Fruit packaging: ZZ2 now seals their cardboard boxes with 64% less glue
ZZ2 in South Africa was facing two problems with their fruit packaging’s hot melt delivery system. One: the farming enterprise was spending too much money on hot melt to glue their fruit boxes. Two: nozzle blockages were causing liability problems. Switching to the InvisiPac hot melt packaging system proved to be the answer. ZZ2’s packaging manager Ferdie Jacobs talks you through the decision making, the integration and the results.
ZZ2 produces and exports various crops, such as tomatoes, apples and pears. It’s one of the biggest farming conglomerates in South Africa, operating mainly in the Limpopo Province.
This story starts in 2020, in one of their packaging houses in that same province.
Their packaging manager Ferdie Jacobs wanted to cut back on the amount of hot melt they used to glue their cardboard packages. So we set up a test. We replaced one of their glueing machines with our InvisiPac.
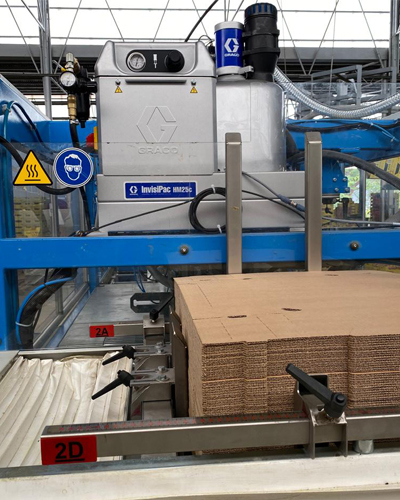
The integration of InvisiPac on one of ZZ2’s fruit packaging lines.
The test was supposed to last six months. But ZZ2 already placed a first order for five units after just two months. “By that time it was clear that we could save around 60% glue, while also improving the uptime of our packaging lines”, says Ferdie.
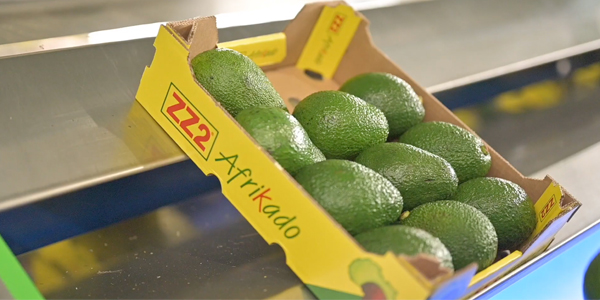

Before: nozzle blockages every day
That uptime was the second big problem ZZ2 had to tackle. Their current glue dispensers suffered from nozzle blockages on a daily basis. They also had issues with adhesive char. With the technology they were using at that point, these are common issues. Those type of systems tend to overheat – even burn the glue. Those burned particles then go through the hoses and eventually clog up the guns.
A problem Ferdie had to solve. All that downtime was preventing their lines to reach full capacity. And ZZ2 needed all the capacity they could get, as they had to improve the output of their fruit packaging to meet growing client demand.
Their fruit box glueing system was becoming more and more of a bottleneck.
“The trial proved that InvisiPac could solve that issue. Our previous unit had to heat up the complete tank. InvisiPac however, melts on demand. This prevents the glue from overheating.”
Now: 24 million boxes packed, only 4 blockages
That was in 2021, in one particular packaging house.
Fast forward to a few years later. Now, all ZZ2’s high flow packaging lines are running on InvisiPac. We integrated our units in 18 of their sites, spread across South-Africa.
“On average – across all our packaging houses, all our different lines and for all different boxes, we now save 64% on glue.”
Also the uptime improved. When they reached 24 million boxes packed, ZZ2 only encountered four nozzle blockages. That means more boxes being packed with the same amount of packaging lines. What they were doing with two lines, now can be handled by one. With one line to spare, they can now easily crank up their production when necessary.
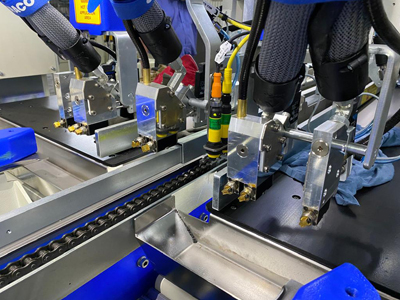
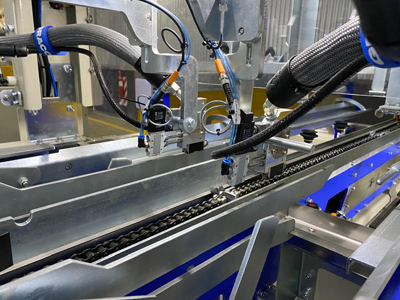
A closer look at one of the conversions.
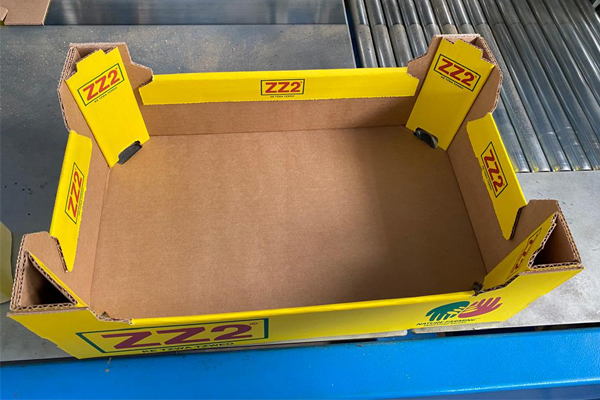
One of the cardboard fruit boxes we are talking about. But as ZZ2 has to pack different sorts of fruits for import ánd export, the boxes vary in size.
Quick fruit packaging line conversions
“Together, we replaced our old glue systems with the InvisiPac. One pack house at a time. Although our fruit packaging lines vary in size and we have different brands of packaging machines, it was pretty straight forward.”
The InvisiPac is designed as a drop-in replacement. It fitted on the same platform as their previous system. On top of that, we could simply reuse the configuration we made for one particular InvisiPac for other units handling the same cardboard fruit boxes. This saved a ton of time.
We even swapped out units that were still working fine. One of the glue systems we replaced was only three months in use. But even for that new unit, it made sense to convert it.
ROI: savings + uptime + maintenance + …
Swapping out a brand new hot melt delivery system… how can that make sense?
Well, next to the glue savings and improved uptime, four other factors contributed to a high ROI.
- We were able to keep the original hose routing. Hendrik: If you need to switch out the hoses altogether, you are talking about a bigger investment. In this case, their existing set-up was compatible with our InvisiPac.
- No more need for unexpected maintenance or clean ups. Blocked nozzles not only mean poorer uptime, but also that one of your operators loses time to solve the problem. Likewise for extra clean ups. ZZ2’s previous set-up tended to drip, spilling glue on the rollers and other components. These drips also prevented boxes to be positioned correctly.
- No more time being wasted refilling the hot melt granules. “Before, an operator had to climb up the machine with a bucket to fill the glue reservoir. That costs time. And it’s also a dangerous task to carry out, as the machine is still running. InvisiPac works with a feeding system and a separate container. Faster and safer to refill.”
- No more need for their operators to come in early. “Our previous system had to heat up for two hours”, says Ferdie. This meant that on each and every of their sites, ZZ2 had to pay an operator overtime to come in early to start up the machine. “Now we just switch on the InvisiPac, and after ten minutes it’s good to go.”
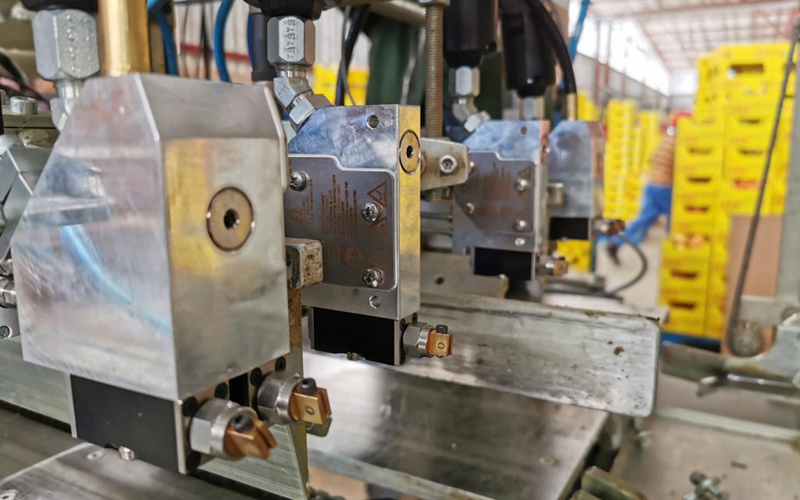
The new set-up
And actually, there’s a fifth and final pro argument. Because ZZ2 could not fully rely on their previous hot melt dispense systems they used to prepack boxes. So when the line came to an unexpected shutdown, they had a back-up. They would prepack 30.000 boxes. That’s a warehouse full with empty boxes. Wasted space.
Front runner
The final word is for our Graco Africa sales manager Hendrik Papenfus. “ZZ2 is one of the biggest agricultural companies in this country. They are front runners when it comes to technology. That such a big name put their trust into us and our equipment – that feels great.”
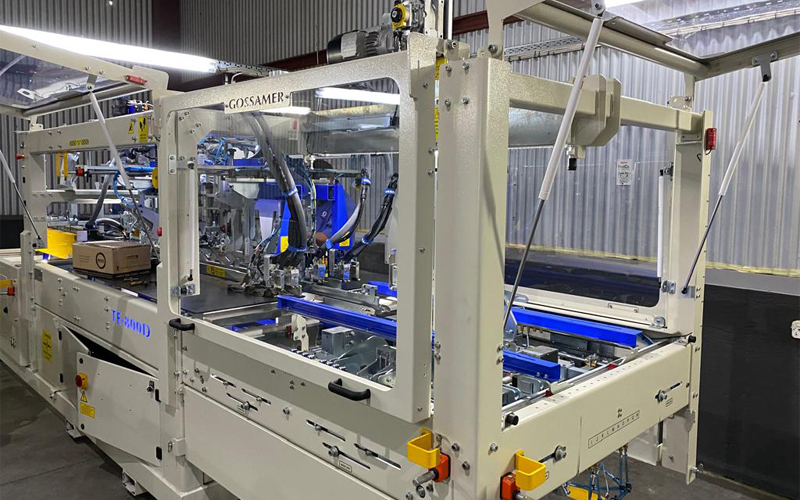
In short
- South-African farming enterprise ZZ2 wanted to level up their cardboard sealing systems.
- We integrated our InvisiPac hot melting system in 18 of their packaging houses.
- The conversions were carried out between 2021 and 2024.
- ZZ2 now saves 64% on hot melt to seal their cardboard fruit boxes.
- Daily nozzle blockages are no longer causing unexpected shutdowns.
Thanks to a better uptime, ZZ2 didn’t have to invest in new fruit packaging lines to up their output.
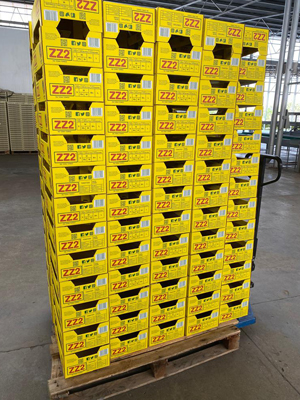
Related Articles
The Venturi effect and InvisiPac
The video explains how a simple concept from a dude with a fancy name makes an incredible piece of packaging equipment, called the InvisiPac Tank-Free hot melt system, work.
Mondelēz Namur sticks with InvisiPac
After a six-month trial, the Mondelēz plant in Namur decided that the Graco InvisiPac was the ideal hot melt delivery system for them.
Why InvisiPac is the reliable option for your packaging line?
An InvisiPac tank-free hot melt glue system with melt-on-demand process avoids charring and nozzle blocking.