Reduce downtime caused by adhesive charring
Adhesive char, nozzle plugs, and hot melt materials
When adhesive properties are altered through thermal and oxidative degradation, the thermoplastic nature of the adhesive is lost, leading to overheating or "charring" of the hot melt adhesive.
Adhesive char is the single major cause of hot melt equipment failure and downtime for end-of-line packaging and case and carton sealing applications. Overall downtime costs from adhesive char can easily be $5,000-$15,000 per hour/per line depending on the application.
Adhesive char increases maintenance and operating costs
Traditional hot melt systems feature a form of a heated tank that maintain large volumes of molten adhesive for hours or days at a time. Along with varying fill levels, these long heat soaks negatively impact hot melt adhesive consistency – producing hard clumps of adhesive char that will not flow through the system.
These hard clumps of charred adhesive cause plugging in hot melt hoses and dispense nozzles, causing unplanned downtime that negatively affects the productivity of the manufacturing process. It is common for line operators to keep a surplus of replacement nozzles at hand to help minimize downtime.
Similar to plaque in a hardened artery, layers of char build up inside a hot melt hose - making it harder to effectively maintain consistent glue viscosity through the entire system. As a result, hoses must be replaced more frequently. If adhesive char is a common problem, it will also get into the system’s pump and ultimately lead to premature failure of fluid seals in pumps and guns.
Depending on the production process, the profitability impact of adhesive char can be significant depending on the problem. Some examples of hard costs from char-related issues (not including related downtime):
- $600-$1,200 - hot melt hose replacement ($100 per foot)
- $1,500-$5,000 - pump replacement and rebuild process
- $7,000-$14,000 - capital cost for additional units
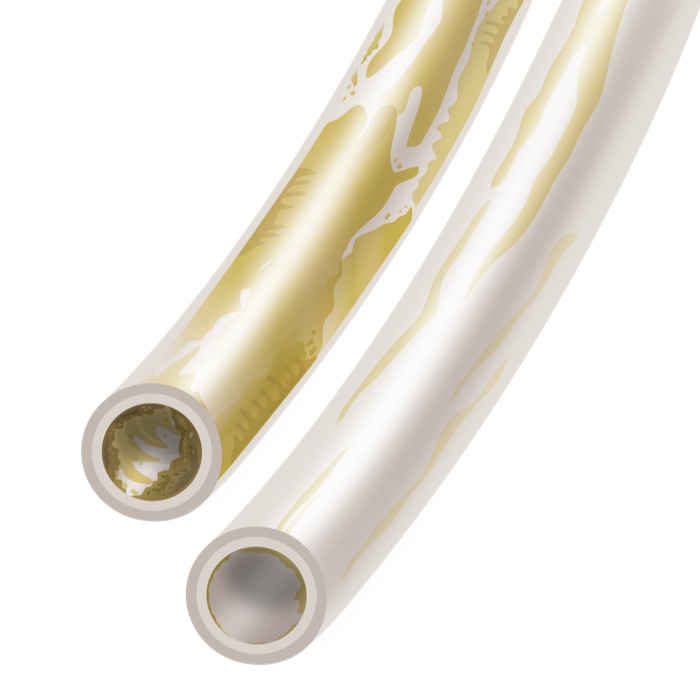
Layers of charred hot melt adhesive can build up inside hoses
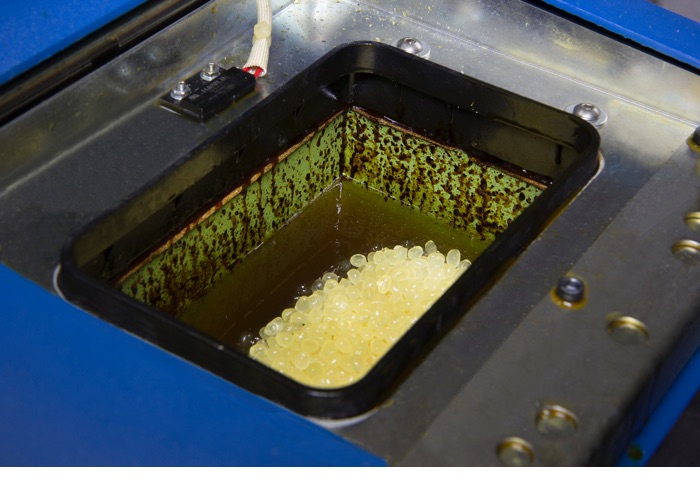
Adhesive char build-up in a traditional, tank-based hot melt system
Downtime caused by cleaning hot melt nozzles & tanks
In addition to hard costs of replacement parts due to char plugging, heated tank systems often require routine cleaning and maintenance to avoid excessive char buildup. These cleanouts can be labor intensive and time consuming, further affecting uptime and productivity.
Manufacturers may have to take tanks offline to completely scrape the inside of a tank free of adhesive char buildup. In some applications, a surplus of hot melt units are often available to keep lines running during these routine tank scrapes. These tank scrapes can take at least half a day to accomplish – resulting in labour and overhead rates from $1,000-$1,500. Companies not equipped to do the tank scrape in-house may have to send the tank out to have the char removed, adding refurbishing and shipping costs, as well as additional lost uptime.
Once the system is cleaned of char, the tank-based technology wastes valuable uptime reaching operating temperature. To avoid charring and its consequent costly downtime during normal production, operators will often leave hot melt tank systems on (even when a plant is shut down) wasting energy and further reducing profitability.
New melting technology eliminates adhesive char
Instead of traditional tanks, new hot melt systems using Tank-FreeTM technology use specially designed melting chambers. The elimination of heated tanks improves hot melt equipment performance dramatically. By providing a greater melting surface, these melters are more efficient and provide significantly faster heating times - achieving operating temperature in 10 minutes or less compared to start-up times of at least 45 minutes with traditional hot melt tanks.
The shortened exposure of the adhesive to heat in these systems also reduces the amount of char formation within the system. Less time at temperature results in less adhesive char. With a minimal melted volume, hot adhesive is dispensed quickly and replenished with a fresh supply. The reduction of char leads to:
- less material waste
- fewer nozzle plugs
- less overall system maintenance
- longer fluid seal life
- less production line downtime
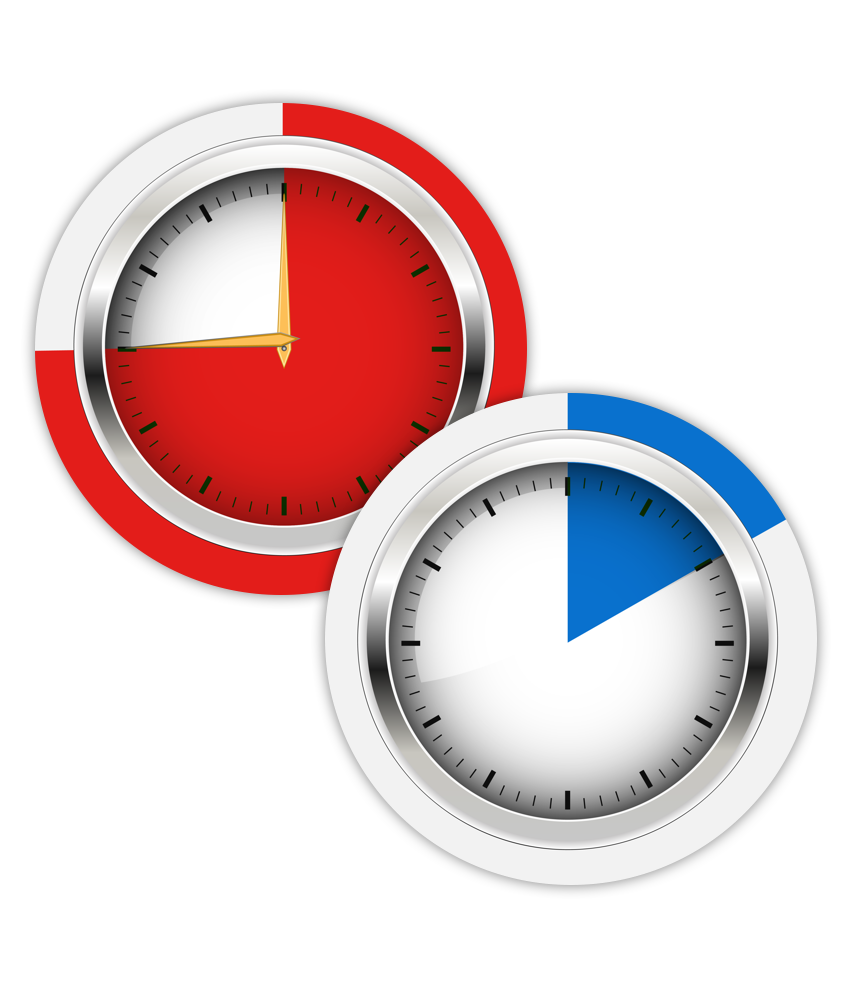
Expanding hot melt material options
Certain hot melt adhesive materials are usually not even considered due to their tendency to char with traditional heated-tank systems. To deal with the negative impacts of adhesive char formation, some manufacturers have switched to more expensive, temperature stable adhesives. While these adhesives may be a good option to consider, the increased cost often impacts profit margins. Ultimately, hot melt equipment should never dictate adhesive choices.
The newly designed melting chambers in the new Tank-Free systems have increased the viability of potential hot melt adhesive options, including metallocene, EVA and others. These adhesive options provide increased affordability and help manufacturers increase end-of-line packaging profitability.
Related articles
What causes hot melt adhesive char
Overheating, contamination and oxidation. Learn about the three causes of adhesive char and how to avoid them.
East Coast brewery improves beer packaging process
Two Roads Brewery was seeking a new hot melt system to improve efficiency and ensure carton quality.
Hot melt adhesive manufacturers
A list of manufacturers of hot melt adhesive for packaging applications - specifically, case and carton sealing.