Supplier Corrective Action Request
In the event a supplier is issued a Supplier Corrective Action Request, the request must be completed by the due date and include a complete 8D analysis of the failure. This completed analysis shall be submitted to the Divisional Supplier Quality Engineer for validation and approval. The rejected part(s) will be added to receiving inspection for a minimum of 3 future lots.
Listed below are the Graco 8D requirements once a SCAR has been issued to a supplier:
D1: Establish a team of people with product/process knowledge related to the complaint/rejection. Assign one person to “own” the Root Cause Analysis (RCA) and Corrective/Preventative Action (CAPA). Potential team member suggestions are:
- Quality: Inspector or Technician
- Manufacturing: Operator, Machinist, or Assembler
- Management: Production Manager or Area Supervisor
- Engineering: Engineer assigned to the specific product or production area
D2: Describe the Problem. This is provided by Graco via the Supplier Corrective Action Request (SCAR) or Nonconforming Material Report (NMR).
- Make sure the defect description is complete and understood
- Contact the Graco Supplier Quality Engineer if any additional information is required
D3: Interim Containment Plan. Goal of this step: Define and implement containment actions to isolate the problem from Graco. This step should include the following items:
- Review inventory: Implement a stock check at your facility and any affected locations for Graco product.
- Review Work In Process (WIP): Determine if there are any parts in WIP. If there are parts in WIP, product will need to be reviewed to determine if it is impacted by the identified non-conformance. This may require placing the WIP on hold until verification can be complete. Contact your Graco Supplier Quality Engineer if the hold will effect delivery of open purchase orders (PO)
- Product in transit: Notify Graco if any parts are currently in transit between companies.
Quantities of parts that fall into each category should be reported. Immediate actions should be taken for all quantities reported. Any actions taken should be reported to the Graco Supplier Quality Engineer. Containment plan is due with 24 hours of receiving the SCAR.
D4: Root cause (failure and detection). Identify all applicable causes that could explain why the problem has occurred. Identify why the problem was not noticed at the time it occurred. How did the product ship to the customer with the defect undetected? Some examples listed below. The following are not the only options and are just examples of how defective parts could escape.
- Inadequate inspection frequency
- Inadequate gaging methods
- Lack of attention to the specific dimension
- Was not identified as a risk in FMEA
- Failure to follow existing procedures
NOTE: All causes shall be verified or proven. One can use 5 Whys or Ishikawa diagrams to map causes against the effect or problem identified.
D5: Identify solutions that will eliminate the root causes for BOTH the failure itself AND the lack of detection.
What changes were implemented to eliminate the failure? Corrective action should be an improvement to a process, machine, environment, training, measurement or material. Corrective actions should not include an Employee is no longer with the company, employee was given a warning, or employee was terminated. The next employee may make the same mistake if the true root cause is not properly addressed.
D6: Validation and implementation.
- Validation. What steps were taken to verify that each corrective action (CA) is effective? To validate/verify a corrective action is effective you should be able to recreate the defect by removing the corrective action and then eliminate the defect again by re-implementing the CA.
- Implementation: When were the corrective actions permanently implemented? Long Term Implementation plan should be completed within the following:
- High Priority - 10 calendar days
- Medium Priority - 20 calendar days
- Low Priority - 30 calendar days
Extensions for long term implementation may be granted at the discretion of the divisional SQE if requested prior to the existing due date.
D7: Prevent recurrence / systematic problems. What other product with similar design, material or process could possibly suffer from the same root causes?
An example of similar designed parts would be different sized pistons. If you have a problem with one piston, what other pistons can benefit from your lessons learned?
An example of similar processes might be die casting or injection molding. If the problem is related to a process, machine, or material, what other product utilizes the same process, machine or material?
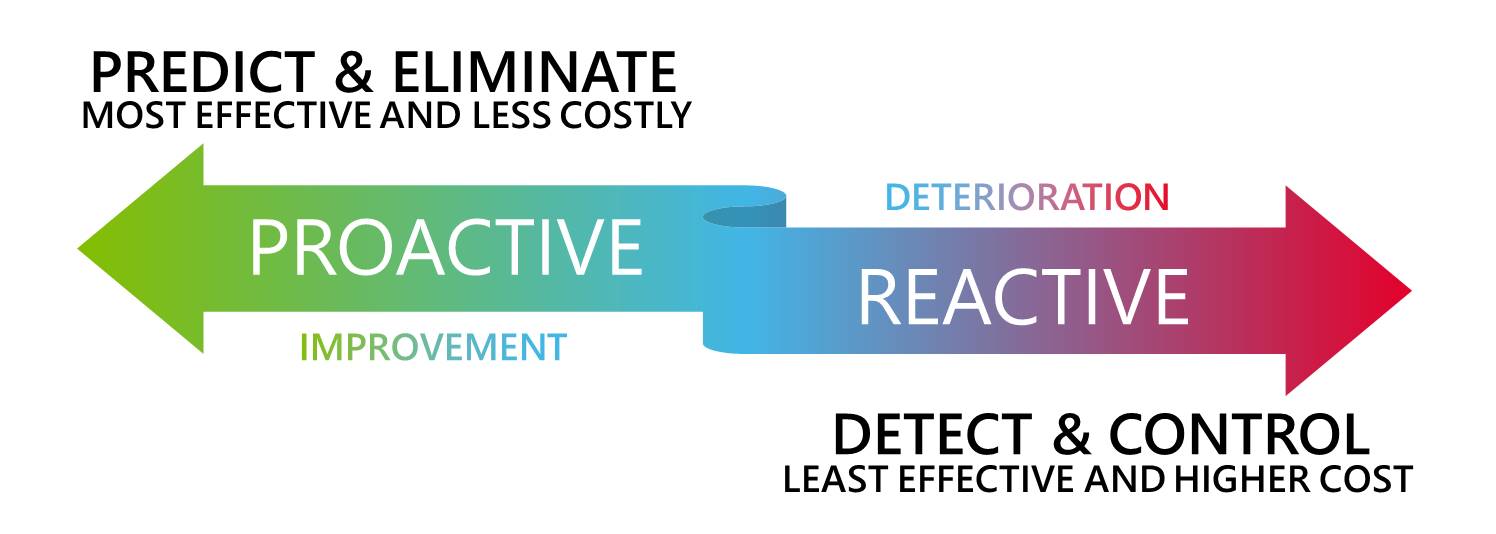
D8: Approval and closure. If your RCA/CAPA is missing information or the submission is vague, you will be contacted by the SCAR author for additional information.
If your RCA/CAPA is found acceptable to Graco, you will be notified via e-mail.