How bottler Refresco saves 45% on hot melt adhesive in their end-of-line packaging
“Initially, we were talking about 30% savings. But we accomplished to reduce our hot melt adhesive usage with 45%.” If you know that Refresco Iberia yearly packs 1.000 millions liters of soft drinks and juices, that is a lot of money. Operations manager Fidel Castello and engineering manager Josep Ferri Sanz explain how InvisiPac makes this possible.
Refresco is the world's largest independent bottler of beverages, with production sites in Europe, North America and Mexico. They have over 80 factories worldwide.
This case is situated in their end-of-line cardboard packaging in Refresco Iberia, Spain.
-45% hot melt adhesive usage, -40% electricity consumption
Juan Manuel Pizarro, Graco’s packaging sales manager: “We started out with two test units in one plant, now over 20 lines have been converted to InvisiPac. We are currently setting up an action plan for other Refresco sites.”
This success was driven by Josep Ferri Sanz and Fidel Castello, who took the lead in optimizing the processes. At Refresco Iberia, we achieved an impressive 45% reduction in hot melt adhesive usage across all our production lines, surpassing our initial target of 30%. Josep explains, “Additionally, we significantly reduced our electricity consumption by 40%. InvisiPac has proven to be a valuable asset, not only lowering costs but also making operations easier for our team, with less maintenance required from our technicians.”
“One of the biggest compliments we as a manufacturer can get, is what Josep Ferri Sanz mentions near the end of the video. One year after the installation, his colleagues on the factory floor have forgotten about the integration: the set-up process was that smooth.”
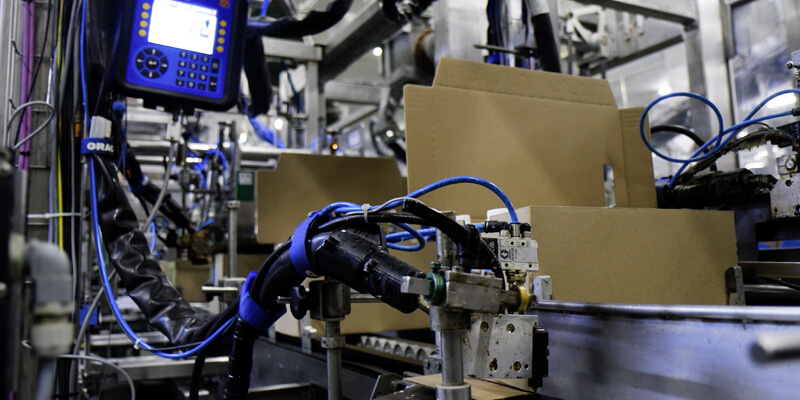
End-of-line packaging at Refresco Iberia.
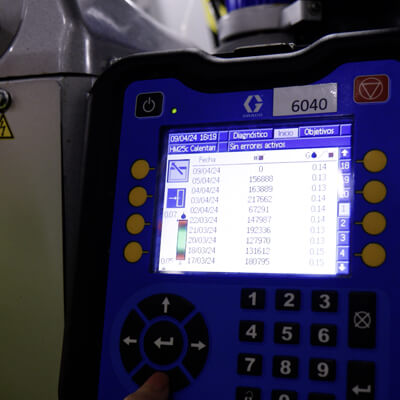
Advanced display module (ADM).
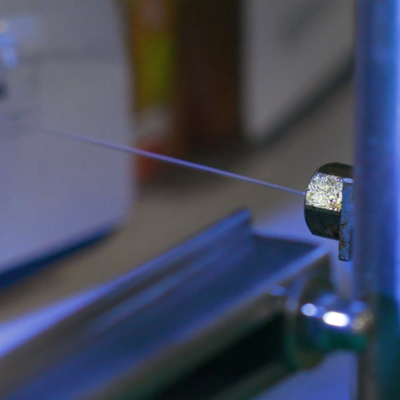
Hot melt adhesive being dispensed.
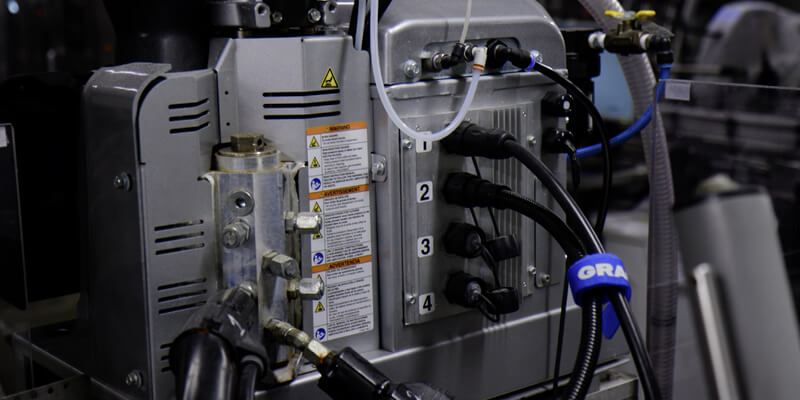
A look at the set-up.
Make InvisiPac work for your cardboard packaging
InvisiPac is a melt-on-demand, tank-free adhesives system. It makes your end-of-line case and carton sealing faster, safer and more reliable and cost-effective.
With a true melt on demand principle, this hot melt delivery system eliminates adhesive char and improves your productivity.
InvisiPac has been proven to:
- Cut energy costs with 45 up to 72%, compared to other systems;
- Reduce adhesive consumption by up to 50%;
- Hugely reduce maintenance time and machine downtime;
- Enhance operator safety by eliminating exposure to hot adhesive;
- Greatly reduce the environmental impact of the hot melt system.
Find out more about InvisiPac: www.graco.com/invisipac
Related Articles
Fruit packaging: ZZ2 now seals their cardboard boxes with 64% less glue
ZZ2 in South Africa was facing two problems with their fruit packaging’s hot melt delivery system. One: the farming enterprise was spending too much money on hot melt to glue their fruit boxes. Two: nozzle blockages were causing liability problems. Switching to the InvisiPac hot melt packaging syste...
Mondelēz Namur sticks with InvisiPac
After a six-month trial, the Mondelēz plant in Namur decided that the Graco InvisiPac was the ideal hot melt delivery system for them.