Packaging quality control to increase reliability & profitability
Optimising the manufacturing process
For many industrial manufacturing applications, defining an efficient and effective manufacturing process is often the key factor to achieving profitability. Process engineers invest significant amounts of time and resources on testing and making refinements to arrive at an optimised process with improved quality.
Standardisation to achieve ISO compliance and maintaining a lean manufacturing approach is commonplace in the automotive industry - where once a process is defined, the thought of altering or changing it during production could be the equivalent of career suicide.
End-of-line packaging within ISO and lean manufacturing
The desire to achieve ISO 9000 or 9001 certifications ultimately drove many industries to define their manufacturing process and stick to it. These certifications do not focus on exactly what the process should be;; they are simply vehicles for documenting the process and then using that documentation for monitoring purposes to ensure manufacturers maintain the quality of the product.
When plants implement lean manufacturing methods, the focus is on eliminating waste to help improve efficiencies and reduce pricing - ultimately providing added value to their customers.
Due to too many variables that have been beyond their control, quality managers have given little focus to developing a lean or optimised end-of-line packaging process.
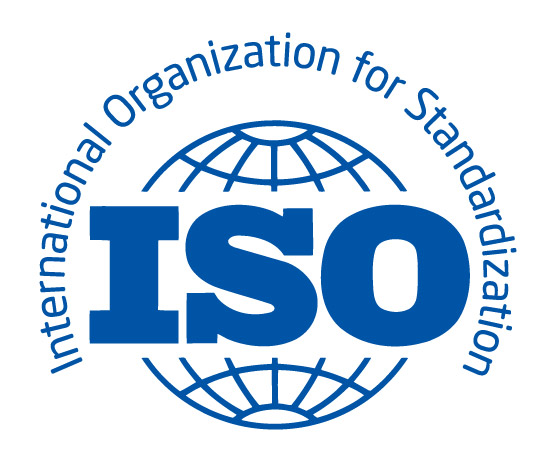
Antiquated technology and lean manufacturing
Lean manufacturing initiatives tend to not include end-of-line packaging applications largely because there is no way to optimise the process due to the limited system capabilities. Antiquated tank-based melting and gear-driven pump technology typically make it virtually impossible to standardise a process.
Since older hot melt systems melt adhesive with a heated tank, it is very difficult to maintain a consistent adhesive temperature. The glue near the outside of these tanks heats up quicker and will start to deteriorate as the glue near the center of the tank reaches operating temperature.
Using tank-based hot melt systems ultimately creates a constant adjustment battle.
It is commonly understood that line operators have to continuously adjust system settings to the achieve desired results. This inconsistency ultimately diminishes the ability to achieve overall process control. Being able to “set and forget” the hot melt system is impossible since the first shift operator’s settings are often different from those on the third shift.
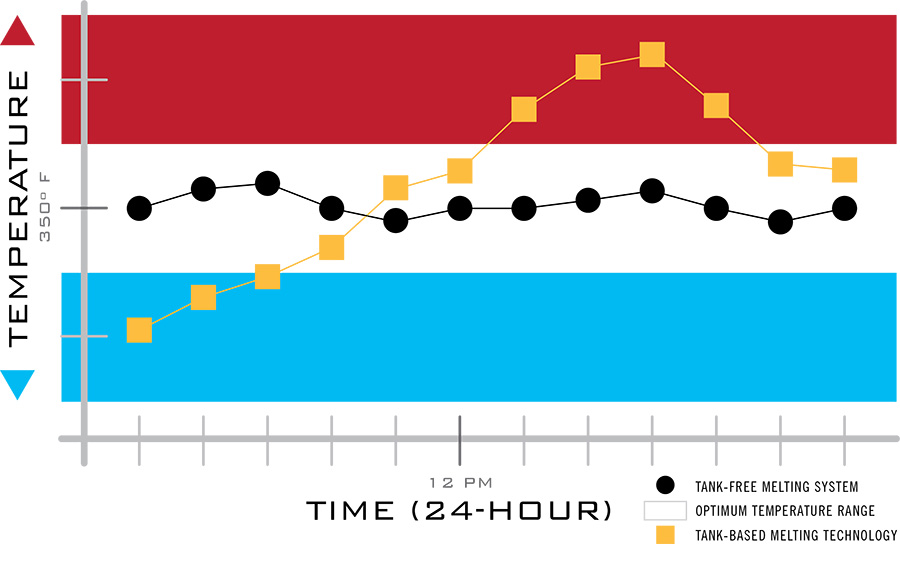
Some newer hot melt systems still use variations of this older approach to melting adhesive. For example, some systems use smaller reservoirs that include “fins” near the bottom of the “tank” in an effort to increase surface melting area. However, this is still a variation of a heated tank that does not maintain a consistent temperature with the adhesive in the system – especially if the adhesive sits for any period of time.
When evaluating hot melt systems, make sure to ask equipment suppliers these six important questions and have them demonstrate how the adhesive is melted – in detail.
Alternative adhesives help address material inconsistencies
In addition to hot melt system technology, a better understanding of hot melt adhesive materials can provide insight to help engineers achieve an optimised end-of-line packaging process. Hot melt adhesive has four components:
1) Base compounds: the backbone or core of the adhesive imparting properties like mechanical strength, flexibility and end use properties such as: heat, cold and chemical resistance. In most cases, base adhesive will not be used alone.
2) Tackifiers: they impart hot tack or the relative stickiness of the adhesive. The tackifier used depends on the specific adhesion properties required for a particular substrate and typically determines the colour and characteristic odour of a particular hot melt adhesive.
3) Dilutants: waxes or oils that modify the adhesive’s viscosity and setting speed – also known as the ‘set time’.
4) Stabilisers: added in recent years to provide viscosity stability and help overcome charring of adhesive sitting in heated tanks over long periods of time.
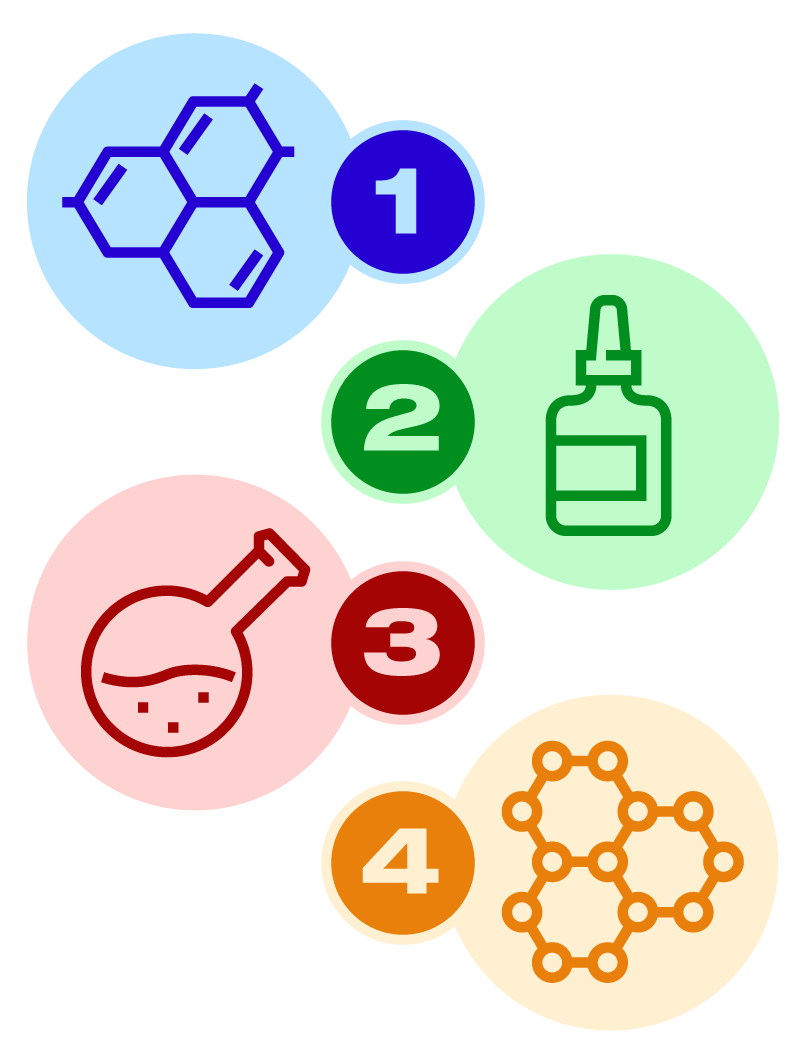
Quality Control & performance
A standardised process means that all of these components are closely controlled during the melting, transfer, and dispense applications. The end goal is to match the hot melt adhesive’s properties to the performance requirements.
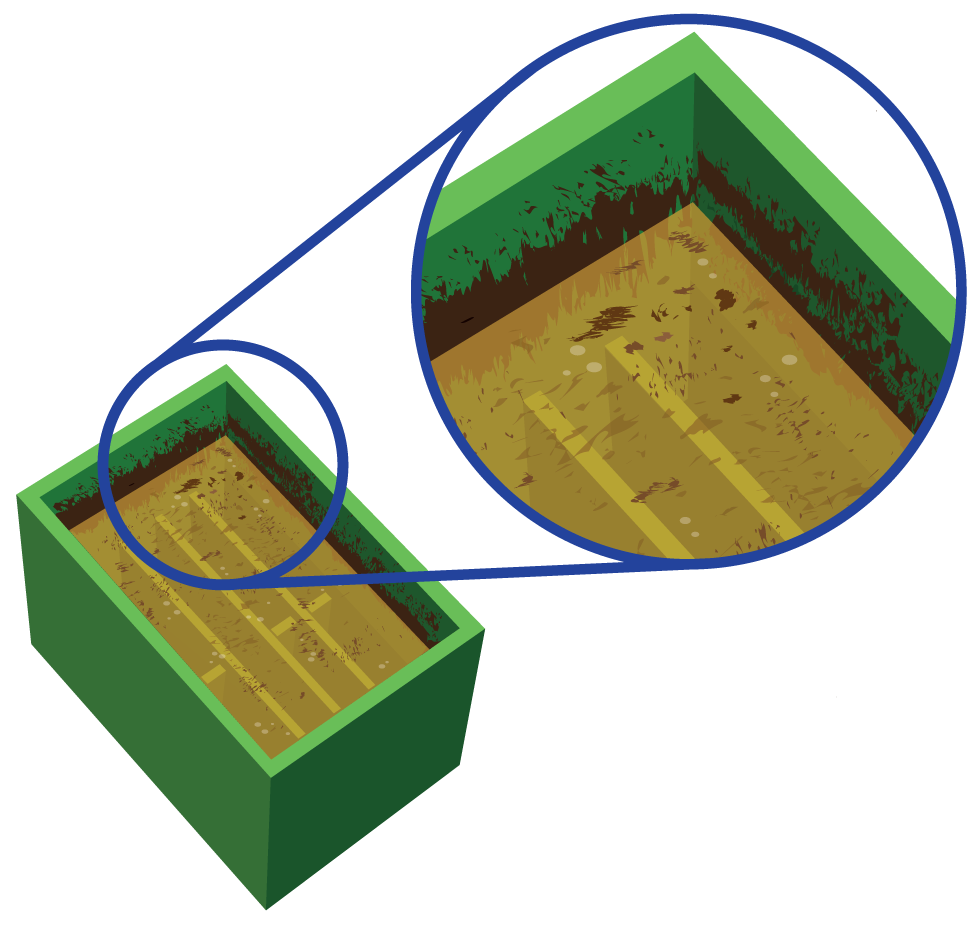
With the typical tank-based hot melt technology, glue consistency is constantly in flux. This situation has just been accepted as part of end-of-line packaging applications along with the glue degradation and dealing with adhesive char within the hot melt system.
To help address adhesive charring and consistency issues, manufacturers turned to material suppliers to develop alternative hot melt adhesives such as metallocenes. The alternative metallocene adhesives tend to clog less, have better temperature stability, and work over wider temperature range. However, these adhesive options are more costly for manufacturers - ultimately minimising profitability.
Quality through improved technology
Hot melt adhesive systems that utilise newer adhesive melting chambers (no heated tanks or reservoirs with fins) are truly Tank-FreeTM systems. Since they melt adhesive on a first-in and first-out basis, these systems are able to maintain a consistent adhesive temperature.
With this approach to melting adhesive, waxes do not evaporate and the adhesive does not deteriorate. Since the properties of the adhesive are maintained, there is no reason for an operator to change any settings after the process has been optimised. Hot melt system reliability is achieved and the same amount of adhesive is applied every time.
With greater control and the ability to monitor the hot melt adhesive dispense, those responsible for end-of-line packaging applications are now able to realise an optimised process and deliver the highest efficiencies possible.
By standardising end-of-line packaging and case and carton sealing processes, manufacturers are finally able to achieve a controlled process, implement lean manufacturing methods and ultimately achieve profitability goals.
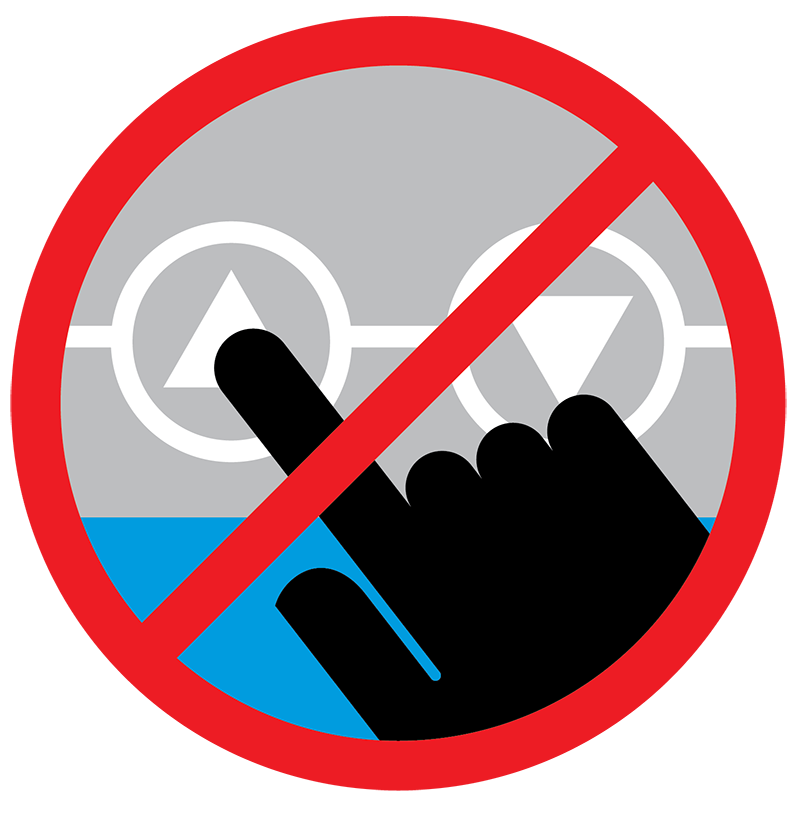
Depending on the application, operators using true Tank-FreeTM hot melt systems can go over a year or more without changing settings or even touching the system.
Related articles
Choosing a hot melt nozzle
The choice of hot melt nozzle impacts the performance of your end-of-line packaging operations.
Comparing the operation of hot melt systems
Comparing how different hot melt systems are designed to dispense material.
Create a safer hot melt environment
Here are four steps you can take to improve the hot melt safety at your facility.