Anti Flutter Application for Body Shop Closures
What is Anti-flutter?
Anti-flutter is an automotive closure application that bonds the inner and outer panels of car bonnets, roofs, doors and boots to reduce vibrations or “fluttering.”
The Anti-flutter Process
This closure application happens in the body shop before forming the hem flange. After securely positioning the inner and outer panels, an adhesive is strategically spaced along the inside of the outer panel. The inner panel is placed onto the outer panel, forming a thicker, more durable panel. Precise dispensing and placement of the adhesive is critical in creating a secure panel designed to protect the exterior of vehicles and essentially reduce noise during operation.

Material Dispensing
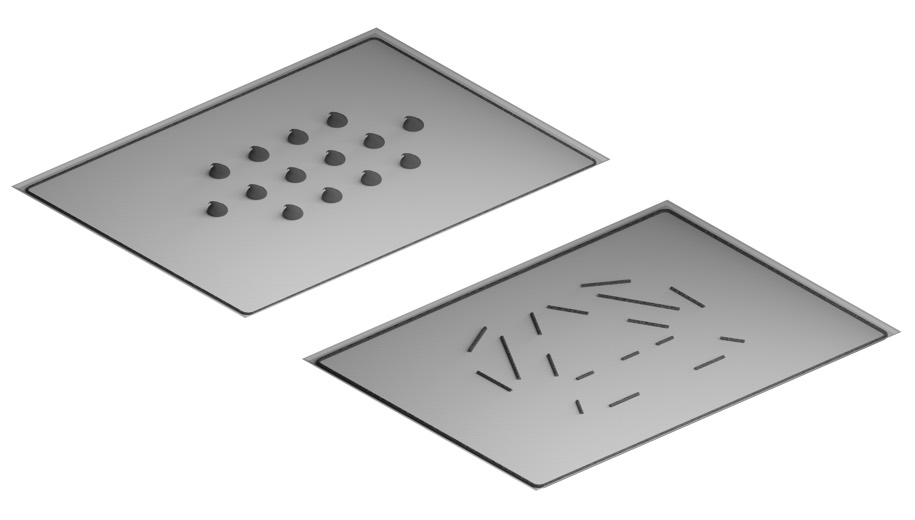
In anti-flutter applications, one component rubber-based adhesives or vinyl plastisols effectively dampen sound while eliminating vibrations in multi-material automotive components. The material is typically dispensed as a traditional bead or conical shape, like a rain droplet, in a stitch pattern or multi-dot application.
Challenges of Anti-flutter
Accurate dispensing is imperative to have reliable and durable car closure parts. Dispenses that have inconsistent Cpk’s and vary in size come with high costs:
- If dispenses are too large, the material is wasted, resulting in higher material costs
- If dispenses are too small, the bonding of the panels is likely to be faulty, resulting in additional repair costs, wasted production time and poor end-user customer experience
Additionally, cycle time plays an essential role in avoiding inefficient production. If the equipment has a long cycle time or requires downtime between cycles, less production occurs in the manufacturing plant. The ability to dispense 60-90 stitches, beads, or drops in a shorter amount of time will boost the effectiveness of your production.
Summary
Anti-flutter applications require strategic placement of precisely dispensed paste adhesive. Graco offers one component pumping and metering systems for automated installations to ensure your automotive closure applications are dependable.
Contact an Expert
Related Articles
Why Electric Motors Improve Quality and Precision of Dispense for 1k Metering
Electric motors have the capability to drive the pump lower more intelligently and therefore, dispense an accurate bead without the need for an intermediate metering device.
Lightweighting in Manufacturing Processes
Lightweighting is a modernised, cost-effective manufacturing concept that is proving superior to old methods. Find out about additional benefits and how lightweighting can bring auto manufacturing to the next level.
Hem Flange Bond in Automotive Closure Assemblies
Hemming is considered one of the most challenging applications in automotive construction. Here’s what you need to know in order to improve crash safety, prevent corrosion and perfect appearance.