Optimally coating gearboxes for self-propelled machines
Graco’s ProMix Easy, ProMix 2KS proportioners, G40 and AirPro spray guns are proving their value at Bonfiglioli’s gearbox manufacturing plant in Forli, Italy.
One of the tasks performed by Pieffeci Spa, an industrial engineering company based in Turin, Italy is to optimize all stages of a coating process. To accomplish this goal, Pieffeci works closely with the coating departments of its clients. One such client is Bonfiglioli Spa. Its plant in Forli, Italy manufactures gearboxes for self-propelled machines (rotation of caterpillars and excavator turrets), electromobility devices, and wind turbines.
Bonfiglioli’s customers include the world’s leading players in the wind energy and earth-moving machinery sectors. With customers like these, the coating specifications are very stringent, so Pieffeci, together with Bonfiglioli, carries out all the laboratory tests needed to meet such specifications. Recently, the demands for high quality and performance have been increasing.
This is a challenge for Pieffeci, but also a spur to improve its work for Bonfiglioli. However, by setting a very restrictive tolerance limit for non-compliance and maintaining tight control of the coating parameters, the painting results have reached the level required. Also important is to use the appropriate equipment for dosing, mixing and spraying – and for this, Pieffeci turned to Graco and its distributor AS Divisione Verniciatura of Bologna.
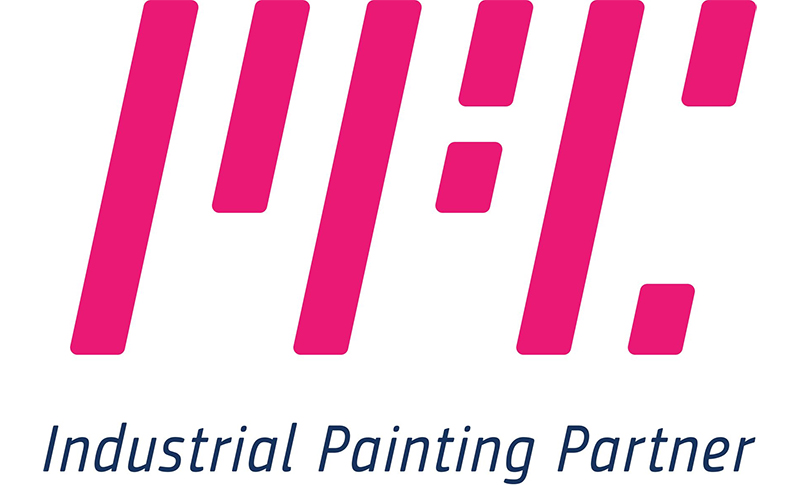
Step-by-step monitoring of the coating process
The coating of gearboxes is complex because of the weight and shape of the parts, and also the difficulty of evenly protecting their surfaces, which are exposed to extreme wear and corrosion. Once the material to be handled reaches the coating department, a barcode is assigned to each product so that every step can be monitored. To reduce the number of color change operations, the components are grouped according to the shade to be applied.
Robotic spray paint booths
The coating system includes four spray paint booths separated by a flash-off tunnel. The thicknesses required for coatings of gearbox components range from 40 to 400 microns in one to four coats; only one system, however, requires the application of a single coat, that of a 40-micron shop primer used if the client is to finish the part.
Normally, the first two booths apply the basecoat and the last two the topcoat. However, in the event of any production peaks, the third booth can apply both basecoat and topcoat. The coating robots are installed in the first three booths, while in the fourth one the operator applies the paint manually, in case of small lots or prototypes or for a touch-up if the result of the visual control on a component has not been positive.
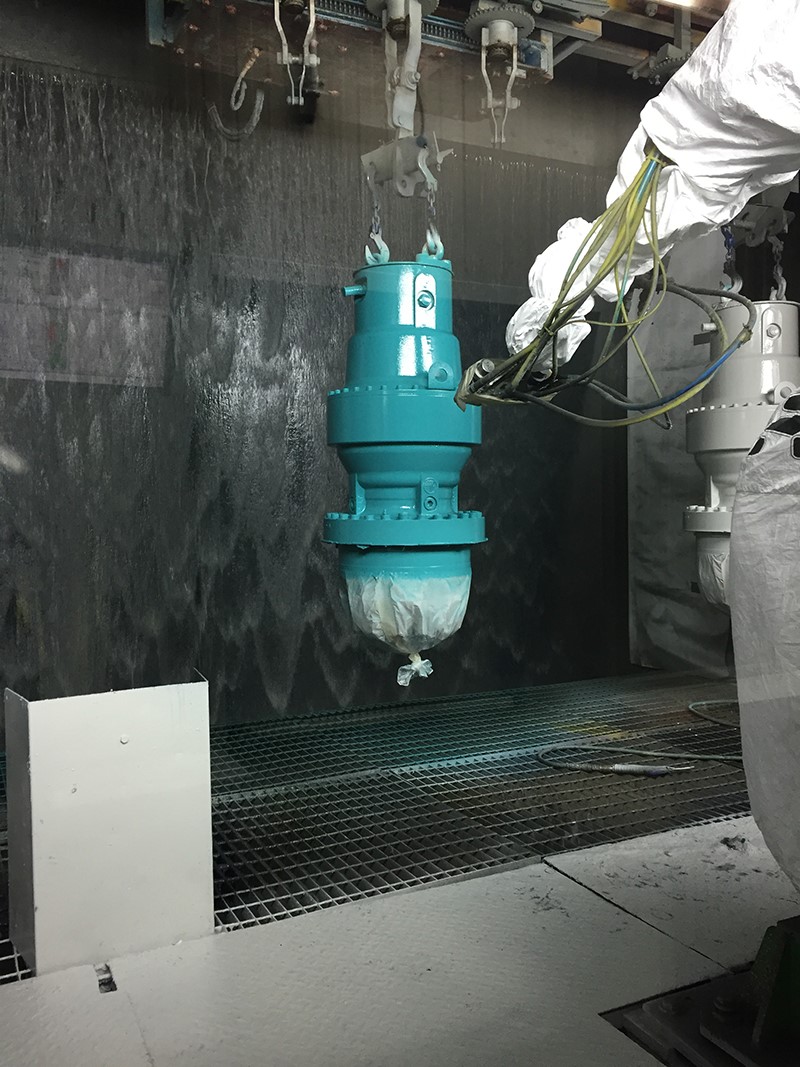
Graco’s dosing systems
Bonfiglioli’s paintshop is equipped with Graco dosing systems provided by AS Divisione Verniciatura. Recently, the ProMix Auto dosing system in the first booth, which had been used successfully for over ten years, was replaced with a ProMix 2KS. This newer, more powerful system ensured greater reliability in terms of both quality and capacity.
Together with the staff of Pieffeci and the management of Bonfiglioli, AS conducted a detailed assessment of the paintshop to discover ways to increase efficiency and productivity. Following this analysis, it was decided to place the mixer inside the booths, unlike the previous arrangement. This reduced the length of the pipes and the amount of catalyzed product circulating, as well as improving the use of space.
The primer’s dosage is managed by two ProMix Easy systems (the previous 2K generation). One is devoted to the standard light grey basecoat and the other to the yellow and black primers required by some specifications to ensure that the surface is protected and the color remains the same as the rest of the component even if the topcoat is scratched.
The ProMix Easy dosing systems were installed with a manual handling process in mind. However, a PLC able to manage the two ProMix Easy devices was added: in this way, the two machines have been turned into semi-automatic systems able to interact, in a limited manner, with the coating robots.
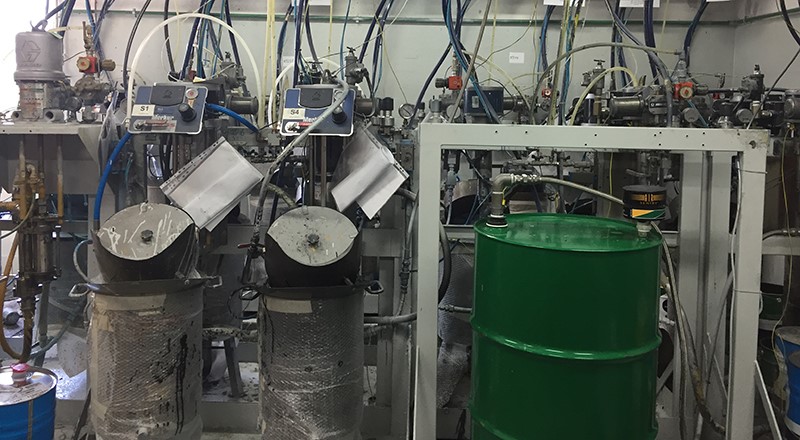
The benefits of an automated application process
The Bonfiglioli catalogue covers a range of 60 topcoats, although only 17 are frequently used. These are kept in the coating management room, in tanks equipped with a stirrer and a pump that are managed by the ProMix 2KS dosing system, which also manages catalyst levels.
A pump handles the rest of the color range by directly drawing the products from the paint drums. Checks are performed on the viscosity of the paints, and on the temperature and humidity of the heated chamber of the coating management room. Pieffeci has also changed how the product volumes are managed by switching, where possible, from 30 kg to 200 kg drums and installing a few drum lifters, which have facilitated the work of the staff involved and increased safety at the plant.
As for the application phase, Graco’s G40 automatic air-assisted spray gun is used. This lightweight gun offers a superior finish quality with tight pattern widths and excellent position accuracy. The robots have two guns each; one for the one-component and the other for the two-component product, with a usage rate of 50% each. This choice was motivated by the need to avoid continuous cleaning and loading operations of the guns. It means that there are always two devices that are loaded and ready for use.
The greatest advantages achieved through automating the process were the saving in paint and the reduction in the color change times. The waste of paint was halved, while the time needed for the color change operation was cut from 75 to 43 seconds. Considering the high number of daily changes (about 40), the resulting time and cost benefits are unquestionable.
Protection of the gearboxes
The drying oven installed after the coating plant polymerizes the gearboxes’ surfaces for about one hour and a half. The following tunnel cools the workpieces before unloading, so that they can be immediately handled for packaging. The paint is checked that it has cooled down to below 40°C, so that the gearbox can be positioned on the base of the box in which it will be shipped.
Before the unloading station, there is an unmasking station to remove the films and tapes that protect the flanges during treatment and an automatic station equipped with a robot for the application of a rustproof oil, which prevents the flanges from oxidizing. Graco was also consulted for the automation of the protective oil application station.
The initial intention was to apply two different oils with two guns located on the robot’s wrist. Due to weight problems however, only one gun was installed – the Graco AirPro. This allows the possibility to fine-tune the spray fan and thus be able to apply a minimum amount (about 10-20 cc/min) of well-sprayed product on small parts and a greater amount on the larger parts. The AirPro gun is frequently used in the automotive industry to treat limited surface areas where a high quality level is required. This very powerful gun was selected by Pieffeci because the various kinds of oil used have very different viscosities.
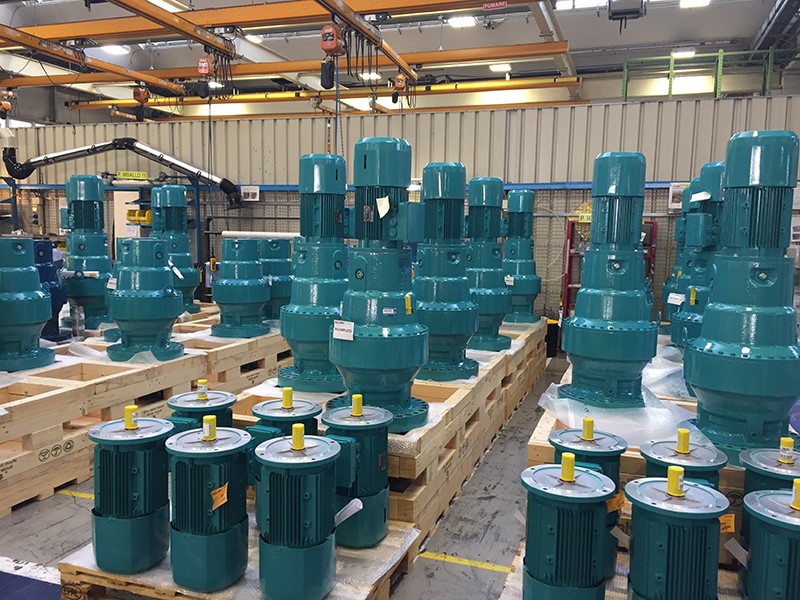
Conclusions
Pieffeci’s involvement at Bonfiglioli has certainly contributed to improving the efficiency and productivity of the gearbox coating process in Forli. It provides clear evidence that proper surface treatment can be an added value to the manufacturing industry, and that partners like Graco and AS Divisione Verniciatura are key to providing excellent dosing, mixing and spraying equipment for the relevant processes.
For more information on Graco’s ProMix Easy and ProMix 2KS proportioners, and G40 and AirPro spray guns, fill out the form below.
Related Articles
What is Paint Degradation?
Paint degradation affects manufacturers who use metallics for high quality surface finishes. As metallic paint circulates, it can get so damaged that it must be discarded.
Extreme material abrasiveness? Problem solved with Elite
Some thermal interface materials (TIMs) are so abrasive, it is like pumping diamond dust or liquid sandpaper. Explore why and how we developed Elite, the longest-lasting pump construction for abrasive material dispense.
Foam Encapsulation of Cylindrical Battery Cells
Learn about foam encapsulation and its role in the manufacturing of high-performance battery modules that remain safe under all failure conditions.