Saving costs in the production line with InvisiPac
SEM, Sistemas En Marcha, a Spanish company located in Onda, is a benchmark in the design of complete polishing, cutting and grinding production lines.
When they built a new plant to polish and square PLP tiles, they needed their new production line to be safe and start-up fast with no downtime due to nozzle plugging or charring issues.
11kg per hour melt rate
Local Graco distributor Domo3, proposed two Graco InvisiPac™ tank-less hot-melt application systems. One system was installed with two hoses and swirl applicators to apply wax swirls on tiles to avoid damage to stocking. The second system was installed with four hoses and standard applicators for two different applications:
- closing carton wraps around tiles;
- stocking tile boxes by 2 or 3, just before a robot pallet application.
Initially, SEM had planned to install three standard melt-tank units, one for each application. However, thanks to the design of InvisiPac that has a small melt chamber of 0.6 kg and a melt rate above 11kg/hour, three applications could be covered with only two InvisPac systems.
Auto refill system & non-char design
InvisiPac is equipped with an automatic refill system which permits the line supervisor to focus solely on the quality of the production without being distracted by having to manually refill the hot-melt tanks with all the risks of charring. This integrated vacuum system feeds the melt chamber with pellets as required by the line. The low capacity of the melt chamber, associated with the free-flow design ensures a non-char production that enables PLP-SEM to use a low-cost hot-melt adhesive without the risk of adhesive degradation or nozzle plugging. These features also permit SEM to maintain its safety and clean-zone policy. With the InvisiPac’s start-up time of 10 minutes, SEM has more production flexibility, less energy consumption and has improved its production and efficiency rate.
More information
For more information about Graco's hot-melt systems, fill in the form below.
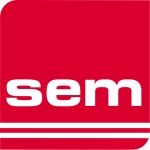
Related articles
Replacing a standard old tank with an automatic feeding system to efficiently seal boxes
Sealing the “top & bottom” of boxes of treated seeds with a 10 minute start-up time, no char, nor nozzle plugging and very good application.
Improve hot melt system performance
Improve the overall profitability of your packaging line by understanding the high price of outdated processes.
The costs of hot melt system cleaning & maintenance
Maintenance costs can quickly add up. Avoid unplanned downtime and replacement parts costs.