Keeping Komatsu dump trucks up and running
The Graco Mining Kit was installed on 14 Komatsu dump trucks to provide efficient automatic lubrication in tough conditions.
On a mining site in Uzbekistan, 14 Komatsu HD465-7 rigid dump trucks work 24/7 in an extremely tough environment. A lubrication system is essential to keep the trucks up and running. These trucks were therefore factory-fitted with a competitive automatic lubrication system.
However, the system presented some major problems for the Uzbek mining site. The grease reservoir on each truck was so small that it had to be filled every day. As there was only one pneumatic grease pump on the site, the drivers had to queue up to fill their truck’s grease reservoir from the grease drum, thereby wasting precious time. Moreover, it was difficult to see when the reservoir was full as the level was not clearly indicated. This meant that the reservoir would frequently be over-filled, which was a waste of grease. The reservoir level needed to be indicated somehow, for example with a tape. Another problem was that the check valve in the pump element (the plunger) was made of a very fragile material and was often wearing out or failing.
If that wasn’t bad enough, the grease pump on the trucks were not sufficiently powerful to get grease to the most distant lubrication points. These points then had to be lubricated manually, which was again additional downtime – especially as these lubrication points were extremely difficult to access. It was also discovered that the grease zerks on the metering devices were uncapped and easily contaminated with dust and dirt. Finally, the system’s controller was located behind the driver in his cabin. Drivers found they could not easily see the status of the system or any error messages.
A temporary solution involved installing a number of hand pumps on site to speed up the refilling time. However, the drivers still needed to refill every day – the basic problem was that the grease reservoir on the truck was small. Ideally, the reservoir should have been large enough to provide for multiple days of lubrication without refilling.

The Graco solution
After discussing these continuing problems with the local Graco distributor, each of the 14 Komatsu HD465-7 rigid dump trucks were fitted with the Graco Mining Kit. Included in the kit is the Graco Compact Dyna-Star pump (incorporating a much larger 12-liter reservoir) with Auto-Fill Shut-Off (AFSO), pressure and level sensors; a Remote-Fill Manifold for fast refilling of the grease reservoir; GL-1 X injectors with extended warranty; and the GLC-X Controller with Bluetooth and data log.
The work was carried out by Danila Samosyuk, Business Development Specialist at Graco, along with two technicians from the local Graco distributor. “It took the three of us around ten hours per truck to remove the old system and install the new Graco automatic lubrication system,” Danila recalls.
The level and pressure sensors of the Compact Dyna-Star pump provide the exact level of grease inside the reservoir, making it easy to see when it needs to be refilled. Thanks to its AFSO feature, as soon as the tank is full, the indicating pin pops up and the filling port automatically closes. The controller indicates that the reservoir is now full.
The Remote-Fill Manifold is located at ground level, which makes the refilling process quick, safe and simple. The driver just connects it to the pump. From the manifold, hoses travel to the injectors and then onwards to each of the lube points on the truck.
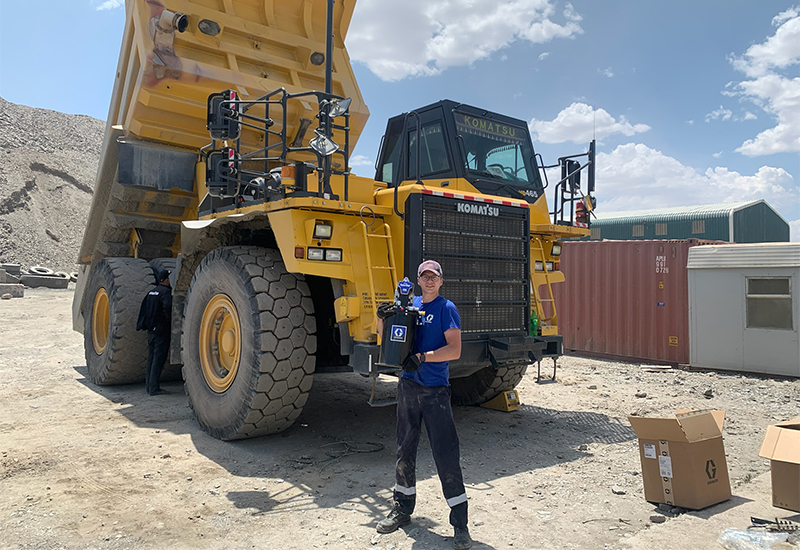
With their rugged, single-piece design, GL-1 X injectors are designed for years of reliable operation in the harshest operating environments. They include an adjustable hex head nut to make adjusting the output simple. The absence of vent holes, combined with fully enclosed press fittings, efficiently prevent any lubricant leaking out. A convenient top-mounted cycle pin indicator enables quick confirmation that the injector is functioning properly. Transparent dust caps keep off the dust while making it easy to see the levels.
The GL-1 X injectors are located all around the truck. Each truck has 35 injectors to service 9 grease points on the left-side of the truck, 8 grease points on the right-side, and 18 grease points at the rear of the truck. “The injectors were installed on standard plates which were slightly modified to make them larger and stronger,” adds Danila, “although no welding work was necessary.
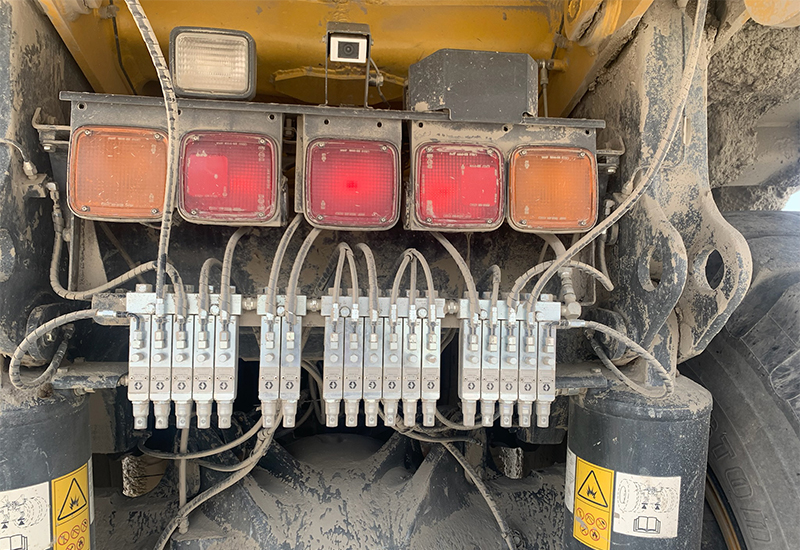
The GLC-X Controller is located on the side of the driver’s cabin in full view. Thanks to its easy-to-read LED screen, the driver can clearly see text codes, faults and other data in any ambient light. The Controller enables real-time system reporting of lubrication intervals, pressure limits, lubricant levels and more. It connects via Bluetooth to the Auto Lube™ app, enabling remote monitoring of lubrication levels, configuration of settings, and the sharing of history and important diagnostics.
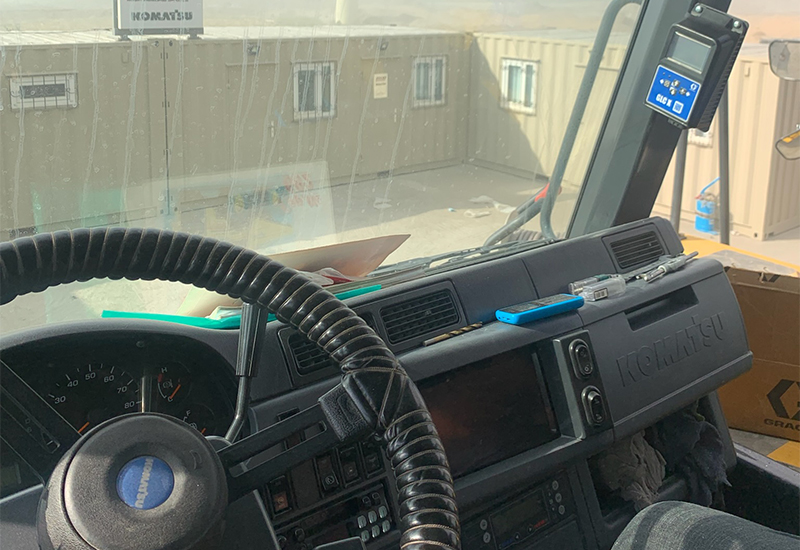
Huge reduction in downtime
“The customer was delighted as the new Graco automatic lubrication system gives 10-12 days of continuous duty,” says Danila. “The system immediately reduced the downtime of the previous system, gaining at least an hour more availability per truck per day. With 14 trucks in the fleet, this is almost like having another truck available for work.” When multiplied across all 14 trucks, it adds up to over 5,000 productive hours gained through the course of one year, and the accompanying cost savings and productivity improvements.
More information
If you are interested in learning more about the Graco Mining Kit, fill out the contact form below.
Related Articles
How to choose the right Off-Road Auto Lube System
Each type of heavy equipment has different component specifications that are required to make up an auto lube system that will properly supply the correct amounts of lubricant to each lube point at the correct time intervals. Learn about these specifications and components...
Recognising Clogged Grease Zerks
When maintenance personnel or the operator is tasked with lubricating equipment, it is possible that they may encounter grease zerks that refuse to accept lubricant. This article aims to help identify common causes of clogged grease zerks.
Lubrication Contamination and the Effect on Pin Bushings
When excessive contamination builds up between a pin and bushing surface, the rotation of the pin and the pressure load begins to dig contamination into the bronze bushing. Over time this contamination builds up and begins to restrict the movement of the pin by increasing friction.