Chemical pumps: Why go electric?
As a chemical company, you are probably using centrifugal or air-driven pumps to unload, transfer or mix your materials. Yet, electric double diaphragm pumps or EODDs like Graco’s QUANTM pump, have several advantages for chemical processing applications over other pump technologies. Here are 6 reasons why you should consider Graco’s QUANTM chemical pumps.
1. Improved safety
Safety is the number one reason companies like yours choose QUANTM.
Many chemical processors prefer double diaphragm pumps over centrifugal pumps for chemical transfer as centrifugal technology relies on mechanical seals, whereas double diaphragm pumps have a seal-less design.
Mechanical seals wear out and when the seal fails, fluid will leak out of the pump casing along the rotating shaft. Depending on the fluid being pumped, the leak could be hazardous or polluting to the environment or dangerous for your colleagues.
Diaphragms are a better option compared to mechanical seals, but they will not last forever. When a diaphragm in a pneumatic pump fails, the chemicals can enter into the air valve and disperse through the muffler, into the air, potentially harming employees.
Leak containment
Leak containment is a critical component of chemical processing – it is a cornerstone of safety and environmental responsibility within the industry. When compared to other pump technologies, QUANTM pumps provide several advantages for leak containment.
QUANTM pumps are fully electric and do not need a muffler. So when a diaphragm fails, material is contained inside the pump, ensuring no loss of containment.
QUANTM also has a built-in leak detector. This detector immediately identifies a problem when a leakage does occur. The pump will automatically shut off, keeping your plant personnel safe.
2. Less noise
The QUANTM electric chemical pump is significantly quieter than an air-operated double diaphragm (AODD) pump because it does not require any compressed air to operate. With QUANTM you can achieve a reduction in sound pressure around 25%.
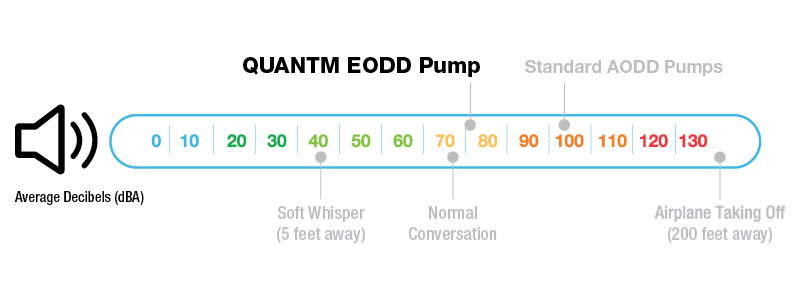
At full power and flow this chemical pump clocks in at 74 dBa, while AODDs are typically around 100 dBa.
100 dBa is the equivalent of a motorcycle or a chainsaw. It is well above 85 dBa, the maximum noise level a worker should be exposed to. Everything above 85 dBa can lead to hearing damage, especially when your hearing is exposed to such high levels for several hours a day.
To put that in perspective: a QUANTM pump is as loud – or as quiet – as a normal conversation. And with 74 dBa, it poses no risk to yours or your colleagues’ ears.
Unload without disturbing the neighbourhood
Replacing loud AODD pumps will significantly reduce noise pollution in your factory. But you will also find a big impact outside of your site.
Noise may not be a problem when unloading at another industrial site, but it can become an issue when unloading in public places – especially in dense residential areas like the municipal swimming pool or hotels.
In order to operate an AODD chemical pump on a mobile truck, you have to run it off your truck’s air brakes – most of the time this requires the truck engine to be powered on to generate the compressed air for pump operation.
Without the need for compressed air to power the QUANTM pump, not only is the pump operation itself significantly quieter, but there is also no need to start up the truck engine. This makes it possible to unload quietly, minimizing disturbance in residential areas.
3. Cost advantage for maintenance
Mechanical seals in centrifugal pumps not only wear out faster than diaphragms, they are also more costly to replace.
Centrifugal pumps are prone to damage caused by deadheading compared to a double diaphragm pump. A closed discharge valve or blockage traps fluid, creating excessive pressure and heat within the pump. Without the purchase of additional sensors and controllers, a centrifugal pump will continue to run until something fails.
Furthermore, leakage into the pump can damage additional expensive pump components like a bearing, dramatically increasing maintenance and repair costs.
Save money on your chemical pump maintenance
Remember QUANTM’s built-in leak detector?
This detector not only improves safety, it also prevents additional damage due to leakage. On top of that, QUANTM pumps stall under pressure to avoid pressure related damage to your system.
This combination gives QUANTM a huge cost advantage for pump maintenance.
4. More materials to choose from, less clogging
Particularly in the chemical industry, selecting a centrifugal pump for pumping solids is quite a challenge. You need a pump that is not only compatible with the chemicals being processed, but one that is also capable of handling solids and abrasive material without causing increased pump wear and potential blockages. Centrifugal pumps are typically made out of metal or materials that are not chemically resistant.
Extended life
With QUANTM EODD pumps, you have a wide selection of material options for the fluid section and internal fluid contact components to enable safe transfer of various chemicals.
QUANTM EODD pumps have a clear flow path with no internal obstructions, making them far less prone to clogging by solids; the flexible diaphragms act as a barrier to the working parts of the pump, reducing wear and extending the pump life while maintaining the integrity of shear-sensitive products.
5. Improved control
You are in the business of metering, dosing and mixing, and this has to be done precisely.
QUANTM EODD pumps offer more advanced capabilities over the basic metering and dosing options provided by pneumatic pumps. The QUANTM chemical pump allows for
- Adjustable flow rates,
- Quick and easy priming,
- Internal overload protection.
Remote operation and speed control
You can control QUANTM with an integrated I/O: it can be controlled remotely and report operational status.
This allows for remote flow and pressure control, minimizing operator oversight.
6. Less energy and CO2 emissions
The sixth notable advantage QUANTM pumps have over pneumatic pumps is the reduction in energy consumption and CO2 emissions. The QUANTM pump minimizes energy consumption by cutting energy usage and costs by up to 80% compared to an AODD. And every kWh saved means less CO2.
Bye bye air compressor
On top of that, replacing your air driven pumps with electric driven pumps also allows you to minimize compressed air consumption. Potentially shutting down energy consuming air compressors.
Compressed air is one of the most underestimated costs within production companies. Compressed air and the electricity to produce it, eat up more of your budget than you might think. For perspective, it takes about 7 horsepower of electric power to operate a 1 HP compressed air motor.
Put safety first with QUANTM
In conclusion, Graco's QUANTM chemical pumps offer several advantages over traditional centrifugal and air-operated diaphragm pumps for chemical processing. With improved safety being the absolute number one reason why other chemical companies are switching to QUANTM.
This pump prioritizes safety with leak containment features and a durable diaphragm pump design that reduces noise pollution significantly and offers considerable cost savings through reduced maintenance and extended pump life.
Additionally, QUANTM pumps provide superior versatility for handling various chemicals and solids, allowing for more advanced dosing and metering, and contributing to sustainability goals through lower energy consumption and CO2 emissions.
By switching to QUANTM pumps, you achieve a safer, quieter, more cost-effective, and environmentally friendly operation.
Interested in going electric?
- Get in touch with our experts
For more information about glue applications and the pumps being used in those applications, fill in the contact form and one of our experts will contact you shortly.
- Calculate your savings
In three easy questions, calculate how much you could save by converting your
facility to Graco electric double diaphragm pumps
Contact an expert
Related Articles
The role of pump technology in LOC prevention in the chemical industry
Preventing loss of containment (LOC) incidents is paramount for ensuring the well-being of employees and maintaining a safe work environment. This article explores the causes of these types of incidents and proposes preventive measures, with a particular focus on the role of pump technology in conta...
Case study: Double Diaphragm Pumps in Chemical Application
A chemical manufacturer transitioning to a newly purchased facility sought to reduce their reliance on compressed air. As the facility was being completely renovated into a new manufacturing plant, they had the opportunity to evaluate and install a variety of pumping options and technologies. Previo...
Chemical transfer pump QUANTM: Selecting the right pump
Safer, quieter, more advanced capabilities, with reduced energy usage and CO2-emissions: in a nutshell the main advantages the QUANTM electric pumps have over centrifugal pumps and air-operated double diaphragm pumps. But where in your processes is the added value most significant and what pump conf...