3 Steps to VOC reduction in industrial painting
With three simple steps manufacturers can reduce their VOC emissions and avoid legal penalties.
Volatile organic compounds (VOCs) from paint can cause serious health and environmental effects. In order to limit VOC emissions from a variety of sources, including industrial painting, the VOC Solvents Emissions Directive requires industrial installations to comply with strict emission limit values. With three simple steps VOC reduction can decrease emissions and help you to avoid legal penalties.
Volatile organic compounds (VOCs) are the carbon-based solvents that give traditional paints their unpleasant odour. VOCs from paint can cause serious health effects including skin and eye irritation, kidney damage, cancer, reproductive disruption, respiratory issues and impaired cognitive function. Due to its health and environmental effects, the emission of VOCs is subject to stringent regulations.
VOC Solvents Emissions Directive
The VOC Solvents Emissions Directive (1999/13/EC) is the main policy instrument for the reduction of industrial emissions of volatile organic compounds (VOCs) in the European Union. The Directive requires installations to comply either with the emission limit values set out in the Directive or with the requirements of the so-called reduction scheme. The Directive sets out emission limit values for VOCs in waste gases and maximum levels for fugitive emissions (expressed as a percentage of solvent input) or total emission limit values.
3 Steps to VOC Reduction
Most manufacturers can lower VOC emissions from their paint lines in three steps.
1. Reduce the Amount of Paint Sprayed at a Target
The term "transfer efficiency" refers to the amount of paint that is deposited on the part compared to how much sprays past the part and is wasted. By increasing transfer efficiency we reduce the amount of paint sprayed.
Spraying less paint leads to a reduction in released VOCs. It also improves the life of your booth filters.
Transfer efficiency increases as a result of using different spray technologies. By maximizing transfer efficiency and spraying less paint, manufactures not only save money, but it also means less maintenance, clean-up, lower filter costs and VOC emissions.
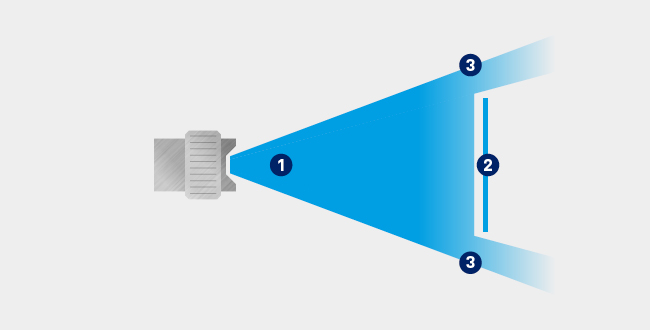
By maximising transfer efficiency, manufacturers can reduce VOC emissions
(1) Fluid (2) Surface (3) Overspray
2. Control the amount of solvent used
The amount of solvent can be reduced through accurate mixing and ratio assurance to ensure materials are mixed on demand at the correct ratio for optimal performance. Precision flow control provides a consistently smooth fluid delivery. A plural component proportioner, designed to reduce waste by moving the mixing point closer to the gun, can result in up to 80% reduction in flushing waste and faster colour changes. This design feature ensures that the material is mixed precisely before it is sprayed. For manufacturers, this means lower VOC expenses and less wasted paint.
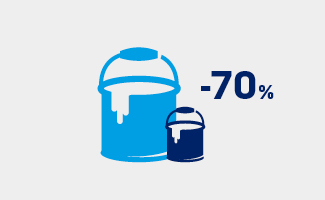
Daily paint usage:
Traditional systems – ProMix PD2K
70% savings
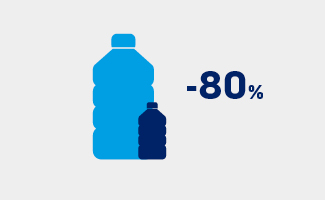
*Based on 7 colour changes per day and a hose length of 50ft with a ¼" diameter, costs can be reduced by up to 80%.
Daily solvent usage:
Traditional systems – ProMix PD2K
80% savings
3. Consider Automating Your Paint Line
Paint booths are hazardous environments. Employees who spend their days in the booth are exposing themselves to toxic fumes and explosive chemicals.
Automation can reduce material consumption by up to 30 percent. Thanks to the accuracy of robots, you have more control and access to how much material is used, which is going to reduce your material costs significantly.
To reduce waste even more, manufacturing managers should look at the type of equipment used with their robot. WIth plural component proportioners that mix material close to the gun and automatic electrostatic guns that increase transfer efficiency, you can save material and money on VOC disposal fees. Using spray equipment that easily integrates with robot technologies ensure that the spray parameters and spraying motion is exactly the same each time, which increases quality.
Conclusion
Manufacturers of all sizes are benefiting from the many advantages of automation. Automation can definitely save manufacturers money far exceeding the implementation costs. The savings are everywhere from quality and increased production to reducing waste and overhead costs. If you have ever considered automation in your plant, now is the time to say yes.
Related Articles
5 significant advantages of robot painting
The advantages of automated painting: reduce costs and waste and improve flexibility and quality.
What determines transfer efficiency of automated paint systems and how to improve it
Understanding the importance and the influence factors of the transfer and spray system efficiency of automated paint strategies.