How to Choose the Right Blast Nozzle
Choosing a Blast Nozzle
When selecting a nozzle, there’s a balance to be struck and it starts with your air compressor. Once you understand how the size of your compressor effects production capabilities, then you'll want to look at nozzle size. Choose a nozzle with too small of a bore and you’ll be leaving some blasting capacity on the table. Too large a bore and you’ll lack the pressure to blast productively.
Next is the shape of the nozzle. The two main nozzle shapes are straight bore and venturi, with multiple size and pattern variations within. Finally, you'll want to consider the material the nozzle is made of. Specifically, the material that makes up the lining inside the bore. The three main factors in selecting the ideal nozzle bore material are durability, impact resistance and price.
Air Compressors
Proper nozzle selection can have a significant effect on the profitability of both small and large blasting jobs, and it starts with your air compressor.
Rotary Compressor
- Intakes 5.2+ m3 (185+ cubic feet) of air per minute at atmospheric pressure
- Compresses the air into smaller volume at high pressure
- Nozzle compresses the air into even smaller volume (3/8" - 3/4" I.D.) at extremely high pressure
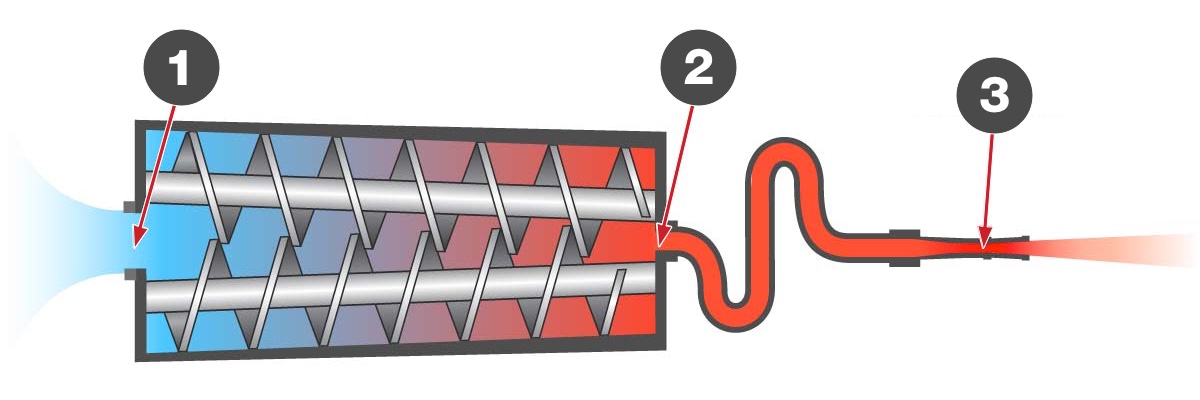
The more air volume you can compress per minute, the higher the pressure produced at the nozzle. This improves your production rate in two ways:
- High pressure increases the velocity of the abrasive particles, delivering more kinetic energy upon impact, imparting a deeper anchor pattern. This allows you to use a finer grade of abrasive, which produces more impacts per volume.
- More air capacity lets you use a bigger bore nozzle, which allows you to put more abrasive on target.
Assuming that the air compressor capacity available to you is not unlimited, you’ll need to select a nozzle with an orifice small enough to maintain a productive air pressure at whatever volume your compressor can supply.
Nozzle Size
For vapour abrasive blasting, the most commonly-used nozzle orifice sizes range from 3/8" inner diameter to 3/4", increasing by increments of 1/16". A 3/8" nozzle is sufficiently constricted to produce a effective blast pressure with a 5.32 m3/min (185 CFM) compressor. A 1/2" nozzle is sufficient to produce an effective blast pressure with a 10.62 m3/min (375 CFM) compressor.
It’s important to note that when you double the diameter of the orifice, you quadruple the size of the orifice and the volume of air and abrasive that can pass through the nozzle.
To find your optimally productive nozzle, determine what nozzle pressure in bar (PSI) you need to maintain for productive blasting and what volume of air your available compressor can supply per minute (m3/min (CFM)), then consult the following chart to find the nozzle orifice size that meets those parameters.
Volumetric Capacity (m3/min (CFM)) Required for Pressure, by Nozzle
Bear in mind that your compressor will produce less pressure at the nozzle than what is indicated on the chart, depending on the condition and configuration of your equipment.
Orifice Diameter | Nozzle Pressure |
Minimum CFM Required | ||||||||
Nozzle Size
| inches | mm | 50 | 60 | 70 | 80 | 90 | 100 | 125 | |
#6 | 3/8" | 9.5 | 110 | 124 | 145 | 160 | 175 | 200 | 275 | |
#7 | 7/16" | 11 | 150 | 170 | 200 | 215 | 240 | 255 | 315 | |
#8 | 1/2" | 12.7 | 200 | 225 | 250 | 275 | 300 | 340 | 430 | |
#9 | 5/8" | 16 | 300 | 350 | 400 | 450 | 500 | 550 | 700 | |
#10 | 3/4" | 19 | 430 | 500 | 575 | 650 | 700 | 800 | 1100 |
Abrasives Affect Blast Pressure Over Time
Nozzles wear out. Abrasive passing through the nozzle will wear away the lining, enlarging the orifice. A worn nozzle requires more volume per minute to maintain your target pressure.
For example, If you bought a #8 (1/2") nozzle to get 6.9 bar (100 PSI) with your 10.62 m3/min (375 CFM) compressor, once it has worn out 1/8" diameter to the next nozzle size up (#9 – 5/8"), you'd be lucky to maintain 4.5 bar (65 PSI) using the same compressor (on the #9 line, the 10.62 m3/min (375 CFM) compressor falls between 9.9 and 11.3 m3/min (350 and 400 CFM), so you can only maintain 65 PSI), because the volume of air passing through the enlarged orifice would be inadequate to maintain the pressure.
However, if you purchased a #7 (7/16"), still using a 10.62 m3/min (375 CFM) compressor and targeting 6.9 bar (100 PSI), once it had worn out to the next size up (#8 – 1/2"), you'd still be able to achieve 100 PSI, but you'd sacrifice some productivity earlier in the nozzle's life (compared to a #8 (1/2") nozzle) because the amount of air and abrasive that could pass through the orifice at 6.9 bar (100 PSI) would be less than what your compressor could supply.
Pressure can drop significantly between the compressor and the nozzle, up to .07 bar (one PSI) per 15.24 m (50') of hose (25.4 mm (1”) I.D.). In addition, pressure will drop with each bend in the hose or change of direction: the shortest, straightest hose configuration is best. On top of that, if there are ill-fitting couplings or leaks in the hose, the pressure drop could be total.
Not only does the size of the nozzle bore effect volume and pressure, but it effects the size of the blast pattern. For each nozzle size increase, expect up to a 10% increase in the size of your blast pattern. But it's the shape of the nozzle, rather than orifice size, that has the most impact on the size of your blast pattern.
Nozzle Shape
Nozzles come in two basic shapes: straight bore and Venturi, with several variations of Venturi nozzles.
Straight Bore

As compressed air enters the converging (left) end of a straight bore nozzle it accelerates, accelerating the abrasive particles suspended in the flow. The particles exit the nozzle in a tight stream and produce a narrow, concentrated blast pattern upon impact.
Long Venturi

Blast Pattern: 3" at 18" distance
Production Rate: 4.5/5
Venturi nozzles feature a converging entry and a diverging exit. This shape is designed to produce an effect which greatly accelerates the air flow and particles – it is not, however, the Venturi effect.
The Venturi effect is an observation that when an air flow accelerates while passing through a constriction, there is a corresponding drop in pressure.
This is not the key principle at work in a “Venturi" nozzle. Technically, these nozzles are de Laval nozzles, the same design featured in jet exhausts. The rapid acceleration of the air flow and particles in a de Laval nozzle is due to an effect that occurs as the flow breaks the speed of sound.
Besides producing tremendous acceleration, the angled shape of the diverging end spreads out the flow, producing a large blast pattern and a more uniform particle distribution than a standard bore nozzle.
Long Venturi nozzles produce up to 40% better production rates and consume less abrasive compared to straight bore nozzles.
Double Venturi

Blast Pattern: 3" at 18" distance
Production Rate: 4/5
A double Venturi nozzle is a de Laval nozzle with an extra wide exit opening and holes at the diverging end.
According to the Venturi effect, as the velocity of a flow increases, the pressure drops, creating a vacuum between the shock wave and the throat, reducing abrasive velocity. With a double Venturi nozzle, atmospheric air is drawn through the holes into low pressure area, expanding the air flow to produce a wider blast pattern.
Wide Throat

Blast Pattern: 3" at 18" distance
Production Rate: 5/5
Wide throat nozzles are de Laval nozzles with a wide throat and an extra 6.35 mm (1/4") wide converging section. When used in conjunction with a hose with matching inside diameter (and with a corresponding air volume increase), the wide throat nozzle can enhance productivity up to 15% over long Venturi.
XL Performance

Blast Pattern: 5" at 120 cm (48") distance
Production Rate: 3/5
These extra-long nozzles accelerate particles over a longer distance, achieving higher exit velocities, allowing the blaster to stand further back from the surface being blasted and producing a larger blast pattern and higher production rates.
Nozzle Material
The third consideration when choosing a nozzle is the composition of the lining inside the bore. Harder materials will be more resistant to wear, but are more expensive to replace and are prone to cracking under rough handling. There are three basic types of carbide nozzles.
Tungsten Carbide
Durability: 1/5
Impact Resistance: 5/5
Price: Low
This is the least durable of the carbide nozzles, but relatively cheap and resistant to impact. Suitable for blasting slag, glass and mineral abrasives.
Silicon Carbide
Durability: 1/5
Impact Resistance: 5/5
Price: Low
Impact resistant and durable like tungsten carbide, but lighter. Causes less operator strain.
Boron Carbide
Durability: 3/5
Impact Resistance: 1/5
Price: High
Extremely hard and durable, but brittle. Up to ten times the longevity of tungsten carbide.
Composite Carbide
Durability: 5/5
Impact Resistance: 3/5
Price: High
Some manufacturers produce their own composite carbide nozzles, which are even harder than boron carbide.
Nozzles are not cheap to replace. One benefit of vapour abrasive blasting is that your nozzles will last up to 3x longer than a dry blasting nozzle, because the particles are enclosed in a lubricating water jacket, which reduces friction between the abrasive and the nozzle lining.
Another important benefit is that the vapour abrasive blaster has fine control over his abrasive feeding rate. With sandblasting, it’s more difficult to adjust, with a lesser range. Moving up from a #6 to a #8 nozzle with a sandblasting rig will almost double the amount of abrasive consumed.
Research has shown that blasting productivity gradually increases with abrasive feeding rate until a critical value is reached, after which productivity maintains constant. So after that value has been surpassed, consuming more media actually reduces particle velocity, wastes abrasive and lowers efficiency.
Because the vapour abrasive blaster can easily adjust his abrasive flow rate to find that critical value, he can achieve optimal productivity at lower pressures than dry blasting.
Final Thoughts
Big air and big nozzles lead to big production rates, but it's the shape of the nozzle bore that determines the acceleration of the particles and the size of the blast pattern.
To maximise your productivity, choose the biggest nozzle bore that your compressor will support at a pressure that will be productive, given the surface characteristics and specifications of the task, while taking into account that there will be a significant reduction in pressure as your nozzle wears to a larger diameter. Finding the sweet spot where your nozzle can be productive over its useful life span is key to getting the most value out of your nozzle.
Contact an Expert
Related articles
Silica Dust and Wet Abrasive Blasting
Innovation in abrasive blasting technology being driven by the need to control silica dust
Silica Comparison Wet vs. Dry Blasting
Third-party Industrial Hygiene Survey in order to evaluate potential exposures to respirable airborne dust and respirable silica
How to Prevent Flash Rust When Wet Blasting
As wet cleaning methods have increased, so has the prevalence of flash rust and the need to prevent it - here are a few tips.