Saving up to 30% of paint by switching from hotpotting to a plural-component sprayer
Freeman Industrie France, a subcontractor of Cameron, is based in the South of France at Beziers. They specialise in coating large or oversized pipes used in petroleum pumping plants.
The automatic painting applications are done in Cameron’s facility. Freeman paints pipes in very different sizes. In the past, this was done via a manual application (also called hotpotting).
The same viscosity all year long
Local Graco distributor JJB, suggested that Freeman use a two-component fixed ratio Graco XP70 4:1 unit to save paint and solvent, to secure mixing and avoid handling. The pot-life of the material is 1 hour at 20°C. After this time, the material manufacturer advises that the mixed material should not be handled by the equipment. The relative long pot-life means that the mix manifold can be kept on the unit which provides more flexibility.
The viscous base is maintained at a constant temperature of 30°C, which enables the same viscosity all year long. The large container of 76 l provides the painter with high autonomy.
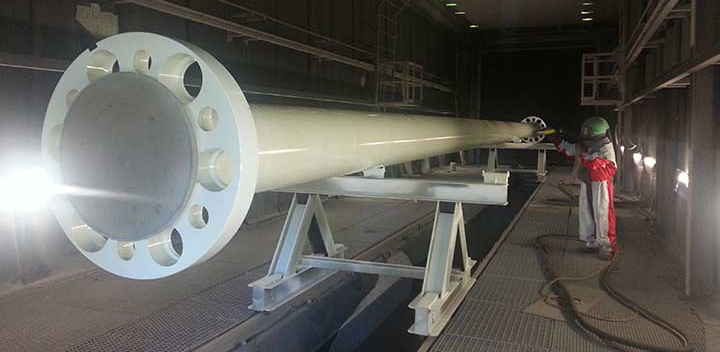
REDUCED LABOUR COSTS & SAVINGS ON PAINT AND SOLVENT
“The consistency in coating quality is impressive. Now, we no longer have to deal with temperature impact on viscosity throughout the year and diluting by hand, resulting in various final finishes,” says Mr David Serre, the paint manager.
The new application has enabled Freeman France to save 30% of paint and 50% of solvent volumes. The automatic preparation of two-component paint also reduces the labour cost. A return on investment is expected after about 1 year.
MORE INFORMATION
For more information about spraying steel structures and pipelines or Graco's XP plural-component sprayers, fill out the form below.
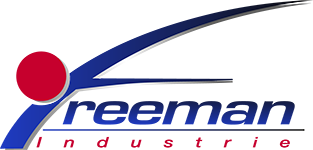
Related Articles
A closer look at Graco’s XP Plural-Component Sprayers
What’s the difference between the standard airless and the high-flow (hf) airless versions?
How to avoid hotpotting inconsistency issues
Frustrated at getting inconsistent spray performance after manually mixing two components? There’s an easy solution …
Three reasons to move from hotpotting to a plural-component machine
Discover the benefits of Graco’s XP and XM line of sprayers when you switch from hotpotting to a plural-component machine.