Hold*Blast Vision Test Results
Introduction
Steel surface preparation prior to coating application typically involves a cleaning and blasting process using an abrasive material to mechanically abrade the surface. The process uses high pressure and typically creates a lot of dust. A growing method to minimize the dust is using wet abrasive blasting equipment such as EcoQuip2 Vapor Abrasive blast equipment. The high pressure water provides dust suppression for safety and still achieves efficient blasting of the steel surface. With the presence of water in the process, there is the risk of the substrate flash rusting as the surface dries which could require the process to be completed all over again.
Background
There are surface passivating chemicals that exist in the market that are added to the water tank of the vapor blasting unit that prevent the flash rusting, not only in the drying process but for days after the wet blasting is completed. The passivation chemistry is typically not a film forming process unless too high of a concentration is utilized or pooling of diluted solution is allowed to concentrate through evaporation. With existing products in the market, there isn’t a way to inspect the surface in the field for any organic residue that may cause adhesion issues with the application of the coating system until now.
HoldBlast VISION is a novel surface passivating technology that ties a UV fluorescing indicator to the passivating chemistry so that a simple black light can be used to inspect if there is any risk of organic residue left on the surface. Even on a sunny day, the fluorescence is easy to see. The synergy of the UV fluorescing indicator with the passivating technology provides for a threshold type inspection providing a simple "Go or No-Go" result. This was developed in the lab using ATR-FTIR for organic residue detection in comparison to fluorescence intensity along with corresponding high performance coating adhesion testing. The remedy is simple. If there is indication of residue by fluorescence, the surface should be washed with potable water. Once the surface is dry, re-inspect with UV light, and apply the coating with zero risk of surface residue.
Test Objective
For this test, the EcoQuip 2 Vapor Abrasive Blaster was used to blast a steel panel using a 2% solution of HoldBlast Vision. After blasting, a black light was then used to inspect for residual HoldBlast Vision on the substrate. To finish off, a spray of 50% and 100% solution of HoldBlast Vision was used on to the blasted substrate in different areas to compare to the 2% blasted part of the panel using a black light.
Test Setup
- EQ-p, 50’ x 1” blast hose
- #6 nozzle
- About 85psi blast pressure with 30/50 abrasive
Test Procedure
To begin the test, the 2% Solution of HoldBlast Vision and water were mixed and then blasted on a steel panel. A blacklight was then used to look for residual Hold Blast Vision on the substrate. The next step was to then mix a 50% and 100% solution into a spray bottle. Apply each of these solutions to a different area and then use the black light to compare the 50% and 100% to the 2% solution. Finally, wash down part of the 50% and 100% solution, and use the black light to see if any residual HoldBlast Vision will show up under the blacklight.
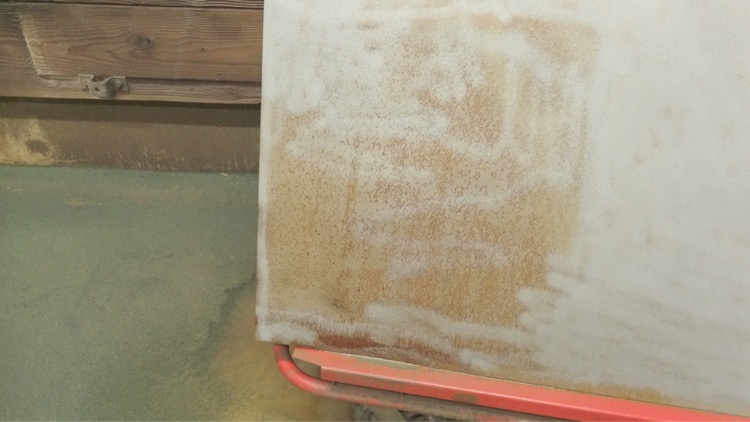
Picture #1 - The entire panel had a uniform corrosion as seen above, before the panel was blasted
Test Results
The 2% HoldBlast Vision solution was added to a blast pot with 30/50 abrasive. This pot was then pressurized and the blast pressure was set to around 85psi. The entire steel panel was then blasted. After blasting, the panel can be tested with a black light for buildup of the HoldBlast Vision. From this test, the results showed that no buildup was found. Refer to picture #1 to see what the steel looked like before blasting, and then look at picture #2, as this is the blasted panel with a 2% solution and black light.
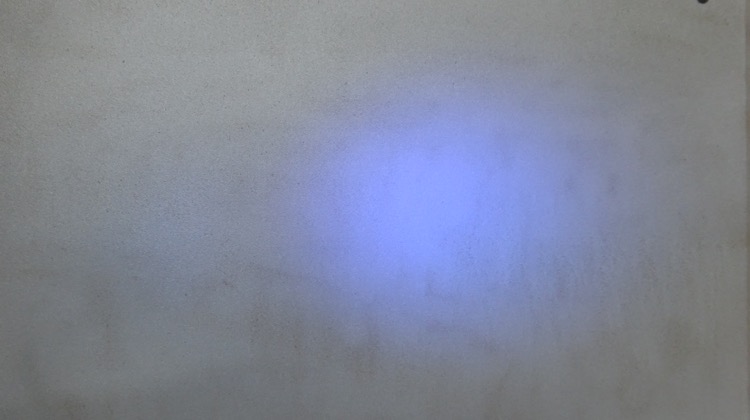
Picture #2 - The blasted panel with the black light showing no fluorescence using the recommended 2% HoldBlast VISION solution
The next step in the process was to use a spray bottle filled with the 50% Hold Blast Vision solution to spray the solution in a vertical line on the blasted panel. This step was repeated with the 100% Hold Blast Vision solution, in the same manner, using a spray bottle. Using a black light on both mixtures, the solutions became visible. Refer to picture #3 below.
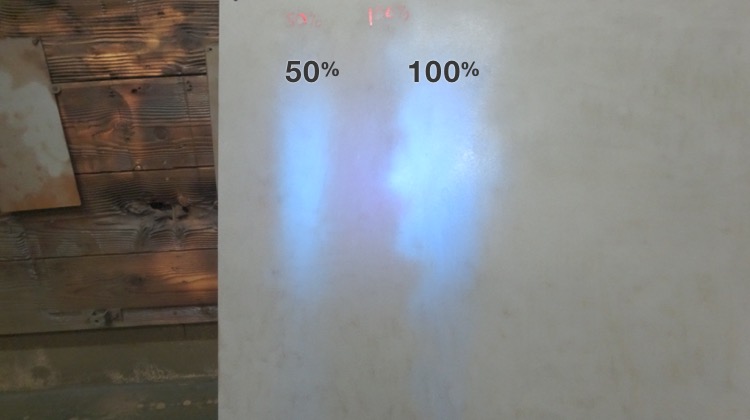
Picture #3 - The 50% and 100% solution were sprayed on panel and shown with the black light
Next, a portion of the 50% and 100% solution was washed down with water and inspected with the black light. Refer to picture #4 below.
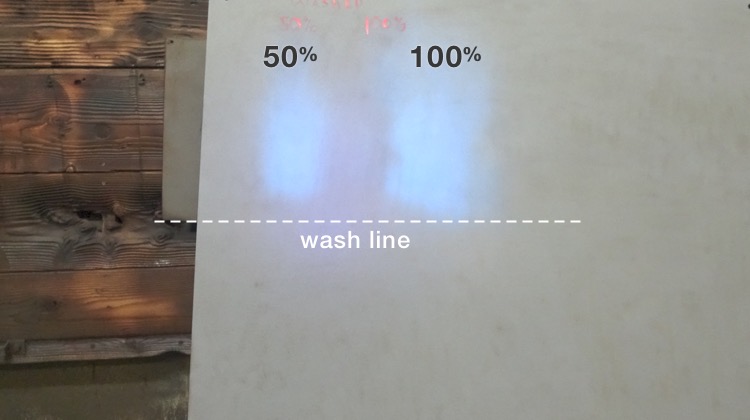
Picture #4 - The portion of the 50% and 100% that was washed showing no fluorescence
After one week of being blasted, the steel surface had minimal corrosion. Refer to picture #5 below. After almost three weeks there was some spot corrosion on the 100% solution area that was not washed off and some spot corrosion on the bottom left part of the panel where it was washed down during testing. Refer to picture #6 below.
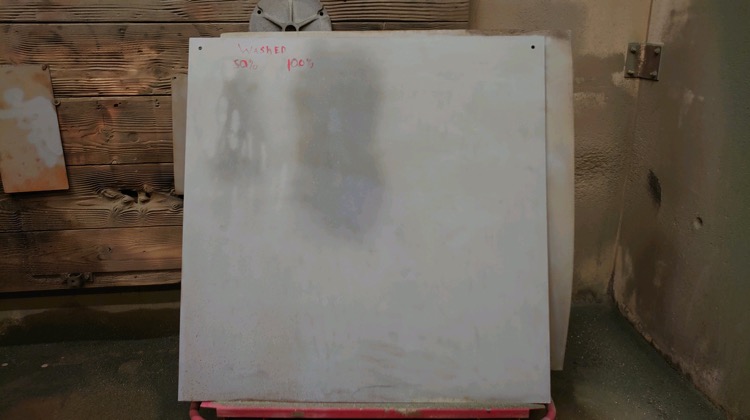
Picture #5 - One week after being blasted and the surface is still passivated
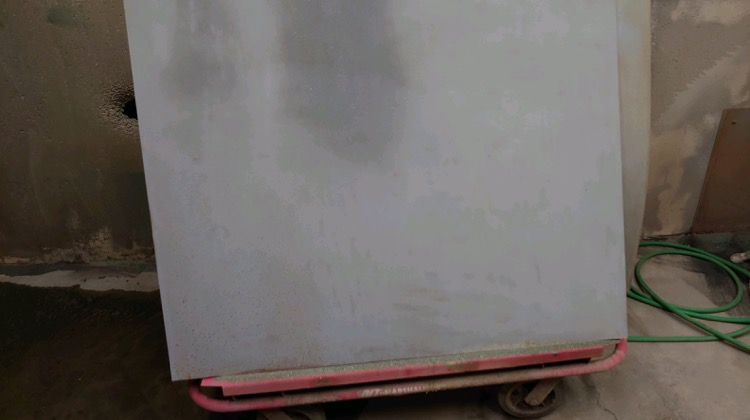
Picture #6 - Three weeks after being blasted with minimal corrosion
Conclusion
HoldBlast VISION surface passivating technology demonstrated a simple way to detect if the material is applied properly for assurance that the applied coating has zero risk of adhesion failure from organic residue on the surface. HoldBlast VISION was also shown to provide superior passivation at 3 weeks and minimal flash rust present.
NOTE: This information was developed under laboratory conditions which may vary with actual field applications. Testing was for showing the fluorescent properties of HoldBlast VISION. The ability for this product to prevent flash rust or corrosion was not part of the test. The pictures that show one and almost three weeks since blasting was for demonstration purposes only as the corrosion on them was not graded.
Contact an Expert
Related Articles
Concrete Surface Prep Part 3: Grades of Roughness
How much surface profile is sufficient for various types of concrete coatings and overlays?
Concrete Surface Prep Part 1: Unsound Concrete
How does the blaster know when he’s achieved the specified surface profile on concrete?
True Dustless Blasting is a Myth
Know the facts: there is no such thing as dustless or dust-free blasting in surface prep