Blast Cleaning for Municipalities
VAPOUR ABRASIVE BLASTING: A NEW CLEANING & SURFACE PREPARATION TOOL FOR MUNICIPALITIES
Virtually every public works department has faced the unenviable task of removing paint or other markings from roadways, walls, or other structures. Whether the target is lane striping for a realigned roadway, unwanted graffiti from a retaining wall, or a weathered monument needing restoration, marking removal has often proven a messy task accompanied by health and environmental concerns.
An Alternative to Dry Blasting
The default choice for large-scale removal has historically been sandblasting or other dry blasting techniques. Dry blasting has been an effective, but dusty approach, with emissions of silica and other abrasive or substrate particles linked to negative health and environmental impacts. As most city projects are located in public areas with local residents and businesses nearby, dust is a concern for the workers, as well as people walking, driving and biking in these areas, especially since they are not wearing proper personal protective equipment (PPE).
As an alternative to dry blasting, wet blasting was developed in the 1960s to minimise fugitive dust, but was slow to catch on due to heavy water use and the problem of containing and disposing of contaminated water. Contractor familiarity with dry blasting and additional costs with the additional water and abrasives of wet blasting also limited acceptance of the newer technique.
To address some of the challenges of wet and dry blasting, a growing number of municipalities are exploring vapour abrasive blasting, which uses just enough water to suppress dust and still achieve desired production rates. Units such as the Graco EcoQuip 2 EQp, shown in Figure 1, combine water and abrasive in a pressurised chamber and inject the mixture into an adjustable airflow, suppressing dust up to 92 per cent when compared to dry blasting. In addition, these new machines live up to the “vapour” name – the EQp uses, on average, one-fourth to one-half a litre of water per minute.
Health, Safety & Environmental Factors
Health and environmental factors have been key drivers in the development of wet and vapour blasting systems. Several European nations banned sandblasting in the 1950s and 60s due to concerns over silicosis, an occupational hazard associated with inhalation of silica dust. While the US has not totally banned sandblasting, the US Occupational Safety and Health Administration (OSHA) established a Silica Rule in 2016, decreasing the permissible exposure limit to respirable crystalline silica by 50 per cent for general industry and maritime, and 80 per cent for the construction industry. The construction standard becomes effective 23 September 2017.
Wet blasting has also been subject to environmental regulatory limitations. According to the United States Environmental Protection Agency (EPA), the Federal Water Pollution Control Act, first introduced in the 1940s and amended several times since then, placed strict limits on discharge of pollutants into navigable waters. States and cities have also scrutinized the amount of fugitive water in storm water systems due to the amount of water used by some systems. For example, halo nozzles, which use a curtain of water to surround the abrasive blast after impact and water-injection nozzles (WINs), which use jets of water to dampen abrasive as it leaves the nozzle, both use significant amounts of water.
Vapour abrasive blasting addresses both the fugitive dust and the water discharge issues. Vapour abrasive blast systems combine water and abrasive in a pot under pressure, then inject this mixture into the airflow, providing precise control over the air pressure and water/abrasive mixture and reducing the amount of media and water expended. The vapour abrasive approach encapsulates individual grains of abrasive material in water, weighing the particles down and providing more mass on the particle at impact. Because dust is minimised, less containment is generally required and media clean-up time can be reduced. With less water use than slurry or other water-based technologies, vapour abrasive blasting does not leave pools of water behind, and the likelihood of toxic run-off is greatly reduced. It also reduces rebound of abrasive particles, which pose risk to workers and the environment.
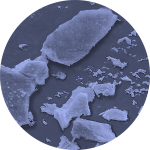
Silica dust, magnified
Contact an Expert
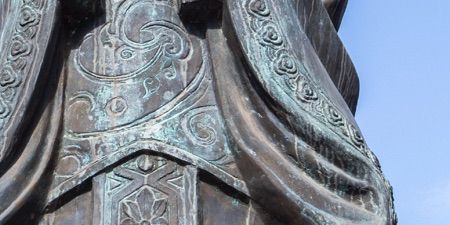
Clean and restore statues and monuments
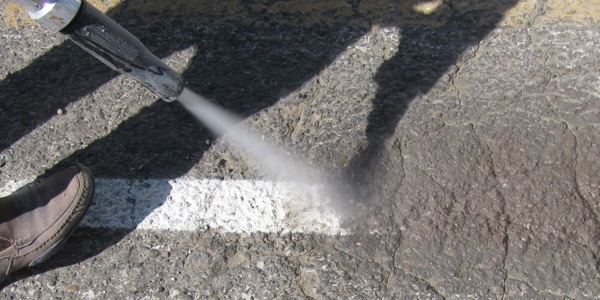
Blast away parking lot lines and lane markings
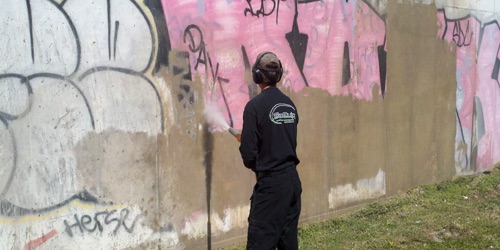
Vapour blasting removes graffiti on concrete
Related articles
Silica Dust and Wet Abrasive Blasting
Innovation in abrasive blasting technology being driven by the need to control silica dust
How to Prevent Flash Rust When Wet Blasting
As wet cleaning methods have increased, so has the prevalence of flash rust and the need to prevent it - here are a few tips.
How to Choose the Right Blast Nozzle for Wet Abrasive Blasting
What you need to know to choose the right nozzle for your abrasive blasting application