ケーススタディ:リチウムイオンバッテリー製造
フォーム材封止ソリューションによってEV バッテリー製造の新工程が迅速化
このEV用バッテリーメーカーは、新しいセルモジュール設計に最適なフォーム材封止プロセスを検討していました。グラコとのスピーディな連携で、納期に遅れることなく生産を開始することができました。
セルポッティングソリューションが必要な新モジュール設計
ある電気自動車 (EV)用バッテリーメーカーは、新しい円筒形セルモジュールの設計期限に直面していました。製品ラインの計画にあたって、熱暴走や熱電導を防ぐための業界要件を満たす、セルポッティングソリューションが必要でした。
フォーム封止工程はすぐにでも生産可能な状態にもって行く必要がありました。しかし、設計チームと材料メーカーは、適切な量の材料をモジュールに均等に注入するための適切な注入ポイントとパラメーターを決定するのに苦労していた。
封止プロセスの課題
それぞれの円筒形セル・モジュールの設計には、モジュール内に適量の材料を均等に吐出するために、流量やディスペンス注入ポイントに影響を与えうる、独自の特徴や要件があります。
その円筒形セルバッテリーモジュールの設計は、すで量産向けに設定済みでした。納期に間に合わせるためには、EV バッテリーのフォーム封止プロセスの要件を満たすことが重要でした。
- 高品質なフォームと充填:バッテリーモジュール内には、難燃性の封止用フォーム材を充填できる空間はほとんどありませんでした。バッテリーセルは互いに密着して設置されており、さらに流れが制限されました。
- 最適な吐出:バッテリーモジュールの上部から吐出しなければならなかったのですが、モジュールの側面から注入することも可能でした。
- スピーディな処理:大規模なバッテリー製造工程には高い生産性が欠かせません。
各社との協業
メーカーのバッテリー設計チームと材料メーカーは、グラコのアプリケーション・エンジニアチームと直接協力し、作業効率、製品品質、再現性のある材料塗布の要件を満たすセルポッティング・ソリューションを開発しました グラコのアプリケーションラボではトライアルを行われました。
- 材料テスト:徹底的な比率と再現性の研究により、最適なフォームと機器要件が定義されました。
- 機器の仕様:この材料試験に加え、過去に同様の試験を行った経験が、このフォーム材封止に最適な機器を特定するのに役立ちました。
- アプリケーションテスト: 電池メーカーが提供したプロトタイプモデルとモジュールは、提案されたプロセス仕様の評価と検証に使用されました。
関係者間のこのような連携によって、量産に必要な流量、塗布技術、吐出ポイントを決定でき、発売期限に間に合わせることができたのです。
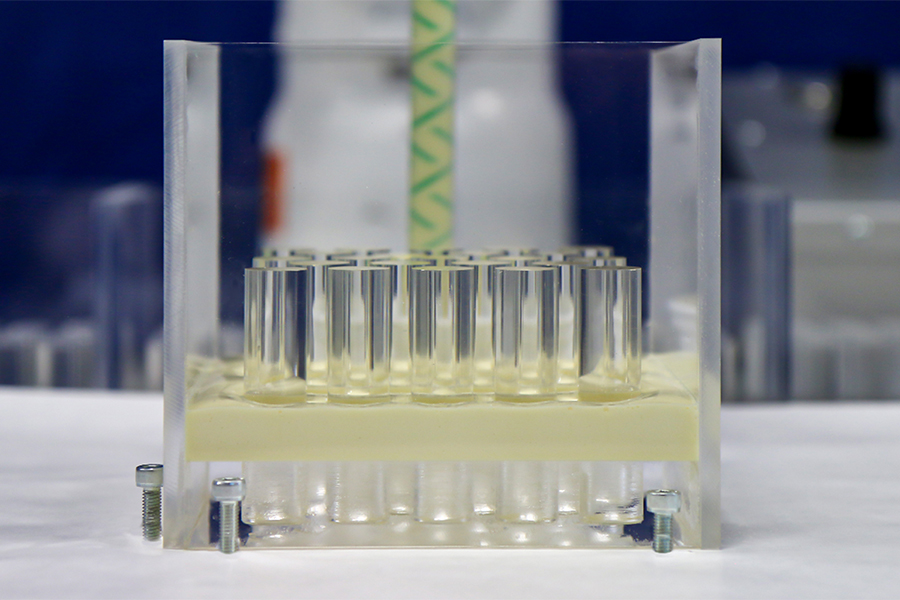
円筒形セルモジュールの新設計は、このバッテリーセル封止プロセスと合わせて量産工程に移行しました。
- 高品質なフォームと充填:Voltex ダイナミック混合バルブ と Electric Fixed Ratio (EFR) 計量システム が、フォーム材を十分に混合し、モジュール全体への均一な塗布、信頼性の高い精密なショットを実現します。
- ディスペンスの最適化:適切な混合パラメーター、流量、ディスペンス注入ポイントにより、正確な量の材料が各モジュールに均等にディスペンスされます。
- スピーディな処理:モデリングや吐出の試行は、移動パターンを最適化して必要な 処理時間の短縮に役立ちました。
グラコとのコラボレーション
グラコの持つ知見と材料メーカーの協力によってイノベーションがもたらされました。グラコはお客さまに対し、グローバルなサポート網に支えられたカスタムソリューションの提供に努めています。
必要なときはいつでもご連絡ください。