, second for the ash conveyors.
Graco moving grate lubrication system
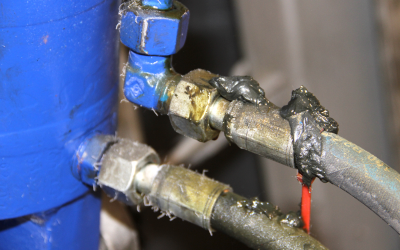
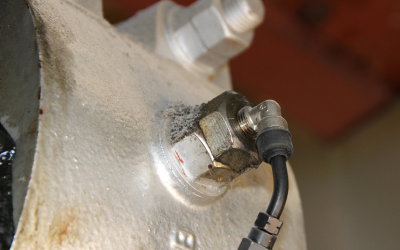
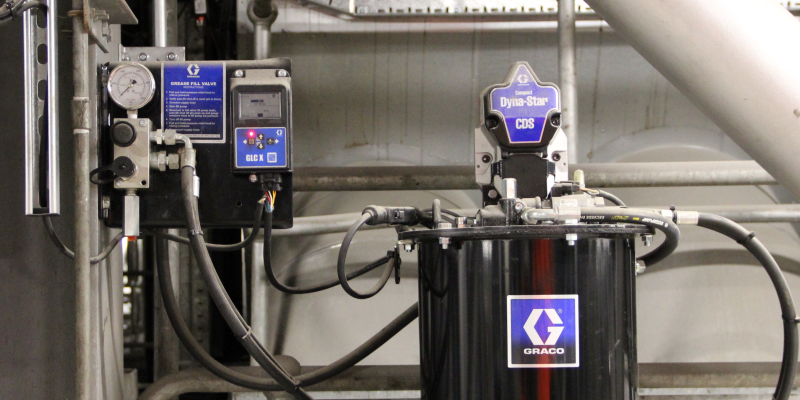
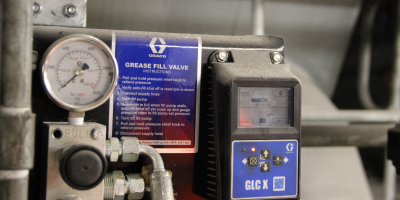
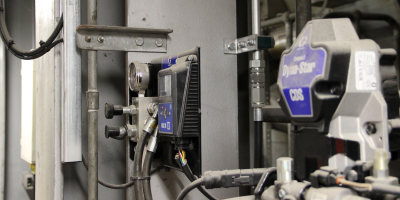
Graco ash conveyor lubrication system
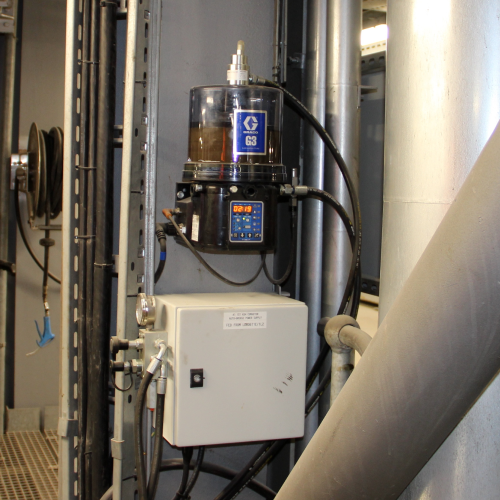
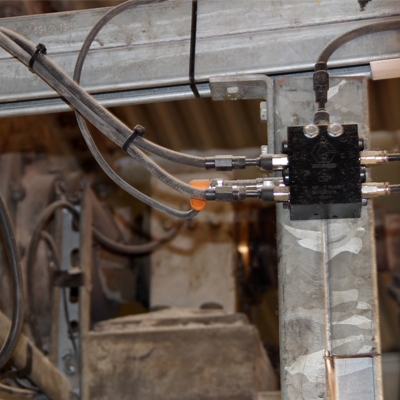
Darren Jones: “Both Graco systems have been running for some months now, and have completely removed human error. We are now sure that every point is getting the correct dosage of grease at the optimum cycle time. This gives us peace of mind.”
Problem solved. But this is not the only upside.
Alex Fox: “Both lubrication systems have reduced the time it takes to check reservoirs. There is this digital readout, showing the level of grease in the dispenser, and a level indicator. During my walk arounds, I can just glance at it, look at the level and I will immediately know how much is left in the reservoir. When the level is too low, a little red indicator light shows.”
“The Graco app is great as well. I walk up to the pumps, unlock my phone, press one button, tap the screen and it brings up both systems. I can read out the stats and quickly change settings. Happy days (laughs). I mean, it is pretty hard not to understand how the app works. It is very intuitive. Everyone on the team finds it very easy to use.”
Saving time and money
Darren Jones: “Due to the precise amount of grease being dispensed, there is no longer any wastage. So these lubrication system are saving us money too.”
“The example Alex gave, shows we are also saving time. The daily check-ups can be performed faster. We do not have to spend ten minutes a day on manual greasing, and we do not have to refill the manual grease dispensers. Before, this took our team around an hour and half, every month. Maintenance and upkeep have been greatly reduced, so our maintenance team can now focus on other tasks and other plant areas.”
“And last but not least, it has reduced the need for communication between departments, as this system can be solely managed by the maintenance team.”
In short
Lakeside EfW’s team was struggling to get the lubrication right for their incinerator grate system and ash conveyor. They switched from manual lubricating the parts to a Graco automatic system.
- Improved reliability: no more human errors causing under- or over-greasing. All points are getting the right amount of lubrication at the right time.
- Fewer hours spend on maintenance: no need for manual lubrication, and no more filling up all those separate reservoirs. That means more time for other priorities.
- Material savings: over-greasing means grease being wasted. Lakeside now saves on their lubrication bill.
- Ease of use: easy to check and easy to maintain.
Or as Alex puts it: “It is all thumbs up from me so far.”
GCI stopped the squeak fest
The engineering and integration of both automatic lubrication systems was a collaboration between two of our distributors: TCE Transmission and Lubezone.
This project encompassed the first ever integration of the Graco GCI injectors in the United Kingdom, in Europe, even. Tony Condon, Managing Director TCE Transmission: “The distances to the lubrication points were not that long, but to sufficiently supply 90 points, was a big undertaking. A lot of thought went into this.”
“The grease now comes out the same colour”
“The first time I walked in here, it was a proper squeak fest. The bearings were screaming. Now, the grease is coming out the same colour – that is s how you know it is bleeding right through. And that every point is getting the right amount of grease.”
“It is nice to see the Lakeside teams are all using the Autolube app. Off course, the young chaps like Alex will. But it is great to hear that the older chaps like myself are also joining in. That proves that the app is easy to work with.”
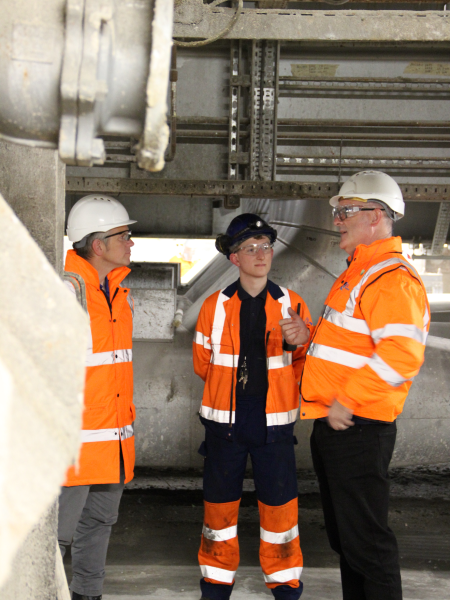
From left to right: Will Benton (Graco), Alex Fox (Lakeside EfW) and Tony Condon (TCE Transmission)
Generating electricity from waste: how does that work?
Lakeside EfW is a joint venture between Viridor and Grundon Waste Management. The plant is located at Colnbrook in the United Kingdom, close to Heathrow Airport. It processes over 450.000 tons of residual waste per year. From that waste, Lakeside EfW generates 306GWh of power – enough to provide electricity to more than 85.000 households.
But how do they convert waste into electricity?
- Waste trucks come in and unload into a waste bunker. From here, the waste is transported to an incinerator.
- The incinerator burns the waste until only ashes remain. The temperature inside climbs to 850°C. The ash falls through a moving grate system onto a conveyor belt. The heat is used to produce steam.
- This steam sets a turbine in motion, which in turn generates electricity. That electricity is put on the grid.
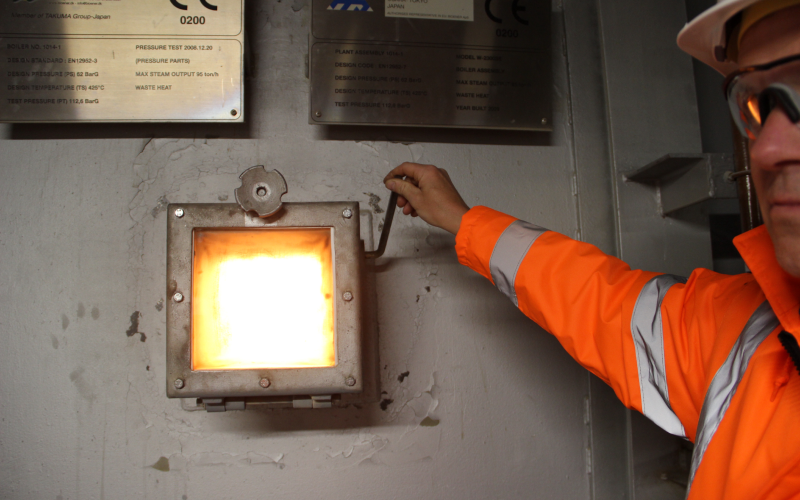
Front row seat for the incinerator at Lakeside EfW.
Want to know more about the processes? And how, for example, the combustion gases are filtered out? This page explains every step in more detail, including videos.
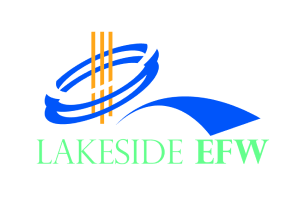
Contact us for more info
Related Articles
The Importance of Trailer Lubrication for Brakes and Bearings
Automatically lubricate not only your tractor, but your trailer too.
Simplify Lubrication with Automatic Grease Systems
Make manual lubrication a thing of the past with an on-vehicle automatic lubrication system.
Effects of Lubricant Contamination
Discover how to avoid lubrication contamination from causing a major disruption in your operation.