WHY INVEST IN A SANITARY DRUM UNLOADING SYSTEM?
Drum unloading systems can help ease the transfer of highly viscous media.
Drum unloaders are an ideal solution for highly viscous, difficult-to-transfer materials. They can move tomato pastes, peanut butter, personal care products and cosmetics.
Today, many food and personal care processors have personnel who manually scoop the product from a drum. Others chain or clamp the drum, and raise it and dump the product into a kettle or hopper. They then spray the drum with water to remove the residue. These processes can be hazardous due to potential employee injury and food safety. Installing a drum unloading system can help prevent these issues.
Benefits
Drum unloaders save processors time and money. The typical evacuation time for a drum unloader is about five minutes. Comparable processes can often take more than 30 minutes. Also, when water is introduced to the material for product removal, it typically needs to be taken out later in the process, which takes more time and money and can introduce contaminants.
The drum unloader not only saves time in the actual evacuation process, but it also saves money in the amount of residual product in the drum. Processors will see a significant amount of residual product with drum scooping or dumping. A high performing drum unloader with an inflatable wiper seal will typically leave less than 1 percent residual product in the drum.
Common Pump Technologies
One of the most common pumps on a drum unloader is a sanitary air-operated double-diaphragm pump. A diaphragm pump unloading system can move materials up to 100,000 cps. Typical materials that a diaphragm pump unloader can handle are fruit juice concentrates, salad dressings, condiments and sauces. If the processor needs to remove materials from the drum of more than 100,000 cps, one way is with a sanitary piston pump drum unloader. Piston pumps are capable of higher pressures to move high viscosity materials longer distances.
Piston pumps come in ratios. For example a 12:1 piston pump gives an outlet fluid pressure 12 times the pressure of the inlet air, up to 1,200 psi. This outlet fluid pressure coupled with the down pressure of the drum unloader’s ram plate allows the processor to easily unload highly viscous materials—such as peanut butter and caramel.
Health and Safety
We all read about contamination problems in processing facilities. Think about the potential of contamination when personnel lean over drums and manually scoop product. Also, the drum is open and the product is exposed to airborne bacteria—something a drum unloading system would help prevent with a ram plate and inflatable wiper seal.
Personnel safety is also a concern. Imagine the potential of a clamped or chained 500 pound drum dropping to the plant floor as it moves up to be dumped into a hopper. Drum unloading systems eliminate this type of in-plant accident potential.
Recent Advancements
Huge advancements have occurred in drum unloader technology. First is the creation of the inflatable wiper seal on the ram plate. After the ram plate and seal enter the drum, the seal is inflated to the appropriate pressure. The seal holds this pressure and gently scrapes the side of the drum as the ram plate moves from top to bottom. This allows users to achieve greater than 99 percent evacuation rates. The inflatable seal prevents product “blowing by” the ram plate, which a flat seal cannot accomplish.
Major strides have also been made in improving the ability to clean the drum unloader. Processors need products that are easy to take apart, clean and re-assemble. Quick disconnect clamps can replace bolted designs. Easy-to-repair air valves can replace air valves with many parts and PTFE over-molded diaphragms can replace diaphragms with an exposed fluid-side diaphragm plate. These over-molded diaphragms eliminate the potential for bacteria to remain between the fluid-side diaphragm plate and the diaphragm. These all help minimize downtime for cleaning.
A huge challenge is the different sizes and shapes of drums (from conical to straight-sided) in food processing facilities, which has caused caution when considering a drum unloader purchase. However, some current unloaders have an inflatable wiper seal and can accommodate drums with internal diameters ranging from 19 inches (48.26 centimeters) to 24 inches (60.96 centimeters).
Return on Investment
Huge returns on investment can be achieved after the installation of drum unloading systems. For example, a facility that is manually scoops 10 drums each day for 300 days per year could have a new drum unloader paid for in less than one year via material and labor savings. With that rate of return, the drum unloader can be a smart and valuable investment.
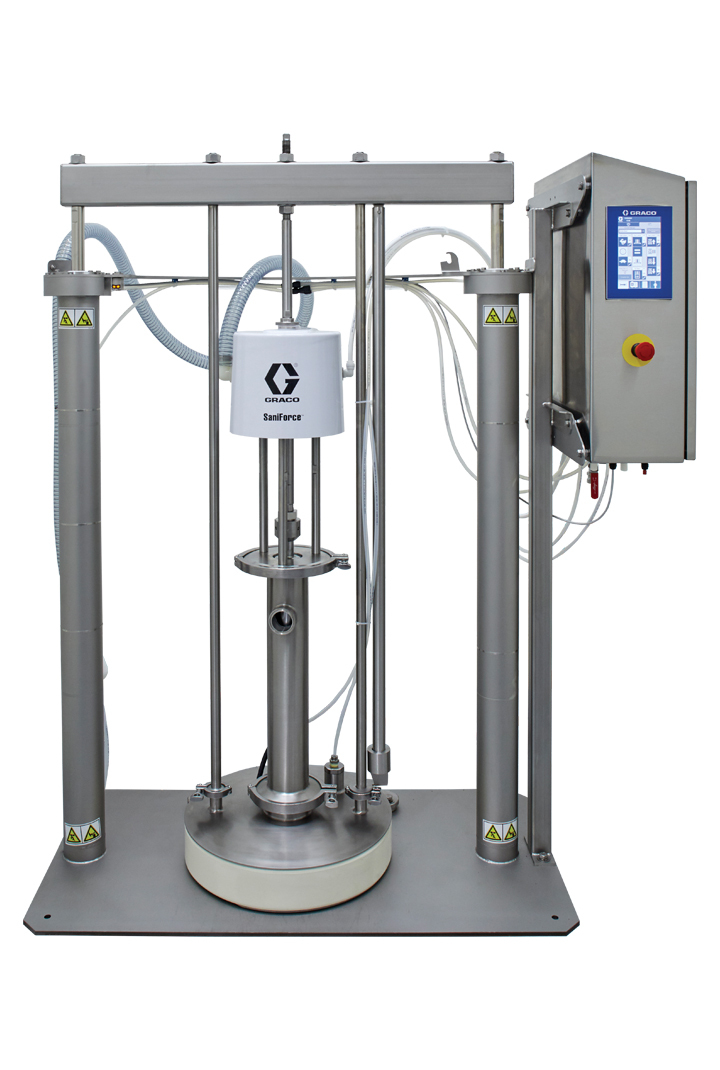
Related Articles
Efficient transfers of tomato paste and diced tomatoes
Established in 1915, the Greek canning company KYKNOS is one of the most loved and recognized brands in Greece. A family owned company, famous for its canned tomato products, KYKNOS selects and packs tomatoes, grown in the region of Peloponesse.
Unloading high viscosity food ingredients safely and effectively
There are several methods that are utilized for unloading high viscosity ingredients within the food manufacturing process. Arguably the most flexible, cleanest, and most ergonomically safe option would be the container unloading systems that address many of the concerns with the other methods emplo...
Céréco improves the unloading of its fillings
The specialist producer of co-extruded organic breakfast cereal ranges for children has changed to a larger drum packaging format for its fillings.