开创性的混合方法每年可以避免价值 7.5 万美元的不良部件
空间有限的汽车零部件制造商通过 ProDispense 获得了精确而安全的混合。定制的流体分配系统在不到一年的时间内就获得了投资回报。
一级汽车供应商找到了安全、紧凑的精确混合方法
客户:一级汽车制造商
固瑞克设备:ProDispense
挑战:一家专门生产后视镜系统的汽车零部件制造商的喷涂生产线上采用了机器人自动作业,每周运行五到六天,每天两个班次。涂饰工艺经理负责喷涂间的各个方面,对两种独立的三组分清漆材料进行了批量处理。
由于空间不足,该喷涂间手动混合每个批次的材料。像大多数手动工作一样,这种方式难免人为错误。溶剂未能正确地添加到清漆和催化剂混合物中,这会影响干燥时间并导致部件不合格。平均而言,这种情况每年发生四到五次,不良部件的成本加起来高达 7.5 万美元。
这家公司以他们的制造工艺而自豪,夸口一次通过率为 98%。与不良部件相关的返工大大降低了这一统计数据。高层管理人员呼吁进行改变。
解决方案:精度和一致性是第一要务。通常来说,电子配比系统是首选的解决方案。但是,由于空间的限制,无法安装这样的系统。他们还需要一种可以在喷涂间内以本质安全的方式进行控制的方法。
为适应他们独特的环境,固瑞克工程师为 ProDispense 系统开发了一种创造性的用法。分别用于两种清漆、一种催化剂和一种溶剂的四个流体面板可以安装在喷涂间的外面,用管道输送到危险区域的料桶内。采用预设好的配方配置可以快速轻松地完成新批次作业。精度在 3% 以内,每个批次都能实现一致的品质。
涂饰工艺经理还需要一种在喷涂间内部开始和停止分配的方法。为此,他们投资购买了本质安全的无线启动/停止开关。
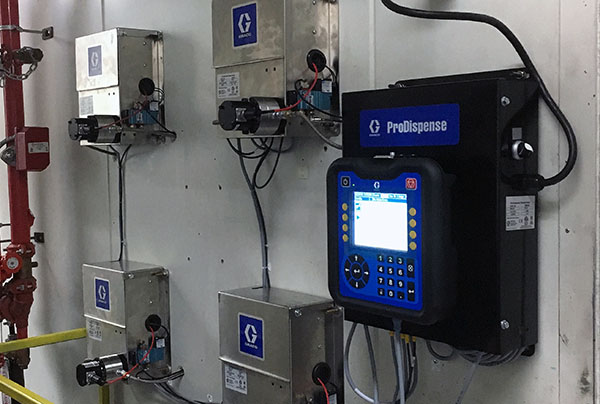
结果:安装九个月后,实现了精确的物料分配。返工率减少了 85%,不到一年内就实现收益。
通过采用固瑞克的解决方案,这家汽车零部件制造商不仅节省了资金,还挽救了声誉。