Graco: Highly active globally in the marine sector
Graco provides a wide range of products and services to the marine industry worldwide. Here are five examples of Graco products that are providing value for some of Graco’s marine customers.
Case study #1
Surface preparation on chemical tankers
A Graco distributor in the UK was contacted by a shipowner with a fleet of 40 ships transporting chemicals around the world. For various on-board spot repair jobs, the company had been using hand tools and dry blasting, but with low success rates.
It’s no surprise, as both methods suffer from major drawbacks. Using hand tools such as scrapers, chipping hammers, or chisels to remove loose, non-adherent paint, rust or scale is the slowest and usually the least satisfactory method of surface preparation. Wire brushing can actually make the surface worse by polishing rather than cleaning the rusted surface.
Dry abrasive blasting is a commonly used method of surface preparation but has inherent problems. Flying abrasive particles and drifting dust may damage equipment, clog filters and create possible environmental problems. It is also possible to trap contaminants on the surface of the substrate being cleaned.
The UK Graco distributor presented the Graco EcoQuip vapour abrasive blasting equipment. It involves adding water simultaneously with the abrasive media in a pressure pot. The abrasive becomes suspended in water, and the mixture is then projected at high velocity by a forceful flow of compressed air. By encapsulating each blast particle with water, extra weight is added to the media which enlarges the impact of the blast media on the substrate. In addition, the removal and feathering of the material goes smoother and less media is used. The water reduces splash back and traps the dust being produced.
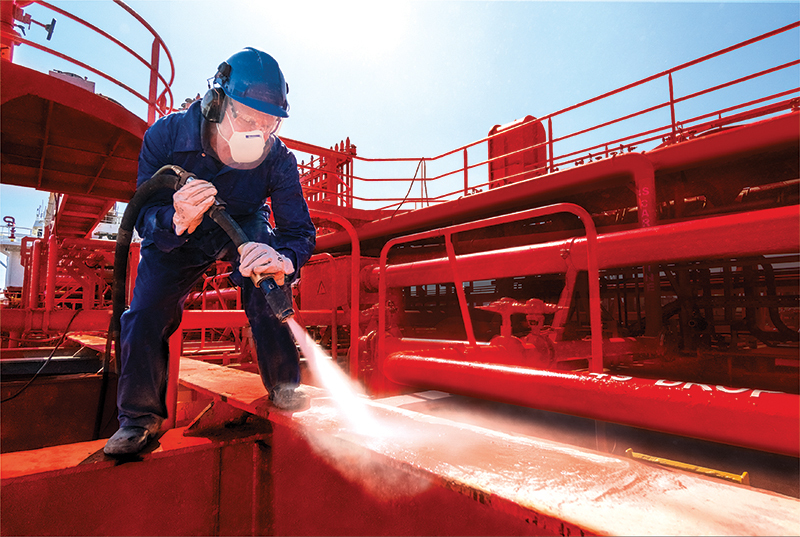
The shipowner was immediately interested but wanted to see EcoQuip in action first. A demonstration was therefore arranged on board one of their ships in Scandinavia. A test was carried out on rusted sections of the deck and on a number of painted valves and similar items. The highly portable EcoQuip 2 EQp was used with a 1" hose and standard nozzle, with Olivine GL70 abrasive, which is a very fine naturally occurring magnesium iron silicate. The machine was operated in its eco-mode.
The deck, valves and other items were blasted perfectly. The customer was most impressed by the excellent results achieved within a short timeframe, the small volume of water needed, the low amount of dust created, and the ease of use and portability of EcoQuip 2 EQp. In fact, when compared to dry abrasive blasting, EcoQuip 2 provides an equivalent performance but with up to 92% less dust, thus minimizing the need for PPE, tenting and containment, and decreasing environmental impact. A final feature of the EcoQuip 2 EQp that swayed the company to order a unit is that EcoQuip is fully ATEX approved for use in dangerous environments.
Case study #2:
Removing rust on cruise liners
Graco was contacted by a globally operating cruise company that was facing a major headache. Rust was appearing on all the hermetic doors in one of their 4500-passenger cruise liners. The problem was compounded because it was discovered in the middle of the cruise season and it was impossible to dock the ship to conduct the necessary maintenance. A solution therefore had to be found to remove the rust during sailing time without any risk or inconvenience to passengers and crew. The cruise company was also looking for ATEX-approved equipment.
Graco presented its ATEX-approved EcoQuip vapour abrasive blasting equipment, which is Graco’s solution for optimal surface preparation for the marine industry. It involves adding water simultaneously with the abrasive media in a pressure pot. The abrasive becomes suspended in water, and the mixture is then projected at high velocity by a forceful flow of compressed air. By encapsulating each blast particle with water, extra weight is added to the media which enlarges the impact of the blast media on the substrate. In addition, the removal and feathering of the material goes smoother and less media is used. The water reduces splash back and traps the dust being produced.
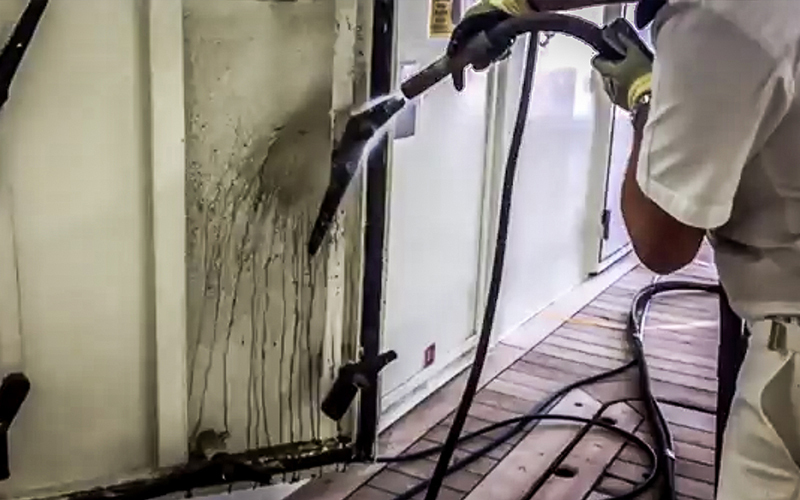
EcoQuip 2 is Graco’s latest vapour abrasive blasting equipment. It provides a performance equivalent to dry abrasive blasting but with up to 92% less dust, thus minimizing the need for PPE, tenting and containment, and decreasing environmental impact. It uses up to 75% less blast media and far less water than wet blasting, and creates little run-off, thus there is no large slurry mess to clean-up and dispose. It’s effective in rain and high humidity, and efficiently removes coatings without damaging the sub-surface. The bottom line is that EcoQuip 2 reduces project costs while increasing the speed, efficiency and productivity of blasting.
A half-day demonstration of EcoQuip 2 was arranged on board the liner during a brief scheduled stopover in a UK port. One rusting hermetic door was blasted using the portable EcoQuip 2 EQp with a 1" hose and standard nozzle, and using Olivine GL70 magnesium iron silicate abrasive. The machine quickly and efficiently removed the rust using only a small amount of abrasive and water. What’s more, the work was completed with a minimum of dust and noise, and with no inconvenience to passengers or crew.
Given the success of the demonstration, the EcoQuip 2 solution was quickly internally approved by the company’s security committee. A unit was purchased and the job was completed satisfactorily on board while cruising/sailing.
Case study #3
Replacing ultra-high pressure water cleaning on oil tankers
A shipowner with a fleet of 30 oil tankers sailing the world’s oceans decided to look for an alternative to ultra-high pressure water jetting to clean the surfaces of its vessels. The main reasons for this decision were linked to the significant health and safety concerns associated with this technique. The very high pressures used can lead to serious injuries with life and limb threatening potential as the combination of irritant material and ultra-high pressure results in an extremely intensive inflammatory reaction. Extra-tough protective clothing is therefore necessary when working with this technique.
The shipowner approached Graco’s distributor in Dubai who immediately recommended the Graco EcoQuip vapour abrasive blasting equipment. Vapour abrasive blasting involves adding water simultaneously with the abrasive media in a pressure pot. The abrasive becomes suspended in water, and the mixture is then projected at high velocity by a forceful flow of compressed air. By encapsulating each blast particle with water, extra weight is added to the media which enlarges the impact of the blast media on the substrate. In addition, the removal and feathering of the material goes smoother and less media is used. The water reduces splash back and traps the dust being produced. A major advantage of vapour abrasive blasting is that it uses less water than ultra-high pressure water jetting or even traditional water-based wet blasting, while reducing dust compared to dry blasting.
The Graco distributor arranged a demonstration of the portable EcoQuip 2 EQp with a 1" hose and standard nozzle, using Olivine GL70 abrasive, which is a very fine naturally occurring magnesium iron silicate. A range of painted valves, rusty pipes, and a section of the deck was blasted.
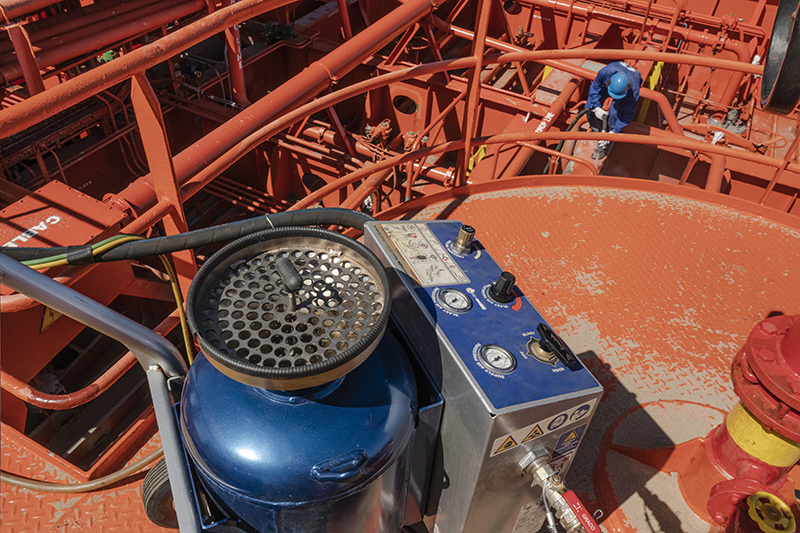
EcoQuip 2 rose to the occasion and performed superbly. The shipowner was impressed by the fact that it used up to 75% less blast media and far less water than UHP water jetting. Indeed, the shipowner admitted that UHP water jetting uses 12 times more water than vapour abrasive blasting, which is a major drawback in the Middle East. On top, the runoff of this waste water can also damage environmentally sensitive areas.
Discussions turned to lifecycle cost, and it was soon realized that the higher initial cost of UHP water jetting equipment, combined with higher maintenance costs and the higher running costs of the air compressor, mean that the advantage is significantly with vapour abrasive blasting, even when the cost of abrasive is taken into account. The bottom line is that vapour abrasive blasting with EcoQuip reduces project costs while increasing the speed, efficiency and productivity of blasting. And do not forget that all Graco EcoQuips are ATEX Zone 1 approved.
Finally, it was also pointed out that with EcoQuip, minimum PPE material is required: only masks, ear protectors and gloves. UHP water jetting requires special safety suits which cost a minimum of $3000 per person. Moreover, with EcoQuip, other tasks can be carried out safely outside a perimeter of five meters, whereas with UHP water jetting, other nearby tasks have to cease due to the very high pressures and safety issues.
Taking all these factors into consideration led to the shipowner deciding to purchase an EcoQuip unit to replace its UHP water cleaners.
Case study #4
Standardizing on AODD pumps on various vessels
A ship manager operating a range of vessels worldwide was looking for a single supplier for all the air-operated double-diaphragm (AODD) pumps on board his vessels. These pumps were used to evacuate the bilges of waste water and oil, and to transfer chemicals to and from the vessels. The chosen pump supplier would have to provide pumps in aluminum (1”, 2” and 3”), polypropylene for use with aggressive materials (½”, 1”, 2” and 3”), and stainless steel for use with water (1”, 2” and 3”).
However, it wasn’t a matter of just choosing the right pumps. The ship manager specified that the chosen pump supplier also had to guarantee rapid delivery of the appropriate pumps from stock. And he also had to guarantee the immediate supply of any necessary spare parts, anywhere in the world, to keep the pumps operating without having to change the whole unit.
After looking at the product range and service capabilities of a number of globally operating pump manufacturers, the company decided to work with Graco, and placed an order for a number of Graco AODD pumps belonging to the Husky range.
So what was it about Graco’s Husky pumps that swayed their decision?
For a start, Graco’s Husky pumps come in a full range from ¼” up to 3” in all materials for on-board applications. The pump itself consists of a simple design that works reliably and prevents stalling. It does not require air supply lubrication and is low in maintenance. Moreover, should a problem occur while at sea, the defect can invariably be repaired on the spot by the operator or maintenance technician, cost-effectively and quickly. In most cases, the problem is only the intake or discharge valve, which can be replaced on-site. Compare this with a defect piston in a piston pump, for example, which requires the entire pump unit to be replaced, which is often very difficult to do on board a vessel. Troubleshooting is also more difficult, since there are more wear parts that could be affected. Replacement can generally only be managed in a workshop. So the maintenance of an AODD pump is more cost-effective in terms of material, and is also less time-consuming.
Furthermore, piston pumps are likely to wear out much quicker than AODD pumps. The piston itself is a wear part, while the packing seals at the top and bottom of the piston must be replaced frequently. Depending on the degree of filling, sooner or later there will be wear and additional costs. The Husky AODD pump does not need packings; the diaphragm itself is the seal, thus reducing spare part costs.
The total cost of ownership of a Husky AODD pump is therefore significantly lower than that of competitive pumps. Not only does its inherent durability translate into a long lifetime of use (more than double the lifetime of most comparable pumps), but the repair kit of a AODD pump costs an average of one-third that of a competitive pump, and its takes only one-quarter of the time to repair.
So much for the Graco product range; what about the company’s service capabilities?
Here too, Graco came out with flying colors. The pumps – and any spare parts needed – are available all over the world through a network of more than 3300 distributors. Ultimately, the ship manager had no hesitation in standardizing on Graco’s Husky AODD pumps on board all his vessels.
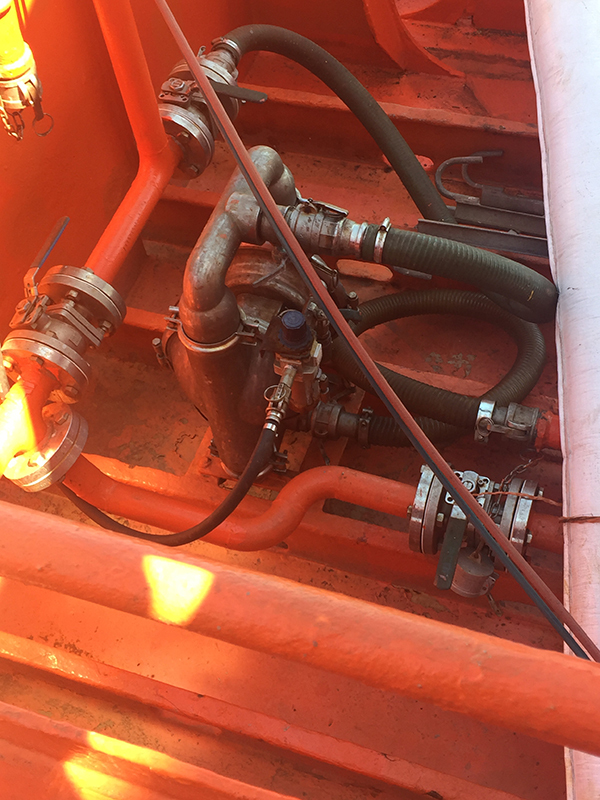
Case study #5
Cleaning oil tankers with ATEX-approved equipment
A shipowner with a fleet of tankers transporting oil and its derivatives, LNG and butane, was facing a specific maintenance challenge. The tanks, decks and bilges of the tanker fleet required special maintenance to be carried out regularly after each transport of oil, fuel and derivatives. Oil and fuel are recognized as particularly toxic and dangerous substances. Therefore, it is advisable to take far-reaching precautions regarding the cleaning of these vessels by using specific products and adapted methods. First of all, before starting any cleaning or maintenance operation, it is necessary to carry out degassing. Only then, other steps can be carried out such as mastering the pumping system, waste treatment, and cleaning high-pressure tanks.
A second challenge is that in the marine and oil & gas industries, cleaning and maintenance jobs take place in atmospheres that are potentially explosive. This means that any equipment used must be ATEX approved. ATEX is short for “Atmospheres Explosibles”. The ATEX Directive is a set of European Union regulations designed to ensure the safety of products being used in a potentially explosive atmosphere. An explosive atmosphere is defined as a mixture of flammable substances (gases, vapors, mists or dusts) with air, under atmospheric conditions capable of causing a hazardous explosion if ignited.
Considering the hazardous environment on board the tankers, the shipowner went in search of fully ATEX-approved high-pressure cleaning equipment. After researching various alternatives, he asked for a demonstration of the Graco Hydra-Clean high-pressure pneumatic cleaning system.
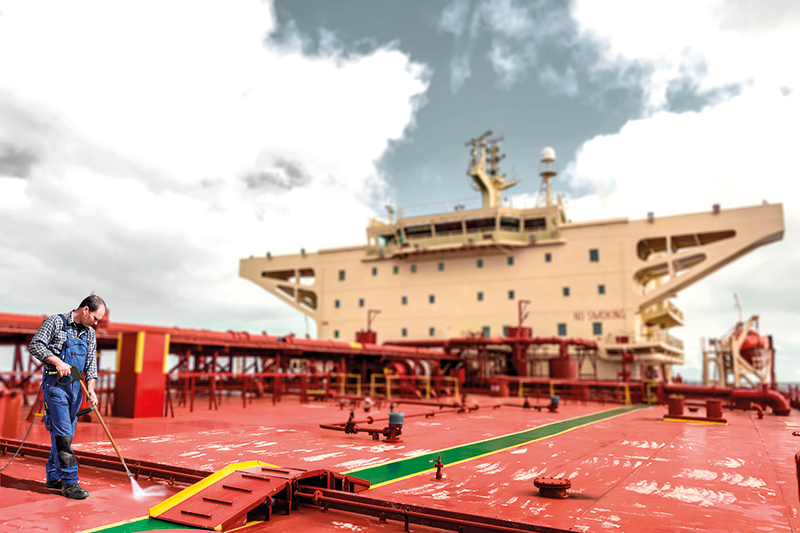
Hydra-Clean is a quick, easy and efficient method to clean decks, bilges and tanks contaminated with oil. It can be used by any vessel that has an air compressor. However, it is specifically focused on vessels with an ATEX zone, as Hydra-Clean is ATEX-approved. This means that it eliminates the risk from sparking, making it ideal for use in explosion sensitive environments, such as a ship’s hold if it is carrying chemicals, oil or other highly explosive materials.
Hydra-Clean provides a pressurized water jet from 70 to 300 bar. The most common Hydra-Clean model used for cleaning high-pressure tanks is the 30:1 cart-mounted unit. The cleaning chemical is injected into the washing water utilizing a dosage kit added to the washing water pump’s suction side, thus eliminating the need for a dosage pump.
The cleaning chemical is sprayed directly onto the tank bulkheads with a long lance, which the operator can direct all around the tank. The cleaning chemical is left on the tank walls for 20-40 minutes. The tank is then washed by hot water with the Hydra-Clean. The unit can handle hot water up to 85˚C without any problems. The process is repeated where necessary until the tank is clean.
Deck cleaning with Hydra-Clean is fast and efficient as two guns can be run off one unit and operated by two operators at the same time. Bilge and engine room cleaning is easy as Hydra-Clean is cart-mounted and is easy to maneuver anywhere on board.
The shipowner was extremely impressed with the performance of Hydra-Clean during the demonstration and has since equipped all his vessels with a unit.
Related Articles
On-board maintenance solutions for the maritime industry
Whether you’re a fleet owner or a ship chandler, keeping up-to-date with the latest developments in on-board maintenance is essential.
How to keep ATEX zones of ships clean
Louis De Hillerin, Manager Marine Division, explains more about Hydra-Clean, a quick, easy and efficient method to clean decks and surfaces, and remove barnacles and marine growth.
Graco strengthens its marine capabilities
It’s “all hands on deck” at Graco as the company further strengthens its position as a major global supplier of marine maintenance services. Louis de Hillerin, Manager Marine Division, explains more.