Moving from pneumatic to electric
A clear explanation of the benefits of using the King-E electric airless sprayer persuaded a steelwork contractor to switch from pneumatic to electric sprayers.
For many years, a structural steelwork contractor based in the north of England has used pneumatic 1K sprayers to apply paint to its steel structures. These sprayers are either 60:1 or 70:1 units, although older 58:1 units are also used. For some jobs, 2K materials are applied through plural pneumatic 2K sprayers. Coatings used by the company are generally epoxy primer and intumescent coatings.
However, although the company was satisfied with the overall reliability and performance of their legacy 1K pneumatic equipment, they were not too happy with a couple of significant drawbacks. One is the high energy consumption and cost, due to the use of compressed air. The other is the high sound level (in excess of 90 dBA).
They considered whether moving from pneumatic to electric sprayers would be more advantageous. However, they were concerned that the pump size of an equivalent electric sprayer might not be sufficient.
To get some advice, they contacted Spray Plant from Leeds, UK. Spray Plant is a UK specialist supplier of paint spray guns and spray equipment. They supply a full range of coating equipment from polyurea and foam spray to PFP and epoxy intumescent systems, and work with manufacturers such as Graco, Devilbiss, Microguard, ASM, Titan, Scott, Binks, Anest Iwata and Honeywell.
Equivalent spray output
After talking with the company about their requirements, Spray Plant Managing Director Mark Crabtree immediately identified the source of their concerns. “The technical challenge with moving from pneumatic to electric is the perception that the pump size of an electric sprayer is less than the pneumatic equivalent. Pneumatic sprayers (60:1) have a 220 cc wet end, whereas the Graco King E-60 sprayer, for example, has a 115 cc wet end. This leads to the understandable perception that the spray output of a 60:1 pneumatic sprayer is greater than that of a King E-60.”
However, Mark explained to the company that output is based not upon wet end size but tip size. In the majority of applications, the output of both pumps is the same. Theoretically, at maximum cycle rate, a 60:1 pump may allow for 12.9 lpm. In practice however, the average cycle rate of a 60:1 pump is 10-20 cycles per minute or 2.15-4.9 lpm. For a King E-60, the maximum volume is 2.9 lpm at 5000 psi, or 4.1 lpm at 3000 psi, as volume increases as pressure decreases. Trials have used tip sizes of .013, .017, .019 and .023. As the tip size determines the actual output of the pump, delivery ranged between 0.69 lpm and 2.15 lpm. In other words, there is no difference in spray output when moving to electric.
Less energy consumption
As they are electric, the energy requirement is considerably less than that required for their pneumatic equivalent. Requiring a 5 kW power source, there is no need to install an expensive air ring main from an air compressor. This avoids the loss of air through the system – or alternatively wasted energy. Additionally, the cost of generating compressed air is an expensive, inefficient process. In new facilities an electric supply will already be present within the sprayshop.
Less noise
And then there’s the second drawback of pneumatic sprayers: noise. “The noise from King E-series is considerably lower than from a pneumatic unit,” adds Mark. “In fact the noise level is a mere 70 dBA compared to the 90 dBA of the pneumatic equivalent.”
Paint wastage through overspray is also addressed with the King E-series. Due to there being virtually no pulsation on pump changeover, the spray fan is more consistent. It has actually been found that a smaller tip may be used in comparison to the same material application using a pneumatic sprayer.
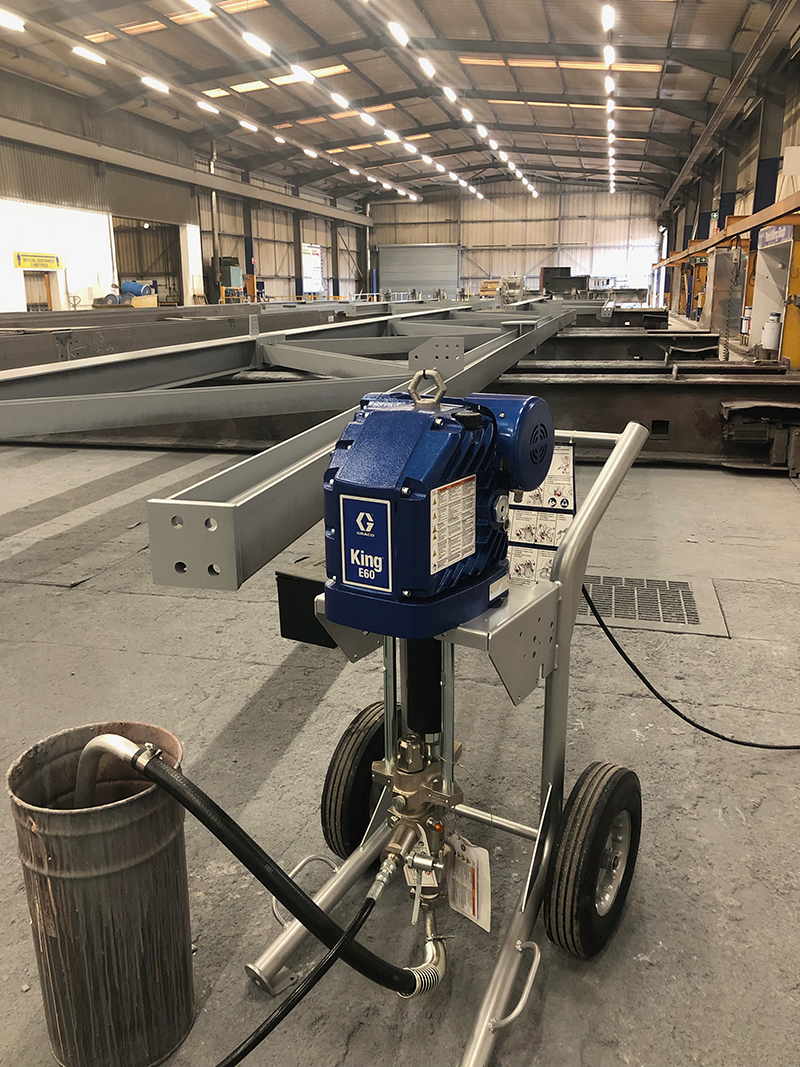
Smoother operation
As with pneumatic sprayers, King E-60 can also support the use of two spray guns simultaneously. It also has the ability to support the same lengths of paint hose as pneumatic pumps. Two further advantages of electrical technology are that it reduces pulsation and completely removes the possibility of motor icing that can occur with pneumatic air motors, both of which make jobs run more smoothly. The King E-Series electric airless sprayers are available for hazardous locations as well as non-hazardous locations.
Based on Spray Plant’s expert advice, the structural steelwork contractor realized that electric sprayers provide a viable alternative to the industry norm, and decided to switch from their pneumatic sprayers to Graco’s King-E electric airless sprayers.
Multiple power options
The King E-60 runs at 15A @ 200-240V, 50/60 Hz, single phase; or 25A @ 100-120V, 50/60 Hz, single phase. Its ability to run from 110-120V is useful as this voltage is required for power tools to operate in certain countries (e.g. the UK).
More information
If you are interested in learning more about Graco’s King-E range of electric airless sprayers or want a product demonstration, fill in the form below.
Related Articles
Graco’s KING electric airless sprayer: what sets it apart from conventional electric airless sprayers?
In one word: ATEX. The Graco KING electric airless sprayer is the world’s first electric sprayer for protective coatings that is approved for hazardous locations.
Why it’s time to replace your conventional petrol/gasoline-driven sprayer with an electric airless sprayer
There are many reasons for exchanging your petrol/gasoline-driven sprayer for an electric airless sprayer such as the Graco KING. Here we highlight just three.
The cost of using an air compressor
Air-powered tools have a number of advantages. One significant but surprisingly often neglected disadvantage is the cost. Air is frequently regarded as “free”, but running an air compressor can often be highly expensive.