How to configure a diaphragm pump with confidence – Part 2
Cristiano Giancola, Technical Training Supervisor at Graco, selects two diaphragm pumps for two different applications.
Part 1 of this series of articles explained how Graco provides three easy-to-follow steps to help you select and configure a diaphragm pump:
- Step 1. Chemical compatibility guide
- Step 2. Materials of construction guide
- Step 3. Diaphragm pump selector
In Part 2 I am going to imagine that I have to select and configure a diaphragm pump for two very different pumping applications: seawater and tomato salsa dip. I will go through each of these three steps and give my reasons why I have chosen specific materials for each pump’s body and internal components.
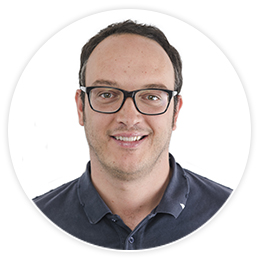
Step 1: Chemical Compatibility Guide
Use this tool as a general guideline for pump selection and to determine compatible materials.
Step 2: Materials of Construction Guide
This tool will allow you to find the most cost effective match for your application.
Step 3: Pump Selector Tool
Which pump works best for your application? Use this tool to configure your pump.
Application: Seawater
For my first example, I’m working on an oil rig! I need a diaphragm pump to evacuate seawater from a tank at a flow rate of 200 lpm with intermittent usage.
Going to the Chemical Compatibility Guide and adding seawater to the first column indicates that seawater is compatible with a range of metals, plastics and elastomers. I’m going to choose a metal body for my pump as it will be operating in a potentially explosive atmosphere so will need to be grounded and be ATEX approved.
Among the metals, Hastelloy® is indicated as Excellent (A) and aluminium as Good (B). Ideally, I would limit my selection to materials that give an A rating. However, as mentioned in Part 1, economics always plays a factor when choosing a pump. Hastelloy® is an outstanding material but it’s three times more expensive than aluminium. My budget won’t stretch that far! So I’m going to choose an aluminium body for my pump.
Now to the inner parts of the pump. A lot of plastics and elastomers are compatible with seawater: polypropylene, Geolast®, Viton®, PTFE, Buna-N … How do I make a choice between them? The answer is found by going to step 2 and the Materials Construction Guide to look more closely at each material.
Geolast® is a low-cost solution that’s very flexible, which suggests a long lifetime. It’s also mentioned as having good abrasion resistance which would be useful as the seawater will contain abrasive sand particles.
Viton®, PTFE and Buna-N also display good characteristics but are more expensive than Geolast® without seemingly offering any additional benefits. So I am going to select a combination of an aluminium pump with Geolast® internal parts.
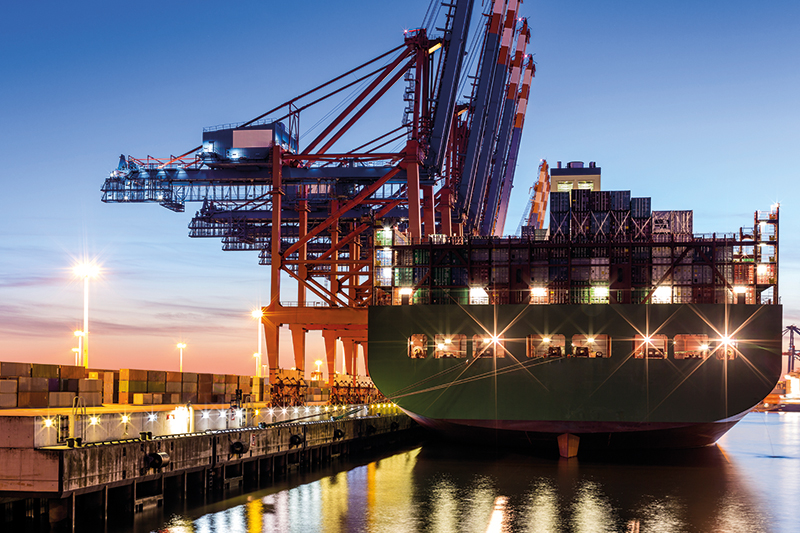
I then go to step 3 and start configuring my pump. I select the power source (air), the certificate (ATEX), and the body material (aluminium).
For the pump inlet size, for a flow rate of 200 lpm a 1-inch pump is indicated as sufficient as it offers 189 lpm. I could upgrade to a 1.5-inch pump to be on the safe side, as this provides a flow rate of 341 lpm, but there is a cost implication of course, and as I said earlier, I’m on a tight budget!
For the centre section, I could choose a standard air valve or a remote air valve. The difference is that with a remote valve, I would need an external PLC to control the pump. I don’t want that so I choose a standard air valve.
For the seats, balls and diaphragm I select Geolast®, and I can only take PTFE manifold O-rings with this combination.
After completing the configuration, I can see a photograph of my selected pump with a part number. Clicking on More Info takes me to a website page that explains the key features and benefits of that type of pump. Clicking on Technical Specs takes me to the data sheet of that product with full technical specifications, including performance charts. I can also see a list of the recommended Repair Kits for that particular product.
If I click on the Download PDF button I will get a full description of all the selections I have made when configuring this particular pump. It includes part numbers of the pump and repair kits, as well as optional accessories and their part numbers. It also includes performance charts for that specific pump, and instructions how to read them.
Application: Tomato salsa dip
For my second example, I’m putting on my other hat. I am now a supervisor in a food & beverage plant! I need to choose a pump for a sanitary application, in this case pumping tomato salsa dip at 20-30 lpm into small pots.
The first important consideration is that tomato salsa dip is a highly viscous material, with a viscosity in the range of 2000-3000 cPs. Secondly, it’s a sanitary application so I need to be able to clean my pump efficiently and quickly. I am therefore looking for a pump that can move highly viscous fluids but that is resistant to cleaning agents or high-temperature cleaning processes.
Turning to the chemical compatibility guide, I enter tomato pulp & juice in the first column and see that stainless steel and Hastelloy® are compatible materials. I’m quite happy with the less expensive stainless steel.
For the inner components, I see that no fewer than 13 plastics and elastomers are noted as showing excellent compatibility with tomato pulp. I need to look at the Materials Construction Guide to narrow down the choice.
The first spec I look at is operating temperature. I don’t want the material to melt when exposed to high-pressure steam. I can therefore immediately discard a number of materials because their maximum operating temperature is only 82oC. This leaves me with EPDM, Viton®, PTFE and PVDF, all of which withstand high temperature.
Viton® and PVDF are in a high price level. EPDM is a very flexible material as it can operate at low temperatures, and it has an attractively low price level. It’s also suitable for caustic solutions should I wish to use a tough cleaning agent, and it’s recommended for use in sanitary applications. So EPDM is looking like a good candidate.
But a couple of remarks about PTFE (Teflon®) catch my eye. It has very low frictional resistance and low adhesion. These characteristics would be excellent for my sticky, adhesive tomato salsa dip. It won’t stick to PTFE in the same way as it might to EPDM. This would make cleaning so much quicker and easier. So I’m going to select a stainless steel body with PTFE inner components.
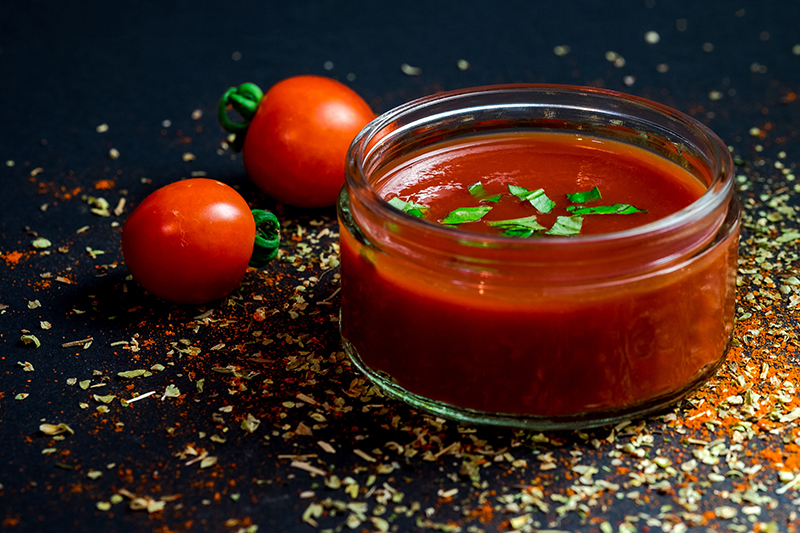
I now go to the Sanitary Pump Selector to see what pumps Graco has to offer me. For my tomato salsa dip application, FDA rating is sufficient; the other certification levels are geared towards highly sensitive fluids that can be easily contaminated. I select 316 stainless steel as fluid section material. A ½-inch inlet offers up to 61 lpm which is more than enough for my anticipated 20-30 lpm. However, I’m going to upgrade to 1-inch. The reason is that with this larger inlet size, I will later be able to choose a polychloroprene-weighted ball. This is a heavier ball that provides a better seal with high-viscosity fluids like my salsa dip.
The centre section is polypropylene as standard, which is fine as this part isn’t going to come into contact with the fluid. I have two choices for the porting: Triclamp or DIN. Triclamp fittings make it possible to connect different sections of process lines with varying sizes and end-point connections. For sanitary applications, Triclamps are the more hygienic solution.
The seat for a stainless steel pump is only available in stainless steel, but for the balls I could choose PTFE, Santoprene® or stainless steel. I’m going for PTFE for the reasons outlined above. For the diaphragm, I could select either PTFE or over-moulded PTFE. I select an over-moulded diaphragm because it has no central hole or bolt, which makes cleaning significantly easier. For the manifold rings, I will also choose them in PTFE for easy cleaning.
I am happy with my configuration and see a photograph of my selected pump with a part number. As explained before, I can now download a product brochure and technical specifications of this pump, including repair kits and optional accessories.
I now have one final step to take: I need to order my two pumps!
Need help configuring your pump?
I hope that these two articles describing the three steps on the Graco website will simplify the process of selecting and configuring a diaphragm pump. If you require further assistance or would like to see a demonstration of a Graco diaphragm pump, please fill in the contact form below.
Related Articles
Pump selection made easy with our online selector tools
Learn more about finding the right pump configuration for your application with online selector tools during a 30-minute webinar
How to configure a diaphragm pump with confidence – Part 1
The Graco website contains tools to simplify the selection and configuration of a diaphragm pump for a specific application.
How to master fluid and material properties of a diaphragm pump
Graco’s Husky Air-Operated Double Diaphragm (AODD) pumps are one of the most reliable and efficient pumps on the market. But to get the best performance out of them means selecting the right pump with the right components for every application.