Case Study: Li-ion Battery Manufacturing
Foam Encapsulation Solution Fast-tracks New EV Battery Production
An EV battery manufacturer had to determine the best foam encapsulation process for a new cell module design. Quick collaboration with Graco put it into production by a critical deadline.
A li-ion battery manufacturer optimises its foam encapsulation process
A li-ion battery manufacturer needed a cell potting solution to meet industry requirements to prevent thermal runaway and thermal propagation for its cylindrical cell battery module design. The manufacturer was facing challenges in determining the appropriate injection points, dispensing parameters, and impact of complex fluid dynamics. Design challenges aside, the manufacturer was facing a critical launch date and needed a production-ready process developed so that they could plan their production line.
Process challenges
Each cylindrical cell module design has unique features and requirements that can impact flow rates and dispense injection points to dispense the correct amount of material into the module evenly. With this design, the process challenges were:
- The battery design could not change at this late stage
- Dispensing had to be done from the top of the battery module with some possible flexibility to inject from the side of the module.
- The battery cells were closely packed and had a minimal distance between each other, which caused additional flow restriction.
- Access for the foam to flow into the battery module from the top with very tight restrictions.
- The process time was critical for the customer’s operation.
Our collaborative process
Our team of application engineers worked directly with the battery manufacturer’s design team and the material supplier to develop a process solution to meet operational efficiency, product quality, and repeatable material application requirements. Through our development lab, our team of application experts and our partnership with the material supplier, we conducted trials to determine the optimal application method which defined flow rates and application techniques and dispense points for the final production process.
Material testing – A thorough ratio and repeatability study was conducted to define optimal foam and equipment requirements.
Equipment specification – From previous trials on similar applications and our material evaluation, we specified the ideal combination of equipment based on the target application.
Application testing – Using prototype models and modules supplied by the battery manufacturer, we assessed and validated the proposed process specification.
RESULT
- Quality foam & fill: The Voltex dynamic mix valve and the EFR metre mix dispense system provided thoroughly mixed foam, even distribution throughout the module, and the shot repeatability required for their production process.
- Optimised dispense: Based on the lab tests, we determined proper mixing parameters, flow rates, and dispense injection points to dispense an accurate amount of material into the module evenly.
- Reduced processing time: Through modelling and dispense trials, we optimised the motion pattern to further reduce the processing time.
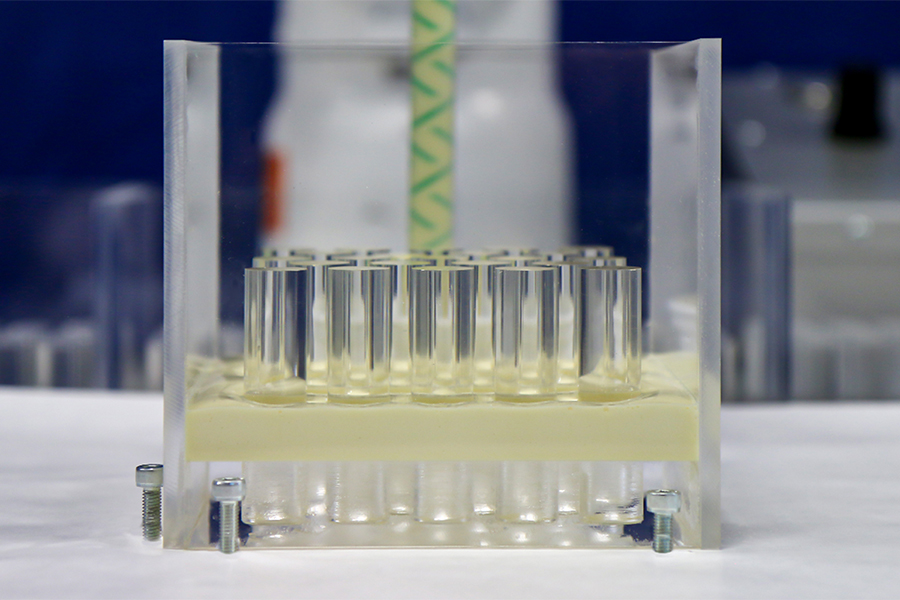
- Quality foam and fill: The Voltex Dynamic Mix Valve and Electric Fixed Ratio (EFR) Metering System provide thoroughly mixed form, even distribution throughout the module, and shot repeatability.
- Optimized dispense: With the proper mixing parameters, flow rates, and dispense injection points, an accurate amount of material is evenly dispensed into each module.
- Rapid process time: The modeling and dispense trials helped optimized the motion pattern to reduce the required processing time.
Collaborate with Us
Innovation truly comes through collaboration with Graco expertise and material supplier partnerships. We strive to deliver custom solutions backed by our global support network.
Contact our team for help with your application.
Related Articles
Foam Encapsulation of Cylindrical Battery Cells
Learn about foam encapsulation and its role in the manufacturing of high-performance battery modules that remain safe under all failure conditions.
Electric vehicle thermal management
Whether it’s assembling electric vehicle (EV) batteries, and electronic products, or miniaturizing printed circuit boards (PCBs), thermal management remains crucial to longevity, efficiency and safety.
Battery Pack sealing - EV battery
A quality seal is critical for the performance and longevity of EV batteries and for protecting integral components from water intrusion and other harsh environmental conditions.