How does an electronic paint dosing system work
Discover how an electronic paint dosing pump works and how it makes colour changes easy.
Electronic paint dosing systems, or proportioners, are an important element in your paint automation. In this article we take a look at the hardware of electronic proportioners, their working principle and how they make colour changes easy and efficient.
Thanks to their many advantages, electronic proportioners have become increasingly popular in many finishing operations. Knowing how they work helps you to understand how they can keep your manufacturing processes running smoothly and efficiently.
Electronic proportioning hardware
A typical electronic proportioning system includes two key pieces of hardware:
- The controller offers an easy-to-use interface for placing the system in standby, mix, purge or colour selection mode. The controller is also used for reading and clearing alarms, printing reports or monitoring live production.
- The fluid panel contains the fluid meters and the dosing valves for the base and the catalyst components used in plural component paints. They work together to control the flow of the individual materials to the systems integrator. Once the materials have been injected into the integrator at the proper ratio, the integrated material is moved through a static mixer. The solvent flush and air-purge valves for clearing the mixed material from the system, as well as the colour-selecting valves, are also located on this piece of hardware.
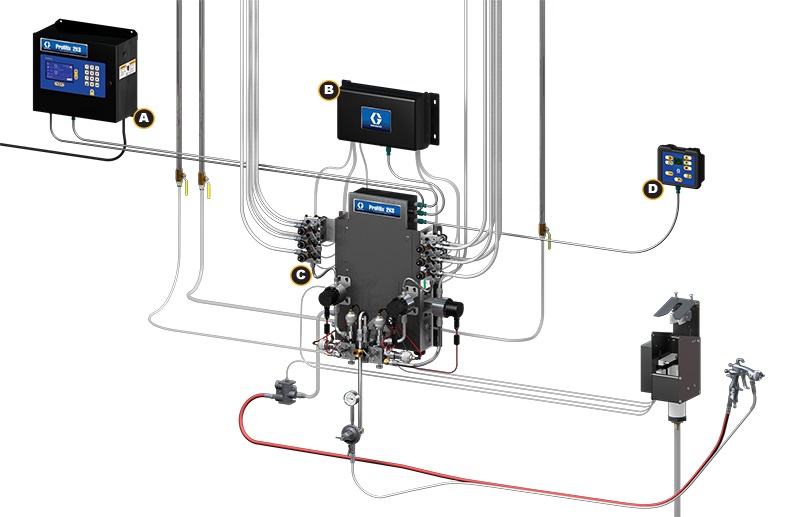
ProMix 2KS
(A) EasyKey (B) Colour-change system (C) Fluid panel (D) Booth controller
The mixing process
After the proportioning system is programmed with the user’s colour and ratio information, the operator simply enters the recipe number on the controller. This will start the mixing process. If the recipe calls for a 4:1 mix ratio, the system will dispense four parts of the base material and one part of the catalyst material. The system completes this operation by counting pulses from the fluid meter and opening and closing the dispense valves accordingly. Each meter pulse represents a specific amount of material that has passed through the system.
After each cycle, the system verifies ratio accuracy. When accuracy has been confirmed, the system mixes another 50cc batch. This continuous process occurs without spikes or surges to the material dispense rate.
Colour changes
When the operator calls for a colour change, the solvent flushes out the previous resin colour from the colour-change valve up to the dosing valves. Once the old resin colour has been flushed from the system, the new resin colour is introduced.
Before the new colour can be sprayed, the mixed material line must also be thoroughly flushed. The system first uses air to push the majority of the old mixed material out of the fluid line. It then uses alternating short pulses of air and solvent, called the ‘air-solvent chop’, to create a turbulent flow for improved cleaning of the mixed material line while conserving solvent. After the line is thoroughly cleaned, the hose is filled with solvent. Once the flushing procedure is complete, the new colour can be loaded into the applicator.
The flush procedure can be automated. All you have to do is choose the colour on the operator station, place the gun in a gun flush box and press the enter key. The system will then perform a pre-programmed flush procedure.
Related Articles
The advantages of an electronic paint dosing system
Electronic paint dosing systems offer many advantages, such as enhanced ratio accuracy and waste reduction.
Electric paint circulation pumps: why brushless DC motors are better than AC motors
BLDC electric circulation pumps in paint systems enable optimal efficiency, control and performance.