Electric, Hydraulic or Air-Driven Spray Foam Machine
Which Is The Best Type Of Spray Foam Machine?
Among the biggest decisions facing spray foam operators is which type of spray foam machine to purchase. Selecting the type of machine that cost effectively meets your business needs for output, longevity and ease of use is critical to your success.
There are three types of spray foam machines from which to choose – air driven, electric and hydraulic. Each has its advantages depending on your spray foam needs and how you plan to use your equipment.
Air-Driven
Air-driven systems are considered easy-to-use entry level machines for low-output applications, and can deliver up to 25 lbs. of material per minute. Air machines are generally used for in-plant applications or as an entry-level machine for contractors.
The relatively low cost of air-driven machines makes them attractive, particularly to start-ups. However, business growth and expansion into new applications may soon necessitate the purchase of larger, higher output machines.
Because air-driven machines require an air compressor to operate, in-plant foam applications where large air compressors are available on-site often make these machines an attractive, cost effective choice. Learn more about how air-driven spray foam machines work.
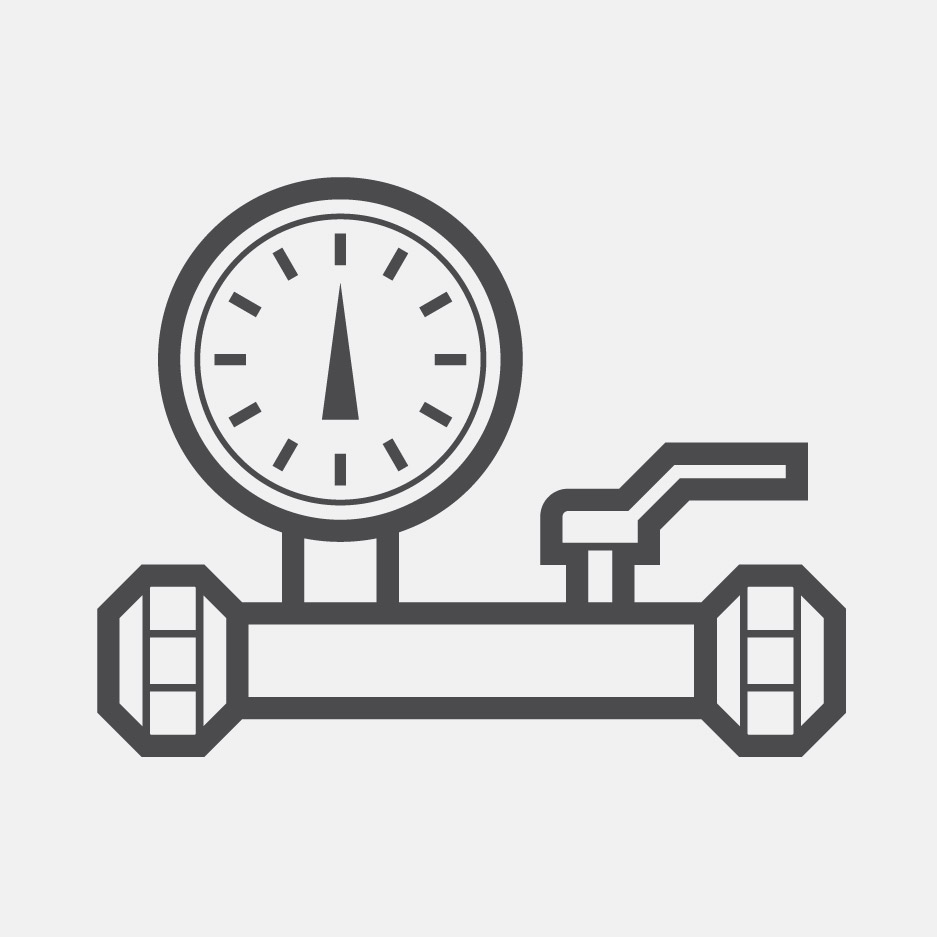
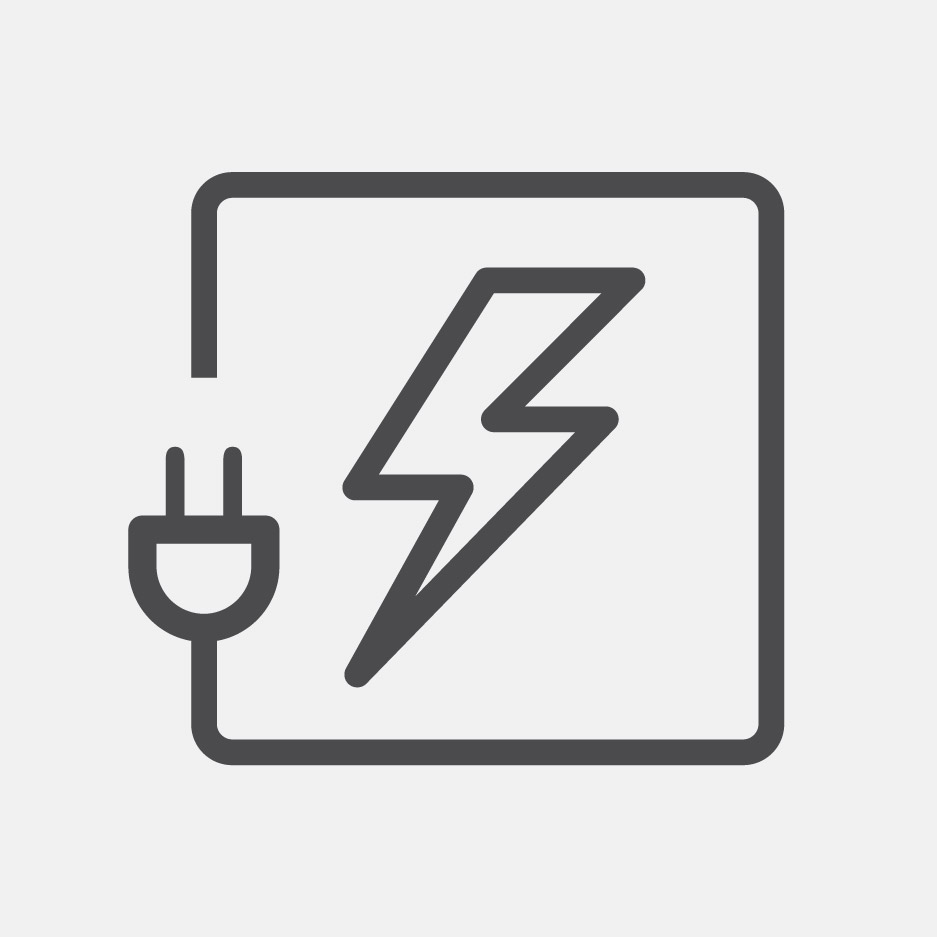
Electric
Electric spray foam machines have become the most popular systems in the industry, and are considered mid-level production units, delivering between 20-30 lbs. of material per minute. Due to the mid-range output of the electric machines, typical applications are residential construction and mid-sized industrial construction. Learn more about how electric spray foam machines work.
Hydraulic
Hydraulic spray foam machines are high output units, delivering 30-50 lbs. of material per minute. These machines are well suited for a range of applications, such as residential construction and larger commercial buildings, roofs, and oil and gas applications. These high output units allow operators to apply material faster and more efficiently.
Another consideration is the life span of the various types of machines. The typical life span of electric foam spray machines can easily be 7 to 10+ years. Due to their robust design, hydraulic spray foam machines last a bit longer, 10 to 12+ years. Keep in mind many factors contribute to the useful life of a piece of equipment, including usage rates, the application environment and preventive maintenance.
The larger pumps on the hydraulic sprayers cycle less frequently, so they need to be rebuilt less often, on average every one to two years. Conversely, pumps on the air and electric machines may need to be rebuilt more often based on the reduced output per stroke. Learn more about how hydraulic spray foam machines work.
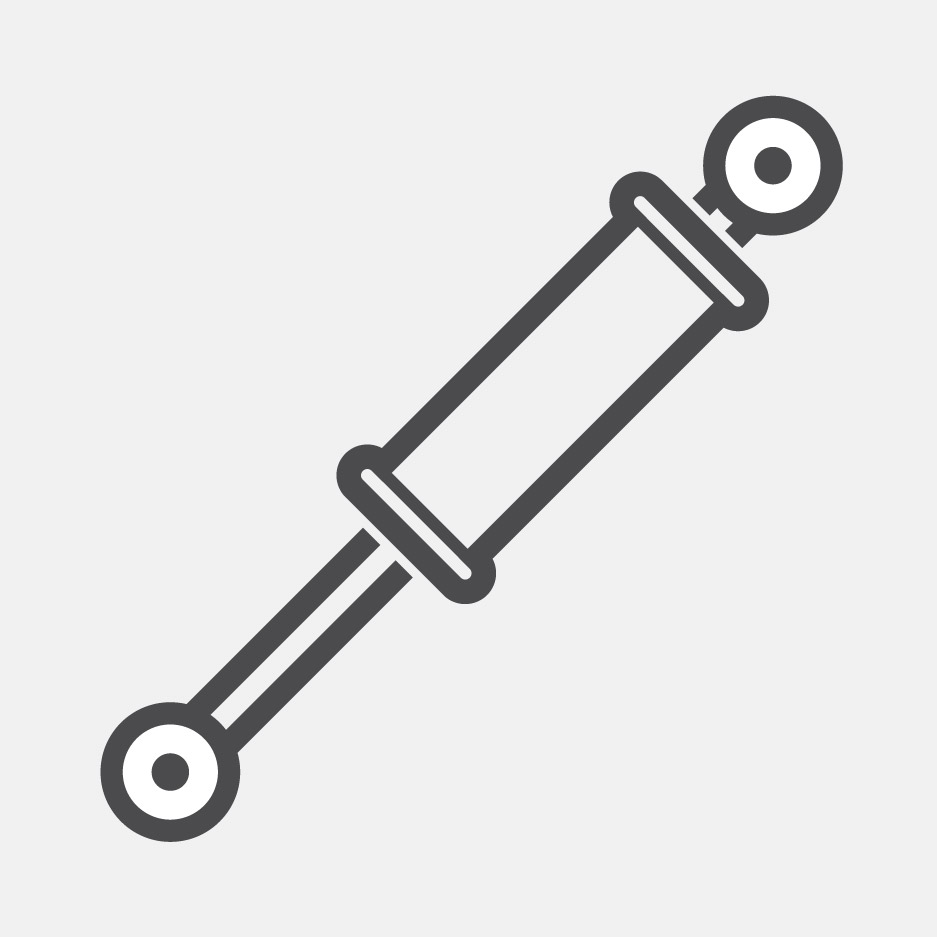
Total Cost Of Ownership
It’s also important to consider not just the initial purchase price of a machine, but the total cost of ownership over the machine’s life. Lower cost machines from second tier manufacturers can have much higher total costs due to more frequent replacement of parts and the labor required to make repairs, as well as the hidden cost of downtime.
If crews frequently need to wait for shipment and installation of replacement parts, the labor cost due to unforeseen downtime, as well as the cost of lost customer goodwill, need to be considered. While it’s tempting to simply pick the lowest price machine and hope for the best, these hidden costs can quickly offset a lower sticker price.
Look for reputable manufacturers who have a nationwide distributor network that can provide next day parts delivery. Graco provides call-in and up-to-date online technical support to quickly trouble-shoot and diagnose problems.
Some machines enable easy troubleshooting for minimal downtime. This helps keep crews spraying foam, rather than waiting for a service technician to arrive and diagnose a problem.
Alarms can also help prevent operators from spraying bad foam as a result of incorrect temperatures, pressures and/or ratios. Without these alarms, operators may unknowingly spray bad quality foam, making a costly mess, and ruining their reputation as well as damaging the spray foam industry’s general reputation.
Remote Tracking And Reporting
Remote reporting technology can allow owners and managers to use their smart phone, tablet or any Internet-connected computer to remotely track and view what’s going on with each machine in real time.
Remote reporting technology can also reduce liability by recording spray parameters once every minute, and owners can print reports that prove their foam was sprayed according to the chemical manufacturers’ recommended settings.
Air machines typically lack data capture and remote reporting capabilities. They also are generally simpler to operate with more basic controls. However, operators shouldn’t be intimidated by the presence of a control panel because they’ve been carefully designed to be intuitive to use.
Finally, any spray gun will work with any machine. Select a good quality gun that you’re comfortable with and that’s able to mix chemicals at high pressure to ensure good spray results.
Selecting a good quality machine to fit your business may seem a bit daunting. But taking the time to research your options and consider the many variables for your specific business needs will help you make an informed decision that will pay dividends far into the future.
Related Articles
How Air-Driven, or Pneumatic Spray Foam Machines Work
By learning how air-driven, or pneumatic, spray foam machines work, you'll be able to understand what to consider before buying one.
How Hydraulic Spray Foam Machines Work
Learning how hydraulic spray foam machines work will help you understand the pros, cons, and if hydraulic is right for you.
How Electric Spray Foam Machines Work
Learn about electric spray foam machines and how they provide reliable performance for a wide range of applications.