Ethyl Mercaptan Use in Chemical Injection
Ethyl mercpatan, commonly known as Ethanethiol, is a colorless chemical compound with an overpowering odor that is used as an additive in natural gas and liquified petroleum gas (LPG) in the oil and gas industry.
The main application of Ethyl mercaptan is as an odorant that provides a vibrant rotten egg or garlic scent that can help detect gas leaks. Mercaptan is used within the chemical injection process of gas operations because its unique smell makes it easily identifiable. When this chemical is combined with natural gas the smell is diluted but becomes potent when exposed to air. The stench helps operators detect leaks earlier so operators can take proactive action, protecting both the job site and the surrounding area. Incorrect use of this chemical in various operational processes can create nuisance conditions that negatively impact how the community views operators and manufacturers.

Note: The above graph shows the odor threshold of other clear chemicals that release a scent. Out of the chemicals shown, Ethyl mercaptan has the weakest odor strength.
Concerns about using Ethyl Mercaptan
Although low concentrations of this chemical get exposed if there is a leak, concerns have been raised within communities surrounding operations that use mercaptan dosing in their chemical injection processes.
Effects of Chemical Spillage
A main concern that these communities have over adding Ethyl mercaptan to most oil and gas operations is chemical spillage. If Ethyl mercaptan were to be spilled, it could harm people, animals and the environment. If humans were to inhale, ingest or have this chemical absorbed through their skin there could be negative, long-lasting effects. These negative effects are similar to what could occur to wildlife if the chemical was exposed to the environment through the ground, waterways, sewers or drains.
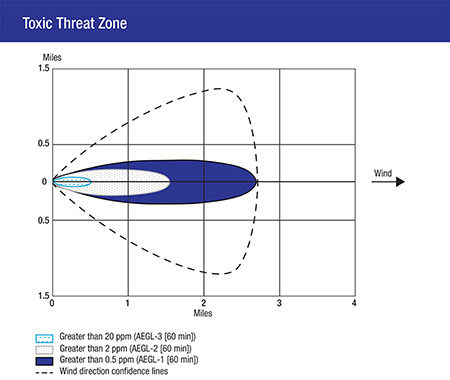
The odor of Ethyl mercaptan can travel great distances and wind direction can impact the range of chemical exposure. Graph source: NOAA Office of Response and Restoration.
Ethyl mercaptan can also be highly flammable if left uncontained. If a fire is caused by this chemical, it can produce toxic gases harmful to the environment, such as carbon monoxide and sulfur oxides. In addition to increased toxins being released, the containers that hold the natural gas and mercaptan mixture could explode, leaving a bigger mess.
Effects of Overaddition
Most of these concerns can only occur if the amount of mercaptan added to the natural gas is more than the recommendation. Not only could the overuse of mercaptan negatively affect the quality of natural gas, but it can also cause other issues.
Pipeline Corrosion and Leaks
An integral part of oil and gas operations is the pipeline that transports material. The pipeline must maintain its pristine condition to keep operations running efficiently. But if too much mercaptan is added there is a greater chance of corrosion in the pipelines. This corrosion can be anything from pipes splitting to cracking, which can lead to leaks – one of the main things that operators want to avoid. Not only can these leaks increase downtime and reduce productivity, but they can also be costly to repair!
Increased Maintenance and Repair Costs
According to a report by the Pipeline and Hazardous Materials Safety Administration (PHMSA), they estimate that the United States oil and gas pipeline industry spends around $7-8 billion per year due to corrosion.
In addition to repairing the pipes, corrosion also requires that operators regularly perform maintenance, which can hurt the bottom line and take time away from workers performing other activities.
Contamination
Corrosion can also cost operations when it comes to the transferred material itself. Specifically, if any pipe cracks formed due to corrosion, the risk of contaminating the product increases. This contamination can decrease the value of the material, which affects the operation's bottom line.
Unsafe Work Conditions
If the pipeline’s integrity becomes compromised from corrosion or leaks, it creates an unsafe work environment for pipeline workers. Corrosion cracks and splits can result in leaks through the release of flammable materials into the environment. This exposure increases the probability that an accident could occur on the worksite. According to the US Pipeline and Hazardous Materials Safety Administration, corrosion is responsible for 18% of pipeline accidents in the United States.
Compliance Issues
Additionally, due to having too much mercaptan added to natural gas, corrosion can occur if operations are not compliant with federal regulations. These regulations include pipeline inspections, reporting corrosion-related incidents, and filing reports of job site accidents.
Environmental Impact
Lastly, pipeline leaks can lead to harmful effects on the environment. If pipelines are not properly operating, the likelihood of oil spills increases. These spills can contaminate the environment around the oil and gas operations as well as the natural landscape and the operation itself.
How to Contain Ethyl Mercaptan Odors and Natural Gas
Adding Ethyl mercaptan to natural gases is not going anywhere, but that does not mean that operators need to worry. Although there are negative things that can occur if too much Ethyl mercaptan is added to natural gas, when the correct amount of mercaptan dosing occurs there are a lot of benefits in ensuring safety in oil and gas operations – especially in detecting gas leaks. Plus, there are products that operators can add to their applications for mercaptan dosing to help provide the correct amount of the chemical while also effectively containing it - keeping production running smoothly.
Graco provides various chemical injection products that help increase efficiency and safety in the oil and gas industries. Specifically, the Graco Wolverine ND Fluid Module offers a spill-free solution for chemical dosing. The fluid head’s design helps capture chemical leaks in the event a seal failure occurs. Featuring a flexible return hose assembly, the module helps operators avoid hazardous maintenance and decrease corrosion - all while containing odors and gases.
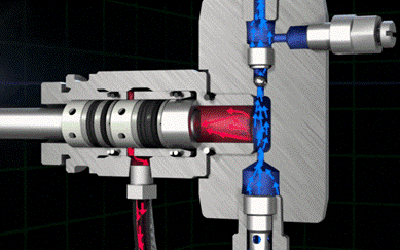
It is a great solution to help fight the environment, safety, and regulatory risks that mercaptan can cause. Watch our video to learn more about the specifics of the Wolverine ND Fluid Module.
Chemical Injection
For chemical injection applications such as dispensing and dosing chemicals at wellheads, Graco offers a broad selection of equipment such as injection pumps, metering pumps, fluid modules and much more.
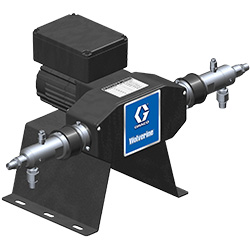
Related Articles
Sucker Rod Pump Maintenance
Sucker rod pumps play an important role in the oil & gas market. Graco describes their components and maintenance strategies to extend system life.
Quintuplex Pump Maintenance for Hydraulic Fracturing Operations
Pump packing failure is a significant contributor to the disruption of frac operations and unplanned machine downtime. Learn how introducing automatic lubrication to quintuplex frac pumps extends packing life and simplifies maintenance.
Chemical transfer pump QUANTM: Selecting the right pump
Safer, quieter, more advanced capabilities, with reduced energy usage and CO2-emissions: in a nutshell the main advantages the QUANTM electric pumps have over centrifugal pumps and air-operated double diaphragm pumps. But where in your processes is the added value most significant and what pump conf...