Reactor 2: Resistance control mode
Resistance control mode (RCM) is Graco's new, patent pending, heated hose temperature control technology.
What is resistance control mode?
Also referred to as "Resistance Mode", resistance control mode (RCM) is Graco's new, patent pending, heated hose temperature control technology. RCM allows you to have full temperature control of your Graco heated hoses without depending on the hose RTD cables and FTS for temperature monitoring and control. RCM can be used on all standard Reactor 2 machines with software version 4.01.001 or higher installed. (Resistance mode will not work with Gen 1 or Gen 2 E-30i, or E-XP2i machines).
RCM uses the electrical resistance of the hose’s heating element to monitor hose temperature. The electrical resistance will change as temperature changes, the Reactor will monitor how the resistance of the hose is changing and then calculate the actual temperature. Resistance mode should only be used with genuine Graco hoses.
Benefits of RCM
- Less downtime. Broken RTD cables and fluid temperature sensors are no longer an issue. No time needed to do repairs.
- Less repair costs. Buying of parts to repair broken RTD cables and FTS sensors is eliminated. No labour costs required to perform these hose repairs.
- Improved yield. Optimise your material yield with consistent and accurate hose temperature control. RCM provides more consistent heating, eliminating hot and cold spots of material within the hose. In addition, if your hose is running in "Amp mode" or "Manual hose heat mode" your material temperature is not being accurately controlled, therefore you are sacrificing material yield.
- Increased productivity. Less downtime due to troubleshooting hose alarms. Increased performance by spraying with a hose providing consistent and accurate temperature control.
HOW TO GET RCM SOFTWARE
All Reactor 2 machines shipped by Graco after September 1, 2019 will have the latest software installed. This software includes "resistance control mode".
To upgrade your Reactor 2 software on existing machines, work with your local Graco authorised distributor to coordinate having your software updated.
How to use RCM
- Update your Reactor software to the latest version 4.01.001 (or newer) if your Reactor does not already have this software
- Enter Setup mode on the ADM and navigate to system screen 3
- Select "Resistance" from the drop down menu
- Upon initial installation, follow the calibration procedure
Video: Resistance control mode set-up and calibration
RCM should only be used with genuine Graco hoses. Temperature controlling a hose using RCM requires software that has been optimised for use with Graco heated hoses. Minor resistance differences of competitive hoses can dramatically affect the accuracy and ability to properly control the temperature of the hoses and should not be used with RCM.
Caliberation procedure
The most important detail is that the calibration should be done when the entire system (Reactor and hoses) are in the same ambient condition. The optimal time is first thing in the morning before the primary heaters or hose heat has been turned on. With a functioning FTS, a calibration may be performed after waiting 5 minutes from when a Reactor was last used. Without a functioning FTS, a calibration should only be done when the entire system is at ambient conditions.
- Make sure the hose and Reactor are at ambient temperature
- Press the "Calibrate" soft-key
- Wait 2-10 seconds while the system measures the hose wire resistance
- Once the hose resistance is measured, a temperature will be displayed. If the temperature looks accurate, accept the hose calibration. If not, cancel and repeat calibration.
Once calibration is complete, return to the run screens of the ADM. Set the hose temperature as normal. When the Reactor is in "resistance control mode" you will see a resistor icon under the hose icon on the ADM and on your Reactor app
Because the hose temperature is now being calculated by measuring the resistance over the entire length of hoses vs. measuring the temperature at the one location (at the FTS), it is normal that you may need to slightly adjust the hose temperature setting by a few degrees from the normal set-point to achieve optimal spray results.
When using Resistance Mode, a reminder will appear when the Reactor is powered on in order to remind the end user to recalibrate if a hose section has been removed, added or replaced. Simply press the "Continue" key to acknowledge.
What is hose calibration and why is it important?
NOTE: A saved calibration factor is required before using RCM.
In order to use "Resistance Control Mode", an initial calibration must be performed. The calibration process measures the hose resistance and the ambient temperature and then saves these values as a "calibration factor" for the Reactor.
To calculate a calibration factor, the Reactor will correlate the measured resistance at the time of calibration to the temperature at the time of calibration. The temperature can be sensed from one of three locations: 1. the hose FTS if it is connected and properly functioning, 2. the A primary heater temperature, or 3. the B primary heater temperature.
Having a properly saved calibration factor allows the Reactor to accurately control the temperature based on the change in electrical resistance of the heating element. Once the machine has an accurately saved calibration factor and the hose control mode has been switched to RCM, the system is no longer dependent on the hose RTD cables and the FTS to monitor and control the hose temperature (the RTD cables and FTS should remain installed to provide static ground protection.)
Calibration is only required during initial setup and will only take a few seconds to perform.
Re-calibration
Re-calibration is only required when:
- a section of hose has been replaced
- a section of hose has been added
- a section of hose has been removed
- over time, the hose temperature does not seem to be controlling accurately
Initial setup of Reactors
- The factory setting for hose control will remain the traditional FTS control mode. RCM will not be the new factory setting because a calibration must first be performed before using RCM.
- Once the calibration is complete, Graco encourages customers and distributors to make RCM the standard operating mode for Reactor 2 machines using genuine Graco heated hoses.
- Even if FTS control mode is preferred. we would like to recommend getting into the habit of automatically calibrating the Reactor during set-up and installation, before first use of their new Reactor 2.
- If an initial calibration is performed and saved at the time of initial machine installation, the customer can then use the traditional FTS hose control mode and switch at any time to RCM. This may be beneficial if the user was spraying using FTS mode and experienced an issue. They would then be able to immediately switch to RCM since the calibration factor was already saved. If the calibration had not been previously completed, the calibration should not be done for several hours to allow enough time for the primary heaters and hose to equalise to an ambient temperature.
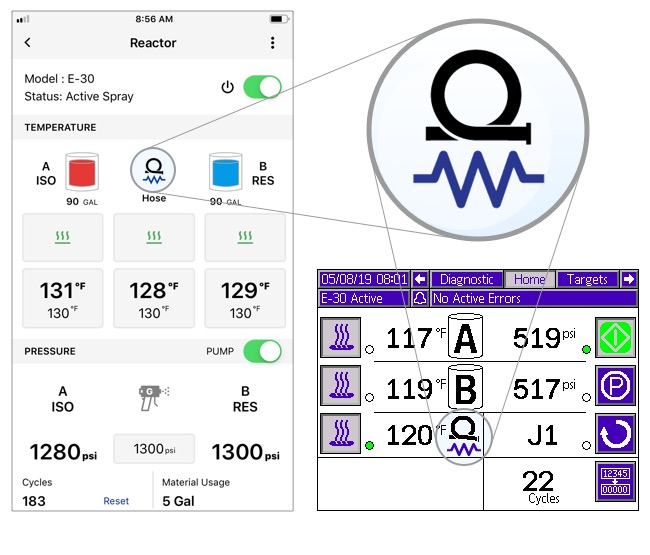
RCM vs. FTS temperature control vs. manual hose heat mode
- Resistance control mode: Monitors hose temperature over the entire length of hose by measuring the total hose resistance. Minimised hot and cold spots associated with typical hose condition like hoses coiled on a hose rack, missing hose insulation, varying ambient conditions, etc. Not dependent on properly functioning RTD cables or an FTS to monitor hose temperature.
- FTS control mode: Measures the temperature at one location, the location of the FTS. Hose temperature control can be significantly affected by several factors: the quality of the hose insulation (or lack of hose insulation) at the section of hose where the FTS is located and the ambient temperature at the FTS location (on frozen ground, on a hot roof, etc.). Both of these factors can significantly affect the FTS and the chemical temperature throughout the hose, causing hot and cold sections of material in the hose.
- Manual hose heat mode: No temperature control or temperature monitoring. The available electrical power used to provide hose heat is significantly reduced. Allows the hose to heat at a reduced capacity to provide the ability to finish a job. Hoses should not be run long-term using manual hose heat mode. The hose temperature cannot be controlled to a specific temperature and one cannot turn the hose heat on/off. Hoses will continue to heat up even if the chemical temperature surpasses the desired value. Hoses will take longer to heat up due the to reduced amperage used for heating. Material yield will be sacrificed due to an inability to control to an optimal material temperature. Do not use manual hose mode for extended periods of time. The system performs best when the hose is either in Temperature Control Mode or Resistance Control Mode.
Related articles
Can I use two guns on one machine?
This video goes through why we do not recommend using two guns on one machine.
At what ratio variance will the electric Reactor shut off?
Automatic ratio variance detection ensures good spraying results. But how is ratio variance calculated?
Can I use a Reactor without a hose thermocouple (FTS)?
Can I use a Reactor without an FTS? Discover the answer to this frequently asked question.