5 Spray technologies: what are the differences and advantages
Understanding the differences between the various spray technologies for paint automation.
There is a wide range of spray technologies and spraying systems for the automation of finishing processes. When selecting the appropriate technology, you should take into account the desired finish quality, transfer efficiency, speed of application, type of paint used and the type and shape of the object. To make the best choice, it helps to understand the advantages of and differences between the types of paint systems.
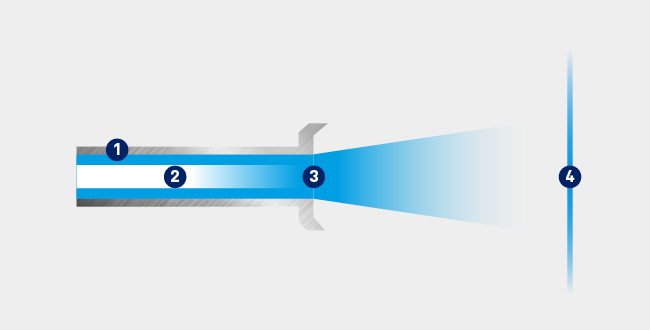
Air spray atomisation with high-velocity air
(1) Fluid tube (2) Compressed air (3) Fluid (4) Surface
Air Spraying
Air spray uses a low-pressure fluid stream that is mixed with compressed air at the air cap to atomise material in a controlled manner. It’s used for the application of low- to medium-viscosity fluids for products requiring a high-quality, class A or decorative finish. Due to changing requirements for environmental regulations, different versions of air spray technologies have been developed:
- Conventional is the traditional form of air spray technology and delivers the highest finish quality and production speeds. To achieve these advantages, a lot of air is utilised, resulting in low transfer efficiency.
- High Volume, Low Pressure (HVLP) was developed for EPA-regulated areas. To meet the regulation, the amount of air used is limited to 10 psi at the air cap. The result is a low-velocity pattern with good finish quality and higher transfer efficiency than conventional.
- Compliant technology is commonly referred to as Low Volume, Medium Pressure (LVMP) and was developed to meet European standards. Following the requirements, the air pressure cannot exceed 29 psi at the air inlet. This allows for an air cap design that delivers a high finish quality while achieving transfer efficiency that is equal to or better than HVLP.
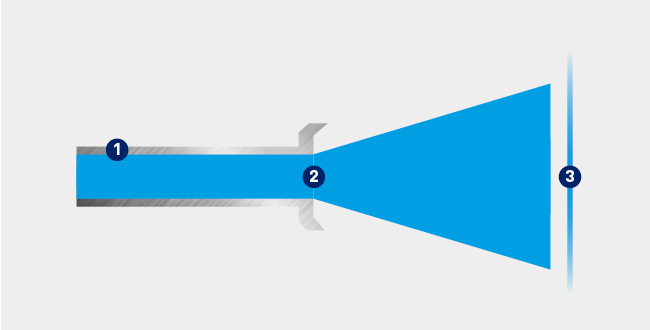
Airless atomization with fluid under pressure
(1) Fluid tube (2) Fluid (3) Surface
Airless spraying uses a high-pressure fluid supply for atomization without the use of compressed air, only fluid pressure. It’s used for medium to high viscosity fluids, delivers a lower finish quality and is ideal for speed and transfer efficiency.
Airless spray atomization is created by hydraulic force pushing material through an orifice. As the fluid exits the orifice, friction between the fluid stream and atmosphere disrupts the stream into small particles. The tip size and pressure is what determines the material flow rate. High pressure is used to create a complete pattern, therefore, the higher the material viscosity, the more pressure required.
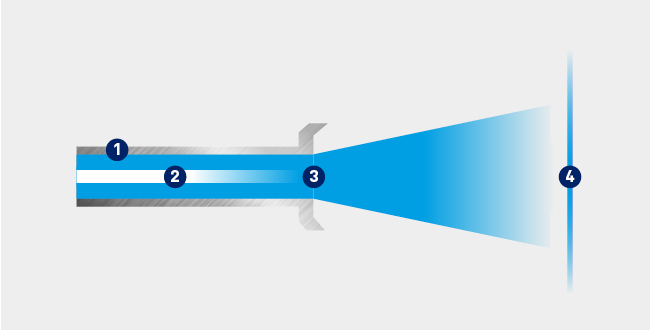
Air-assisted airless: where airless spraying and air spraying meet
(1) Fluid tube (2) Compressed air (3) Fluid (4) Surface
Electrostatic spraying
Electrostatic sprayers charge material particles as they pass or contact an electrode to achieve higher transfer efficiency. They rely on the attraction of opposite electrical charges. The material is electrostatically charged as it passes through an electrostatic field produced between the electrode on the front of the gun and a grounded object. The charged particles of the material are attracted to the grounded (neutral) object and form an even coating. The charged material will then wrap itself around the object, which will increase the surface space that is coated. Because of this wraparound effect, electrostatic sprayers are especially suitable for coating tubular products.
Air Spray electrostatic spraying uses a low-pressure fluid stream mixed with compressed air at the air cap to atomise material in a controlled manner. It is used for the application of low- to medium-viscosity fluids for products requiring a high-quality, class A or decorative finish.
Air-Assisted airless electrostatic spraying uses a high-pressure fluid supply for atomisation and compressed air at the cap for pattern control. Air-assisted airless electrostatic spraying solves many problems that arise with the use of high-viscosity and high-solids coatings and other issues associated with heating and using higher fluid pressures to aid in the atomisation of more viscous materials.
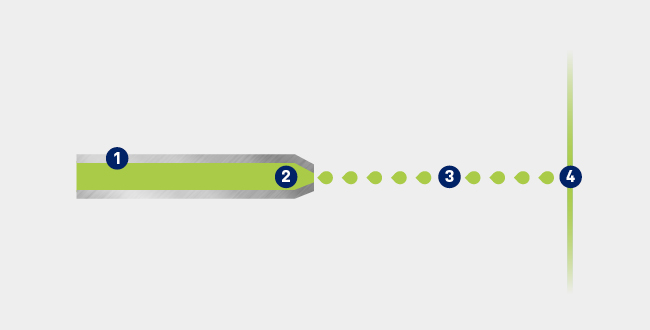
Electrostatic spraying: charged particles are attracted to the grounded object
(1) Fluid tube (2) High voltage DC to fluid (3) Charged fluid (4) Grounded surface
Rotary atomisation electrostatic spraying
Rotary atomisation electrostatic spraying, or centrifugal spraying, is another form of air spray. It uses an electrostatic charged bell cup that spins at a high rotation speed, so the paint is subjected to centrifugal force. The paint flows along the surface of the cup and when it reaches the edge, the high centrifugal forces break it apart into a fine cloud of fluid particles. The paint droplets carry the electrostatic charge from the bell cup and are directed or shaped by the shaping air coming out of the air cap. The charged droplet size is finer and more consistent than other atomisation methods, resulting in high transfer efficiency and finish quality.
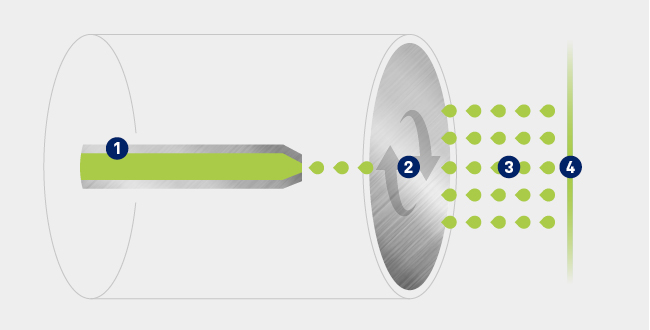
Rotary atomisation electrostatic spraying or centrifugal spraying
(1) Fluid tube (2) Spinning disk (3) Charged fluid (4) Grounded surface
Related Articles
Lift your spraying precision to another level with the ProBell Rotary Atomiser
Discover the many benefits of Graco’s ProBell Rotary Applicator series for automatic painting applications.
The differences between conventional and electrostatic paint spray guns
Comparing the strengths and weaknesses of conventional and electrostatic spray guns.
How to achieve the best results with electrostatic spray painting guns
5 simple steps to get the best finish quality and transfer efficiency with electrostatic sprayers.