What causes hot melt adhesive char?
Three causes of char
For most end-of-line packaging operations, adhesive char is often the main cause of most downtime incidents. Once char is in a hot melt system, it is almost impossible to remove without taking extreme measures. Even after system flushes, char may still stick to tight corners within the system and continue to cause problems that effect uptime and productivity.
There are three main causes of char – overheating, contamination and oxidation – and all are occurring in most hot melt packaging applications on a regular basis. Learn more about each of these causes and how to avoid them.
Video: Causes of adhesive char
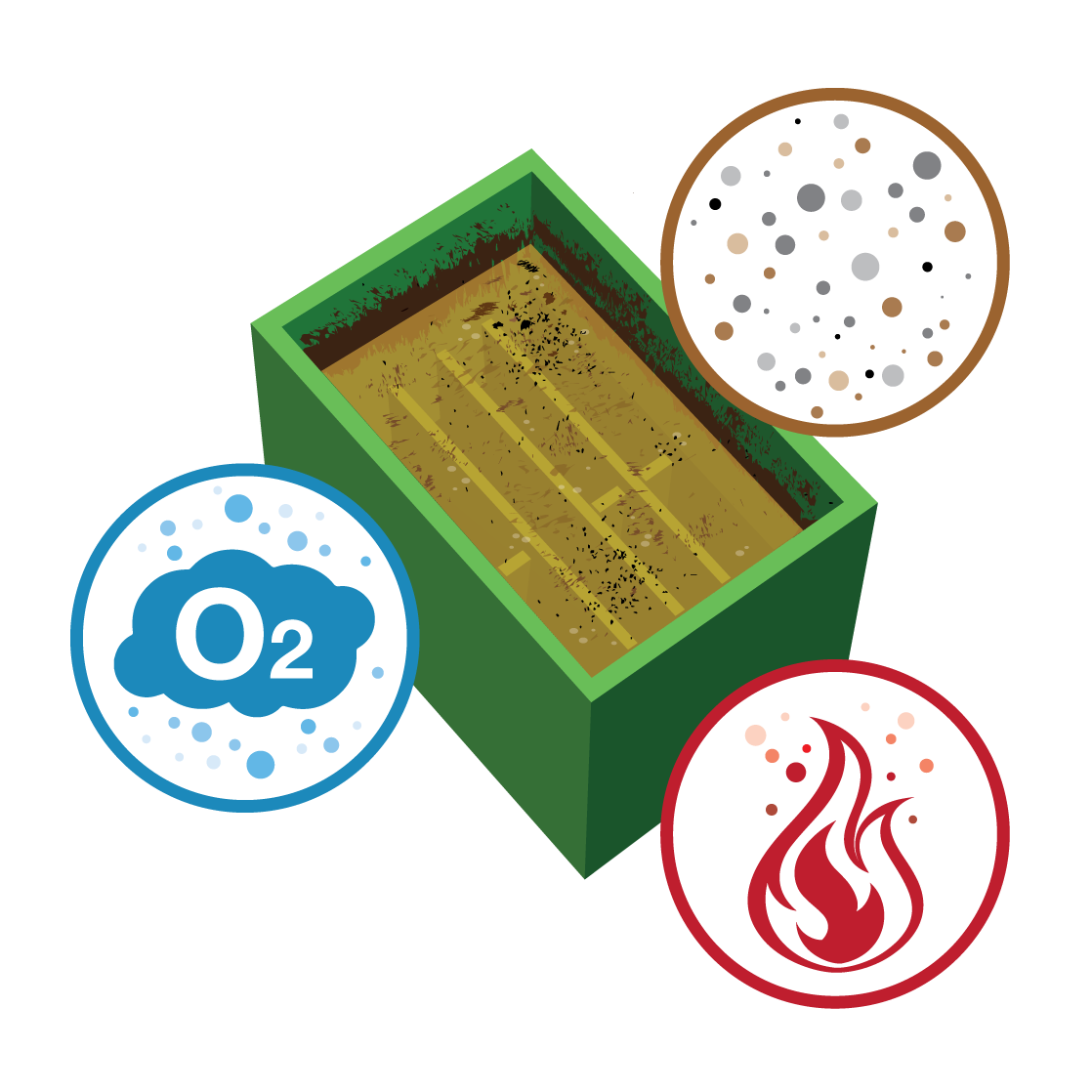
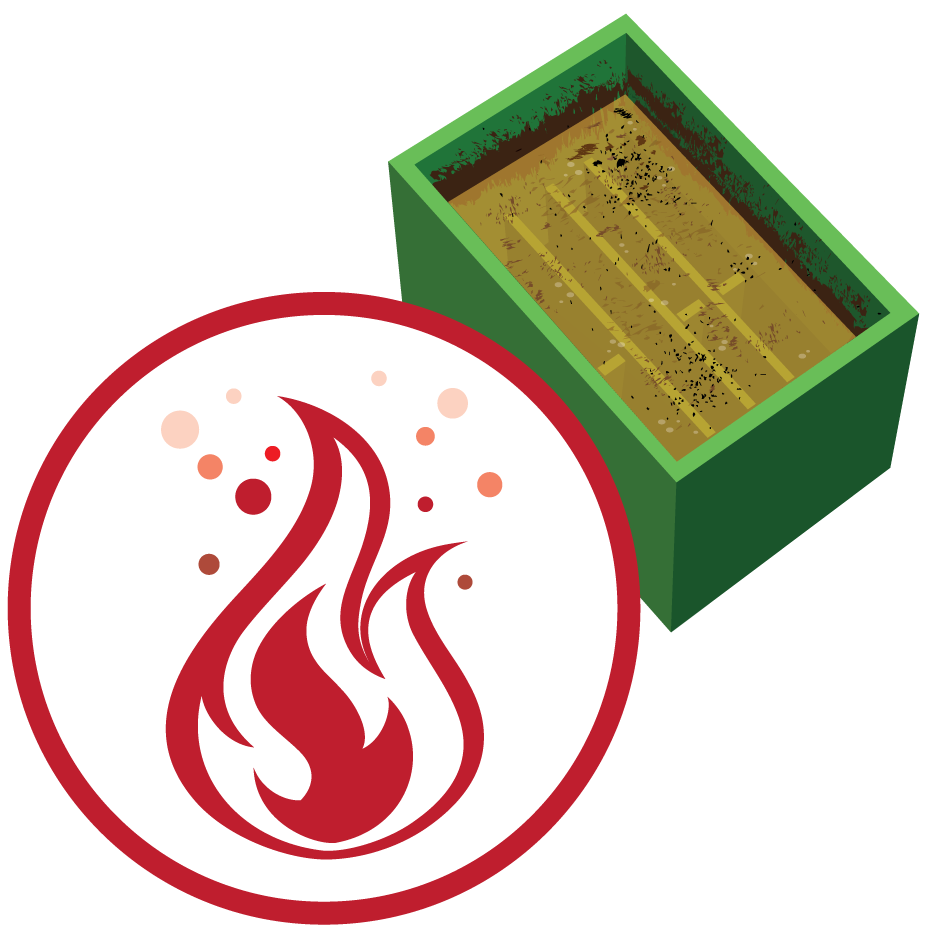
Overheating
The formation of char begins as adhesive breaks down and forms into gels after long exposure to heat. These gels are unable to flow through a hot melt system and eventually stick to walls of melting tanks and hoses. Once adhered to the system components, the gels are exposed to excessive heat over an extended period of time and become burnt or “charred”.
Traditional tank-based and tankless hot melt systems use melting tanks to heat the adhesive to the required temperature. The adhesive along the outside of the tanks is exposed to higher heat levels and burns more quickly, much like a crock pot will create charred food around the perimeter. This inefficient heating method is usually compounded by some common practices found in many end-of-line packaging applications:
1. Leaving hot melt systems and metering tanks turned on for extended periods of time
2. Increasing system heat settings to compensate for temperature loss or “shocking” when adding room-temperature adhesive to the heated system
3. Using a disproportionate melting tank size for the adhesive throughout
Regardless of the application, if the hot melt adhesive is sitting in a heating tank for any length of time it is degrading and creating adhesive char.
Contamination
While heat and oxidation are the two primary causes of adhesive char, environmental contaminants such as dirt and dust can also create char. Many manufacturing facilities such as bakeries, dairy production and paper converting have a significant amount of contaminants floating in the air as a result of the processes involved. If there is poor ventilation and operators are opening lids on the hot melt systems, particulates can enter into the melted adhesive, burn, and eventually turn into adhesive char that will stick to system components.
Ultimately, prevention is the best approach to dealing with adhesive char in end-of-line packaging operations. With proper equipment and procedures, you can prevent adhesive char from creating costly downtimes due to unplanned maintenance issues.
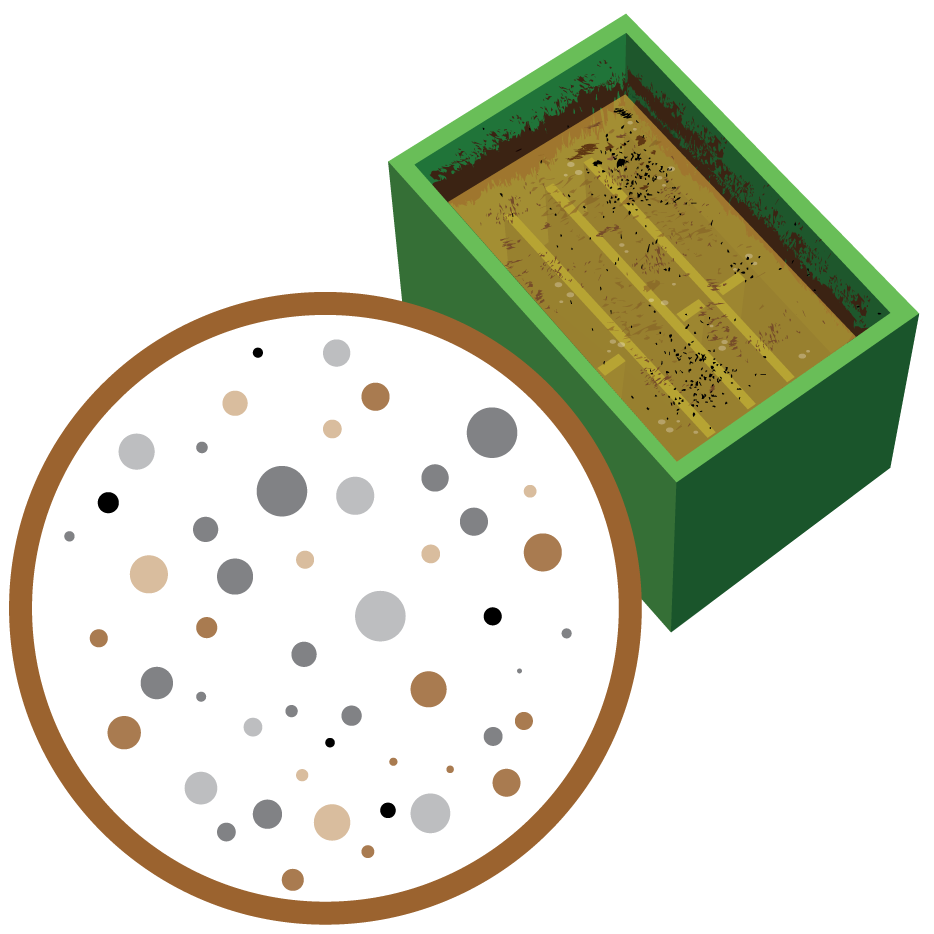
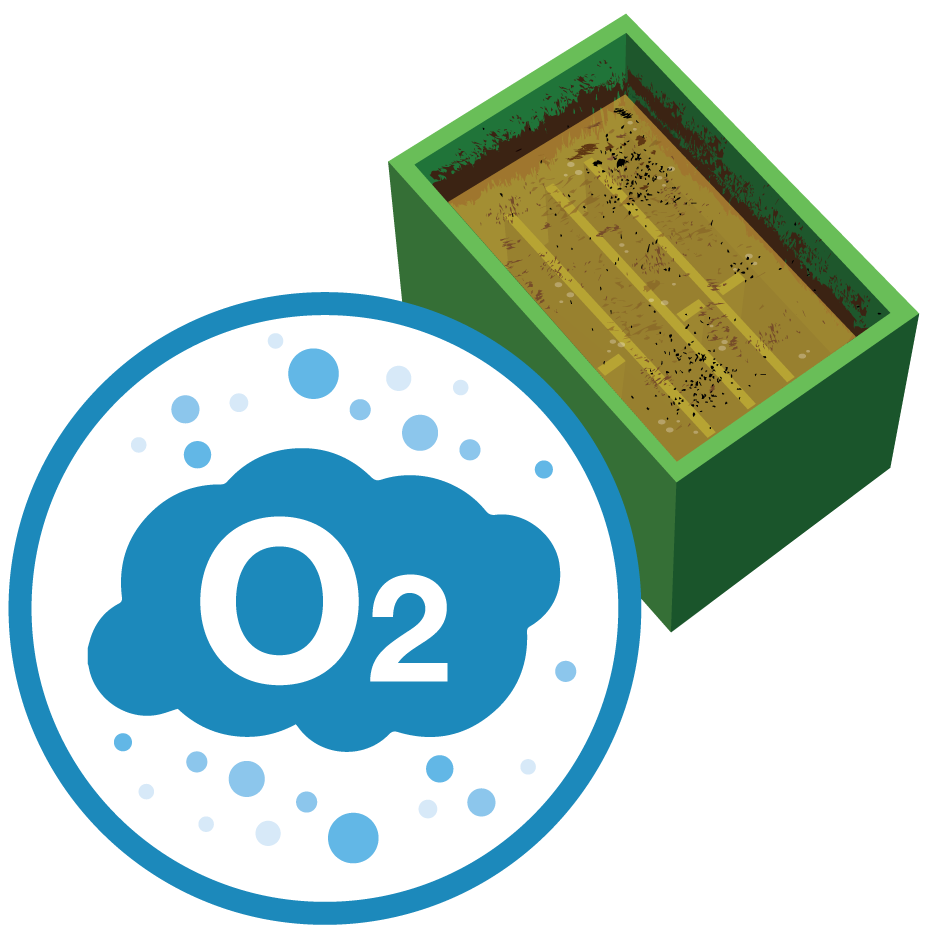
Oxidation
Adhesive char can also form if molten adhesive is exposed to air on a regular basis. This can occur if the level control of the adhesive is not properly maintained or if the operators are constantly opening and closing the lid on the system. This is a common occurrence as most hot melt systems require manual feeding of adhesive pellets due to nonexistent or inoperable automatic feed systems.
How Graco's InvisiPac avoids char
The InvisiPac Tank-Free Hot Melt System eliminates the three leading causes of char by using innovative melt-on-demand technology.
Related articles
Choosing a hot melt nozzle
The choice of hot melt nozzle impacts the performance of your end-of-line packaging operations.
Comparing the operation of hot melt systems
Comparing how different hot melt systems are designed to dispense material.
Create a safer hot melt environment
Here are four steps you can take to improve the hot melt safety at your facility.